Lean Manufacturing
Introduction
Lean manufacturing is the production of goods through an approach which aims at reducing waste material while channeling them to useful activities. Lean manufacturing focuses on using less human and machinery effort, less manufacturing space and less time to produce and develop new products while producing less waste material. The concept of lean manufacturing focuses on three major aspects which include improvement of quality of products and production time and also cost reduction. Other aspects of lean manufacturing have been established which emphasize on improving the smoothness of work and in effect leading to waste reduction. Lean implementation’s main goal is to get the right things at the appropriate place, at the required time in the correct quantity so as to attain good products while reducing wastes. Lean techniques are implemented to make work easier to understand and to perform. (Field, W. M. 2001).
The concept of lean production requires that the products produced must meet the customers’ needs at the specific time by understand the activities required and optimizing them to complete the process from the customers view. The aim of lean manufacturing is to eliminate waste material in all aspects of production which includes factory management, customer relations and design in this concept, waste material is considered as anything that the customer is unwilling to pay for. Lean techniques are concepts designed to reduce waste products and achieve an efficient production system.
Order custom essay Lean Manufacturing with free plagiarism report
Lean techniques help industries to improve performers, productivity, reduce cost and improve the value of the company. A lean manufacturing system requires the use of correct resources and tools to attain the main goals of lean production. Lean techniques are designed in a product aligned manner where production is based on a one piece flow system in which production is in a continuous flow. Lean techniques require a continuous improvement of processes services and products over a period of time with the aim of reducing waste, improving product performance and customers’ satisfaction. The main goal of lean technique is to eliminate waste in every aspect of production including factory management, product designs and supplier system. Incorporation of less human effort and less time to develop the products has led to achieve this goal.
A range of quality/lean improvement techniques related to the study of Industrial problems.
Industries and companies are both using this methods and the six stigma method to reduce waste, increase speed while at the same time providing defect and variation reduction, using this tools together has help a great deal in achieving the benefits and reducing production of wastes. Lean Six Sigma is an improvement technique which helps to attain maximum improvement in customer satisfaction, cost reduction, quality improvement and speedy processing.
Lean techniques help in stigma so as to maintenance tools, materials and personnel in a proper manner so as to minimize waste and to increase speed. The lean six stigma techniques are also provided for improvement of the information technology, and human resource department of the company. In this method, company practices such as having and framing new employees can be minimize when speeding is increased and non value adding activities are removed and also when waste is eliminated. The lean six methods assist in keeping the focus of the industry on the two goals. Through this commercialization process of the company is made efficient by delivering within the shortest time new capable products and services to the market.
Lean improvement techniques are focused on the main goal which is to identity the value of an industry. After identifying the value, they work to create the value in steps which minimize the amount of waste created. To achieve this, they need to standardize and regulate working practices and at the same time clear up the workplace. 5s is a methodology of cleaning up and organizing the workplace which originated from Japan.
This technique emphasizes more on how to achieve and maintain cleanliness and visual orderliness at the workplace. In this methodology, companies are required to remove unnecessary items from the workplace and organize it, to make it easier for employees to perform their tasks in a clean and orderly working environment. 5s usually can be translated into sort, set in order, shine, standardize and sustain. Sort refers to remove unnecessary tools and items from the workplace and identifying the most needed tools to perform the tasks.
Set in order, ensures that tools and materials are arranged in a manner which is easier for the employees to access. Finally sustain ensures that 5s method is assimilated in the organization culture. To ensure this is adhered to by all employees, their performance is measured and they are informed of their progress routinely. The main benefit of this method is that it keeps the workplace orderly and clean. As a result, efficiency is improved by reducing time take to search for tools by reducing inventory and cycle of production time. (Hobbs, D. P. 2003).
Total productive maintenance (TPM) is a lean technique which focuses on incorporating all functions and categories of an organization so as to improve the efficiency and effectiveness of their production process. Its main aim is to reduce accidents and mistake made during operation and production. It is a technique which aims at preventing maintenance breakdowns, eliminating product defects and designing tools and materials which require less maintenance. Cellular manufacturing also referred to as one-piece flow system, supports a smooth flow of materials, where equipments are arranged in an aligned procedure so as to reduce transport delays. By using this technique, the production capacity of an industry can be increased by adding more production units. (Dennis, P. 2002).
The concept that “Lean” has on economic aspirations of developed and developing countries
Lean manufacturing which is described as a system to eliminate waste and improve productivity, is the answer to eliminate the problem of jobless people in these countries. Lean manufacturing technique must be aligned appropriately at all production levels so as to improve the economy of these countries. Developing countries have discovered lean manufacturing techniques are effective in reducing costs and waste by increasing their workforce, so as to have a one piece flow system.
