Compare and Contrast: Capital One 360 to Dezurik
Company Overview
From an operations management perspective, we compared and contrasted Capital One 360 to Dezurik. We looked at many different aspects of both businesses in relation to various operational and business elements. We conclude that both corporations have significant differences based on manufacturing versus service operations. Dezurik is a pure manufacturing company, which was founded in 1928, while Capital One 360 is a pure service company that was founded in 2013. Dezurik designs and manufactures valves for use in commercial and residential applications. Capital One 360 provides online banking options to consumers in the United States.
Topics Covered
Order custom essay Compare and Contrast: Capital One 360 to Dezurik with free plagiarism report
Our goal in this business report is to compare and contrast Capital One 360 and Dezurik based upon the following categories:
- Service vs Manufacturing contrast
- Business and Operations Strategy
- Process Design and Supply Chain, Flow Chart
- TQM, Jit, Six Sigma
- Kanban, Kaizan
- SWOT Analysis
- Capacity Planning
- Layout and Design
- Recommendations
In summary, both companies are making short and long-term adjustments to prepare themselves for the years ahead. By implementing our original recommendations within each company, they will both become more efficient and effective companies as a whole.
Manufacturing often provides services, and services often provide tangible goods. Dezurik is a pure manufacturing company, whereas Capital One 360 is a pure service company. Dezurik designs, develops, and manufactures tangible products that are valves and inventories them inside their manufacturing facility. Dezuriks plant equipment is used solely for the production of their valves and related products. The dezurik manufacturing company has low customer contact and a longer customer response time. In contrast to Dezuriks pure manufacturing company, Capital One 360’s pure service corporation handles their business much differently.
Capital One 360 has intangible products that cannot be inventoried. Capital one 360 has high customer contact and can be reached 24/7. They offer many different ways to service customers such as in their cafes, calling and talking to a real capital one associate, blogging, and also offer a mobile app. The café allows customers to interact with Capital One 360 employees and the employees working behind the counter are educated in their business. Capital One 360 has a short response time; customers can go online to access their accounts which saves them time and money. They are also labor intensive and have around 450 associates working in their St. Cloud office.
Although Dezurik and Capital One 360 differ in terms of service vs manufacturing, they share many similarities. Both corporations use technology. Dezurik uses modern up-to-date technology in the machines they use to manufacture valves, as well as in their 3-D solid modeling of valve parts and assemblies. Capital One 360 also uses technology by offering services over the web, phone, ATM or by mail. Both companies have quality, productivity, and response issues that must be dealt with on a daily basis to maintain customer satisfaction. Both companies must have forecast demand and each will have capacity, layout and location issues.
Both Dezurik and Capital One 360 have business and operations strategies in place to ensure success in their respective businesses. Dezurik has a strategy of giving their customers high quality products that will withstand the test of time. Capital One 360 wants to give the consumer an easy to use product that is incredibly efficient and environmentally friendly. Both companies have strategies that are similar, while others are completely different from each other. Dezurik, being a pure manufacturing company, needs to focus more of their work on their manufacturing process.
In order to produce the valves they need, they must regulate their supply to correlate with their demand. This can be shown in their manufacturing process. Dezurik has some valves that they are mass producing all of the time. They also are able to take on project builds for custom sizes and designs. These are two different segments of Dezurik which require two different business strategies. The first strategy that Dezurik has is to be continuously producing their standard size valves. This is a fairly straight forward operations strategy. Keep up with the demand for the valves, and at the same time maintain an efficient product assembly line. The second strategy has to do with their special product order segment. They do this in several different ways.
The first is to complete the projects in house, which shares the same as the previous strategy. The second strategy is to have one of their teams build and complete their projects on site. This typically happens when they work on a project with components that are too big to build in house. The business strategy for Dezurik is much different. They want to become the largest producer of valves in the world. They do this by outsourcing some of their components to China, which brings down production costs. They also need to be certified to be sold in other countries around the world. They are trying to expand internationally and build up partnerships and relationships with governments and companies from around the world. In order to keep these relationships intact, Dezurik has a full time service team that travels around the world to ensure that their products are working correctly and that they have satisfied customers.
