Discussions / Technology & Management Operations
Project management is an essential process that should be applied in operations in a company to ensure success leading to quality improvements. Toyota has practiced project management in most projects or initiatives carried out. In most cases, workers have been encouraged to carryout self tests when carrying out a given duty to ensure product conformity. Toyota Company has carried out various statistical tests such as chi-square, hypothesis tests and came up with multiple regression tests to analyze the fitness of a new brand in the market (Tata Interactive Systems, n. d).
Moreover, Toyota Company has trained its employees regularly to ensure they are the required expertise to achieve a continuous quality improvement in the company translating to improved customer satisfaction and cost efficiency production. TPS has been used as a potential through which improved quality productions can be achieved (Toyota Motor Corporation, 1998). Project Management concepts and their Applications in the workplace Toyota Production Systems (TPS) has been used as a way through which development can be achieved amongst people working in the global manufacturing arena.Toyota motor manufacturing Canada (TMMC) based their management processes on wise decision-making to ensure quality productions and continuous improvements (Johnson, n. d). TMMC has localized most of its operations to ensure increased market reachability and reliability through long-term relationship with its customers leading to increased profitability and market leadership in automobile productions. TMMC has developed strategies through which quality improvements can be achieved in the organization.
Order custom essay Discussions / Technology & Management Operations with free plagiarism report
TMMC has formed joint ventures with other companies to ensure profitability through shared responsibilities leading enhanced competitive advantage and sustainability in the market (Toyota’s driving force Baseline, 2006). TMMC that came up with the TPS as an initiative through which continuous quality production can be achieved in Toyota Company. TPS has been used for restructuring the production processes in the automobile companies leading to increased efficiency and effectiveness (Johnson, n. d).
TMMC has used a just-in-time management system where production patterns are based on specific orders on demand to ensure no wastage of resources through reduced inventories and defects in production (Toyota Motor Corporation, 1998). Just-in-time production management system will be used in the company to eliminate non-value adding processes leading to reduced lead-time and increased customer satisfaction. TPS emphasizes on employee empowerment not necessarily through freedom but also through trainings, collaborations or joint ventures and to facilitate communication amongst stakeholders.
Top management introduced new initiatives to the company upon approval by the internal stakeholders as a way through which the new project can be communicated and made visible in a company. Toyota Company implemented performance metrics through which business operations could be monitored to ensure cost efficiency (Johnson, n. d). In Toyota company, a flexibility system have used that emphasizes on continuous assessment of production operations to identify any defects and therefore find out the necessary remedies in time to avoid wastage of resources leading to improved productions (Toyota Motor Corporation, 1998).
Performance levels have been assessed to ensure the right expertise required for any production is achieved to meet customer requirements. Quality performance standards have been set where workers monitor themselves by comparing quality of their productions with others in the company to ensure it conforms to the required standards (Toyota Motor Corporation, 1998). Workers have been encouraged to respond to presence of an error or defect in a product development phase positively to make the necessary decisions on how to go about it for example by using Six Sigma or multiple regression tests to ensure customer satisfaction.
You have to identify possible causes of a problem, possible consequences and ways through which they can be reduced without incurring a lot of losses. In Toyota Company training is very essential and they consider this as a way through which employee empowerment can be achieved leading to improved productions to ensure success through improved customer satisfaction for example through asking yourself the why questions as you design a system (Toyota Motor Corporation, 1998).
Toyota has encouraged interaction amongst its employees to harmonize the multicultural differences leading to dedicated teamwork towards achieving common company goals. TPS use in the company was aimed at proving a lasting solution to the critical threats in the production or product development life cycle in a cost effective way. Toyota has always carried out customer awareness tests for their products in the market by designing simulated designs and testing for product fitness in the market using a chi-square test (Tata Interactive Systems, n.
d). Toyota has made various versions of simulated designs and carried out numerous regression tests to ensure a product is accepted in the market. The various simulated design versions is a potential way through which customer satisfaction can be easily achieved and in the same way new products will be easily developed through the different versions by simply making little improvements.
Toyota has always carried out different tests such as chi-square in different places in the world to determine the brand fitness in the market depending on how many people are aware of it (Johnson, n. d). Conclusion Toyota is a very successful automobile manufacturing company in the global arena. Toyota has managed well its projects by carrying out different tests based on its products awareness and fitness in the market.
Toyota has carried out multiple regression tests of its new products using simulated product designs developed in the markets to ensure customer satisfaction (Tata Interactive Systems, n. d). Employees have been encouraged to produce as many designs as possible to help them meet customer requirements. The employees are to asks themselves the why questions severally on every design produced that does not meet customer specifications to find possible solutions based on the decision made with the available information collected (Toyota’s driving force Baseline, 2006).
Reference:
Johnson, W.H.A. (n.d.). Toyota Motor Manufacturing Company Canada (TMMC): The
Lexus RX 330 Line. Waltham, MA: Department of Management, Bentley College. [Viewed on 27th June 2009] Available at <http://polaris.umuc.edu/~jstewart/Amba604/TMMCCase_Final.pdf>
Tata Interactive Systems (n.d.). Research methods for managerial decisions. [Viewed on
27th June 2009] Available at <http://info.umuc.edu/mba/public/TIS/statistics/statistics_simulation.html>
Toyota’s driving force Baseline. (2006). [Viewed on 27th June 2009] Available at
<http://www.baselinemag.com/c/a/Past-News/Toyotas-Driving-Force/>
Toyota Motor Corporation. (1998). The Toyota production system. [Viewed on 27th June]
Available at <http://www.toyotageorgetown.com/tps.asp>
Cite this Page
Discussions / Technology & Management Operations. (2016, Aug 22). Retrieved from https://phdessay.com/discussions-technology-management-operations/
Run a free check or have your essay done for you
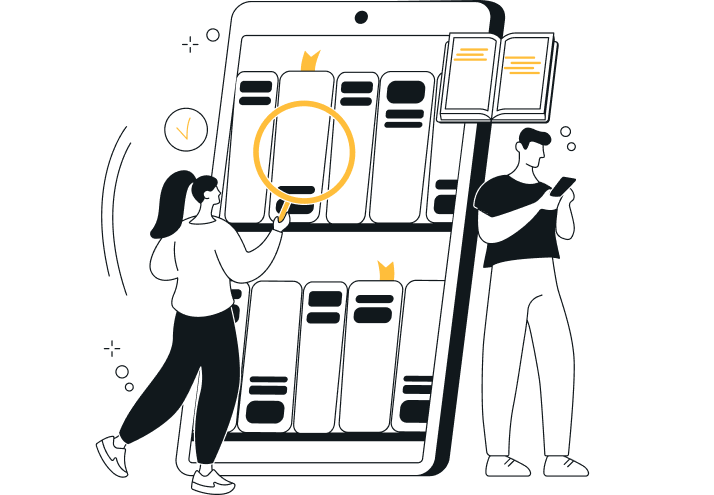