Methodology Of Six Sigma
The application of static-tactical methods to analyze data, study and monitor process capability and performance Methodology of Six Sigma used at Allied Signal Step 1: Define ; Identify the projects that are measurable. Projects are defined including the demands of the customer and process. the Initial stage of starting the project and the most significant step. Step 2: Measure The current level of quality is measured into Sigma level ; It precisely pinpoints the area causing problems. It forms the basis of the problem-solving. ; Project defects must be precisely defined and all possible and potential causes for such problems must be identified in this step. ; Subsequently such problems are analyses statistically. Step 3: Analysis ; In this step, when and where the defect occurs is investigated.
Projects are statistically analyses and the problems are documented. ; Major elements to be performed In the 'Analysis' step are as follows: o Projects must be statistically and receives defined in terms of Sigma. O The gap between the target and the actual state is clearly defined in statistical terms like mean and moving average. O A analysis is carried out to reduce the potential causes into few causes. Finally based on above steps, the financial implication of the project is calculated and further review is carried out if necessary.
Tools for analysis Flow Chart / Process Maps Failure Mode & Effect Analysis Statistical Tests Parent charts Design of Experiments Control charts Measurement system evaluation Quality Function Deployment (SF). Step 4: Improve Improvements for the potential causes identified in the 'Analysis' step are carried out in this step. Solutions to all the potentials problems must be found. ; The choices are how to change, fix and modify the process. ; A trial run must be carried out for a planned period of time to ensure the revisions and improvements implemented in the process result in achieving the targeted values.
Order custom essay Methodology Of Six Sigma with free plagiarism report
The steps are repeated if necessary. Step 5: Control Proper control and maintenance of the improved states are established in this step. It is also a step to regularity the new method. ; The results and accomplishments of all the improvement activities are documented. There is continuous monitoring of whether the improved process is well maintained. Strengths of Six Sigma Six Sigma is a relatively new concept. It was originally developed by Motorola in 1986. Six Sigma signifies a process of six standard deviations normally distributed about the mean. Disciplined methodology that utilizes a set of tools for continually improving the operational performance of an organization. ; Minimizing the variability and waste within any of organizations processes ; Produce no more than 3. Defects per one million opportunities (DEMO), a theoretical Six Sigma process would only make 0. 002 DEMO. Six Sigma takes into account realistic process behavior and includes a plus or minus one and a half sigma process shift about the mean for a normally distributed process. This one and a half sigma shift then equates to 3. 4 DEMO.
This can still be classed as a zero defect process or close to near perfection. Defects per Million Opportunities (DEMO)% Accuracy one Sigma 691,500 30. 85% Two Sigma 308,500 69. 15% Three Sigma 66,810 93. 32% Four Sigma 6,210 99. 38% Five Sigma 233 99. 977% Sigma 3. 99. 9997% Six Sigma utilizes its tools which include statistical methods to improve the quality of process outputs by identifying and removing the causes of defects. The Six Sigma tool set can also be used at the design and innovation stage to create designs Organizations that adopt the Six Sigma initiative have to train their personnel to varying levels of knowledge.
These employees are then certified to that level after successful examination and projects. Typical Six Sigma levels of certification are Blue belt, Green belt, Black belts & Lean expert. Master Black belts are created to train and enter new Six Sigma employees. Six Sigma champions are trained who are usually from senior management in organizations. The champion's role is to form Six Sigma teams capable of defining the processes that require improvement within the organization. These teams are usually created from cross-departmental personnel including, design, production, purchasing, quality and finance.
These teams are given projects that follow a defined sequence of steps with clear cost cutting objectives which are usually cost reduction or profit increase. Figure 6. 1. 1 Quality Improvement Improved process flow Employee Skills Improve market shares ; Earnings and profitability Customer Satisfaction Generates sustained success Sets performance goal for everyone Enhances value for customers Accelerates rate of improvement Promotes learning across boundaries Executes strategic change In almost all Six Sigma projects some type of re-design is necessary to create a more robust process capable of Six Sigma outputs.
