Implementation of Lean Logistics in Harley Davidson
Lean Logistics, simply put, can be described as a way to recognize and eliminate wasteful activities from the supply chain in order to increase product flow and speed. In order to achieve Leaner Logistics; organizations need to implement leaner thinking. Lean production involves eliminating waste and using less labors, materials, time and space. That's why it is save production. This in turn reduces costs.
Harley-Davidson Motor Company, the only major U. S. -based motorcycle manufacturer, is known for setting the world standard when it comes to the design and manufacture of heavyweight motorcycles. The company chose UPS Supply Chain Solutions to help set world standards with its logistics processes. Before going lean, the company operated in a cluster of factories that could have been mistaken for an industrial park from the mid-20th century.
The lack of automation and other new techniques kept it far behind in terms of operating productivity. But since adding lean to its operations, manufacturing that once comprised 41 buildings has been condensed into one well lit plant that employs more robots than laborers. The company has shaved the number of hourly workers to about 1,000 from more than twice that only three years ago, with more than 100 of these employees on contracts that allow them to come and go as is needed by Harley.
Order custom essay Implementation of Lean Logistics in Harley Davidson with free plagiarism report
Using historic data from the suppliers, the analysts calculated optimal shipping frequencies for each of the suppliers, enabling the company to reduce the rate of regular inbound shipments to three times a week, while also giving the manufacturing plant faster access to larger stocks of parts. UPS Supply Chain Solutions is gradually optimizing the entire Harley-Davidson inbound transportation network, by calculating optimal ship frequencies for all the suppliers and identifying cross-docking opportunities at the other manufacturing facilities.
As a result, Harley-Davidson Motor Company is gaining efficiencies throughout its manufacturing operations, while reducing its transportation costs. The comprehensive solution also added value to Harley-Davidson’s shipments of parts and accessories to dealerships. In the previous system, Harley-Davidson shipped parts and accessories to its distribution center in Wisconsin where parts were stocked, picked and packed to fill orders. The orders were delivered by less-than-truckload to dealerships around the country.
Leveraging its delivery network, UPS will begin shipping orders of less than 1,000 pounds directly to the Harley-Davidson dealerships. Orders of more than 1,000 pounds will be delivered to a UPS Supply Chain Solutions cross-docking facility in Wisconsin where they will be loaded onto pallets the same day and shipped by less-than-truckload. As a result, Harley-Davidson expects to further reduce its transportation costs and speed up average delivery times of parts and accessories to its dealerships.
JIT inventory is the driving force of Harley's quality-improvement program. JIT works on a demand-pull basis and seeks to eliminate all waste and activities which do not add value to the product. Suppliers of Harley had to implement JIT into their production process in order to compliment Harley's system. Previously, Harley utilized a complex, computerized inventory system, Material Requirements Planning, which was based on maintaining high levels of stock, to offset any manufacturing problems, so the assembly line would not be halted.
This system was inefficient because it did not address the manufacturing process problems. This is a typical problem with many traditional firms, where planning becomes the focus. Since the focus for traditional firms is planning rather than control, the result is to try and improve planning for next time. Firms then end up not executing these plans but rather planning and re-planning. With the lean approach the focus is on control. Procedures are kept simple, visual and made as routine as possible.
With JIT, as each problem is exposed, you are forced to identify its cause, fix it, and move on to the next problem that is revealed. Although JIT system had top management support, without full employee participation in the planning and implementation, Harley's JIT would not have been effective. Harley Davidson’s success with the implementation of JIT had a lot to do with the fact that when JIT was put into practice, process problems could no longer be hidden by costly inventory that helped to meet ship dates. The inefficiencies in the processes were quickly identified and solved.
Cite this Page
Implementation of Lean Logistics in Harley Davidson. (2017, Jun 01). Retrieved from https://phdessay.com/implementation-lean-logistics-harley-davidson/
Run a free check or have your essay done for you
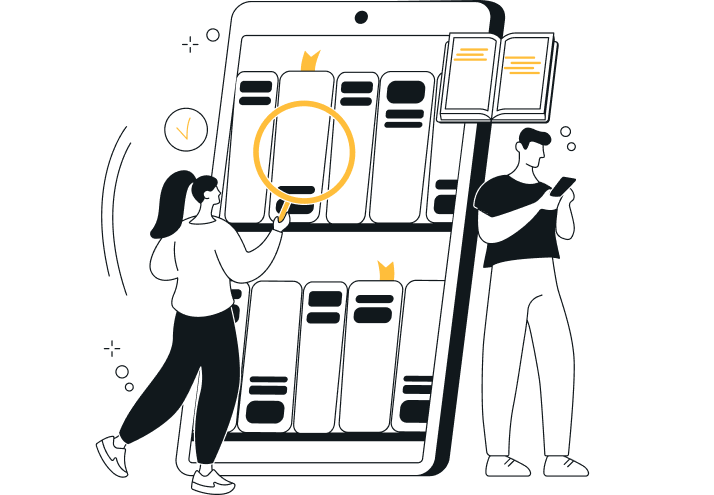