Capital One 360 shares some similarities with Dezurik in their business strategies, but is completely different with their operations strategies. To begin, Capital One 360 is a pure service company. They have around the clock customer service to provide help and services to their customers. This is similar to Dezurik, but on a much larger scale. Since Capital One 360 has no physical locations, they need a much larger service department to help satisfy the demands of their customers. Their service department does differ in that they do not need to travel around the world to help their customers, rather they can do it all from their computer with just a few clicks of the mouse.
Capital One 360 has a unique business strategy for the banking industry. All of their banking business is done online. This means they have no physical banks. Also, all the money they have is virtual. This means they will need a large technical service department to help keep everything that is online, sorted out. Their operations strategies are different from Dezurik in several ways. First, Capital One 360 does everything online. They do have a sale department, but they never have to leave their cubicle to make a sale. This is different than Dezurik who may have to send their sales person out to a job site in order to ensure that the product they receive will be correct.
While these two companies do share business strategies, their operational strategies do tend to be further apart from each other. Dezuriks process design supports product manufacturability and defines their product characteristics of appearance, materials, dimensions, and performance standards. Dezurik’s process design starts with the idea that customers need better valves. Dezurik uses a hands-on philosophy that begins with design. They then use modern computer aided design systems to construct 3-D models of valves and assemblies. From here, the models are transferred to an area where stress tests are performed on the models. The final step in Dezurik’s process design is continually analyzing and adding safety factors to the models to ensure long-term reliability.
The flow chart inside Dezurik’s manufacturing facility starts at the loading docks. Here, ready to go shipments of valves are placed. As you enter further into the facility, the size of the valves placed in inventory decrease from 72 ’’all the way down to 3’’. This ensures that heavier and harder to move valves are placed closer to the loading dock to improve efficiency. Dezurik also uses intermittent operations, which means they produce a variety of products in lower volumes. Intermittent operations are used because different valves have different processing needs. This causes the workers to perform different tasks, and during the tour we learned that some workers switched stations on a daily basis. Dezurik has multiple buyers who want different specifications for every valve they receive.
This creates a batch process within the manufacturing facility allowing Dezurik to separate one customers order from another customers order. Dezurik’s designing process and consideration consists of make-to-order strategy. Moving away from Dezurik and into Capital One 360, there is contrast in the design of services that Capital One 360 has vs Dezurik’s design of goods. Capital One 360’s service design is unique in that the service and entire service concept are being designed. However, they are similar in which product and service design must match the need and preferences of the targeted customer group. Capital One 360’s flow chart differs from Dezuriks flow chart. Capital One 360 does not flow from one end of the building to the other in a line; instead they have different floors within their building where they communicate back and forth.
This creates a batch process where each floor is a batch working on a different project then the other floors. This is also called intermittent operations where Capital One’s resources are grouped together by function. The overall efficiency at Capital One 360 is around 65%. Both Capital One 360 and Dezurik have Total Quality Management plans in place to help ensure that their customers get the products and services that they want. Capital One 360 has different banking plans that have been developed to help cover a wide range of customers. Basically, they have standardized their products to help ensure efficiency and to keep costs lower.
Dezurik on the other hand, has many different products and services that can be produced based on what the customer wants. This may not be as efficient, but it gives them the advantage in securing business that cannot be obtained by companies that incorporate standardization. Dezurik also does a ton of product testing to ensure that the customer is getting a product that is guaranteed to last a long time. Capital One 360 and Dezurik also work with JIT. Just In time production can be shown more effectively in Dezurik since it is a pure manufacturing company. They use a pull system for production which causes them to have an inventory of their products. They can increase or decrease their production of certain models based upon forecasting.
