Lean Thinking Model and Its’ Positive Effects on Manufacturing Processes
Running Head: Lean Thinking Model Lean Thinking Model and its' Positive Effects on Manufacturing Processes June 11, 2009 Table of Contents Introduction4 Steps of the Lean Manufacturing Process5 Step 1:Identify the Value to Customers in Specific Products and Services5 Step 2:Identify the Business Processes the Delivers this Value to Customers8 Step 3:Organize Work Arrangements around the Flow of the Business Process8 Step 4:Create a Pull System that Responds to Customer Demands9 Step 5:Continuously Pursue Perfection in the Business Process10 Summary12
References14 Abstract The lean thinking model has many positive effects on the manufacturing process. The model aids companies in the significant reduction of both human and natural resources by removing waste from all aspects of the manufacturing process. Establishing sound processes will in turn help to eliminate waste in production, workforce, and management resources. The lean thinking model is a process with multiple steps involved to ensure effectiveness for a company.
These steps are guidelines that do not fit every organization exactly since there are so many differences between businesses. The function of lean is to seek and find the value of your business. This process will determine the customer’s needs, allow for the removal of non-value added functions and tasks, and materials to become a lean business machine. Henry Ford and the Toyota Company depict an example of the lean thinking model. They invented, re-invented, and added to the lean thinking model over the years and have demonstrated that the model does elp create an efficient business. Introduction The Lean Thinking Model (or lean) falls directly in line with expectations of customers needs for a particular product line by totally reducing excess waste out of the process. A company using lean must optimize the flow of production processes in order to make it cost effective and an efficient process. The philosophy of lean is to remove all waste in the manufacturing process, provide reasonable pricing to the customer, which in turn will result in company profits and stability.
Order custom essay Lean Thinking Model and Its’ Positive Effects on Manufacturing Processes with free plagiarism report
Toyota is the forerunner of the Lean manufacturing process and has been utilizing, improving and perfecting this method since 1902 (Becker, 2009). Toyota’s hourly wage including benefits such as health care and pensions plans is significantly less in comparison to their other competitors. Toyota’s rate is $48. 00 dollars an hour where GM’s rate is $69. 00 dollars an hour (Hirschfeld Davis, 2008). With both the current economic crisis and government bailouts, some of Toyota’s automobile competitors obviously did not follow the lean manufacturing process. Therefore, Toyota is one of the top automobile companies today.
The Toyota Production System is credited for Toyota because of their “sustained leadership in manufacturing performance” (Johnsoton, 2001). Toyota has adapted to changes within the automobile industry with excellence. They drive towards “continuously improving the micro levels of manufacturing processes through identification and systematic reduction or elimination of non-value adding activities” (Sullivan, 2008). Dennis Sowards stated it very well when he said, “For lean construction to be truly successful, it requires a cultural change in the company, not a few random uses” (Sowards, 2009).
Not only must a company participate in a cultural change, they must develop a plan to change their processes and their way of thinking. Company programs lacking support and participation from employees’ typically are unsuccessful. There are five management steps contained within the Lean Thinking Model. This management step approach works well when applied to organize a company’s resources such as equipment and personnel. These resources are incorporated “…around the flow of business processes…” and the products are “…pulled through this process in response to customer orders” (Garrison et al. , 2008, p. 13).
A company will see many benefits from this process, which could include “lower inventories, fewer defects, less wasted effort, and quicker customer response times” (Garrison et al. , 2008, p. 13). Shown below are the five lean steps along with descriptions of each demonstrating the significant of how these steps contribute to the success of a company. Steps of the Lean Manufacturing Process Step 1:Identify the Value to Customers in Specific Products and Services In order to sustain business, a company must identify what the customer values in a product and service which will bring that customer back to buy again.
A prime example where customers were disappointed by a product change is when the Coca Cola Company© released their new product called The New Coke©. This occurred in 1985 after the Coca Cola Company© researched and marketed a new product formula, which they initially intended to replace their orginal Coca Cola© Classic formula. Have you seen New Coke© product invending machines or on the grocery shelves anywhere today? No. Because customers hated the new product and wanted their original Coca Cola© back.
The Coca Cola© company did not find out what their customer wanted prior to changing their formula and their customers were highly offended. Lessons learned: The organization found out very quickly that their customer found absolutely no value in their new product. Coca Cola Company© spent four hundred million dollars for research, development and marketing of the new formula (Unknown, 2009). After 87 days of bad press, customer letters and phone calls with complaints against the new formula, the Coca Cola© Company pulled the New Coke© product off the shelves (Unknown, 2009). The organization could have prevented this issue.
