Visual Stream Mapping
Introduction
Lean manufacturing is a production practice that considers the expenditure of resources for any goal other than the creation of value for the end customer to be wasteful, and thus a target for elimination. Working from the perspective of the customer who consumes a product or service, "value" is defined as any action or process that a customer would be willing to pay for. The goal of Lean is to becomes the creation and maintenance of a production system which runs repetitively, day after day, week after week in a manner identical to the previous time period. Lean is actually the set of "tools" that assist in the identification and steady elimination of waste. As waste is eliminated quality improves while production time and cost are reduced. Examples of such "tools" are Value Stream Mapping, 5S, Kanban (pull systems), and poka-yoke (error-proofing).
Visual Stream Mapping (VSM)
Order custom essay Visual Stream Mapping with free plagiarism report
Value stream mapping is a process designed to reduce lead time, to make product flow, and to eliminate waste (non value added operations or activities), all for the purpose of meeting customer demand at the lowest cost, and with the highest quality.
Lean thinking relies on recognizing the “seven wastes” – over-production, over-processing, inventory, motion, scrap, waiting, and transportation. Target maps reveal which of these wastes can be eliminated now, and where. The key to producing useful target maps is to look for low-cost improvements that encourage flow, reduce inventory, and test the organization’s ability to manage in a lean environment. The challenge of developing the attitudes, systems and communication necessary for a true pull system operating at customer takt should not be underestimated.
A high inventory system hides a multitude of problems, which will slowly be exposed as batch sizes and WIP are reduced. The level of organization and standardization required for one-piece flow are rarely found in companies with traditional production planning and traditional management. Visual Stream Mapping can identify wastes such as:
- Over-production. Over-production is the production of material which is not needed now. It usually occurs in the form of large batches, produced faster than the rate at which they can be consumed Over production is caused by a number of factors, such as long setups, poor quality, machine unreliability, avoidance of setups in order to make performance measures look better, or the desire to keep an expensive resource working.
- Over-processing. There are two aspects to this kind of waste which is overdoing it in the sense of doing too much, too soon, and beyond what is necessary and using inappropriate equipment, especially equipment that is much larger, faster, or more complicated than necessary. It can be difficult to distinguish between over-processing and over-production, because the first often leads to the second. Over-processing is usually associated with going beyond what the customer requires. Examples are reports and presentations that have more information than the audience is looking for, and therefore are difficult to understand and act on.
Inventory
Whether in the form of work in process (WIP) or finished goods, inventory is considered the great problem in production. With material always available, the focus is taken away from the process, quality, and the rate of work. Inventory thus actually hides problems that exist in the production system. In addition, inventory has an impact on waste that is indirectly caused by having more than needed. Inventory leads to a lack of attention to the process. This means that processes are designed with cycle times well outside of the average. By buffering the process with inventory, the wide variance in cycle times is not noticed until an attempt is made to set up a continuous flow cell or line.
Transportation
When a facility layout extends over a large area, the movement of inventory from operation to operation becomes necessary. It is thus another result of over-production. It also results from laying out production equipment by function. Functional layout places each type of machine in its own cell for a variety of reasons, mainly to do with the perceived benefits of specialization. 5. Motion Motion is a waste associated with both operators and equipment. In the case of operators, wasted motion includes bending, walking to get or place parts, lifting, and taking more than one step to reach or view machine interfaces. Motion can add significantly to cycle time, and must therefore be considered separately when creating and balancing cells and focused factories. . Scrap Scrap and rework are obviously wasteful. In batch production, scrap is rarely visible, since there is always more material available, and the run can be extended for a short while to produce the required quantity. In a continuous flow system, scrap is a serious problem, since every machine loses a cycle when a piece is rejected. This destroys balance, and when producing to customer takt, results in a missed shipment. 7. Waiting Waiting takes a number of forms. Operators wait for machines to complete their cycle, or for material to arrive so they can work on it. Machines wait for work, and also for operators to load and unload work pieces or other production material. The kinds of waiting that are common in batch production facilities are different from the waiting that is wasteful in a continuous flow system.
