Manufacturing Resource Planning
MPR II is a modification of MPR (Material requirement planning) which is an information system that uses computer in scheduling items for purchase or production. The system uses information as input and the results are the products ordered or produced. MRP II (Manufacturing resource planning) has additional features to include all production and marketing operations in an organization. MRP II therefore includes all the required resources for production and marketing (Hill 2000). The Major Components of MRP II
MRP II is a system for scheduling resources for manufacturing and marketing of products (Hill 2000). The major components are the major operational areas in an organization. The processes included; Data collection where customer orders are being recorded. Customer details recorded are used as the input for the master production schedules. This information determines the end product. Another component is the data analysis where the collected information is analyzed and fed in to the system.
This information is transferred in various departments for production of the required product. The third component is the Evaluation area where performance level of various departments and machines is monitored. This is to ensure quality products are produced to satisfy the customer needs (Hill 2000). From the data generated in the first place, customer details can be accessed to get the shipping information. Within the evaluation department is where billing and invoicing done. This will help in managing production and finances in an organization.
Order custom essay Manufacturing Resource Planning with free plagiarism report
Production and financial reports made for future reference (Hill 2005). The forth component is the feedback where all customer responses and suggestions on delivered products are recorded. Feedback can also be from workers in various departments within the organization. The system uses a closed loop to allow for an all round flow of information within the organization. Members of an organization from all the departments are required to respond to any resource shortage or excess (Hill 2000).
How JIT/Lean Manufacturing Paradigm Could Improve the Competitiveness of Business Operations over Conventional MRP II in a Particular Industry. Just In Time/ Lean manufacturing paradigm is a production coordination system that emphasizes on production on demand. The paradigm encourages production when it is required to minimize the resource wastage (Womack & Jones 1996). This paradigm has been used to achieve very high quantity and quality of productions with minimum resources possible. JIT/ Lean production can be more advantageous in businesses than MRP II in the following ways.
When JIT/ Lean manufacturing model are used in coordinating human resources for instance sales and marketers, there will be a reduced chain of suppliers. Through reduced delivery chains an industry will achieve an improve delivery time. Customers will be receiving their orders in time and at relatively cheaper prices. This will be an advantage to a company since they will have improved customer satisfaction (Hill 2000). When a company has used JIT in coordinating there resource usage during production there is likely to be a change in the industry layout (Hill 2000).
To maximize resource usage for quality production and at the same time reducing wastage at all costs, there has to be numerous testing. An industry has to carryout tests at the end of every process or system operation to ensure quality and minimum resource consumption. This will be achieved through using portable machines, arranging continuous production processes in the same or nearer places to ensure continuity. All the required production and marketing processes should be done in the same place if possible to avoid wasting time and other resources.
Cite this Page
Manufacturing Resource Planning. (2018, Jun 12). Retrieved from https://phdessay.com/manufacturing-resource-planning/
Run a free check or have your essay done for you
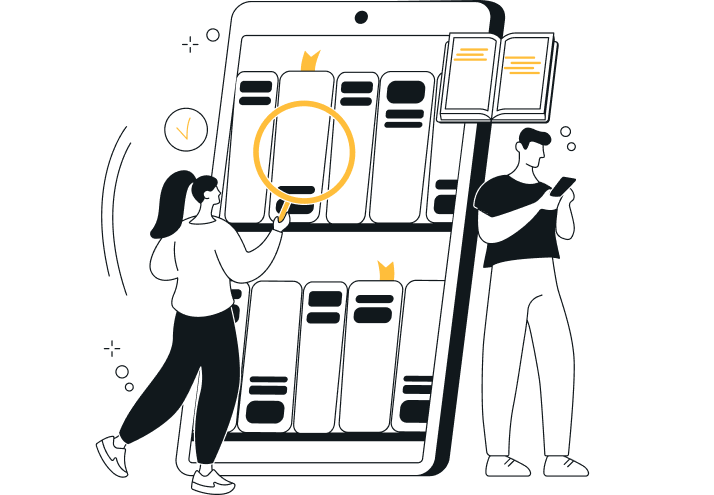