Materials Management Proposal
Materials and operations management play a crucial role in the success of any organization. Of particular importance to the materials and operations divisions is management’s complete understanding of the hospitals functions as a whole entity. After reading this paper, one will understand the importance of materials management and operations management as well as how both departments must work together to ensure the hospital runs efficiently and maintains profitability.
Furthermore, one will also understand the importance of a supply chain and possible constraints to the implementation of the process. Additionally, one will understand the effects of a new collaborative planning process and why such a process is beneficial to the hospital. Finally, suggestions will be given to enable the hospital to manage the supply chain in situations of disaster. Role of Materials and Operations Management Materials management is perhaps the most important part of health care as "total expenditures can total nearly 50% of a hospital's budget" (Langabeer, 2008, p. 41).
Materials managers are held responsible for many functions. However, the most important attribute a materials manager must possess is coordination. “Materials management directs the healthcare supply chain by coordinating the flow of goods from manufacturers, through distributors, through hospital receiving docks, to the point of ultimate use or consumption” (Langabeer, 2008, p. 242). Operations management is another important function of a hospital. Healthcare operations management is the quantitative management of the supporting business systems and processes that transform resources (or inputs) into healthcare services (outputs)” (Langabeer, 2008, p. 6).
Order custom essay Materials Management Proposal with free plagiarism report
Just as materials managers have many functions and goals, so too do operations managers. Key functions of the operations manager include “workflow, physical layout, capacity design, physical network optimization, staffing levels, productivity management, supply chain and logistics management, quality management, and process engineering” (Langabeer, 2008, p. ). Goals of the operations manager include reducing costs, reducing variability and improving logistics flow, improving productivity, improving the quality of customer service, and continuously improving business processes (Langabeer, 2008). However, the most important goal operations managers must strongly consider when implementing a materials management plan is reducing costs. Operations managers have many opportunities to reduce costs.
Costs can be reduced by analyzing budgets, tracking resources, and finding ways to reduce product and services costs. “Finding waste, improving utilization, and generally stabilizing and reducing the overall cost of delivering services are essential functions” (Langabeer, 2008, p. 9). The most effective way for operations managers to reduce costs is to record all aspects of the organization and periodically review progress either monthly or quarterly. A hospital with appropriate tracking and management systems will be much more likely to reduce costs because it understands the underlying cost structure” (Langabeer, 2008, p. 9). A few ways materials management influences operations management are as follows: "the nature of the activities" in the materials management department "is actually quite operational, they have an impact on downstream departments and patient satisfaction, they are labor-intensive processes, and many times they draw from the same labor talent pool" (Langabeer, 2008, p. 244).
Constraints to the Supply Chain Constraints are inevitable and every organization is prone to them whether the organization is in the manufacturing sector or service sector. A few constraints hospitals face include “managing supply levels, higher labor costs, space constraints, and multiple product classifications” (Sentient Health, 2007). Considering the above constraints, the main goal of both operations and materials managers is to reduce costs. The most beneficial way for hospitals to overcome constraints as well as reduce costs is to automate the supply chain. Supply automation is the use of technology to streamline inventory, consumption, charging and ordering procedures. Examples of this include the use of bar codes or radio frequency identification to identify and track inventory as it moves throughout the supply chain” (Sentient Health, 2007, p. 2). However before implementation can begin, the hospital must evaluate the advantages of automation as well as the factors the hospital must consider when deciding to implement such a system.
According to Sentient Health (2007), the advantages of automation include “reduced manual effort, greater information accuracy, improved inventory performance, improved cash flow, improved space utilization, and improved purchasing decisions” (p. 3). While understanding the benefits of such a system is important to the process, knowing which areas the system will have an effect on is detrimental to the hospitals implementation success.
Factors to consider before implementing such a system include “mobility, ease of use, cost/budget/objectives, flexibility/ease of integration, and reporting” (Sentient Health, 2007, p. 3). Effects and Justification of a New Collaborative Planning Process Although automation is one option for the hospital to reduce costs and improve supply chains, other options such as sales and operations planning (S&OP) and collaborative planning, forecasting, and replenishment (CPFR).
