Application in General Electric Company
Ever since the end of the Second World War, quality management is given more and more importance by business organizations. Indeed, the evaluation and monitoring of the quality of management provided by a business organization to its clientele has been considered as an integral part of the activities conducted by any business organization management structure, particularly among companies that are involved in industries dealing with the manufacturing of products and the provision of services to their clients.
This high regard for the regular monitoring and evaluation of quality management has been brought about by the belief by business organization that unless a particular activity conducted cannot be measured, this would not be properly managed. As a result, business organizations and schools of thought have prompted the development a series of standards of measurement for the performance of the activities of a particular business, which would, in turn, result to the systematic evaluation of the overall productivity of the operations and activities of a particular business organization (Bohlander & Snell 2007).
One particular set of quality management standards being used is the ISO 9001 standards. This paper will look into the current performance evaluation tool utilized by General Electric Company and how the use of the ISO 9001 standards for quality management can be used to improve the quality of the production and customer service being provided by the company.
Order custom essay Application in General Electric Company with free plagiarism report
In line with this, the paper would provide an overview of the ISO 9001 standards of quality management and the methodologies that can be recommended for the utilization of General Electric Company as opposed to the current quality management performance evaluation tool it is currently using. Overview of the Use of Performance Evaluation Tools In order to provide an understanding of the ISO 9001 standards for quality management, an overview on the use of performance evaluation tools and the development of ISO 9001 standards will first be discussed.
The recognition for the importance of quality in production and performance in business organizations can be traced back during the Second World War. Weapons and vehicles that were constructed and manufactured for the use of the Allied Forces were done so with the creation of manuals and methods to produce and test them prior to being distributed to ensure optimum performance. This was given the term Quality Control (Kanji 2002). At the end of the Second World War, Dr. W.
Edward Deming, Joseph Duran and Kaoru Ishikawa began to carefully study the different methodologies utilized by Japanese business organizations who were trying to rebuild themselves after the destruction caused by the war. Based from the studies that they conducted, they determined that business organizations, particularly those belonging to industries of manufacturing and the provision of services, develop a set of principles and guidelines in order to ensure that the needs and wants of the clients would be continuously improved.
These studies led to the development to the Total Quality Management philosophy used in most business organizations today (Bohlander & Snell 2007; Hackman & Wageman 1995; Kanji 2002). With the globalization now becoming a trend observed among business organizations all over the world, there was now a need for an international set of guidelines and standards in order to ensure that the quality standards observed in a particular branch or office in one country is the same quality standards observed and executed in another part of the world.
It was for this reason that the International Organization for Standardization was developed. The International Organization for Standardization, more commonly known as ISO, was responsible for the development of standardized sets of guidelines and measurements which can be modified and tailored to meet the needs of a particular business organization, regardless of the industry that the business organization is a part of.
As a result, the ISO became a basis of an international scale which aims to determine the level of the quality of management practiced and utilized in a specific business organization belonging to a particular industry in a specific country. This, as well as the paving the foundations of a “standard language”, led to the development of the ISO 9000 Standards Series. The ISO 9000 Standards Series is composed of five different sections, each pertaining to a specific aspect in the overall monitoring and evaluation of quality management in a business organization.
One of the series is the ISO 9001 series. This series is considered to be the most comprehensive of all the five sections such that the ISO 9001 series can be used by business organizations that offer a wide range of products and services to their clientele (Hormozi 1995; International Standardization of Organizations [ISO] 2007). Today, more and more business organizations have begun utilized the ISO 9001 series as a means to monitor and evaluate their business activities in terms of quality management. This is due for a number of reasons.
One of these reasons is that because of the comprehensiveness of the guidelines provided by the ISO 9001 series, these guidelines can be applied to a business organization belonging in any industry and situated in any country. As such, business organizations would be able to enforce this set of guidelines while remaining confident that the standards of quality that is practiced in the head office in one country will be the same standards that will be observed and practiced by the branch of the same business organization established in another country.