These countries must reduce costs at all levels by challenging all their activities to establish whether the activities add value to the customers. This way, they can eliminate business processes which do not add value to the customer or benefit the industry. They should focus their attention more by determining why a certain operation must be used. Preventing production defects is more profitable than fixing it. Therefore, removing all non-value added activities is more beneficial to the company, and in the long run, improves the economy of these countries. (Conner, G. 2001).
By identifying activities which provide more value to the customer, companies will be able to reduce costs, reduce the time required to achieve a product and also improve the quality of their products. Use of lean manufacturing in developing countries ensures flexibility and one- piece flow production which leads to production of goods which are best suited for the customers needs by meeting the delivery time at a reduced cost. This enables the countries to expand their internal market by reducing costs. Having a customers’ based focus, is a technique which has enabled industries to focus on customers input and feedback to ensure customers satisfaction and so promotes the sales.
Physical and Socio – economic impact of Lean on resources and pollution
While lean manufacturing techniques focus mainly on reducing waste and eliminating non-value added activities in their production system, they also assume practices which help in improving environmental performance. Through this, they are able to focus on the environment and related resources by reducing pollution. Industries are directing their attention to lean manufacturing so as to reduce cost and production requirement resource, to improve their product quality and enhance customer satisfaction and responsiveness so as to boost the company’s profits. The main goal of lean technique is to eliminate waste in every aspect of production including factory management, product designs and supplier system. Incorporation of less human effort and less time to develop the products has led to achieve this goal.
Industries engage in lean techniques which focus more on production efficiency and improving production of resources. Doing this results to, using less material, using less energy, and in effect, producing less waste. This culture in turn benefits the environment, in the sense that industries train their employees to focus on environmental friendly practices so as to reduce waste production and prevent pollution.
Lean methods have established continual improvement based waste elimination techniques which lead to improvement in environmental performance. Research studies have shown that lean techniques focus on environmental management tools which include, life –cycle and tools implemented to reduce the environmental risks and pollution. Decreasing the material used during production especially water, chemicals, energy and other inputs, reduces chance of producing more waste during manufacturing and thus less waste is channeled into the environment. The continual improvement techniques used by industries enables them to identify and remove waste materials during the production process. (Taghizadegan, S. 2006).
Conclusion
Lean manufacturing techniques have been implemented so as to provide customers with a range of higher quality products at lower prices through many different sales channels. Lean manufacturing focuses on using less human and machinery effort, less manufacturing space and less time to produce and develop new products while producing less waste material. The concept of lean manufacturing focuses on three major aspects which include improvement of quality of products and production time and also cost reduction. Other aspects of lean manufacturing have been established which emphasize on improving the smoothness of work and in effect leading to waste reduction. Lean implementation’s main goal is to get the right things at the appropriate place, at the required time in the correct quantity so as to attain good products while reducing wastes.
Lean techniques are implemented to make work easier to understand and to perform. The concept of lean production that the products produced must meet the customer needs at the specific time by understand the activities required and optimizing them to complete the process from the customers view. The aim of lean manufacturing is to eliminate waste material in all aspects of production which includes factory management, customer relations and design in this concept, waste material is considered as anything that the customer is unwilling to pay for. Lean techniques are concepts designed to reduce waste products and achieve an efficient production system.
References
Conner, G. (2001). Lean Manufacturing for the Small Shop. SME.
Dennis, P. (2002). Lean Production Simplified. Productivity Press.
Field, W. M. (2001). Lean Manufacturing. CRC Press.
Hobbs, D. P. (2003). Lean Manufacturing Implementation. J. Ross Publishing.
Taghizadegan, S. (2006). Essentials of Lean Six Sigma. Academic Press.
Cite this Page
Lean Manufacturing. (2017, Feb 05). Retrieved from https://phdessay.com/lean-manufacturing/
Run a free check or have your essay done for you
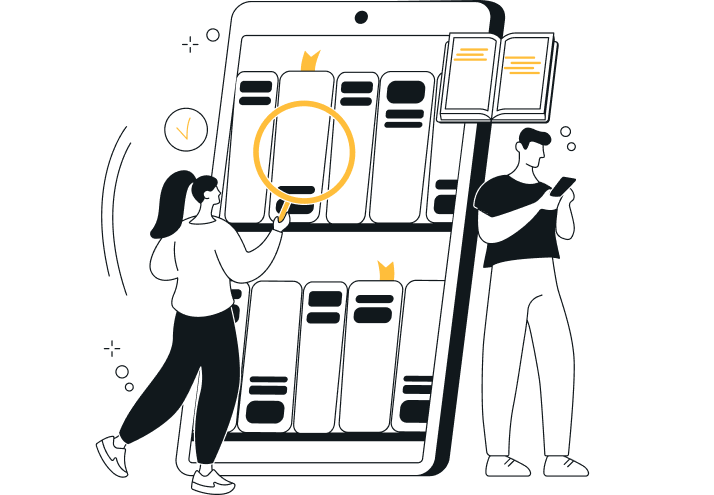