Capital One 360 does not focus as much on Just-in-Time manufacturing, rather they spend more of their time using TQM and respect for people. Since they are purely a service company, They are constantly working with people to ensure that they have an enjoyable experience banking with Capital One 360. If Capital One 360 doesn’t respect their customers, it would be extremely easy for their customers to take their business to another bank. Like Capital One360, they also need to focus on TQM. They need to constantly be updating their products and services to give the customer want they want. They need to be surveying and working with their customers all the time to help them develop effective strategies in the online banking world.
Capital One 360 does focus a lot on Six Sigma. They have people in house that are constantly working to help make the company more efficient and effective. Basically, there are only four defects per million opportunities. This forces Capital One 360 to run incredibly lean. A few ways they do this is by going completely paperless. This saves a ton of money, as well as paper. Another way Six Sigma has been useful to Capital One 360 is in processing time. They have reduced the amount of time it takes to pull up and process a customer when they are on a service call. This is critical because the faster they can make their customer service process, the faster they can help more people. By doing some serious improvements to Capital One 360, they have become incredibly lean and efficient. This is different than Dezurik.
They can’t run Six Sigma because they take on custom jobs. These can be made more efficient, but to run a whole company Six Sigma test just is not practical.
Dezurik follows Kaizen, continuous improvement, which requires the company to continually strive to get better at manufacturing valves through learning and problem solving. One way they comply to Kaizen is in their testing room, where they test their valves to see where any improvement can be made. Dezurik uses a pull system where communication is made possible through the use of kanban cards. These kanban cards consist of the product name, the part number, and the quantity that needs to be produced. The kanban cards are attached to a group of Dezurik’s products.
When the employees need products from a preceding workstation, they pass the kanban to that station. This kanban authorizes the worker at the preceding station to produce the amount of goods specified on the kanban. These kanban cards are placed in visible areas for everyone to see. There are as many kanban cards in the system as there are batches of products or valves. This allows Dezurik to continually improve the efficiency of their system. In contrast, Capital One 360 does not have kanban cards, but they do follow the Kaizen approach of continuous improvement. Capital One 360 is constantly trying to help their customers save time and money. They are doing this in part by offering simple financial products such as giving fee-free checking and savings that they can access from their own computers. They are also continually trying to find ways to outpace and outperform their competitors.
This approach forces Capital One 360 to continually improve their business functions in order to get a step ahead of competitors. Layout and design for Both companies is incredibly different. Dezurik, being a pure manufacturing company, has their main office, and they also have a large warehouse where they manufacture their valves. The front office of Dezurik is rather old. This works for them because they don’t necessarily need to keep up with the newest, up-to-date technology to make their valves. Instead of investing money into their office, they have spent more of their money investing into newer, more efficient machines in their warehouse. They have also changed some of their design to allow for a more efficient production process. They run a pull process at Dezurik. At one end of the plant, they take in all of their supplies.
The supplies then get put into an inventory rack until they are needed. The supplies are then distributed throughout the factory to where they are assembled. The first area you walk into from the supply area is where all of the standardized valves are made. They have multiple stations where one person is running about four machines constantly. These are very efficient. This is because they have outsourced the production of their standard valves to China for manufacturing. The next segment of the plant is made up of several assembly lines that produce other varieties of products. The other side of the warehouse is where all of the large valves are made. They are made here because they typically are too large to be moved across the entire plant. This end of the warehouse is also where their products get painted.
The paint booths are strategically placed at the end of the assembly lines so that as soon as the products are manufactured, they can be painted. They then get sent off to testing. All the valves they make are tested to ensure that the product can withstand the pressures of daily use for years. After the products are tested, they are either loaded onto trucks and sent off, or put into the warehouse until they are needed. Capital One 360 has a completely different layout than Dezurik. To start out, They are in a very modern building located right in the middle of downtown St. Cloud. When walking in the door of Capital One 360, the first thing you will notice is that you are in an ultra-modern café. Since Capital One 360 doesn’t have physical banking locations, the cafes are the closest thing that people can get.
