Bridgeton Industries Case
The dynamics of the automobile industry have been very volatile in the last few decades, and the case depicts how the changing environment has affected the Bridgestone Industries. The Bridgestone Industries is a supplier of components and parts for the three main automobile manufacturing companies in the United States. The increase in the fuel prices as well as the technological evolution and the ease of availability of cheaper, cost efficient imported European and Japanese automobiles have taken a significant section of the demand from the US based manufacturers.
As a result there is less demand for products and components from the Bridgestone Industries who are facing low volume of sales and therefore low profitability. In addition to this the increasing costs and overheads in the company are aggravating the cost position of the Bridgestone Industries by decreasing the profit margins per sale. The paper provides an analysis of the cost position of the Bridgestone Industries and the overheads associated with the production lines being manufactured by Bridgestone Industries at the ACF.
Order custom essay Bridgeton Industries Case with free plagiarism report
The overhead burden rate for the company is determined to be 437% in 1988, 434% in 1989, 577% in 1989 and 562% in 1990. A budget is also drafted for the year 1991 which considers outsourcing the manifold production line. The budget has depicted that through the outsourcing of the manifold production line significant cost savings in the expenses for direct labor, direct material and the overheads can be achieved which can result in the lowered overhead burden rate of 307% only.
As a result it is proposed that the Bridgestone Industries should seek to outsource the manifold production line as it can be highly advantageous for the cost position of the company. Bridgeton Industries Case Overview of Bridgeton Industries The Harvard Business review case depicts the problems that were faced by the Bridgeton Industries due to technological evolution, changes in the internal and external environments of the businesses and the changing consumer preferences for automobiles. The company Bridgeton Industries is a major supplier of the complements of the parts and components for the United States automotive industry.
The automotive component and fabrication plant in question in this case was originally founded in 1840 but was acquired by the Bridgeton Industries in the early 1900s. Since then the plant was used to manufacture complements for the main automotive manufacturers in the region. However increasing costs of manufacturing the components and increasing overhead costs caused the plant to shut down. The products that were mainly manufactured by the Bridgeton Industries pertained to components of automobiles that were required by the main manufacturers of automobiles in the industry.
The main product lines that were manufactured at the automotive component and fabrication plant by the Bridgeton Industries for its customers included fuel tanks for automobiles, stainless steel exhaust manifolds, the front and rear doors of the automobiles, the muffler exhaust systems for the cars as well as the steel oil pans that are incorporated in manufacturing an automobile. These products were custom made according to the requirements of the customers in the United States market for automobile manufactures only.
The target market of the Bridgeton Industries included the three main bid automobile manufactures that operated in the United States. These automobile manufacturers had a large percentage of the market share of the US automobile market and therefore consumed almost the entire production generated by the automotive component and fabrication plant by Bridgeton Industries. The nature of the business at the Bridgeton Industries was such that a business to business customer/ client model was adopted by the company as the customers of the products manufactured by the Bridgeton Industries were not the end users of the products.
The case presents that the Bridgeton Industries was a highly successful manufacture of components and the automotive component and fabrication plant churned out components and products under the product lines of fuel tanks, exhaust manifolds, doors, mufflers and exhausts as well as oil plans that were entirely purchased by the three big manufactures of the automobiles in the country. However with the advent of the Japanese car manufactures in the United States, the company was forced to operate at reduced costs in order to be effici9nt and appeal to the changing markets.
Despite the changes that were made to control the costs and stream line operations in the plant, the automotive component and fabrication plant was shut down as it was reporting incrementally increasing overhead levels that could not be contained regardless of the effort put into managing the overheads. This case analysis how the company fared and what initiatives could have been taken to better manage the overheads to reduce costs and make the automotive component and fabrication plant more cost effective. Cost Position Evolution
The cost position of the company has developed over the time of its operations due to the internal as well as the external factors that include the demand for automobiles and how much the customers are willing to pay for them in the market. The changing requirements of the customers for cheaper and more affordable cars that provided high mileage increased in the 1970s in the US automobile industry and this impacted the cost bearing capability of the automobile manufacturers. These manufacturers in turn started purchasing the components at cheaper costs.
This meant that companies like the Bridgeton Industries that were in the business of making components and parts for the big three manufacturers in the United States in the 1970s and 1980s were faced with the challenge of reducing their cost of production and operations in order to be more affective. The strategy was adopted by the Bridgeton Industries to reduce the value and the volume of the overheads that existed for the manufacture of the product lines of fuel tanks, exhaust manifolds, doors, mufflers and exhausts as well as oil plans in order to reduce the costs associated with operations.
This strategy was focused on reducing the cost in order to increase the margin on the sales made to the big three automobile manufacturers in the market for increased profitability to sustain operations of the Bridgeton Industries The Bridgeton Industries underwent significant changes and evolution in its cost positions. The company first wrote off the physical machinery, the equipment and the buildings from the automotive component and fabrication plant’s financial books to reduce the costs associated with the depreciation expenses for these items.
Then the company employed the costing strategy for its product lines that was based on the three elements of materials, direct labor, and overheads. The research undertaken to determine the high levels of costs at the Bridgeton Industries and the factors contributing to these costs provided that the overhead burden was one of the main factors that was forcing the automotive component and fabrication plant to be least cost effective when it came to generating profit. The results provided that the overhead burden existed on a ratio of 435 percent of the direct labor cost (Patricia & Cooper, 1993).