Another reason for the popularity of the use of the ISO 9001 series is that instead of creating a specific set of guidelines that would be observed in a particular division of the company, and a completely different set of guidelines to another division, business organizations utilizing the ISO 9001 series can use one set of guidelines to be adhered to by all the divisions of the business organization (Hormozi 1995; ISO 2007). General Electric Company For this paper, the selected company to be used as the study of the application of the ISO 9001 series is General Electric Company, or GE.
General Electric Company was established back in the year 1890 under the name Edison General Electric Company. The company was founded by Thomas Alva Edison, who is popularly known as the inventor of the incandescent light bulb. Edison initially established the company to provide him a means to explore the potentials of dynamo and a variety of other electrical devices. At the time of its establishment, Edison General Electric Company was in stiff competition with the Thomson-Houston Company.
The difficulties of competing due to the patenting of different electrical devices which were developed by the two companies resulted to the merging of the two companies in 1892. As a result, the General Electric Company that we know today was established (“Thomas Edison & GE” 2008). General Electric Company is the leading manufacturer and distributor of lighting, industrial, power transmission and medical equipment. Over the recent years, the company has begun to branch out into serving clients more by entering a variety of other industries.
Some of these ventures include the establishment of a financial institution in the form of GE Money Bank and the entertainment industry with its acquisition of the NBC International Broadcasting Network (“Products and Services” 2008). Current Performance Evaluation Tool of GE The current performance evaluation tool utilized by General Electric Company is the Six Sigma System Approach. The approach was in use since the year 1995 (Eckes 2001). The Six Sigma System Approach was developed by Mikel Harry, an engineer in Motorola.
Harry observed during his employment with the company that Motorola utilized a number of processes in the hopes of improving the level of customer satisfaction provided by the company to its clientele. Unfortunately, the reverse was actualized in the company’s endeavor. He then developed the Six Sigma System Approach in the effort to provide the company a means to efficiently and effectively manufacture its products and provide high level of customer service to its clientele at the same time (Eckes 2003).
The results of the application of the Six Sigma Approach in General Electric Company was almost instantaneous. Its inventory rating increased to 9. 2 from the average of 5. 8. The depreciation rate observed in plant equipments and expenses have also greatly reduced. One of the reasons, according to the management of General Electric Company, is its ability to provide the company a means to incorporate changes in its methodologies.
The Six Sigma Approach already anticipates that employees and management in a particular organization would resist any form of change that would be implemented in order to improve the quality of management and performance observed in the organization. This being the case, the methodologies provided by the Six Sigma Approach allowed the management of General Electric to implement the change and motivate the employees to accept the changes by focusing on countering the resistance of change within the company (Eckes 2001).
Another reason for the success of the Six Sigma Approach utilized by General Electric Company is that the approach had bee able to provide the company the ability to determine the specific needs of a particular target market of the company. This was achievable with the ability of the Six Sigma Approach to provide a variety of methods and processes into a number of specific tasks, which would, in turn, allow the management to determine which is the most effective methodology which should be used to meet the needs and wants of the company’s target market.
Moreover, the approach provided the company with a means to predict any possible shortcomings or barriers that may arise in the implementation of such processes and methodologies prior to it being implemented. As a result, the company is able to determine the different methods in order to ensure to address potential issues which may not only lead to the dissatisfaction of the customer, but also to the damaging of the image and reputation of the company as a whole (Bohlander & Snell 2007). Limitation of the Six Sigma Approach
While it is true that the Six Sigma Approach has been documented to have provided the General Electric Company an effective means to evaluate and monitor its performance to ensure that customer satisfaction is achieved, this approach still has a number of limitations. One of the limitations is the scope of the industries where the Six Sigma Approach can be effective and efficient. The Six Sigma Approach, as previously mentioned, has been designed and developed for business organizations whose activities are mainly involved within the manufacturing and distribution industries.