These cafes are not just for a cup of coffee either, the people who work at these cafes are a highly knowledgeable sales associate who can make you a latte and sell you a checking account at the same time. This is for people who are either curious, or just not as comfortable with starting a new bank account online. Once past the café, Capital One 360 pretty much looks like almost every other office building except for a few key features. The first is that All the departments are located separate from each other. Sales is located on one floor, while fraud protection is located on another floor. Capital One 360 also has an interesting layout design. The cubicles are very different from your traditional office building.
To start, they run diagonally across the entire floor. They also are much shorter than a normal cubicle. This is so people can locate each other without having to walk across the office to find out they are not there. They also are not enclosed. This promotes an open workspace that allows people to communicate information quickly and efficiently. Another interesting aspect is that they only have about 60 percent of their office filled with employees. This is so that they can grow and add on employees at any time. The new employees can start and have their own functional workspace instantly.
Capital One 360 also has a central command area located right in the middle of the office. This is where security works. Also this command center has TV monitors that are linked up with their other offices around the country. This feature is so they all can be working together with their offices all around the country. If something happens at their Delaware office, they can get it verified by their office in St. Cloud.
Capacity planning within Capital One 360 and Dezurik are decisions that depend tremendously upon forecasts of demand. These forecasts determine the size of current and future capacity needs. Capital One 360 recently put their capacity planning into effect when they purchased ING Direct and moved into a new building downtown St. Cloud. Capital One 360 made the choice to expand now enabling it to meet customer demand not only for now, but also in the future. If Capital One 360 planned its capacity incorrectly, they may find that they don’t have enough output capability to meet customer demands, or has too much capacity sitting idle. Capital One 360’s move into the new building required long-term commitments and expensive resources.
This move of purchasing a new building came in anticipation of greater demand from their customers. To measure Capital One 360’s capacity, you need the amount of available capacity and the effectiveness of capacity use. From our tour of Capital One 360, we determined that their capacity was operating at an efficient level. When examining Dezurik’s capacity planning, we looked at their recent expansion. In 2011, Dezurik acquired two water and wastewater brands and then in 2012 Dezurik acquired a valve company. This tells us that Dezurik is expanding to meet customer demands in the future. These recent acquires to Dezurik increases capacity and allows them to meet customer demands as well as sales.
We can reasonably measure Dezurik’s capacity by measuring their input, which is labor hours, with their output, which are valves per shift. However this is not a very effective method to measure capacity because Dezurik produces many types of valves. We believe that Dezurik is having success because of its focused factory that responds more efficiently to demand. In todays’ world, large factories need to be more flexible and focused, and from the tour, we believe Dezurik is doing a good job of staying agile within the industry.
This will help Dezurik identify long-term capacity requirements in their forecasts of future demand. In Dezuriks planning for capacity, they have strategic and tactical decisions. Their strategic decisions consist of what investments in new machines and equipment it should make, and by the looks of it, they are investing in new machines that increase automation and decrease manual labor. Their tactical decisions consist of planning their workforce, inventories, and day-to-day use of machines. From the tour, we learned that some of the new machines run 24 hours a day. Dezurik and Capital One 360 have similarities in their capacity planning, that being that they are both preparing for long-term and high customer demands in the future.
Let’s look at some of the strengths of Dezurik. The first strength is that they make a high quality product. Also, they have a very efficient production process for their standardized products. Another pro for Dezurik is they are working hard to become more efficient. They are implementing all sorts of new machines to help speed up and improve the manufacturing process. There are multiple weaknesses that plague Dezurik. To start, they are not an efficient company. This is mainly due to the poor layout of their production area.
A second weakness is that they have begun to outsource some of their products to China. This can be a negative because if they get a bad shipment, it can take over 6 weeks to be corrected. This could become a huge problem if they get the wrong product sent multiple times. There are a few opportunities that Dezurik can expand into. For starters, they are putting in a new paint booth. This will help cut down on time. Before, they outsourced their paint of some products to a place in Alexandria. This means that the product had to leave and come back before it can be shipped out.
