Reflection Essay on Role of Operations Management
Role of Operations Management Operations management is the design operations and improvement of systems that create and deliver a company’s products and services. In other words, “is the process of taking input such as raw material and component and turning it in to out put by adding values” (Shaikh, 2010). Any activity that relates to the management of the entire business process that produces goods and services falls into the operations category. Competition among today’s organizations has become immense and is getting tougher and tougher day by day since more new companies are starting businesses in the same industry.
Whether they are from the manufacturing sector or service sector, the need for cutting the unnecessary costs, achieving maximum efficiency, and implementing operations management strategies is increasing with the passage of time. Therefore, more focus is being laid on Supply Chain Management these days by the businesses in order to set up certain operations approaches, distribution systems, and capacity layouts that not only reduce redundant costs but also provide better quality goods and services to the customers.
This paper will discuss two operations approaches for each of these sectors manufacturing and service and would relate those approaches to quality control and efficiency that can be achieved by the businesses. Operational Approaches for Manufacturing Organization There is no wonder to know that the manufacturing organizations deal with the inventory much more as compared to the service organization. The inventory includes raw materials, complementary parts, actual or finished products, and other packing materials therefore, the two most used operational approaches for by these organizations are Lean manufacturing approach and Outsourcing.
Order custom essay Reflection Essay on Role of Operations Management with free plagiarism report
Lean manufacturing is the approach that identifies and minimizes waste by adopting continuous improvement to satisfy the customer’s demands. It ensures maximum quality by examining each part of the good after its production to identify the flaws that might be there (Blacharski, 2010). Second approach is outsourcing where the organizations that are not efficient enough in producing a certain product or material, assigns that production task to some other company, entity, business, or vendor that actually possesses the skills, mastery, technology, and resources to produce and deliver it.
Operational Approaches for Service Organizations Just-in-time approach and the Balance between Degree of labor and degree of customization are the two operational approaches that are often used by the service organizations. Just-in-time or JIT system is designed and implemented in order to produce or deliver services just as they are needed. In this approach the raw material or inventory (potatoes or chicken) is delivered to the service department or facility such as, Mc Donald’s restaurant just at the time when it is needed.
And secondly service organizations often try to maintain the balance between the degree of labor employed for the provision of services and the degree of customization based on the needs and wants of the customers. Advantages and Disadvantages The advantages of Lean manufacturing include reduced set up times, less lead times, lower expenditure of materials, simplification of materials for easy identification, reducing wastes, standardizing operating procedures, sustaining better environment and results, good maintenance, and safe practices (Heizer & Render, 2010).
Disadvantages can be excess time spent on cleaning and identification purposes, also with the use of resources and money. Advantages of outsourcing include reduction in inventory costs, reciprocity, preserve supplier commitment, better production results, and offsetting the lower technical expertise and capacity the company has. Disadvantages include increase in expenditure, high production costs, and the company might not obtain desired quality or core competence. Advantages of JIT include reduction in inventory costs, storage costs, handling costs, cutting costs of quality, and improving quality.
There is one major disadvantage that can be the stoppage of production or delivery of services if inventory is not delivered at the right time. The degree of labor and customization provides better customer satisfaction, customer loyalty, increased ordered and sales, less wage costs, and service variety. Disadvantages might be the increased costs in setting up new technology or method for providing unique or customized service for different customers, their maintenance costs, technology costs, and increased layoffs.
In conclusion, I think this will improve my approach as in one day starting my own business to understand how operations management can be beneficial to a wide variety of organizations, both big and small. Operations management plays a vital role in the daily functions of an organization whether the company has identified this or not. Every process that a company employs to meet its strategic goals is a result of operations management.
Operations management aids a company in becoming well-organized, operating more efficiently and productively, staying competitive and improving customer relations. Nationwide Business Interview I expect to learn what is fundamental to achieving and more importantly sustaining a career and business success, particularly within a competitive sales and marketing environment. The most challenging task is to motivate and manage employees to get on the same page and get something planned and completed on time and within a budget.
The most critical skill you need as a manager is to understand and manage through tough current economic conditions, such as planning and executing, cost-control, developing and motivating employees and communicating and managing change. To have great communication skills for sales, negotiaton and networking also leadership skills is essential in order to reach your goals. . A big part of surviving in business is about solving problems fast and effectively. An manager needs good problem solving skills.
The important trend I have experienced is and crucial is customer experiences scanning our consumer trends, you will be able to understand where your industry may be headed, or even better, shape its direction yourself, by introducing new products and services that catch the competition off guard. The steps I take to organize my task for today is to first make a list of all tasks that you have to do. At the start of the day I select my most important items and start working on them. If a new task comes up during the day, I keep working on the current task unless the new task is more important.
When deciding which tasks take priority when completing a project is deciding what needs to be completed first and it depends what is critical to meet deadline. To be effective in a business crisis your communication plan must be and easy to reference document that contains decisions, action, resources and contacts you and your team will need to represent your organization in the high pressure of a crisis. Employees should always keep in mind the interests of the organization and realize the company standards are more important than the customer’s nterests to bend the rules.
Bibliography 1. Blacharski. D. (2010). What is Lean Manufacturing. Retrieved on November 13, 2010. From http://www. wisegeek. com/what-is-lean-manufacturing. htm 2. Heizer. J & Render. B. (2010). Operations Management. Eighth edition. Pearson Education, Inc. Prentice Hall. Dorling Kindersley India Pvt. Ltd. 3. Shaikh. S (2010). Operational Approaches. Retrieved on November 8, 2010. From http://safeshaikh. com/business/supply-chain-management/operational-approaches/
Related Questions
on Reflection Essay on Role of Operations Management
Cite this Page
Reflection Essay on Role of Operations Management. (2018, Sep 13). Retrieved from https://phdessay.com/role-of-operations-management/
Run a free check or have your essay done for you
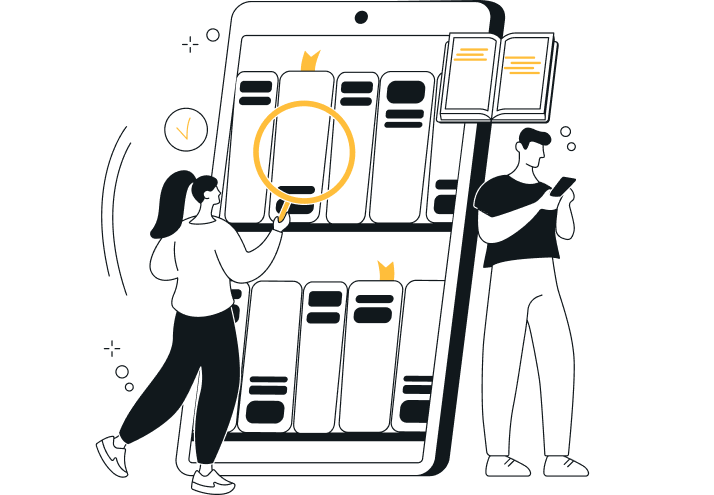