The decisions made within a Six Sigma project are based on actual calculated data and statistical methods. Quality management System used at Honeywell Honeywell had developed and was using a bespoke quality assessment model called Honeywell Quality Value (WHQL). WHQL was based upon two different business excellence models, which are the ; Malcolm Baldrics Quality Model ; European Foundation for Quality Management (FEES) The main constituents of the WHQL where based from the Malcolm Baldrics Quality Model, whilst the remainder where based from the FEES model.
The Baldrics and the FEES are similar models in that are balanced both internally and externally and give a holistic view of how to operate a business. These balanced models used by the WHQL include strong customer orientation as well as being internally process focused. This allowed Honeywell to be highly responsive to their customer needs, thus enhancing the company's competitiveness within the marketplace. Strengths of Honeywell Quality Value The Honeywell Quality Value (WHQL) was based upon two different business excellence models, as stated above which are the 1.
Malcolm Baldrics Quality Model 2. European Foundation for Quality Management (FEES) measure itself. The Honeywell Quality Value provides the framework for how a business should be run as a whole. It is a way of measuring the effectiveness of an organizations quality system and its business results. The main criteria of the Malcolm Baldrics Model are: ; Leadership- This category examines how the organization's senior leaders 'personal actions guide and sustain the organization.
Also examined are the organization's governance system and how it fulfills its legal, ethical, and societal responsibilities and supports its key communities. ; Strategic planning - The Strategic Planning category examines how the organization develops strategic objectives and action plans for operating efficiently. Also examined are how the chosen strategic objectives and action plans are implemented and changed if resistances require, and how progress is measured ; Customer focus - The Customer Focus category examines how the organization engages its customers for long-term marketplace success.
This engagement strategy includes how the organization listens to the voice of its customers, builds customer relationships, and uses customer information to improve and identify opportunities for innovation. ; Measurement, analysis, and knowledge management - The Measurement, Analysis, and Knowledge Management category examines how the organization selects, gathers, analyzes, manages, and improves its data, information, and knowledge sets and how it manages its information technology.
The category also examines how your organization uses review findings to improve its performance ; Workforce focus - The Workforce Focus category examines the organization's ability to assess workforce capabilities and capacity needs and build a workforce environment conducive to high performance. The category also examines how the organization engages, manages, and develops the workforce to utilize its full potential in alignment with the overall mission, strategy, and action plans ; Operations focus -
The operations focus category examines how the organization designs, manages, and improves its systems work and work processes to deliver customer value and achieve organizational success and sustainability. Also examined is the readiness for emergencies. ;Results- The results category examines the organization's performance and improvement in all key areas product and process outcomes, customer-focused outcomes, workforce-focused outcomes, leadership and governance outcomes, and financial and market outcomes. Performance levels are examined relative to those of competitors and other organizations with similar product offerings.
Cite this Page
Methodology Of Six Sigma. (2018, Jun 06). Retrieved from https://phdessay.com/methodology-of-six-sigma/
Run a free check or have your essay done for you
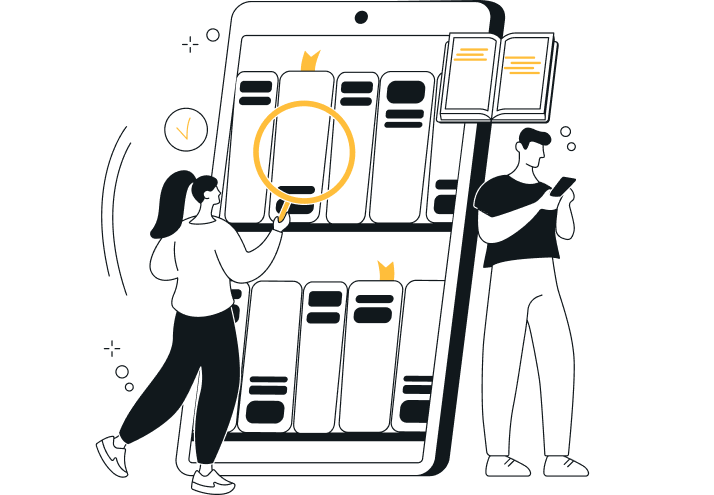