They could have sent out Coca Cola© samples to millions of customers rather than the initial two hundred thousand of taste testers (Unknown, 2009). The reason for this anology is that the target group of Coca Cola© lovers is in the millions, not in the thousands. To keep prices as low as possible, and create a sustainable competitive advantage, waste must be removed from the manufacturing process (Baker, 2006). This includes the office worker who wastes time with two hours of cooler talk, the shop worker who is standing idley by waiting for the production line to gear back up, or there are missing steps to the design flow process.
For an organization to be lean, the idea must be implemented from top down, not from the bottom up. It must include support from all levels. When individuals are standing around and others are working excessively, there is an imbalance in the work flow process which could be corrected by implementing cross-training throughout various departments (Baker, 2006). Part of the waste reduction process is identifying all pocesses or business elements that create waste and then modifying them to reduce that waste.
Most organizations think that the lean process is to clean and organize an office, for example, or shift personnel around without any thought to reduce non-value added functions. By pulling out those steps that do not add value from the customers point of view and by removing waste, a company may just have a sustainable product on their hands (Baker, 2006). A business that understands the customer’s values will be able to provide that customer with a product that they need. Remember, the lines of communication must remain open. Customer’s feedback for products is extremely important.
The customer feedback provides an invaluable tool to maintain existing quality and steps to improve a product line if needed. The customer interaction is a part of the lean process. This step in the lean process takes constant maintenance and interaction between both parties on regular bases (Baker, 2006). Company’s that value their customer opinions helps the organization improve product lines, reduce waste, and adds value for success. What causes a customer to remain loyal to a particular brand and purchase it repeatedly? It is often that a customer finds value in a specific brand name, not just the item.
For instance, some people will only wear Nike© tennis shoes, this is specific brand loyalty. The value of a reasonable priced item is typically a good second indicator, but not always. Product price versus the quality of the product is another comparison the customers will make prior to buying. It has been my personnel experience that a cheaper product of lesser quality will often need to replaced because it worn out too soon. If the quality of the product lasts as long as the customer feels it should based on the price of the item, then when it is time to replace it, they are more likely to venture back to the same brand.
What the customer values in a particular product must be identified to meet their budgets need and keep them coming back as a repeat customer for the company. Customer loyalty is free advertising for the manufacturer. When customers are happy about the products or services that they receive from a business, they brag about the product and the organization. Bragging is free advertising of products or services. By acknowledging the value of customer feedback, making the customer feel good while using a particular product, the company may gain a loyal friend for life.
Step 2:Identify the Business Processes the Delivers this Value to Customers After a business identifies what products and services the customer wants, needs and values, their business processes that deliver these products and services must be identified as well (Garrison, et. al, 2008, p 14). The next step is to lean out those processes to make them more efficient. During this step of the lean process, there are no departmental boundaries in the company’s organizational chart when determining what business process will deliver the identified value to the customer (Garrison, et. l, 2008, p 14). This element removes waste from both manufacturing and human resources. This ensures effective processes. Each business department has the opportunity to be lean. Step 3:Organize Work Arrangements around the Flow of the Business Process Effective layout for business flow is essentional to an efficient production line (Sullivan, 2008). The Lean Manufacturing system organizes process and places them in manufacturing cells based on the product that they are creating. The cellular approach takes employees and equipment from departments that were previously separated from one another and places them side-by-side in a work space called a cell” (Garrison, et. al, 2008 p 14). Every aspect from the equipment process line to the employee running the machines is organized in a cell. Training the employees to perform all the steps in their manufacturing cell ensures accurate and consistent skill training. This step ensures that the manufacturing of the product is completed in a sequential manner that follows detailed process steps.
By applying this step, time reduction for an employee in the overall process will take place. For example, the employee would no longer have to run clear across the two-mile plant to obtain the nut for the bolt that was produced in their cell. The bolts and nuts would be in the same cell since it is part of the new process cell. This is a significant cost savings for the company, which is passed directly to the customer. Step 4:Create a Pull System that Responds to Customer Demands Creating a pull system to respond to customer demands starts by a customer placing a product or service order.
A company reduces inventories to bare minimum levels because production will only occur after the customer orders something from the organization. “In an ideal situation the company would only purchase the raw materials needed for each day or shift of operation, with none left at the end of the day and immediately ship the finished goods to the customer” (Garrison, et. al, 2008 p 14). This sometimes can cause a problem. This type of workflow pattern can cause work stoppages because when orders are not coming in, workers are waiting for customer orders to perform work (Garrison, et. al, 2008 p 14).
