Computers in Modern Manufacturing
Computers in modern manufacturing introduction:
Computers play invaluable role in modern manufacturing. In fact, nearly all modern manufacturing support systems are implemented using computer systems through automation. It reduces manual work in manufacturing and production. Computer Integrated Manufacturing(CIM) is the terminology used to describe the complete automation of a manufacturing plant. CIM involves integrating the functions of designing products, production planning, operational control and business-related functions in one system that operates throughout the enterprise.
All of the processes function under computer control. Digital information ties them altogether. The different computer controlled processes are as follows: -aided design , computer-aided manufacturing CAD/CAM: The heart of CIM is CAD/CAM. Computer-aided design(CAD) denotes the use of computer systems to support the product design function. Using CAD, it is possible to simulate in three dimensions the movement of a part through a production process.
Order custom essay Computers in Modern Manufacturing with free plagiarism report
Computer-aided manufacturing (CAM) denotes the use of computer systems to perform functions related to manufacturing engineering, such as process planning and numerical control(NC) part programming. Some computer systems perform both CAD and CAM, and so the term CAD/CAM is used to indicate the integration of the two into one system. CAD/CAM is concerned with the engineering functions in both design and manufacturing. The method of manufacturing a product is a direct function of its design.
Through CAD/CAM technology, it is possible to establish a direct link between product design and manufacturing engineering. They have together overcome traditional NC shortcomings in expense, ease of use, and speed by enabling the design and manufacture of a part to be undertaken using the same data encoding system. CAD/CAM has also given the designer much more direct control over the manufacturing process. ADVANTAGES: CAD/CAM enables manufacturers to reduce the costs of producing goods by minimizing the involvement of human operators.
They enable manufacturers to make quick alterations to the product design and obtain instant results. Also there is no risk of human(repetitive) error. This finally results in lower operational costs, lower end product prices and increased profits for manufacturers. CAD/CAM systems also facilitate communication among those involved in design, manufacturing, and other processes. This is of particular importance when one firm contracts another to either design or produce a component.
Dissadvantages:
There are no means of comprehending real-world concepts in CAD systems, such as the nature of the object being designed or the function that object will serve. CAD systems function by their capacity to codify geometrical concepts. Thus the design process using CAD involves transferring a designer's idea into a formal geometrical model. Thus CAD cannot build the exact design as it is on the designer’s mind. Also, there are several limitations of CAM. Setting up of infrastructure to begin with is very expensive.
CAM requires not only NC machine tools themselves but also an extensive software and hardware to develop the design models and convert them into manufacturing instructions. The output from the CAM software is usually a simple text file of G-code, sometimes many thousands of commands long, that is then transferred to a machine tool using a direct numerical control (DNC) program. CAM packages still cannot reason like a machinist. The field of computer-aided management is fraught with inconsistency.
While all numerical controlled machine tools operate using G-code, there is no universally used standard for the code itself. CAD systems tend to store data in their own proprietary format, so it can often be a challenge to transfer data from CAD to CAM software. There are some problems with CIM also. Existing equipment and software may be incompatible with each other leading to expensive updates or replacements. Extensive programming may also be required to produce optimal schedules and part sequence.
CAE: Computer Aided Engineering (CAE) systems are very useful systems for engineering area. Integrated or independent CAE systems are used by design engineers and specialists. Computer simulation is very significant tool for designers. The reason is to understand to the behaviour of the technical systems before their prototype production. Therefore many analytical programmes have been created in the last thirty years for engineering area. These programmes are entitled as Computer Aided Engineering (CAE).
Utilisation of CAD/CAM systems PRO/ENGINEER:
Pro/ENGINEER is full parameter 3D graphic CAD/CAM system, determined mainly for general manufacture engineering and for automation of design engineering. With graphical system Pro/ENGINEER is able to create fully, unambiguous and accurately spaced model of solid body simply and quickly. CONCLUSION: Utilisation of CAD/CAM systems is highly effective because it enables to reduce the process development time and the introduction of a new product in the market in a large scale. Recent technical developments have fundamentally impacted the utility of CAD/CAM systems.
For example, the everincreasing processing power of personal computers has given them viability as a vehicle for CAD/CAM application. Another important development is the establishment of a single CAD-CAM standard, so that different data packages can be exchanged without manufacturing and delivery delays.
References:
- Groover, M. P. : Automation, Production Systems, and Computer-Integrated Manufacturing. USA, January 2000, Prentice Hall
- Paper on Design for Engineering Unit 6 Research and Development Annette Beattie August 10, 2006 3. www. wikipedia. com
Cite this Page
Computers in Modern Manufacturing. (2018, Aug 04). Retrieved from https://phdessay.com/computers-in-modern-manufacturing/
Run a free check or have your essay done for you
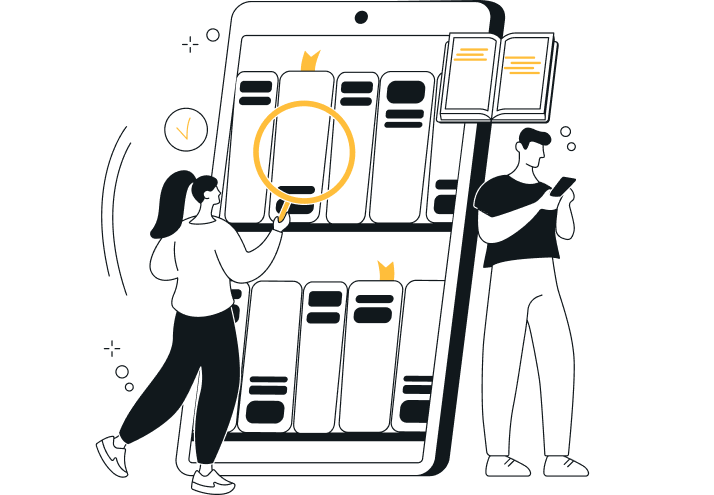