Current Strategy Definition
Dell Computer is, currently, the world's largest manufacturer of personal computers, over companies such as IBM, Toshiba, Compaq or HP with a market share of 14% which continues to grow as a fact in 2008, where despite the recession and the drop in sales of PCs, Dell has overtaken its main competitors on a sales increase of 8%. The objective of this report will be to analyze and evaluate Dell and its procurement, manufacturing, transporting and distribution areas, as well as suggesting a new strategy offering a methodology for process improvement to improve the company results.
In order to carry out the objective of this report, the firm should realize continuing improvements in the planning and estimation of sales to reduce the problems from a sudden increase of demand, setting up "Lean Six Sigma Method" and fulfill the different steps of its implementation. Managing the supply chain, Dell integrates into the company its customers and suppliers, which allows a speedy and flexible management of their supply chain, thus Dell delivers its products in a reliable and very rapid manner, obtaining a competitive edge.
The major difference between Dell and its competitors is that Dell is not dependent on retail outlets to distribute its product. It sells online or by phone, and obtains the competitive edge through its electronic commerce. The chart below shows Dell's production chain process. Internet order Dell's factories are able to produce one computer in less than 4 minutes. After receiving the order from the customer, through an integrated platform that takes the request made by internet or by telephone directly to the factory that night it starts production.
Order custom essay Current Strategy Definition with free plagiarism report
The assembly line for its plant is capable of producing a computer in less than 4 minutes. About the distribution chain process, the device is delivered from the factory through outsourcing companies, the same day of production to distribution points and then straight away to the final customers. I have tried to show the process in the chart below. Taking the order just before the assembly, Dell gets the components which are an average of 60 days newer than those of machines sold by IBM and Hewlett-Packard at the same time.
That may translate into an advantage of a 6% gain in only the components. The strategy of procurement, manufacturing, logistics and distribution has enabled Dell to produce computers that are manufactured according to specifications that gives every customer, either through internet or telephone, a price lower than Dell's competitors. However, the company has still some faults, for instance it has over 10% of delayed deliveries, especially in South America and also some problems with the suppliers. New Strategy for Supply Chain Improvement.
Due to the high level of Dell's efficiency and lack of any method to improvement the process, I propose a new strategy which will try to improve the supply chain based on perfecting the current strategy, plus providing the keys to resolve its main troubles such as supply problems and delivery delay, improving the quality of process outputs by identifying and removing the causes of defects, in order to reduce as much as possible the orders that are not processed in an early manner due to not being detected on time.
The purpose of this strategy is to improve the distribution and transportation process and eliminate the overall process fault. Dell should implement an improvement method, there are many such as Lean Manufacturing or lean Production (LM), Total Productive Maintenance (TPM) or Quick Response Manufacturing (QRM). However, from my point of view the Six Sigma Method is the most appropriate for Dell's needs because Six Sigma seeks to minimize errors and satisfy the customer. Six Sigma is a highly disciplined approach to decision making that helps company focus on improving processes to make them as near perfect as possible.
According to I suggest the Six Sigma DMAIC method to improve an existing business process, the steps to implement the Six Sigma DMAIC methodology are shown in the chart below. In order to reinforce its accomplishments it is most appropriate to combine management with Lean Six Sigma, a methodology that includes tools such as work cell environments, polyvalence, the Kanban or scheduling systems with finite scheduling, flexibility in production and self - quality.
See the chart below. According to Objectives. The main objective is to introduce Lean Six Sigma DMAIC method in a successful manner and apply it to the procurement, manufacturing, transportation and distribution areas in order to achieve the objectives below. Six Sigma is about "solving a problem with an unknown solution. " To unearth the solution, the problem needs to first be defined in concrete measurable terms. 2. Measure
Critical measures that are necessary to evaluate the success of the project are identified and determined. The initial capability and stability of the project is determined in order to establish a measurement baseline. Once the project has a clear definition with a clear measurable set of indicators, the process is studied to determine the Key Process Steps and an operational plan defined to measure the indicators. Once the reasons for input failure are determined, preventative action plans are put into place. 3. Analyze
The team should determine the causes of the problem that needs improvement and how to eliminate the gap between existing performance and the desired level of performance. This involves discovering why defects are generated by identifying the key variables that are most likely to create process variation. 4. Improve This phase is where the process transitions into solutions. Critical inputs have been verified and optimized toward nailing down the problem causes. Once problem causes are determined in the Analyze phase, the team finds, evaluates through testing, and selects creative new improvement solutions.
The team identifies and quantifies what will happen if needed improvements are not made and what will happen if the improvements take too long. 5. Control Success in the Control phase depends upon how well the team did in the previous four phases. The keys are a solid monitoring plan with proper change management methods that identify key stakeholders. The team develops a project hand off process, reaction plans, and training materials to guarantee performance and long-term project savings.
Documenting the project is very important so that the new procedures and lessons learned are maintained and provide concrete examples for the organization. At the close of the Control phase, ownership and knowledge is transferred to the process owner and process team tasked with the responsibilities. Finally, the team identifies what the next steps are for future Six Sigma process improvement opportunities by identifying replication and standardizations opportunities and plans.
The schedule plan advised to Dell new strategy implementation will last 11 months starting on January 2010 and finishing on November of the same year. A provisional Gant Chart is provided to aid in the schedule planning of the project.
Reference List
Walters, D. (2003), Global Logistics and Distribution Planning, strategies for management. UK: Kogan Page Limited. Janice Burn, Peter Marshall and Martin Barnett (2002) E-Business strategies for virtual organizations, UK: Butterworth Heinemann.
Cite this Page
Current Strategy Definition. (2018, Feb 18). Retrieved from https://phdessay.com/current-strategy-definition/
Run a free check or have your essay done for you
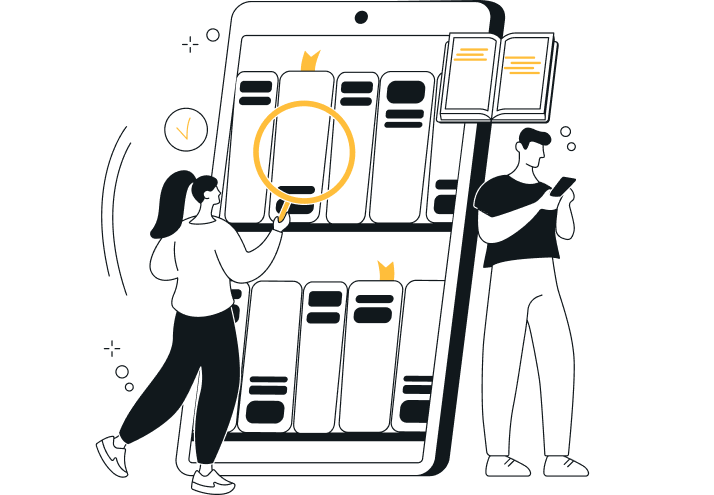