This problem can be alleviated by ensuring that cross training is conducted with those employees that may have to wait for orders. Just-in-Time (JIT) is another example of a pull system and is used at many large manufacturing companies such as Northrop Grumman, Ford and Toyota. When the JIT System is applied to a manufacturing process, materials are purchased for what is needed, when they are needed, and the quantities produced are based specifically on what customers order. The JIT system made Henry Ford and Toyota famous in their efforts to minimize waste and organize their manufacturing process successfully.
For example, Toyota to this day does not start production on their vehicles until there is an order from a customer for a vehicle. Another excellent example of a company that uses the JIT process is Northrop Grumman Shipbuilding. They are located on the James River in Newport News, Virginia and are the only manufacturer of nuclear aircraft carries for the United States Navy. Northrop Grumman Shipbuilding developed the Nimitz class carrier for the Navy with the famous slogan of 90 tons of steel. The painting of all that steel is amazing to witness.
In 1990, the Northrop Grumman Shipbuilding environmental department estimated the waste paint volume at nearly 60% of the paint purchased. Northrop Grumman Shipbuilding decided that something needed to change to reduce this double cost of extra paint purchased and waste. They began working with paint manufacturers and applied a JIT system with all paint purchases. The paint manufactures signed teaming agreements with Northrop Grumman Shipbuilding to supply all paints JIT. The environmental department estimated a 25% reduction in waste from this JIT application. Only 25% reduction was seen as a great feat, but it was also disturbing.
The environmental department with Northrop Grumman Shipbuilding was concerned that there was not a 60% reduction. This led the company to further investigation of the painting application process. Northrop Grumman Shipbuilding discovered that the paint distribution and application process was the culprit for the missing 35%. Their next lean step after discovering this problem was to eliminate it and they have since created processes to do just that. Step 5:Continuously Pursue Perfection in the Business Process A company must continuously review all aspects of their business in order for it to improve in the pursuit of perfection.
This is not just production line review (Garrison et al. , p. 14). Quality control is a vital attribute in this step as well. Raw materials and parts are inspected for defects, including finished products manufactured in the shop and raw materials received from supplies to produce those products. Business and suppliers must work together to ensure each has a quality program that will enhance their product line, not hurt it with inadequate materials or products. The company’s production workers will inspect a second time since they are directly responsible for spotting defective pieces.
A worker who discovers a defect immediately stops the flow of production and start working on trouble shooting a solution to correct it. Supervisors and other workers in the area will assist in determining the root cause of the problem and correct it before any further defective units are produced (Garrison et al. , p. 14). This way of thinking allows the company to ensure quick problem identification and solutions in their business process. It is not a common philosophy in manufacturing processes where the production line worker can stop the production line because they found an error in a part.
Typically, the worker is required to inform their supervisor, the supervisor will inform the shop production manager and then perhaps senior management all while the production line is still running and generating defective parts. This entire succession of informing all those in the management chain can take hours or even days to accomplish. With lean manufacturing and the Jidoka system, the worker would stop production immediately, resolve the issues before any more defective parts are produced and subsequently scrapped as waste (Brodek, 2009).
A very interesting aspect of lean is that the process relies on those working the deck plate to find defective or wasteful processes and solve the problem. Traditionally, an individual would go up the chain of management and those in upper management would make the corrective action decision. The Jidoka system is a process established by the Japanese that provides front line workers the ability and responsibility to stop the production line immediately when they find a problem (Brodek, 2009). They are then required to alert their fellow workers and problem solves the situation.
If they are inexperienced in this problem solving process, other works or supervision may make suggestions for correction, but not before the individual that stopped the process attempts to solve it. This forces the new employee to acquire learned problem solving skills, which is invaluable in a manufacturing process line. Permanent and perfect solutions are expected result of the Jidoka system. Employees must understand that the Band-Aid approach is not acceptable in correcting company production or process problems.
The entire company must pull together and problem solve, because by using the lean process, repeat defective parts are not acceptable. In 1926, Henry Ford could manufacture a car in four days and at that same time, Toyota and General Motors needed ten weeks to produce just one vehicle. Henry Ford’s Jidoka system vehicle manufacturing process is a great example of how reducing waste worked for Ford. Toyota studied the Ford process and applied lean manufacturing to their processes and reduced their vehicle manufacturing process from ten weeks to just two days (Brodek, 2009).