Characteristics of VSM
This is an elements that need an observation and a consideration during applying this VSM:
- Recognize where environmental impacts occur in a product line.
- Quantify raw materials used by processes and compare it to materials actually needed to produce the product.
- Identify pollution and wastes generated by the production activities.
- Identify root causes of wastes and inefficiencies. There are a number of common icons used in value stream maps, but icons can also be customized to best serve a value stream map. Icons help distinguish different elements of a product line from another.
Implementation
Once future state map completed a plan to achieve this aim need to be developed, the implementation cannot be done unless there is an actual plan that can vividly visualize the aim of VSM. Without a full blown project implementation with full commitment from everyone in the company you will not reach your future state and gain the identified benefits. The future state map will detail the amount by which your lead times will be reduced, lower stock holdings, potential efficiency improvements and so forth so it should be possible to justify any project financially.
Also known as the Deming Cycle in many circles, Plan, Do, Check, Act is a simple model for improvement, you make your plan, you implement your plan, you check if you have achieved your stated aims and you then act to make any necessary changes. This cycle is repeated over and over again continually driving improvement. This is how you implement your Value Stream Mapping, it is an iterative process, one that you repeat over and over. You make your initial current state map, plan your improvements, then make your improvements.
Then you check your progress by creating a new current state map and plan additional improvements, your value stream mapping should be repeated to ensure continual improvement of your processes. 2. 1 Process of VSM The first action of value stream mapping is to map the existing process which is the result is a Current State Map. Once a valid current state map has been constructed, it is then possible to suggest improvements, with confidence that the results from the proposed system will be quite similar to those of the Future State Map.
In this way, the lean initiative moves from solid footing to solid footing. There is no “leap of faith” or “trust me” required to convince everyone that there really is a better way to carry out the process. 2. 1. 1Current State When reviewing a product or process line, the first value stream map you develop should record the current state of the line. Remember, conventional value stream mapping tends to focus at a facility-wide level. The current state map should take a snapshot of the current practices and materials usage rates for all processes.
A current state map should also record where environmental impacts occur in the product line. Other inputs and outputs that conventional value stream maps identify include changeover and cycle time, labour, and rework. Exhibit 2. 0 illustrates a conventional value stream map, shows how to denote process inputs and outputs may exist in the product line. . 1. 2Compare ‘Use’ Vs ‘Need’ In the past, value stream maps would examine the time it takes to produce a product and the proportion of that time that is value added or the time spent actually working on the product. The timeline was a graphic representation that compared the two, but didn’t focus on the resources consumed and waste generated in making the product. A materials line is a variation of a timeline and can be developed for any type of resource (e. g. , water, energy, total materials, and/or a critical substance used in the product).
A materials line, located on the bottom of a value stream map, shows the amount of raw materials used by each process in the value stream and the amount of materials that end up in the product and add value from a customer’s perspective. For example, the materials line illustrated below in figure 2. 0 compares the amount of water used and needed in the milling and parts washing processes in a product line. Figure 2. 1. 2 Once you collect data for the materials line, you may notice large differences between the amount of material used and the amount needed for the product.
This exercise can help you target the largest sources of waste for prioritizing improvement efforts. Exhibit 2 presents a value stream map with a materials line that focuses on water usage. You can also create separate maps that address other inputs such as hazardous materials or energy use. 2. 1. 3Visualize an Improved “Future State” Future state maps are created to show what a product or process line would look like after improvements are made. Future state maps should be drafted following the completion of a current state map.
Practitioners play a vital role in developing future state maps, as they can help suppliers identify areas where environmental improvements can be made. More often than not, future state maps look closer at process level improvements. Facilities cannot typically make changes to the order in which processes take place in a product line, but they can implement changes to specific steps of a process. Opportunities for process improvement can be shown on a value stream map with a starburst as illustrated in Exhibit 3. Starbursts can identify processes that need to be examined closer, such as in Exhibit 4.