This being the case, the Six Sigma System Approach may not be able to be as effective when applied to the activities of business organizations belonging to different industries. General Electric Company is no longer involved in the manufacturing and distribution industries. As mentioned earlier, the company has now ventured into different industries such as the financial and banking industry as well as the entertainment industry.
This being the case, the efficiency of the Six Sigma Approach utilized in these branches of the company may not be as promising as in the case of its manufacturing and distribution branches. Another limitation in the use of the Six Sigma Approach is the system used. The system utilized for this performance evaluation tool relies heavily on the Human Resource Department of the head office to provide the different methodologies and procedures and to ensure that such methodologies would be properly executed and implemented (Bohlander & Snell 2007).
Since General Electric Company has established offices in different parts of the world, the company needs to utilize a specific set of standards that would be efficiently applied by the Human Resource Departments of the different offices and branches without having to rely on the intervention of the Human Resource Department located in the main office. Lastly, the guidelines that are utilized in the Six Sigma System Approach are extremely broad. The broadness of such guidelines paves the way for numerous subjective interpretations by management.
As a result, this would eventually lead to the possibility of different interpretations of the guidelines not just by members of management of the same division and same office, but also by members of management belonging to a different division and different branch. Application of ISO 9001:200 to GE Based on the limitations observed in the use of the Six Sigma System Approach, it is then determined that the ISO 9001:200 standards series are more ideal to be utilized in General Electric Company.
This is because the guidelines provided in the ISO 9001:200 series are stated to the last detail which would prevent any incidence of subjective interpretation to occur between members of management within the business organization. It also minimizes, if not eradicates, the rise of friction between departments resulting from one department or division questioning the decision of another department or division since members of management can always refer back to the standards that have been itemized by the ISO 9001:200 series (ISO 2007).
The first part of applying the ISO 9001:200 is the determination of the goals of the business organization. This is done through the careful analysis of the mission and vision of the company, in this case, General Electric Company. The management would also need to look at the significant issues currently being faced by the different branches of the company, and determine which of these issues are the most pertinent to address (ISO 2007).
After the determination of the issues to be addressed, management would then need to gain substantial information with regards to the knowledge base that is available to be used by the company while taking into consideration what its target customers want and need. Once this information is gathered, a criteria of measurement that will be utilized by management in order to assist them in determining the importance of the issue in relation to the ability of the company to address the specified issues.
From here, the management can now develop the proper tools and strategies to be implemented (ISO 2007). In the application of ISO 9001:200, the quality evaluation plan to be created applying this set of standards would be done with the purpose to ensure that the different companies that comprise the conglomerate would be able to experience the same efficiency and level of customer satisfaction that is enjoyed by the manufacturing and distribution divisions. A number of criteria will be taken into consideration for its construction.
Among these would include the prompt servicing of the inquiries, needs and concerns of the clients served by these new businesses and the periodic measurements of the level of customer services being provided to the new customers of the company. After the criteria for evaluation is determined, the management of GE would now be able to sit down to discuss the necessary steps that can be utilized for the implementation of these evaluation tools in the different companies of the conglomerate.
Since General Electric Company fosters an open communication system within the entire business organization (General Electric 2008), the employees would be addressed with regards to the new methodologies and procedures to be implemented in the company through the use of a general assembly. This approach is beneficial for a number of reasons.
The first is that by addressing the employees of the changes that would be implemented within the business organization, employees of the different companies belonging to the conglomerate would be able to address and air their opinions and issues concerning the changes and methodologies to be implemented as a result of the company to shifting from the Six Sigma System to the ISO 9001:200. As such, management would be able to revisit the procedures and methodologies that would be implemented to ensure that any concerns that have been addressed by the employees of the different branches of the conglomerate would be taken into consideration.
Because the employees are provided a chance to air out their opinions and concerns, they feel that they are involved in the decision-making process, minimizing any form of resistance on the part of the employees once the new methodologies are implemented. In line with this, communication methods and training would be provided in association with the implementation of the new procedures and methodologies that adhere to the ISO 9001:200.
