Logistics management – Evaluate the logistics operations
Reading through the case study I have found that SF is a very active company in terms of the movement of goods within the business. Their demand fulfillment system hosts most of the logistical activities. Looking over figure 1 you can see 2 definite independent logistical channels. The Channel on the right shows how the Map stocks move from the print planning to the Printing lines, the printed maps move to the Bulk store. Broken down orders are then taken to the Picking area. The channel on the left displays how the customers' orders and trade orders meet up with the Million inventory control system.
The system is in constant communication with the right hand side channel making sure there Is enough stock In place. Through a bar coding system, using hand held scanners, Million automatically finds the requested orders in the Bulk store, a picker then brings it down to the picking line. The goods are then packed and dispatched using a contracted logistics service provider. The movement of goods within SF have both a manual and an automated system working together to produce maximum output.
The printing department has the most activity, as much as 4 hours can be spent on setting up Just one machine with he majority of time spent on configuring the plates and ad]gusting the colors. Once set up, the printing machines work two seven-hour shifts, each producing as much as 8000 maps per hour. The company has four printers with two deferent printing machines, Alpha and Beta. The Alpha machines are older and less efficient, with almost twice as much time needed for set up whilst, only producing half as much output compared with the Beta machine.
Order custom essay Logistics management – Evaluate the logistics operations with free plagiarism report
Nonstop et al, 2003:170). SF has two fairly distinctive levels of demand. The first is a lower level, where monthly sales volume accounts for only 5% and 7% of the annual total and a second, landing procedures department use as much as 12 months lead time in preparation for new maps and stock replenishment. The team determine the need for placing a map (stock) on the printing schedule as much as 6 months in advance. They aim to deliver a batch of printed maps to the Bulk store 3 months before stock is projected to run out.
Holding 12 months of inventory can be expensive. Warehousing for storage including rent and utilities, Insurance and taxes on inventory finance for the stock, and stock losses due to shrinkage/deterioration are Just a few costs for holding inventory over a long period. Inventory optimization www. Sap. Com Accessed 2. 1. 2007 Moving over to the left channel of figure 1 we see more activity coming in from customers and trade orders. SF aim to have dispatched the customers order within three to four days of receipt, with an 88% performance target regularly being exceeded.
Only over the busy Easter months have SF had problems with delivery times, this was mainly due to their contract logistics service provider. SF should have forecasted from previous years that Easter was the busiest time and so they should have hired more transport through their logistics providers. The company uses an Electronic Data Interchange (DEED') for their customers to place orders. Only 50%-60% of the orders are EDI with the remaining orders being keyed in to Million by hand. This process is slow, not cost effective and can generate errors.
Use of this channel is limited to a small amount of Cuff's largest customers. Here I think is Cuff's biggest downfall. According to Stock, If the EDI was available to all the customers, Million, the system used to generate the EDI orders to the warehouse would be working independently without the need of any keyed in manual orders. This would save time and money, (Stock, 2001) The final logistics operation happens in the picking area. Once the maps have been made, they are stored in aisles with the maps arranged by country and then by numerical order.
When an order comes through scan guns will find the order and tell the pickers exactly where the maps are stored using an onboard display. When the entire order has been picked, the scan gun is uploaded into Million, allowing the system to reorder the necessary stock. The order is then packed and palliative and is ready to be dispatched. Discuss how the use of various IT applications contribute to enhancing efficiency of the logistics processes. Are there any areas which could be further developed using Carters Sans Frontre's distributes nearly 5 million maps a year throughout Europe.
This figure would not be possible without the use of IT within the organization. SF uses a very sophisticated order processing system, a SAP R/3-based system called 'In the face of continual growth, the increased turnover, and an increasingly global and competitive market, Million adopted a simple strategy - improve efficiency and manage costs by integrating and streamlining its retail, manufacturing and distribution businesses located around the world'. Strategy behind Million www. Sap. Com Accessed 2. 1. 007 Million receives an order via Electronic Data Interchange (DEED'). Saunders states that, "EDI is the transfer of data between different companies using a File Transfer Protocol (FTP) connection and is becoming increasingly important as an easy mechanism for companies to buy, sell, and trade information. It is unmanned, reduces paperwork and reduces error". (Saunders "The purpose of EDI is to eliminate duplicate data entry and to improve the speed and accuracy of the information flow by linking computer applications between companies" (Emailing, M.
A. ,1992: 17) An order number is then produced generating a pick list; this is then downloaded into hand-held barded scanning guns that inform operators which maps to pick up and where they are stored. Emailing argues bar-coding is a very useful form of an IT application. Varying widths of bars represent letters and numbers, they are simple to use, accurate and quick, and they can store large amounts of information and can produce instantaneous transmission of information giving greater central control and inventory reduction. (Emailing, M.
