Potato Starch
n the past, fields of wheat and rows of potatoes were seldom destined for anything more than a rumbling tummy. But bio-products have come a long way since people first branched out into weaving hemp into clothes and pulping papyrus into scrolls. Today the line between Mother Nature and man made has never been more blurred. Animals are re-engineered into living drug factories, crops fuel our cars and now plants are increasingly being repackaged as the epitome of the synthetic world – plastic. Wheat, maize, vegetable oils, sugar beet and even the trusty spud are finding new life as water bottles, car fuel lines and laptops. Wheat, maize, vegetable oils, sugar beet and even the trusty spud are finding new life as water bottles, car fuel lines and laptops. | Bio-plastics harness the natural structures found in crops or trees, such as slightly modified forms of the chains of sugars in starch or cellulose, that share the ability to be easily reshaped that has made conventional oil based plastics so useful. Bio-materials scientists are also constantly tweaking these natural structures to try and better replicate the durability and flexibility of conventional plastics.
Global business is now turning to bio-plastics for an increasing number of applications, as consumers and governments demand cleaner alternatives to petroleum based technologies and their reckless production of the greenhouse gas CO2. Worldwide players, such as DuPont and Toyota Motor Corp, are making vast investments in new technologies and processing plants with the hope of cornering a multi-billion pound industry. The "BC" at Bangor University in North Wales has 18-years experience of working with large companies and Non-Governmental Organisations (NGOs) to find sustainable and viable bio-based alternatives to man-made materials.
BC director Paul Fowler points out that “practically anything that you can find as polyethene you can find as a bio-plastic. You are talking about a whole range of everyday products - cups, combs and wrappers, everything you can think of is out there. There are inroads being made all the time - on the one hand there is research into trying to get biological alternatives to replicate the properties of conventional plastics and on the other hand people are looking at the natural properties of these plants and trying to find an application for them. Most of the manufacture is happening in the US and continental Europe.
Order custom essay Potato Starch with free plagiarism report
The UK is a producer of wheat starch and biotimber but the only major bioplastic producer is Innovia Films in Cumbria, which produces cellulose films. ” Innovia Films has an annual turnover of ? 400m, employing 1,200 people worldwide and producing more than 120,000 tonnes of film – used in packaging to protect food. Japan is also forging ahead, from the leading role in bioplastic production played by Toyota to its recent passing of a triumvirate of laws pushing forward environmental initiatives. In South Korea too there is a rapid drive to replace conventional plastic packaging with polylactic acid bio-plastics.
Fowler says bio-plastics also offer an opportunity to get a double return for the energy used in their manufacture – first as a useful item and secondly as a fuel source. “My view is that we should burn them at the end of their life to recover energy, which could be then used to produce new materials,” he said. “In the first instance you have a valuable resource can use, be it as packaging or a shopping bag, and then you are also getting some energy back at the end of it. The biggest advantage of such bio-materials is the reduction of CO2 emissions in their production over petrochemical-based plastics. He also suggests that burning bio-plastics would also avoid the problems caused by them breaking down and producing methane, which is 25-times more potent as a greenhouse gas than CO2. The BC is currently looking at developing naturally-derived alternatives to phthalates, which are plasticisers added to PVCs to make them more flexible in products such as electrical cable flex. It follows concerns that phthalates are metabolised in the body into substances that can mimic the body's own hormones, including those concerned with fertility.
The centre is also developing bio-resins, natural alternatives to synthetic resins such as phenol and formaldehyde. What types of bioplastic are there? The common types of bio-plastics are based on cellulose, starch, polylactic acid (PLA), poly-3-hydroxybutyrate (PHB), and polyamide 11 (PA11). Cellulose-based plastics are usually produced from wood pulp and used to make film-based products such as wrappers and to seal in freshness in ready-made meals. Thermoplastic starch is the most important and widely used bioplastic, accounting for about 50pc of the bio-plastics market.
Pure starch’s ability to absorb humidity has led to it being widely used for the production of drug capsules in the pharmaceutical sector. Plasticisers, such as sorbitol and glycerine are added to make it more flexible and produce a range of different characteristics. It is commmonly derived from crops such as potatoes or maize. | FOMA(TM) N701iECO phone made of PLA bioplastics reinforced with kenaf fibres developed by NEC, UNITIKA and NTTDoCoMo © Paul Fowler| PLA is a transparent plastic whose characteristics resemble common petrochemical-based plastics such as polyethylene and polpropylene.
