National Cranberry Cooperative Critique Essay
Background National Cranberry Cooperative
(NCC) had faced operational problems at Receiving Plant #1 (RP1) during the peak harvest season in the fall of 1995, which had resulted in the unhappiness of the owners of the Co-operatives and high labor cost, despite the purchase of an additional dumper. To avoid the same problems in the coming peak season, it is important to analyze the plant operations based on predicted demands and make recommendations if new equipment should be purchased before the fall of 1996.
During the peak seasons, RP1 faces 2 key operational problems:
Order custom essay National Cranberry Cooperative Critique Essay with free plagiarism report
- Long idling time of trucks and drivers prior to unloading berries at the plant; and
- High overtime cost due to the long plant operation hours. The long idling time of trucks and drivers caused extra cost and much unhappiness among the growers, who are the owners of the cooperative. In spite of this, NCC’s profits are not affected. On the other hand, high overtime cost will negate the revenue from the sales of berries, affect profits, and is a more crucial problem to be solved.
Plant Operations Analysis
The process flow diagram for RP1 up to the separation processes, including the process and storage capacities, is shown in Appendix A.
Following assumptions were made to calculate the capacities:
- There are 2 continuous flow processes in RP1, 1 for wet berries and 1 for dry berries;
- Berries flow continuously at a constant rate throughout the entire process;
- There is negligible flow time at the receiving and testing process, and the process is treated as an inventory;
- Trucks spend 7 to 8 minutes to empty their contents and leave the platform and it was assumed that an average of 7. minutes was required to unload a truck carrying 75 barrels of cranberries at each of the dumping units.
Implied Utilization
From the implied utilization, it was determined that the operations at RP1 are process constrained, with the capacities of both the drying and separating processes lower than their demands. It was also identified that the drying process is the bottleneck of the operations and will require 63% more capacity to process the demand for wet berries. Although not the bottleneck, the separating process requires 17% more capacity to process the demand for berries. NCC is concerned about the overtime cost incurred from the peak harvest season and the plant operation time would be determined to address this concern. Another concern is the waiting time for the trucks and drivers before unloading berries at the dumpers and the waiting time required for the last truck would be determined.
The following assumptions were made:
- There are no berries inside the holding bins before operations begin each day;
- There is no idle time between processes and all processes are able to operate at full capacity;
- Due to the peak season, the dryer operators will start work at 7:00 am;
- As the bottleneck process is the one processing wet berries, holding bins #17 – 24 would be used to hold wet berries only to optimize plant operations thus making total wet berries holding capacity to be 3,200 barrels;
- Trucks will arrive at RP1 at a constant interval over a period of 12 hours starting from 7 am. Figure 1 illustrates the plant operation time and the truck waiting time.
Wet Bins (barrels) Berries waiting on trucks Figure 1 Process Flow of Wet Berries at RP1 In the current plant setup where there are only 3 dryers, the holding bins will be filled up at 380 barrels per hour, which is the excess demand flow rate (980 barrels per hour) over the processing capacity (600 barrels per hour). At this rate, the wet bins would be completely filled at 3:25 pm. At 7:00 pm, when the last truck has arrived at RP1, 4,560 barrels of wet berries would have accumulated, of which 1,360 barrels would be on the trucks. With the plant processing rate of 600 barrels per hour, the trucks would be emptied by 9:16 pm with the last truck having waited for 2 hours 16 minutes. The entire process stops at 2:36 am, with the total processing time of 19 hours 36 minutes. Potential Solutions Installing a new dryer will increase the drying capacity to 800 barrels per hour but this process will still remain the bottleneck (with implied utilization of 123%). In a typical peak harvest day with 16,800 barrels of berries delivered, the rate of accumulation of wet berries is reduced to 180 barrels per hour and a total of 2,160 barrels will be accumulated at 7:00 pm. The entire operation will complete at 9:42 pm, with the total processing time of 14 hours 42minutes (Figure 1). At the same time, there would be no truck waiting time as the holding bins will not be filled up completely before 7:00 pm.