The main focus of S&OP is to coordinate demand and supply with the intention of increasing the hospital’s profitability (Langabeer, 2008). To ensure the S&OP process is successful, the hospitals operations management must focus on four key principles: (1) provide a common base of information around the immediate market dynamics; (2) manage supply chain performance; (3) manage product portfolios collaboratively; and (4) create business plans and scenarios in which departments can share.
According to Langabeer (2008), “benefits from the S&OP process include better cross-functional alignment, gap analysis, more efficient resource planning, and more effective use of promotional resources” (p. 338). CPFR is another option available to the hospital. “CPFR seeks to improve the relationship between retailers and suppliers with the intent to achieve full collaboration and improve the sharing of information around consumer point-of-sales data through the retail supply chain to improve overall chain performance” (Langabeer, 2008, p. 338).
The main difference between CPFR and the other two options available to reduce costs and improve supply chains is a set of guidelines operations managers must follow during implementation. The guidelines are as follows: (1) share a common philosophy among all parties of implementation; (2) operations managers must use specific definitions and detail into the business process; (3) operations managers must ensure data resulting from the process is precise, easily accessible, and understood completely by all parties taking part in the process.
Finally, for CPFR to be successful, milestones must be set. Particular milestones of importance to the hospital “include an improvement in forecasting accuracy, improvements in customer service levels or fill rates to providers, increased product line availability, reduction of inventory levels, and generally better financial cash flows” (Langabeer, 2008, p. 340-341). Coping in a Disaster Situation
Disaster situations are difficult to plan for because disasters are unpredictable. However, materials and operations managers must understand the implications a disaster situation has on the hospital as well as ways to effectively handle such a situation to ensure patient safety, customer satisfaction, and profitability remain a priority. Richey (2009) refers to a pyramid when discussing supply chains in disaster situations.
The composition of the pyramid includes the following tiers: capstone-resource management; left-facing front corner-collaboration, which is based on the relationship management theory; right-facing front corner-communication, which is based on communication theory; and back corner-contingency planning, which is based on the competing values theory. According to Richey (2009, p. 621), he interconnection” of the above principles include “(1) finding ways to effectively partner and develop improving collaborative relationships built of long-term commitment; (2) fostering information development and exchange for facilitating strategic planning based in limited safeguarding; and (3) developing contingency programs that incorporate the flexibility for responding to the inevitable changes in expected events while pursuing sometimes inconsistent goals.
Conclusion Materials and operations management work hand-in-hand to ensure the hospital runs as efficiently as possible. Furthermore, understanding all aspects of the supply chain will ensure materials and operations managers are readily equipped to deal with situations of disaster. However, operations and materials managers must understand the importance of such a concept. Understanding how to handle such a situation will ensure materials and operations managers the ability to maintain order as well as patient safety and continued profitability.
Cite this Page
Materials Management Proposal. (2017, Mar 21). Retrieved from https://phdessay.com/materials-management-proposal/
Run a free check or have your essay done for you
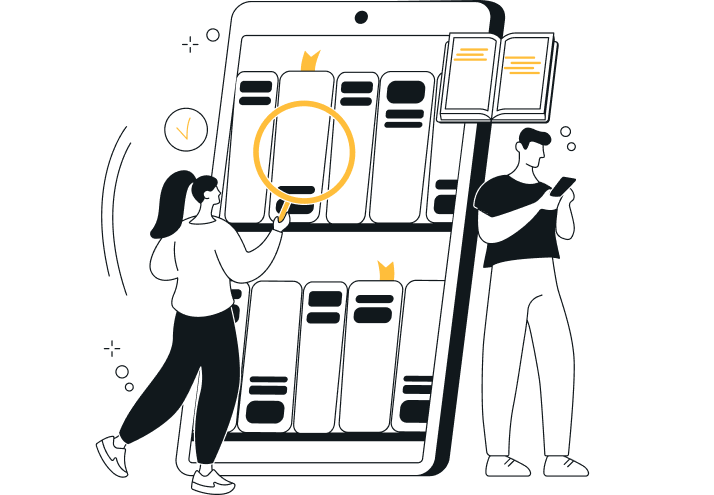