Vendor-Managed Inventory at NIBCO
NIBCO has 100 years history and $ 400 million revenues. The main product is flow control like valves, fitting, and hangers so on. Compare to other same types of manufacturers, NIBCO wants to provide low price and differentiation of flow control products. In these days, the product quality is not only a requirement among the commodity markets. The value-added services also are good ways to attract more customers. However, when NIBCO wants to give value-added services to customers, the old system cannot suit their needs.
The managers of NIBCO decided to use SAP R/3 implementation project, which helps them to deal with issues. From 1998 to 2001, SAP R/3 implementation has run smoothly in NIBCO. As a supply chain business processes, the improvements are both in supply-side and customer-side. The SAP implementation begins a demand-pull system instead of forecast push-system in NIBCO. Further on, NIBCO wants to reduce costs, improve customer satisfaction, and increase revenues. Vendor-managed inventory (VMI) program and a multiple customer service channels were initiated to enhance customer loyalty and increase electronic ordering. Wirelesses scanning for warehouse management and inventory replenishment policies were constantly processed to improve worker productivity and order fulfillment accuracy. Raw material purchase consolidation, followed by supplier-managed inventory pilots results in cost savings practices. Therefore, NIBCO uses vendor-managed inventory (VMI) program to meet their wants. After using this approach, NIBCO builds closer relationship with key customers.
Key Accomplishments
Order custom essay Vendor-Managed Inventory at NIBCO with free plagiarism report
• Increased from 30% to 87% in perfect order rate.
• Enhanced on-time delivery rate from 60% to 99%
• Stock outs decreased from 11% to 2%
• For key customers, decrease in order-to-ship times (from more than 48 hours to 8 hours). • Improvements for the customers with which NIBCO conducts VMI: improved average inventory turns 75% and decreased inventory by 30% to 50%. SAP for supply chain investments along with Just in time (JIT) inventory management system causes reduction in cost. • Decreased in inventory levels from $102 million to $76 million • Inventory turns enhanced by 17% (from 3.66 to 4.27).
• Reduction in administrative costs and annual sales by 19%. • Decreased cost of annual distribution by 20%.
• Decreased costs of annual purchasing by $6 million.
• Overall support staff was decreased by 16%.
• Customer service center staff was decreased by 40%.
• Financial closing cycle was decreased from 10 to 2.5 days. • Approximately $40 million (per year) decrease in baseline procurement costs.
Discussions:
Q1: The key advantages of SAP supply chain investments
1.Improved customer service by focusing on order accuracy and product available 2.Developed multichannel customer service capabilities and electronic partnerships for customers and suppliers. 3.Increased the effectiveness and reduced the costs of doing business through continuous business process improvements in both its internal and external supply chains.
Q2: Describe what types of transactions are involved in NIBCO’s VMI program? NIBCO’s domestic wholesale and retail customers have already made an investment in EDI. For those who need to start from the bottom, investment doesn’t only include technology but also ongoing technical support personnel. But another choice for that is outsourcing to an EDI trading partner. 4 different types of EDI transactions are currently involved in NIBCO’s VMI program. 1.Product data activity – is a message format standard used by retailers to transmit point-of-sale data to suppliers via EDI. 2.Product order acknowledgement – is a confirmation that the order is booked/or received. 3.Advanced ship notice – is a notification of sending deliveries, similar to a packing list. 4.Invoice – is a commercial document issued by a seller to a buyer, indicating the products, quantities, and agreed prices for products or services the seller has provided the buyer.
Q3: What types of benefits have been attributed to the VMI initiative-for both NIBCO and NIBCO’s customers? For the NIBCO, VMI initiative can be critical business measurements used by NIBCO to define whether the program is sold primarily on the basis of gross margin return on inventory (GMROI). Since the supplier is responsible for pre censorship of inventory and to avoid stock outs, it will make VMI-supported customer to stay in or out a contract for the long term. This action helps NIBCO not only keep their income stable and definable, but also decreases the risk that customers go to another supplier. Thus, NIBCO can monitor its customers’ inventory, at the same time it can schedule its operations more effectively and efficiently. For the customers, NIBCO, now, is able to see if its customers are about to switch it with another supplier or not according to its absence of stockouts. Customers have clear sight about the NIBCO’s ability to restock the ordered goods without interrupting their operations. Therefore, customers can refit their needs since NIBCO has effective and efficient schedule for its operations according to the customers’ inventory. Therefore, the summary of benefits for NIBOC and NIBCO’s customers as following, Customers:
• Perfect order rate: increased from 30% to 87%
• On-time delivery: increased from 60% to 99%
• Inventory turn-over rate: improved 75%
• Stock outs rate: reduced from 11% to 2%
• Order-to-ship times: reduced from 48 to 8 hours
NIBCO
• Smoothing of demand
- Inventory levels: reduced from $102 M to $76 M
- Inventory turns: increased 3.66 - 4.27 times/year.
• Operation costs reduction:
- Costs of distribution: reduced 20%.
- Costs of purchasing: reduced $6 million.
- Cost of support staff: reduced 16%.
• Financial closing cycle:
- reduced from 10 days to 2.5 days.
Q4: What new initiative would you recommend that NIBCO pursue next to continue to take advantage of its current IT capabilities? CPFR (Collaborative Planning, Forecasting and Replenishment) is a concept that aims to enhance supply chain integration by supporting and assisting joint practices. Information shared between suppliers and retailers aids in planning and satisfying customer demands through a supportive system of shared information. To implement CPFR will reduce the cost in expenditures for merchandising, inventory, and logistics.
Cite this Page
Vendor-Managed Inventory at NIBCO. (2018, Mar 17). Retrieved from https://phdessay.com/vendor-managed-inventory-at-nibco/
Run a free check or have your essay done for you
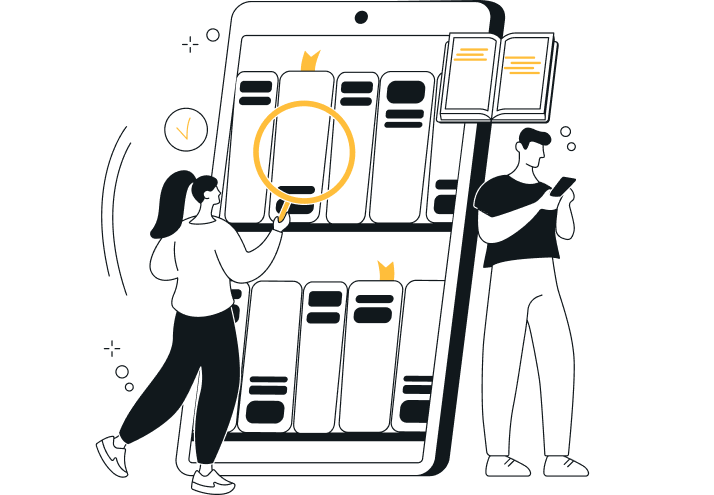