Future state maps should represent the product or process line in a perfect state or fully optimized and highly efficient. It should not be restrained by cost. The future state should include the best available technologies and equipment, and estimated waste reductions should be included where appropriate. For example, if a surface coating line could reduce solvent use by installing a solvent recycler, the future state map should represent that improvement. The materials line that should be included on a current state map can be a good indicator of where improvement opportunities exist.
If a process showed a large difference between the amount of a material used and the amount of material needed, practitioners should question why the difference exists. Inefficiencies are the root cause of most wastes. Efficient production lines will have little to no difference between the amount used compared to the amount actually needed to produce the product. Exhibits 5 and 6 show the difference between a current state and a future state parts washing line. Current and future state process maps can be generated for one or many processes that occur in a facilities product line.
Benefits and Importance of VSM
Value stream mapping is often used at the outset of a lean program to identify the current process within an organization. Strictly speaking Value stream mapping is used to map information and materials through a production process but it can be used for so much more than simply transcribing the process. This is the list of benefits and importance of applying VSM technique:
- It helps portray the process from the start of the production process to the end.
- It help finds bottlenecks and find waste within the process.
- It’s a group exercise and therefore can involve your workforce as part of your lean improvement program.
- You can use a completed value stream map as an improvement aide to document transitions to a future state value stream map.
- It’s an inexpensive tool, basically all you need is a paper and pen.
- It can be easily critiqued by your workforce to highlight problems that exist within the process.
- It’s not just for manufacturing, value stream mapping has been used in offices, service industries healthcare etc.
- It’s easy to understand with a little bit of training on VSM, icons maps are easy to understand conveying powerful process in a simple pictorial fashion.
Conclusion
This study has outlined a decision-making process for the mapping of the value stream or supply chain. This general process is grounded in a contingency approach as it allows the company to choose the most appropriate methods for the particular industry, people and types of problem that exist. The typology is based around the identification of the particular wastes the company or value stream members wish to reduce or eliminate. As such, it allows for an extension of the effective internal waste reduction philosophy pioneered by leading companies such as Toyota. In this case, however, such an approach can be widened and so extended to a value stream setting. This extension capability lies at the heart of creating lean manufacturing, with each of the value stream members working to reduce wasteful activity both inside and between their organizations.
Reference
- http//: EzineArticles. com/225609 2. www. gardinernielsen. com 3.
- www. en. wikipedia. org/wiki/Value_stream_mapping 4. www. greensuppliers. gov/pubs/VSM. pdf
Cite this Page
Visual Stream Mapping. (2017, Dec 05). Retrieved from https://phdessay.com/visual-stream-mapping/
Run a free check or have your essay done for you
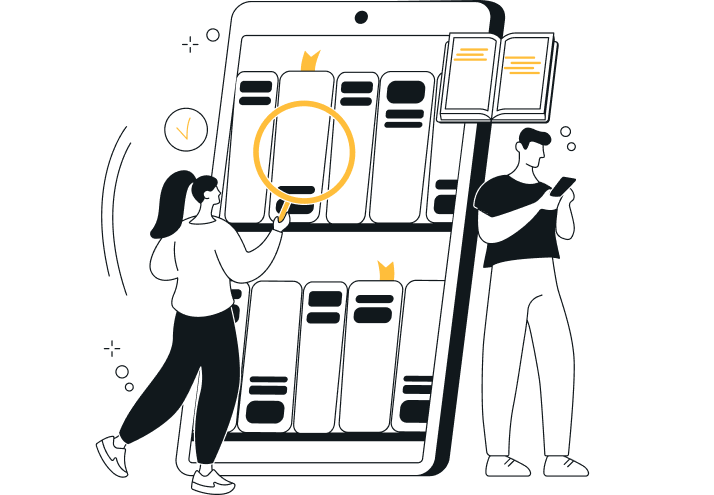