It can be processed on equipment that already exists for the production of conventional plastics. PLA is produced from the fermentation of starch from crops, most commonly corn starch or sugarcane in the US, into lactic acid that is then polymerised. Its blends are used in a wide range of applications including computer and mobile phone casings, foil, biodegradable medical implants, moulds, tins, cups, bottles and other packaging. PHB is very similar to poylpropylene, which is used in a wide variety of fields including packaging, ropes, bank notes and car parts.
It is a transparent film, which is also biodegradable. Interest in PHB is currently very high with companies worldwide aiming to expand their current production capacity. There are estimates that this could lead to a price reduction below five euros per kilogram but this would still be four times the market price of polyethylene in February 2007. The South American sugar industry has commited to producing PHB on an industrial scale. PA 11 is derived from vegetable oil and is known under the tradename Rislan.
It is prized for its thermal reistance that makes it valued for use in car fuel lines, pneumatic air brake tubing, electrical anti-termite cable sheathing and oil and gas flexible pipes and control fluid umbilicals. These are often reinforced with fibres from the kenaf plant, a member of the hibiscus family traditionally used to make paper, to increase heat resistance and durability. At the cutting edge of bioplastic technology lie polyhydroxyalkanoate (PHA) materials. These are derived from the conversion of natural sugars and oils using microbes.
They can be processed into a number of materials including moulded goods, fibre and film and are biodegradable and have even been used as water resistant coatings. What are the benefits of bio-plastics? - Reduced CO2 emissions. One metric ton of bio-plastics generates between 0. 8 and 3. 2 fewer metric tons of carbon dioxide than one metric ton of petroleum-based plastics. Electronic giant Sony uses PLA in several of its smaller components, including one of its new walkmans, but in future hopes to use PLA-based polymers to reduce its carbon dioxide emissions by 20pc and non-renewable resource input by 55pc compared to oil-based ABS. Rising oil prices Despite currently costing more to produce than conventional plastics bio-plastics are becoming more viable with increasing and instability in oil prices, which are in turn triggering spikes in conventional plastic costs, illustrated in a sharp upturn two years ago. Dwindling oil supplies means that man will eventually be forced to turn to a sustainable basis for plastics. - Waste Bio-plastics reduce the amount of toxic run-off generated by the oil-based alternatives but also are more commonly biodegradable.
The US’s second largest biopolymer producer Metabolix, of Cambridge, Massachusetts, claims that its plastics are biodegradable in composting bins, wetlands and the oceans. On the flip side not all bio-plastics are biodegradable and there are a growing number of conventional plastics that can naturally break down. The downside of their biodegradability is the methane that can be released as the bio-plastics decompose is a powerful greenhouse gas. - Benefit to rural economy
Prices of crops, such as maize, have risen sharply in the wake of global interest in the production of biofuels and bio-plastics, as countries across the world look for alternatives to oil to safeguard the environment and provide energy security. - Enhanced properties In some fields engineered bio-plastics are now beating oil-based alternatives at their own game. Multinational materials giant Arkema has produced a form of Rislan PA11 that is being used in Europe and Brazil in fuel lines to carry biofuels as it is better able to withstand the corrosive effects of biofuels than oil-based alternatives such as polyamide 12.
Rislan is widely used in oilfield applications as well as automotive brake lines. Elsewhere innovations in PA11 production are helping increase car passenger safety and reduce the risk of accidents by inhibiting spark ignition in the fuel lines. US car giant General Motors has replaced its non-conductive fuel-pump modules for new North American car models as it felt it was the best material for the job.
In the US chemical multinational DuPont says it has developed a bioplastic derived from corn sugar that has superior stiffness and strength to its naturally based competitors. Global electronics corporation NEC has produced a kenaf-reinforced laptop casing, made of 90pc PLA, which helps reduce overheating by conducting heat better than stainless steel coupled with high temperature resistance and increased strength. Who are the flagwavers? Bio-plastics are not being produced by a group of hippies brewing up in their garage.