This is to ensure that the employees would not only understand the methodologies and procedures but they would also be able to perform and execute such methodologies and procedures as how management hoped that they would. Some of these communication methods would include the dissemination of memos and team meetings. This is to ensure that the employees are able to provide their feedback which would be beneficial in the management’s evaluation of the implementation of the procedures and methodologies within the company. Training would also be provided to the employees of the company.
In line with this, handouts would be disseminated which would discuss the new performance evaluation methodology that would be implemented. While the training would be initially be provided to the management of the different divisions of the conglomerate, the training would also be provided to the employees of the company. This is to ensure that the employees are fully aware on how the performance evaluation tool would be utilized by their superiors and what the different best practices that they need to adhere to in order to satisfy the new performance evaluation methodology to be implemented.
Conclusion General Electric Company is just one of the many companies that have become a key player in the globalization and business diversification trend now observed in different parts of the world. For this reason, the use of the proper performance evaluation tools is extremely crucial to ensure that the business activities of the company would not just be lucrative in terms of profits, but would be able to provide the company a means to provide a high quality of customer service to its clients.
While it is true that performance evaluation tools such as the Six Sigma System Approach is still effective in the evaluation and monitoring of quality management in certain industries, companies such as General Electric Company who are now venturing in business diversification must upgrade and update their evaluation tools to ensure that a standardized set of guidelines would be used with the least amount of room of subjective interpretation.
The application of the ISO 9001:200 in General Electric Company has proven to be an effective means to adequately monitor and evaluate the business activities of the conglomerate regardless of the industry or location of the branch of the company. References Bohlander, G. W. & Snell, S. A. (2007). Managing human resources 14 ed. Florence, KY: South-Western Publishing. Eckes, G.. (2001). The Six Sigma revolution: how General Electric and others turned process into profits.
New York: Wiley. Eckes, G. (2003). Six Sigma for everyone. Hoboken, New Jersey: Wiley. General Electric Company (2008) Products and services. Retrieved from http://www. ge. com/products_services/index. html. General Electric Company. (2008) Thomas Edison & GE. Retrieved from http://www. ge. com/company/history/edison. html. General Electric Company. (2008). Working environment. Retrieved from http://www. ge. com/company/culture/working_environment. html.
Hackman, J. R. & Wageman, R. (1995). Total Quality Management: empirical, conceptual, and practical issues. Administrative Science Quarterly, 40 (2), 309. Hormozi, A. M. (1995). Understanding and implementing ISO 9000: a manager’s guide. SAM Advanced Management Journal, 60 (4), 4. International Standardization of Organizations. (2007). Quality management systems – guidelines for the application of ISO 9001:200 in education. Geneva, Switzerland: Author.
Cite this Page
Application in General Electric Company. (2018, Jun 22). Retrieved from https://phdessay.com/application-in-general-electric-company/
Run a free check or have your essay done for you
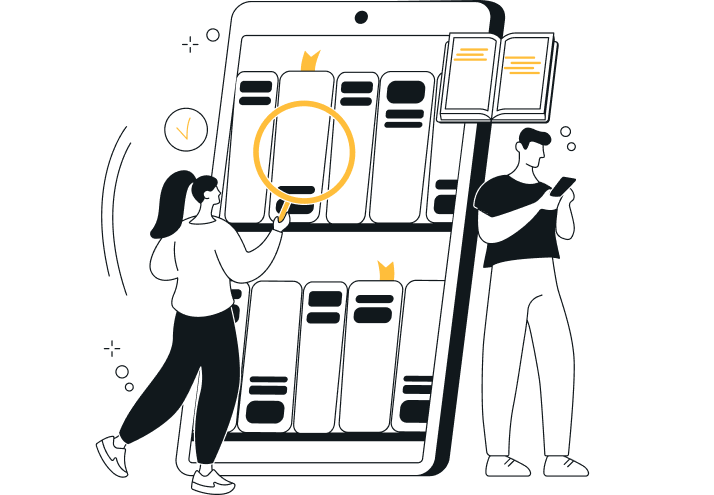