This was a significant percentage of the total costs being attributed as an expense for overheads which was forcing Bridgestone Industries into a negative cost position with its customers. The cost position evolution saw that the Bridgestone Industries were gradually facing increasing costs in the form of incremental overhead expenses, increasing spend on the manufacture and processing of the product lines as well as the costs associated with the management and the operation of the automotive component and fabrication plant.
This decreased the appeal of the products being produced at high costs for the customers of the Bridgestone Industries which forced the Bridgestone Industries to reduce shut down the automotive component and fabrication plant as it was continuously depicting increasing costs that reduced the profit margins for the Bridgestone Industries on the products that its sold to the big three automobile manufactures in the Unites States automobile industry.
Internal and External Factors Effecting the Cost Position The increased imports of the European as well as the Japanese make of automobiles in the United States significantly impacted the demand of the automobiles manufactured by the US manufacturers. “Imports of sub-compact cars from Europe and Japan rose steadily in the 1950s, often as families’ second cars but US manufacturers retained their hold on the lucrative markets for larger vehicles.
” (French, 1997, p142) The US manufactures saw their market shrink as the more aware and price conscious consumers shifted to the European and Japanese counter parts for their automobiles, while the US manufacturers were left with making large, excessive fuel consuming vehicles that denoted social status and personal style.
Aside from this the increasing prices of crude oil in the international market in the 1970s also significantly changed the demand of the automobiles as depicted by the consumers. “A crisis in the US car-market developed as a result of sudden unforeseen shifts in the general environment which allowed overseas producers to expand market share rapidly. New car sales faltered in the 1970s and excess capacity increased.
At the same time the leap in fuel prices shifted the consumer preference towards smaller, more fuel efficient cars which Japanese and European makers already supplied in their domestic markets and were better able to produce that were the US manufacturers used to making larger, more up-market ‘gas-guzzlers’” (French, 1997, p142) The automobiles of French and Japanese make were smaller, more fuel efficient as well as more stylish yet cheaper than the those manufactured by the big three US automobile manufactures.
As a result the consumers opted for purchasing the imported cars instead of those manufactured by the Unites States manufacturers. The recession of the 1970s also further reduced the disposal income and the propensity to save for the people in the United States which made purchasing the imported European and Japanese models of automobiles much more attractive to the consumers instead of opting for those models manufactured by the big three US automobile manufacturers.
In the same period the perception of the consumers also significantly changed as was marked by the baby boomer generation and the hippy era. In this period, the consumer became more aware of the environment, the increasing pollution and the contribution that automobiles made towards adding to the pollution levels. As a result the consumers started to look for cheaper alternatives of travel and those which were more environmental friendly that the vehicles manufactured by the big three US automobile manufacturers.
The internal factors that contributed to the changing cost position of the Bridgestone Industries, specifically at the plant pertained to the decreasing demand of the US manufactured cars and increased demand for cheaper cars that was reflected un the restricting cost based purchases being made by the big three manufactures form the Bridgestone Industries.
As the volume of sales decreased for Bridgestone Industries, along with the margin for profits on sales made due to the rising overhead costs the cost position of the Bridgestone Industries significantly changed to become negative and resulted in the closing of the automotive component and fabrication facility by the Bridgestone Industries. Overhead Burden Rate The Bridgestone Industries had a specific method for determining the overhead burden rate for the products that was proposed and set on an annual basis.
“The budgeted unit costs provided by the plant for the 1987 model year study included overhead (burden) applied to products as a percentage of direct labor dollar cost. The overhead percentage was calculated at the budget time and used throughout the model year to allocate overhead to products using a single overhead pool. The overhead rate used in the study was 435% of direct labor cost” (Patricia & Cooper, 1993)
Cite this Page
Bridgeton Industries Case. (2016, Aug 04). Retrieved from https://phdessay.com/bridgeton-industries-case/
Run a free check or have your essay done for you
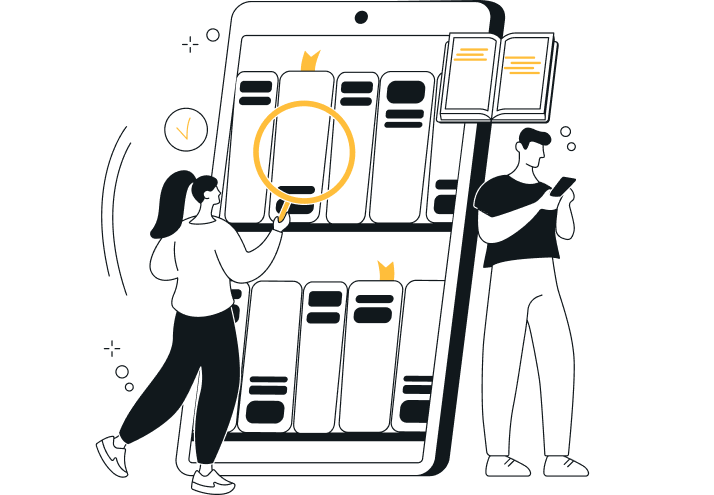