Health safety and the environment report feyzin
The aim of this project is to describe the incident which took place in Feyzin, south of France, on Tuesday January 4th 1966. This project describes the history of the refinery, a description of the LPG manufacture processes, the cause of the accident, details of the accident, inquires and safety measures, conclusion and personal recommendations.
A focus group for the project was the first approach on research to explore people's ideas and attitudes to the accident. There were several weekly group meetings excluding the weekly tutor meetings putting forward ideas discussing whether the accident could have been for seen and reasonable measures were in place. Each member of the group was assigned a particular area in which they were to collect information. The required information was gathered from various highly reliable sources such as a HSE investigation.
History And Background Information
Order custom essay Health safety and the environment report feyzin with free plagiarism report
Feyzin is situated in the suburbs of Lyon in the southern part of France. The France national petroleum was located in Feyzin.
The refinery at Feyzin had started operating in 1964. The main objective of this processing plant was to produce 1.7 million tonnes a year of LPG (liquefied petroleum gas). LPG is a by-product of the distillation of oil from crude oil. When the distillate is put under pressure its physical state changes into a liquid. It is in this form that LPG is transported around in cylinder tanks.
Because of the relatively short life p of the site prior to the incident, the cascade of events may be relatively short and that major issues will have risen during both the design and construction of the site. We can assume now that the plant was between its 1st and 2nd year of operation.
LPG is a combination of Propane and Butane. The LPG is used as an alternative to petrol.
The LPG is important because it is widely used as a fuel for vehicles and as cooking gas since its manufacture. They are also used as Industrial fuel and heating oils which are vital for many process plants.
LPG is employed for starting up solid-fuel and oil-fired boilers supplying turbo generators. It is potential stand by for gas turbine generating equipment run on interruptible gas supplies. Its use for peak-load turbines will be economical to some circumstances.
Cascade events
The causes of the deadly incident which took place at Feyzin
There were quite a few reasons reported which were believed to be the causes of the explosion.
Cause of the leakage
Three operators opened 2-inch valves which were mounted in series at a bottom of a 1200m3 propane spherical tank. The valves did not close at a LPG tank which contained 1200kl propane, which led to the leakage of LPG gas, a major cause of the explosion.
For LPG that is Propane gas, when the pressure is lowered to atmospheric one the temp drops to -40. At this temperature moisture in air is frozen, but also the moisture reacts with LPG forming a solid hydrate. So either the downstream valve did not close tightly because of hydrate formation or the valve handle was stuck by the frozen moisture. This accident was believed to be caused as the upstream valve was not opened fully and the pressure at the outlet of the first valve was near the atmospheric pressure, the pressure difference cooled. It is very wrong to operate the valve system like that. Therefore, the cause of the explosion is either the operator's human mistake or a mistake on the management not to inform the proper execution of the operation.
Cause of the ignition
The leaked LPG is presumed to be travelled for a distance and spread along the ground. A car driving down a local road might have sparked the ignition which is maybe due to the driver's cigarette or the car engine's hot temperature. Note that the layout of the plant was restricted to the landscape; a highway was constructed just 50m away from the large LPG tanks which exploded during the incident. Moreover there was no dike around the tanks which exploded, when large amount of LPG leaked, the vapour flew along the ground to the highway. The main cause of the ignition is that there was no dike around the LPG tanks and the distance regulation insufficient.
Secondly, the legs of the spherical tank were made of iron which weren't fire proof. Thirdly, is that the distance between the adjacent tanks was really close, The actual distance between the centre of the tanks was just 27m according to the facility information provided. This proves that the adjacent tanks were affected so easily from the explosion of the first tank.
Event
A BLEVE (Boiling Liquid Expanding Vapour Explosion) was the disaster that occurred at Feyzin. It is an explosion phenomenon caused by the rapid phase change (vaporization) of a liquid.
At 6:30am three operators started the water draining operation of a tank. Two valves were opened in series on the bottom of the sphere. When the operation was nearly complete, the upper valve was closed and then cracked open again. No flow came out of the cracked valve, so it was opened further. The blockage, assumed to be ice or hydrate, cleared and propane gushed out. The operator was unable to close the upper valve and by the time he attempted to close the lower valve this was also frozen open. The LPG leak started here because that valve was not closed completely. After a few minutes the operators were covered in propane vapour. The leaking LPG spread in the direction of the highway, with partially vaporizing. The alarm rang in the control room at this time.