They are also making their assembly line more efficient which will really help them improve the speed at which they can produce valves. Dezurik does have some threats that they have to deal with looking into the future. The biggest threat will be imports from China and other places. These places have very low labor costs, and they also don’t have the same environmental regulations that we do. This means that they are able to produce similar products at a much cheaper price. The only flaw is that these products also tend to be of a much lower quality. This is why Dezurik has not been highly affected by this threat. Capital One 360 has multiple strengths as well. The first is they are incredible efficient.
By not using any paper, they are able to cut down on the amount of waste that they have. No physical banks helps to cut down on their carbon footprint too. Second, by utilizing standardization, they are able to run a very lean company. These strengths can also be some of their weaknesses. Having no locations means that people have to do all of their banking online, or over the phone. They cannot go to the bank to talk to a person, rather they have to call into their customer service lines and do all of their problem solving over the phone. There are some opportunities that Capital One 360 has that they are taking advantage of. They are targeting the younger generation. This is because they are appealing to the tech savvy crowd.
They younger generation tends to be more familiar with technology. They will be able to expand into this younger generation, and this is where their greatest opportunity will lie. In the world of banking, there are threats all over the place. For starters, all the banks are going to online banking. Most of these banks also have physical locations that people can go to when they have questions. Also, you will tend to be more of a number at Capital One 360. At the smaller banks, people will know you by name, and the service will be more personal. If Capital One 360 can deal with these threats, they will be able to succeed in a threat filled environment.
There are a few recommendations that could be made for both Dezurik and Capital One 360. To Start with Dezurik, we would recommend that they make some serious improvements to their factory layout. They should be able to take the supplies right off the truck and instantly put them into production. They could implement a better JIT strategy. They are doing a good job of spreading their business around the world. We would also recommend that Dezurik should go paperless. Its more sustainable, and it would help them to move towards and electronic inventory system. This would speed up their order processing time, and make them more efficient. For Capital One 360, we would recommend that they begin to open more cafes around the United States.
These are a tangible part of Capital One 360 that consumers can actually go. Also, they could provide their users with more banking options. Giving their customers banking options can be key in making them feel like they are more than just a number to Capital One 360.
In Conclusion, Both Dezurik and Capital One 360 are both leaders in their respective industries. Dezurik, being a purely manufacturing company, is run completely different from Capital One 360. Being a bank, Capital One focuses their efforts on its services. This means they are more frequently talking to consumers while providing them with a service. Dezurik focuses its efforts on their manufacturing operations. Both companies compare and contrast greatly in relation to various operational elements. Overall, these are two strong companies that are innovative and leading the way in their respective fields.
Cite this Page
Compare and Contrast: Capital One 360 to Dezurik. (2016, Jul 15). Retrieved from https://phdessay.com/compare-and-contrast-capital-one-360-to-dezurik/
Run a free check or have your essay done for you
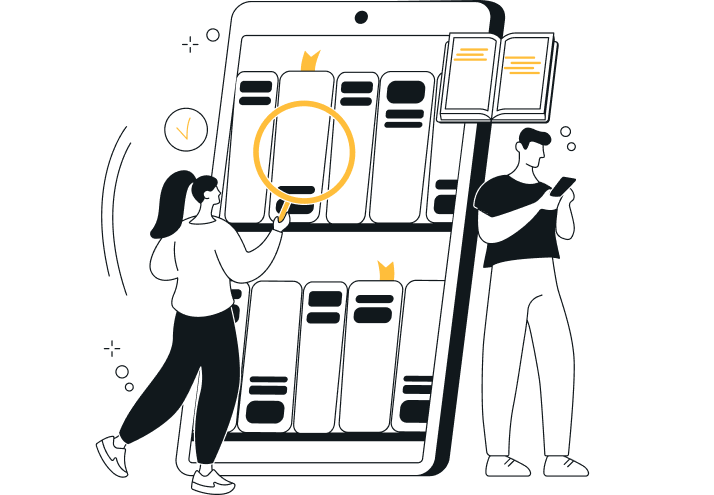