A. 1992) Once the order has been packed and is ready for distribution, the scanning guns are uploaded back into Million for the system to re order and replenish stock. This is known as the order processing technology capable of processing ongoing data through data management. Supply chain management is a focal topic in business today. Render has defined "supply chain management" as the integration of activities that procure materials and services, then transform them into intermediate goods and a final product, and deliver them to customers. Render. 1997:64) Million seems to be a very useful tool in this industry. Although the company is not utilizing the system to its maximum potential, unfortunately for SF, only 50% of orders are received by DEED', with the remainder arriving by other channels either fax, telephone, post or e-mail. These orders then have to be typed manually into Million, this is not a cost effective method as man hours are wasted inputting data. The reason for the low percentage of orders flowing through EDI is mainly due to the customers who are placing the orders.
Many large companies have an electronic data costly to install and implement. Companies that have EDI installed may also find there system is not compatible with Cuff's, Million. In terms of this application enhancing efficiency and contributing to the business, the Million system can identify and fix simple mistakes in an order such as replacing superseded codes with current numbers. Around 97% of all orders pass smoothly through the process.
This is somewhat beneficial as it means less man hours are spent fixing small errors. The Surveying and Design Division use another form of IT application. When it comes to printing the maps, the design division need to set up the printers manually as mentioned above, and one printer can take as long as 4 hours to perfectly align the colors and set up. The case study notes that the Alpha printers are old and can only reduce half of the amount to that of the Beta printers output.
If SF invested into 2 new printers where the color alignment was loaded automatically and gave out the same output as the Beta printers, SF would save 8 man hours every time a new line was uploaded, whilst generating twice the amount of maps to that of the Alpha machines. One way for Carters sans Frontre's to significantly reduce manual labor throughout the warehouse would be for the whole operation to become automated, transforming the warehouse using an automated highboy narrow aisle laser navigated rack stacking system.
The picking area would become obsolete, with the break through technology of a fully automated laser navigated forklift in the warehouse. Million would simply receive the order from the customer then immediately send the information to the automated warehouse, the unmanned cranes would set to work pulling off the right pallets with no error, they would then send them down a large set of rollers called a 'hydra foil' and within minutes the order will have been created ready for distribution.
Of course not all warehouses will have the infrastructure to house an automated highboy and the cost would be very expensive. The other problem may be order quantities, if a customer only wanted half a palette of each map, the cranes would not be maximizing output as they would have to be hand picked in order to make half pallets. (Bowers, D. 1996) What actions should be taken by the company to reduce stock levels and improve customer service levels? Holding inventory is a very costly procedure.
When looking over the way Carters Sans Frontre's hold there inventory, I think there is room for improvement. A single map could be held in bulk storage for as much as 6 months. In the case of maps where ewe roads and motorways are constantly being updated, that map will become obsolete 6 months down the line. I suggest that SF move to a more efficient way of at the time they are needed, the system coordinates supply and demand using a pull system, where customers demand the orders and those actual orders are used for production.
This is a more efficient way of holding much less inventory. SF host their production on a pull system based on forecasting previous demand; instead, they should use real time data as this would increase stock turnover. (Porkier, C. 1996) There are a number of different solutions SF could take to reduce inventory. Firstly, they could think about moving from a storage warehouse to a cross docking operation, this uses less storage, lower lead time thus resulting in faster delivery.
Secondly they could use a shared user warehouse, enabling overheads, electricity, rent and insurance to be divided. Thirdly they could priorities fast moving and more popular maps by producing more, whilst reducing the size of slower moving, less popular products. As I mentioned before, they could use warehouse automation. This significantly improves speed and efficiency reducing the amount of people employed. Although all of the above are definite solutions for Cuff's inventory problems, in reality the cost factor may be too large.
Cite this Page
Logistics management – Evaluate the logistics operations. (2018, Aug 26). Retrieved from https://phdessay.com/logistics-management-evaluate-the-logistics-operations/
Run a free check or have your essay done for you
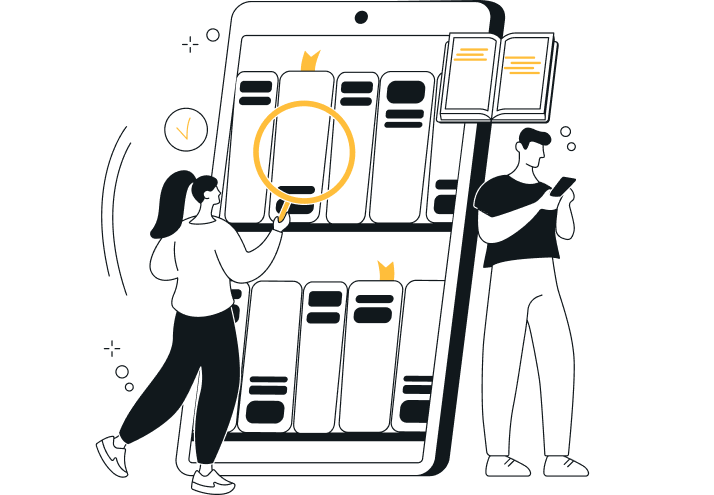