At around 7:05am; the alarm rang and it is not clear if it rang throughout the Feyzin districts or just the Feyzin refinery. The first fire truck of the factory turned out immediately. After this the traffic on the highway next to the refinery was stopped. The fire brigade of Lyon arrived at 7:20.
Just after 7:30am, a car came and stopped on the local road where the traffic had not been stopped. The explosion apparently occurred after the car had stopped. The fire increased in power, spread along the leaking LPG, and the tank was overcome with flames immediately.
By 8:40am the first tank at the refinery exploded by the BLEVE. The second and third spherical tanks exploded five minutes later. Two more spherical tanks and many oil tanks burned continuously. The next day in the morning the fire was extinguished.
As a result of this it was reported that 18-81 persons died and about 80-130 persons got injured included members of the fire fighting team. The physical damage included five LPG tanks, many atmospheric tanks containing crude oil and jet fuel, and so on. The Feyzin Refinery suffered extensive damage.
The LPG tank farm where the sphere was located consisted of four 1200 m3 propane and four 2000 m3 butane spheres. The fire brigade arrived on site, but were not experienced in dealing in refinery fires, and it appears they did not attempt to cool the burning sphere. They concentrated their hoses on cooling the remaining spheres. About 90 minutes after the initial leakage, the sphere ruptured, killing the men nearby. A wave of liquid propane flowed over the compound wall and fragments of the ruptured sphere cut through the legs of the next sphere which toppled over. The relief valve on this tank began to emit liquid.
What is believed to have happened on the day of the accident is: the upstream valve was not opened fully and the pressure at the outlet of the first valve was near atmospheric pressure, hence the upstream valve was cooled by the pressure difference.
It is absolutely prohibited to operate valves in such manner. Therefore, the cause of the accident is either the operator's human error or a mistake on management side in not explaining the proper operation protocols.
Another contributing factor to the accident is that the operator did not close the downstream valve. There is insufficient information available to why this valve was not closed. It is assumed that either ice is generated in the downstream valve like in the upstream valve or a rapid large LPG leak occurred, the operator may have panicked when they could not close the upstream valve and therefore may have not remembered to close the downstream valve. Basically they had to decrease the downstream valve opening when the LPG began to appear in the drain water. Then the valve had to be closed at the end of the drain work. Either they forgot to carry out this procedure or they could not close the second valve because it had also become stuck by freezing.
- Valve A is closed
- Valve A cracks open
- Valve A becomes blocked due to freezing
- No flow through valve A
- Valve A is opened
- Ice block in valve A becomes dislodged
- Valve A freezes in open position
- Unable to close valve A
- Valve B freezes in open position
- Unable to close valve B
- Pressure sphere fluid leaks through open valves
- Fluid level in pressure vessel drops decreasing internal pressure
- Liquid propane begins to boil due to pressure drop
- Pressure in vessel increases due to liberated gaseous propane
- Fluid flow through valves A and B increases due to increase in pressure
- Vessel pressure continues to increase
- Pressure vessel ruptures
- Gaseous propane escapes vessel
Recommendations and summary
- Geographical location and details
- History of Feyzin, including cascade events
- Incident timeline and possible description of why it happened
- Geographical effects of the incident
- Results of the inquiry and official recommendations
- Personal recommendations not covered by the enquiry
Geographical location and details
In order to get a better understanding of the scale of the Feyzin incident, it is important to note the location of the site in regards to the local area in which the site was and still is positioned. This will give an indication to understanding the safety procedures that were in place at the time of the incident and how emergency procedures were carried out at the time.
It has proven very difficult to obtain a clear picture of the geographical location either prior to or following the incident of the site and so it will be assumed that the current location of the site, circa 2009, is the same location at the time of the incident. Close examination of this map may also indicate the most likely positioning of the epicentre of the primary detonation.
Sandwiched between the A7 Expressway to the east of the site and the 'Le grand large' river to the west, on close examination, it appears that some form of storage containers are located just west of the top E15 label in the image. This may lead us to assume that the storage containers were in the same location prior to the 1966 incident.
On a broader scale it may also be seen that this location is approximately 10 km south of the major city of Lyon. Research suggests that at the time of the incident, the site lacked any serious on site systems in case of a major crisis, relying more on the local public services to resolve anything arising such as the incident in question.
Again on close inspection of the map, it can be seen that the site is placed within a fairly urbanised area. Again we must assume a similar layout at the time of the incident though populations will be quite different from the 1966 incident and the 2009 map. This will assist in understanding the cause of the incident overall and the scale of the overall effect in this area.
