Critical Assessment of Toyota Processing System
Toyota Processing System (TPS) is a quality process that is not only used in the Toyota Company but also applicable in Toyota corporations. TPS is also known as lean manufacturing, which is a management philosophy involving systematic and highly developed strategies through which continuous quality productions can be achieved in a company to meet or exceed customer satisfaction (Kotelnikov, 2009).
There are different ways through which TPS can be defined and applied in different organizations because quality production processes are aimed for different purposes such as overproduction, reduced inventories, lead-time and wastages leading to improved customer services. Basic understanding of TPS Definition Toyota Production System (TPS) is a quality system used in Toyota Company to enhance productions through integration of processes, people and systems with two main principle jikoda and just in time being used.
Order custom essay Critical Assessment of Toyota Processing System with free plagiarism report
Toyota production system has many terms used to define it and these includes. First, Andon which is a vision control system that displays activities going on at a given time such as any abnormalities, work procedures and information on job progress. Second, Genchi Genbutsu, which means go and see the problem calling for a practical rather than theoretically approach in solving a problem. This is a belief that suggests the preference of practical expertise to theoretical ones (Toyota Processing System, 2006). Third, Heijunka, which is a requirement for a just in time production.
This is used to determine the production patterns in terms of quantity and quality over a period depending with the customer demands. Forth, Hoshin, which helps companies come up with clear goals and strategies through which the long and short-term goals could be achieved for a quality improvements. Fifth, Jidoka is a TPS pillar referring to the ability of a production system to fault tolerant or intelligent to automatically detect any anomalous behaviors in the system to prevent any poor productions because of a defect that could have been corrected.
It emphasizes on localization and isolation leading to quality production processes (Toyota Processing System, 2006). Sixth, Jishuken is a quality enhancement process that helps companies identifies critical areas that require continuous improvements and communicate it throughout the company for everyone to take part. Seventh, just in time is a pillar of TPS, which emphasizes on production of just what is required in specific quantities and on demand leading to pull, continuous flow processing and takt time systems (Toyota Processing System, 2006).
Eighth, Kanban, is a control factor used in just in time production by giving instructions and conveyance, controls production to prevent surpluses and defective products and identifies critical areas where improvements should continuous. Application of TPS to a different Organization (Wal-Mart) TPS can be applied in Wal-Mart in different ways leading to quality improvements. Muda meaning waste can be used in Wal-Mart to monitor production processes to identify most critical processes for an added attention while eliminating non-value added ones.
This is in order to reduce lead-time, overproduction, conveyance and inventories. Kaizen can be used in Wal-Mart to help assess production systems to identify critical areas where continuous quality improvements are required and eliminating non-productive processes to reduce production cost, time and resource (Kotelnikov, 2009). Description of TPS as a total entity TPS is purposely for enabling Toyota Company to continuously produce quality automobile products at relatively affordable prices to meet or exceed customer satisfaction.
TPS goal is to continuously produce excellent quality automobiles products in the most reliable and cost effective ways. TPS has the following advantages high focus on products specifications and they have had a record of being a successful automobile manufacturer in the market (Toyota Processing System, 2006). In every good thing there has to be side effects, Toyota had some limitations in the market such as it depended human inability to defend themselves when it comes to automobile productions and its successes were rarely realized for example through the record of success (Kotelnikov, 2009).
Toyota has evolved and is still evolving on its production patterns. Toyota has produced automobile products to suite international markets by constantly renovating its plants. Toyota became the second largest automobile manufacturer in terms of sales revenue in 2007 (JAL Group Cargo Operations, 2005). Is TPS adopted or adapted by major automobile manufacturers TPS is highly adaptable because it is a matter of identifying the critical production processes in a business and putting the required efforts to ensure continuous quality production is achieved (Bowen & Spears, 1999).
TPS has been adopted with many successful companies dealing with motor vehicle manufacturing such as BMW and GM for quality improvements even though some organizations have found it too expensive to continuously train employees (Johnson Controls, Inc. , 1993). BMW has used TPS leading to its market expansion and increased market share globally and GM has used it in an attempt to achieve market sustainability in a cost effective way. Conclusion TPS is very essential for quality productions in all organizations or companies.
This is because it helps companies in achieving the required quality productions in a cost effective way leading to improved customer satisfaction. TPS is easily adaptable under quality project management strategies in a company (Bowen & Spears, 1999). Many companies especially motor vehicle manufacturing companies such as BMW have been very successful and TPS should be adopted by other organizations other than the motor vehicle manufacturing companies.
This is because it emphasizes on production on demand and managing all production processes to identify any defects for correction in localized areas or in isolation to avoid any resource wastages (Toyota Processing System, 2006). Reference: Bowen, H. K. and Spear, S. (1999). Decoding the DNA of the Toyota Production System. [Viewed on 28th June 2009] Available at <http://hbswk. hbs. edu/item/0869. html> JAL Group Cargo Operations. (2005). Toyota Production System Steers JAL Group Cargo Operations at Narita. [Viewed on 28th June 2009] Available at <http://press. jal. co. jp/en/release/200508/000472. html> Johnson Controls, Inc. (1993).
Graduate School of Business Stanford University Johnson Controls, Automotive Systems Group. [Viewed on 28th June 2009] Available at <http://www. stanford. edu/~milgrom/publishedarticles/Johnson%20Controls,%20Inc. %201993. pdf> Kotelnikov, V. (2009). Lean production: 7 Principles of Toyota Production System (TPS). Lean Manufacturing. [Viewed on 28th June 2009] Available at <http://www. 1000advices. com/guru/processes_lean_tps_7principles. html> Toyota Production System. (2006). Toyota Motor Manufacturing Kentucky, Inc. [Viewed on 28th June 2009] Available at <http://www. toyota. eu/02_About_Us/06_toyota_production_system/index. aspx>
Cite this Page
Critical Assessment of Toyota Processing System. (2018, Mar 30). Retrieved from https://phdessay.com/critical-assessment-of-toyota-processing-system/
Run a free check or have your essay done for you
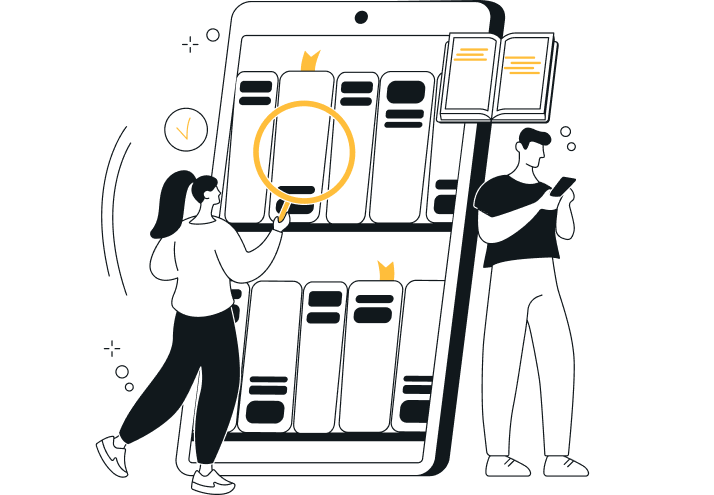