That is impressive for any company. Another Application for the Lean Thinking Model “The lean thinking model can also be used to improve the business processes that link companies together. The term supply chain management is commonly used to refer to the coordination of business processes across companies to better serve end consumers” (Garrison et al, 2008, p 14). For example, Costco teams with their suppliers to ensure materials and products that they need are available based on customer demand.
Both Costco and the supplier understand that their mutual success is highly dependent upon them working together as a team. Summary The significant benefits of the Lean Manufacturing Model include many different aspects. The first is the reduction of resources, human and natural. By removing waste from work scopes, production lines and management, the company will save money. Another significant benefit is the reduction of time for an employee and a given product on the production line will result in additional cost savings.
By leaning out an organization’s processes, human resources, and materials in the production process, this elimination of non-value added steps would add the benefit of saving the company time and money. Other examples of the reduction in resources used include electricity, natural resources (metal, gas, electricity, and fabric) and personnel. Truly honing in on what the customer wants, needs and values will help create a process that defines those values. This is a key function of lean manufacturing. References Baker, W. H. (2006, May). Profit Online.
Retrieved June 7, 2009, from Five Steps to the Lean Enterprise; creating a sustainable competitive advange: http://www. oracle. com/profit/features/p26lean_3. html Brodek, N. (2009). Mold Making Technology. Retrieved May 13, 20069, from Five Rules to Problem Solving in Your Shop: http://www. moldmakingtechnology. com/articles/010508. html Becker, R. M. (2009). SAE International. Retrieved May 16, 2009, from Lean Manufacturing and the Toyota Production System : http://www. sae. org/manufacturing/lean/column/leanjun01. htm Garrison, R. H. (2008). Managerial Accounting (12th edition).
New York, NY: The McGraw-Hill COmpanies, Inc.. Hirschfeld Davis, J. a. (2008, December 11). USA Today. Retrieved June 7, 2009, from Auto bailout talks collapse in Senate over union wages : http://www. usatoday. com/money/autos/2008-12-10-house-approves-auto-bailout-bill_N. htm Johnsoton, S. J. (2001, November 26). Working Knowledge, Harvard Business School. Retrieved May 13, 2009, from How Toyota Turns Workers Into Problem Solvers: http://hbswk. hbs. edu/item/3512. html Sowards, D. (2009, March 01). snips Magazine. Retrieved May 15, 2009, from Lean and Mean: http://www. nipsmag. com/Articles/Feature_Article/BNP_GUID_9-5-2006_A_10000000000000539426 Frost and Sullivan. (2008, January 3). Frost and Sullivan Market Insite. Retrieved June 7, 2009, from Cellular Manufacturing : http://www. frost. com/prod/servlet/market-insight-print. pag? docid=116843703 (Sullivan, 2008) need to fix this one. The authors are Frost and Sullivan…no first names, but the citation is wrong Unknown. (2009, June 9). Building Brands. Retrieved June 7, 2009, from Cost-effective promotions can build the brand too: http://www. buildingbrands. com/didyouknow/08_new_coke. php
Cite this Page
Lean Thinking Model and Its’ Positive Effects on Manufacturing Processes. (2018, Feb 09). Retrieved from https://phdessay.com/lean-thinking-model-and-its-positive-effects-on-manufacturing-processes/
Run a free check or have your essay done for you
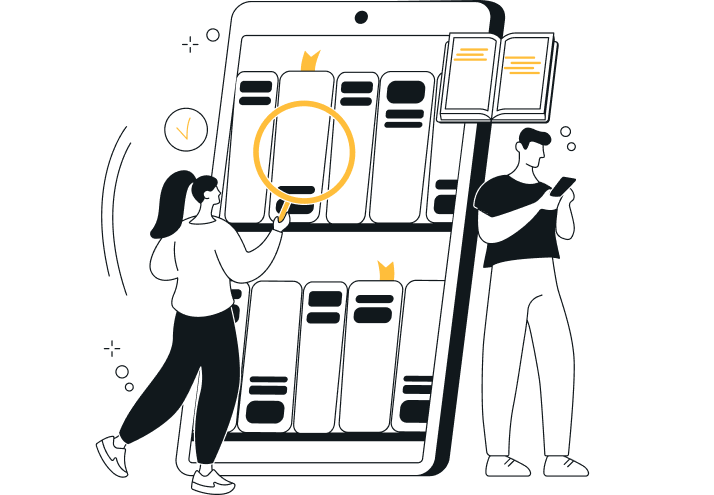