Apart from just repeating the timeline for the actual incident, it is important to try and understand why the incident took place, outside of the events leading up to and after what happened.
The sequence of events surrounding the cracking and freezing of the 'upper' valve, and the subsequent rupture of the pressure vessel need to be understood, in order to get a better understanding of how such a crises may be avoided in the future. These events may only have taken place over a very short time frame but they are essential to understanding the crises.
One of the critical questions that should be asked is why following the closure of valve A and the subsequent cracking and freezing up of the valve, was the valve then opened. Thus allowing the ice block to become dislodged and the rest of the above sequence to take place.
The reasons for this particular action, in opening valve A may be described in four ways. The first possibility may be a simple case of curiosity. The valve was closed and froze, and so to check that the valve was still properly operational was then opened.
The second possibility is that the correct procedure for such an event was not properly followed. That the correct procedure would have stated that in such an event, the valve should have been kept closed and the problem be properly reported to maintenance. Therefore the valve operator was responsible for the incident that took place.
The third possibility is that no official procedure or training had been formulated for such an event. Therefore panic may have ensued resulting in the opening of the valve as a panic decision which can therefore be described as human error.
The fourth possibility is that the official procedure was followed properly and that the procedure was critically floored. So the issue of a misunderstanding of such an event or even ignorance of such was present at the time of this crisis.
The third possibility seems likely case based on the immediate actions of the individual as he made the decision not to use a phone close to the pressure tank and instead ran approximately 800 meters to the next nearest phone in the fear of causing a detonation of the released vapour cloud. The fourth possibility may also have some bearing in the crisis as prior to this event, the term BLEVE had still not been discovered or at least recorded prior to this.
The rest of the sequence should be covered in the full breakdown of the crisis.
An important issue to be considered is the overall control displayed by both the emergency and municipal authorities during the crisis. Even though the A7 expressway was closed following the leak, the authorities failed to close the local roads to all traffic, which resulted in a car being within 160 meters of the leaking pressure tank and causing the point of ignition.
The failings in the emergency service appear to be more in association with a lack of sufficient training in the order of dealing with industrial crises as it was primarily there to deal with public situations. This resulted in a fatal misunderstanding of how to control such a situation as a leaking pressure tank and resulting fire, due to a lack of prior knowledge which is strengthened in the term BLEVE only being created some 4 to 5 years later
Results of the enquiry and official recommendations
The official investigation was not fully resolved until 1971 by the Grenoble court case. This may have been due to political reasons or due to the enquiry investigating why the crisis had occurred in the first place. On the principal that such events have happened since the Feyzin disaster, it cannot be assumed that the enquiry was successful in bringing about sufficient change in the safety of pressurised fluid containment.
Personal recommendations not covered by the enquiry
The first recommendations are for the design and construction of all current and future proposed plants dealing with pressurised fluid containment. The second recommendations are in association with work practices involved on chemical plants in general.
Third valve (reserve)
A third valve should be installed for the purpose of maintenance and crisis control. To be kept open at all times so as not to induce unnecessary wear and tear on the valve. When maintenance is required to be carried out on the two principal valves, the reserve can be shut to allow for maintenance to be carried out safely. In the event of a crisis similar to that of Feyzin, this valve can be shut as an emergency back up system in minimising fluid leakage from the pressure vessel.
'Cold' pipe lagging
In order to prevent freezing of any pipes or valves dealing with potentially 'cold' fluids, lagging should be fitted to all appropriate pipe work and fittings in order to minimise any potential freezing of these systems. Systems not dealing with 'cold' fluids must be scrutinised independent of this point.
Rubber sealed pressure box
High pressure boxes should be installed around all vital valves dealing with pressurised fluids. They should be big enough to allow for ease of working but not to big as to incur any additional hazard to plant running. They should be designed with an environmental rubberised seal so that if a valve begins to leak, the box can but locked shut with an emergency key. Thus minimising any excessive leakage until the situation can be bought under control. See: A third valve (reserve)
Deluge system - Control box and master switch
If geographically located near to a natural water source as in the case of the Feyzin site, a deluge system should be installed. It must have pipe work leading to all critical locations around the entirety of the plant. This system must be regularly checked so as to remain in good working order. Each piece of equipment covered by this system must be fitted with a local switch, so in the event of either a leak or a fire, the operator can activate the system in order to prevent escalation of the situation.