To determine savings, the following assumptions were made:
- 2 shifts will be implemented during the peak season and overtime is paid after 11:00 pm;
- The processing capacity of RP1 is not affected by the implementation of the shifts;
- Workers would be paid for the full shift (8 hours a day) even if plant operations end before 11:00 pm;
- Only 8-9 seasonal workers would be used to do overtime and an average of 8. 5 workers is used for calculations. With the current RP1 setup, overtime cost is $37,087 (8. 5 workers x $12 per hour x 3. 6 overtime hours x 101 peak season days). With the additional dryer, no overtime will be required and the cost savings is $37,087. The cost of the dryer ($60,000) exceeds the cost savings for the coming season.
As such, NCC’s investment in the dryer will be recovered in 1. 6 seasons ($60,000/$37,087) and net cost savings from the additional dryer will be produced during the 1997 peak season. Another option to improve the process is to install two additional dryers that would increase the drying capacity to 1,000 barrels per hour and the drying process will not be the bottleneck anymore (with 98% implied utilization). The new bottleneck will be the separating process. At this point, the rate of accumulation of berries will be 200 barrels per hour resulting in 2,400 barrels of berries accumulating in the bins by 7:00 pm. Of these, 1,680 barrels are wet berries and 720 barrels are dry. After 7:00 pm, all berries will be separated in 2 hours (2,400/1,200). The entire operation will complete at 9:00 pm (Figure 1). There would be no truck waiting time as both wet and dry holding bins will not be filled up completely. Installing the second additional dryer would cost yet another $60,000 but would benefit only by reducing the total processing time by 42 minutes compared to the processing time achieved by installing one additional dryer.
This reduction in time is not considerable compared to the capital that would be invested to install the second additional dryer. Hence this option may not be viable to choose. The third option to consider is to convert some of the holding bins for the dry berries to hold wet berries at a cost of $10,000 per bin. This solution will reduce the waiting time of the trucks but does not reduce the overtime cost for the plant as the bottleneck capacity is not increased and operation will continue to end at 2:36 am.
Recommendation
After analyzing all 3 options, it is recommended that one additional dryer be installed. This will eliminate both the need for overtime expenditures and the waiting time for trucks and drivers at a minimal cost. There will be overtime cost savings of $37,087 when compared to the current plant setup. Growers will also save on truck leasing cost although it does not directly affect the profits of NCC. The cost will be recovered in 1. 6 seasons and is expected to turn out as a good long term investment.
National Cranberry Cooperative Critique Essay. (2016, Dec 21). Retrieved from https://phdessay.com/national-cranberry-cooperative-182790/Cite this Page
Run a free check or have your essay done for you
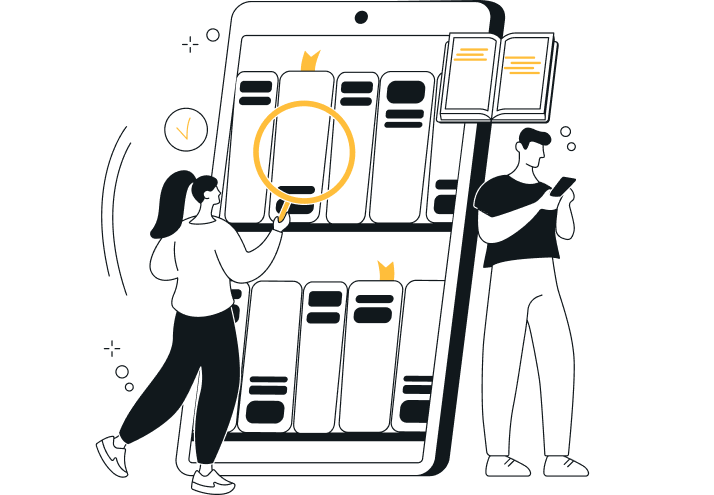