Some of the world’s largest companies including multi-billion dollar chemicals company DuPont, car manufacturer Toyota, UK-based Innovia, US food processing behemoth Cargill and electronics giants NEC and Fujitsu are pouring money into driving the technology and production forward. NEC and its partners Unitika and NTT DoCoMo produce mobile phone and laptop casings based on plant-derived bio-plastics, mostly PLA. NEC plans to expand its green credentials by substituting more than 10pc of the oil-based plastics in its electronic products with bio-plastics by 2010.
Toyota Motor Corp uses mainly PLA bio-plastics, derived from sweet potatoes corn and sugar beet, reinforced with kenaf to produce components for its cars such as the Prius and Lexus. It hopes to grow its bio-plastics division into a four billion yen business by 2020 and capture two thirds of the global market for petroleum free plastics. Fujitsu introduced its FMV BIBLO notebook PC series two years ago, which it has manufactured using a material called Ecodear, a combination of 50 pc PLA and an oil-based plastic.
Fujitsu is now developing a castor oil derived PA 11 plastic with Arkema, which is more flexible and will help expand its use of bio-plastics in notebook computers. The material can withstand repeated bending thanks to scientists weakening the interaction of the chain molecule in PA 11 and relaxing the stereoregularity of their organisation. The improved durability means its prototypes of PC cover components consist of 60-80 percent of the new bioplastic, an unprecedented achievement to date.
Fujitsu is also using high density fillers to increase strength and extend its use into notebook covers and other applications requiring high impact resistance. The new material is expected to cut carbon dioxide emissions by 42pc compared to oil-based nylon 6/6. DuPont in particular is continuing to expand the market for bio-plastics and plans to continue to offer hybrid bio/conventional plastic materials until the market matures, which could eventually cost less than the oil-based alternatives.
DuPont has teamed up with sugar giant Tate ; Lyle to build the world’s largest aerobic fermentation plant in Loudon in Tennessee in the US for the production of bio-PDO, with a capacity of 45,000 metric tonnes a year. The largest commercial producer of bioplastic in the US is NatureWorks, owned by Cargill. The company’s plant in Blair, Nebraska uses corn sugar to produce PLA plastics packaging material and its own Ingeo-brand fibres. What lies ahead?
With US President George Bush’s recent pledge to produce 35 billion gallons of renewable and alternative fuel by 2017 - driving the price of maize up 60pc in the past two months - the farmer’s field is fast turning into a high tech bio-battleground. Mr. Fowler warns that the still fledgling industry will have to fight for space and commercial viability as millions of hectares are given over to corn, rapeseed and sugarbeet for bio-fuel production. "There is a real tension between the use of agriculture for fodd versus plastics and other non-food uses and this whole move to produce new fuels," he said.
Whereas only two years ago plant materials were at the cheap end of the market and bio-products such as straw had little value, now it is really much more costly. There would have to be a step change in the extent of the production to match oil-based plastics. The amount of bioplastics produced worldwide is less than 200,000 tonnes a year; contrast that with the more than 30 million tonnes of oil-based plastics. You can see we have a long way to go before they replace conventional plastics". - July 2007
Cite this Page
Potato Starch. (2017, Apr 04). Retrieved from https://phdessay.com/potato-starch/
Run a free check or have your essay done for you
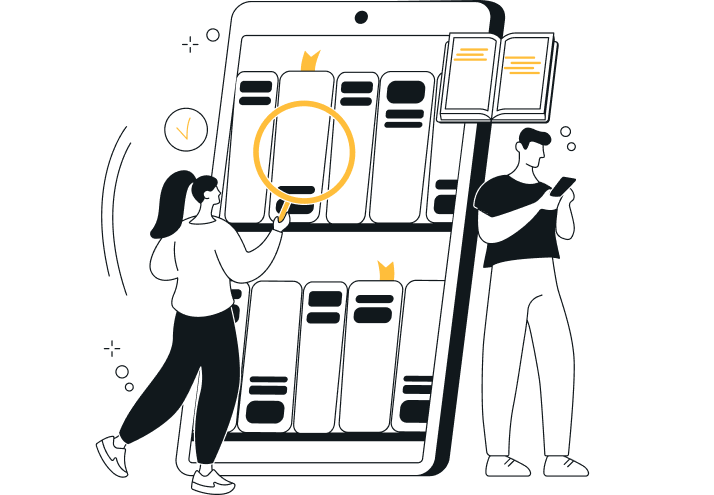