A central control post should be equipped with a control panel covering all local deluge systems via an override system and also be installed with a master switch that can activate all systems at once. This will allow for the main operator to activate systems in a sequence or all at once should a major sit6uation occur. Communication is vital for this system to work properly, so an emergency phone network should be installed in order to insure proper working of the system. This will only be part of the solution and fire brigades properly trained with dealing with such an event will ensure that the crisis is resolved effectively.
Completion of site before going online
It is important that a site should be safe to operate before going online. In the case of Feyzin, the site was still under construction when the accident occurred. Even though construction work may not have been the cause of the incident, neither can the incompletion of the site be assumed to have helped in the scale of the incident itself. So before a plant can go online, all safety systems must be installed.
This is not to be confused with site maintenance which is an ongoing process throughout the plants lifetime.
Inclusion of full earthworks around site
Only effective if any vapour or fluid is heavier than atmospheric air. May also be affected by environmental conditions, however if all other systems are overwhelmed, then this system is designed to delay the spread of any possible leak. Earth works should be built around all containment vessels and if possible the entire site. So in case of an emergency, any leaking vapour may be contained within the confines of either the leaking vessel or the plant.
Preventions
To prevent valves from freezing redundant sampling valves and drain valves are installed in series. In the tank involved in this accident, the double valve was already installed. In the LPG tank, the doubling of the valve is a minimum requirement as in the case of a single valve, there is a strong possibility that the valves main body will be cooled, damaging the closing function of the valve by freezing of the moisture in the air. The distance between the two valves must be sufficient to prevent the low temperature of the second valve affecting it. The size of the second valve must be approximately 10mm or less. It is recommended that a distance of 1m or more to be allowed between valve 1 and 2.
Countermeasures in other facilities around the world
- Dike installation: - LPG spreads along the ground as it is heavier than the air. A dike is effective for prevention the spread of LPG.
- As a precaution against the BLEVE phenomenon, the tank wall must be cooled by placing water showering facilities above the tank.
- The Tank legs must be fire proofed. If the legs are made from iron they can be damaged by fire.
- The distance between tanks is kept to prevent the spread of fires. The minimum distance is generally the diameter of the larger tank, however if possible greater distance between tanks is recommended.
- Gas detectors are installed within the facility.
Conclusions
The Feyzin accident was a cause by human error and unsafe conditions. The accident could have been prevented if correct procedures were followed and if the plant was designed with appropriate fail safe systems such as a dike and LPG detectors.
This accident lead to a greater understanding of the BLEVE phenomenon and has given future LPG companies the knowledge of its existence which has led to further research into this occurrence.
Explosion of LPG tanks cause devastating damage. The companies that store and handle large volumes of LPG must consult with the local government to ensure they can communicate with the local government, inform local inhabitants and relay instructions for how to restrict traffic in case of an LPG leak.
It has now become clear that the location for which the plant is located must be thoroughly studied, to ensure there is enough distance between the plant and built up areas. Without doubt future companies designing LPG refinery plants can benefit from the findings of this accident report.
Glossary
- BLEVE - Boiling Liquid Expanding Vapour Explosion
- LPG - Liquefied Petroleum Gas
Cite this Page
Health safety and the environment report feyzin. (2018, Jan 07). Retrieved from https://phdessay.com/health-safety-environment-report-feyzin/
Run a free check or have your essay done for you
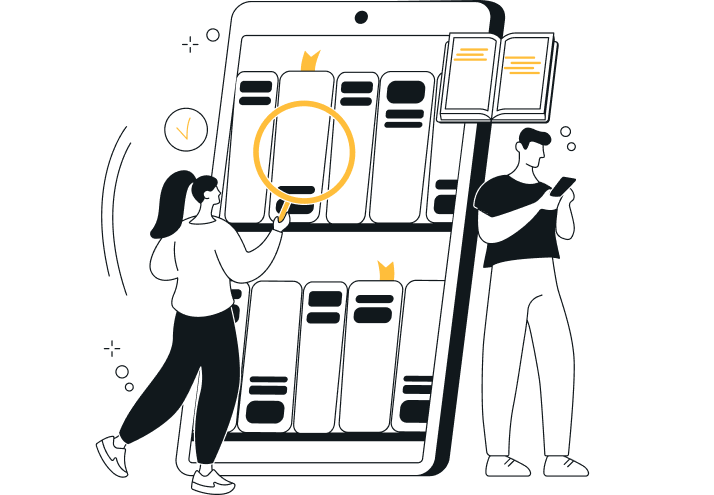