Inventory Management And Simplified Costing Methods Objective
Cost Accounting, 14e (Horngren/Datar/Rajan) Chapter 20 Inventory Management, Just-in-Time, and Simplified Costing Methods Objective 20. 1 1) Which of the following industries would have the highest cost of goods sold percentage relative to sales? A) computer manufacturers B) retail organizations C) drug manufacturers D) The percentage will usually depend on the success of a particular company. Answer: B Diff: 2 Terms: inventory management Objective: 1 AACSB: Reflective thinking 2) The costs of goods acquired from suppliers including incoming freight or transportation costs are: A) purchasing costs
B) ordering costs C) stockout costs D) carrying costs Answer: A Diff: 2 Terms: purchasing costs Objective: 1 AACSB: Reflective thinking 3) The costs of preparing, issuing, and paying purchase orders, plus receiving and inspecting the items included in orders is: A) purchasing costs B) ordering costs C) stockout costs D) carrying costs Answer: B Diff: 2 Terms: ordering costs Objective: 1 AACSB: Reflective thinking 4) The costs that result from theft of inventory are: A) shrinkage costs B) external failure costs C) stockout costs D) costs of quality Answer: A Diff: 2 Terms: shrinkage
Objective: 1 AACSB: Reflective thinking 5) The costs that result when a company runs out of a particular item for which there is a customer demand are: A) shrinkage costs B) shortage costs C) stockout costs D) EOQ estimation costs Answer: C Diff: 2 Terms: stockout costs Objective: 1 AACSB: Reflective thinking 6) The costs that result when features and characteristics of a product or service are NOT in conformance with the specifications are: A) inspection costs B) costs of quality C) purchasing costs D) design costs Answer: B Diff: 2 Terms: stockout costs Objective: 1 AACSB: Reflective thinking ) The costs that result when a company holds an inventory of goods for sale: A) purchasing costs B) carrying costs C) opportunity costs D) interest costs Answer: B Diff: 2 Terms: stockout costs Objective: 1 AACSB: Reflective thinking 8) Quality costs include: A) purchasing costs B) ordering costs C) stockout costs D) prevention costs Answer: D Diff: 2 Terms: quality costs Objective: 1 AACSB: Reflective thinking Answer the following questions using the information below: The following information applies to Labs Plus, which supplies microscopes to laboratories throughout the country.
Order custom essay Inventory Management And Simplified Costing Methods Objective with free plagiarism report
Labs Plus purchases the microscopes from a manufacturer which has a reputation for very high quality in its manufacturing operation. Annual demand (weekly demand=1/52 of annual demand)20,800 units Orders per year20 Lead time in days15 days Cost of placing an order$100 9) What is the reorder point? A) 1,040 units B) 857 units C) 1,560 units D) 2,080 units Answer: B Explanation: B) 20,800/52 = 400/7 = 57. 14 daily demand ? 15 = 857. 1 Diff: 2 Terms: reorder point Objective: 1 AACSB: Analytical skills 10) Retailers generally have a high percentage of net income to revenues. Answer: FALSE
Explanation: Retailers have a low percentage of net income to revenues. Diff: 2 Terms: inventory management Objective: 1 AACSB: Analytical skills 11) Inventory management is the planning, organizing, and controlling activities that focus on the flow of materials into, through, and from the organization. Answer: TRUE Diff: 2 Terms: inventory management Objective: 1 AACSB: Analytical skills 12) Purchasing costs arise in preparing and issuing purchase orders, receiving and inspecting the items included in the orders, and matching invoices received, purchase orders, and delivery records to make payments.
Answer: FALSE Explanation: Ordering costs arise in preparing and issuing purchase orders, receiving and inspecting the items included in the orders, and matching invoices received, purchase orders, and delivery records to make payments. Diff: 2 Terms: purchasing costs Objective: 1 AACSB: Analytical skills 13) The opportunity cost of the stockout includes lost contribution margin on the sale NOT made plus any contribution margin lost on future sales due to customer ill will. Answer: TRUE Diff: 2 Terms: stockout costs
Objective: 1 AACSB: Analytical skills 14) Carrying costs arise when an organization experiences an ability to deliver its goods to its customers. Answer: FALSE Explanation: Carrying costs arise when an organization holds its goods for sale. Diff: 2 Terms: carrying costs Objective: 1 AACSB: Analytical skills 15) Shrinkage is measured by adding (a) the cost of the inventory recorded on the books in the absence of theft and other incidents just mentioned, and (b) the cost of inventory when physically counted. Answer: FALSE
Explanation: Shrinkage is measured by the difference between (a) the cost of the inventory recorded on the books in the absence of theft and other incidents just mentioned, and (b) the cost of inventory when physically counted. Diff: 2 Terms: shrinkage Objective: 1 AACSB: Analytical skills 16) Shrinkage costs result from theft by outsiders, embezzlement by employees, misclassifications, and clerical errors. Answer: TRUE Diff: 2 Terms: shrinkage Objective: 1 AACSB: Analytical skills 17) All inventory costs are available in financial accounting systems. Answer: FALSE
Explanation: Opportunity costs are rarely recorded in formal accounting systems and they are often a very significant cost component. Diff: 2 Terms: shrinkage Objective: 1 AACSB: Analytical skills 18) Sharing inventory data throughout the supply chain leads to more "rush" orders occurring. Answer: FALSE Explanation: Sharing inventory data throughout the supply chain leads to fewer "rush" orders occurring. Diff: 2 Terms: inventory management Objective: 1 AACSB: Analytical skills 19) Managing inventories to increase net income requires companies to effectively manage costs associated with goods for sale.
Required: Classify the below listed items as either Purchasing Costs, Ordering Costs, Carrying Costs, Stockout Costs, Costs of Quality, or Shrinkage Costs. ________________a. costs of obtaining purchase approvals ________________b. costs resulting from embezzlement by employees ________________c. internal failure costs ________________d. opportunity cost of the investment tied up in inventory ________________e. spoilage of stored items ________________f. costs of lost sales as a result of not having an item requested by a customer ________________g. costs of incoming freight ________________h. osts of matching invoices received to the items and the purchase orders ________________i. costs of wages for work-in-process inspections ________________j. costs that result from clerical errors Answer: a. Ordering Costs b. Shrinkage Costs c. Costs of Quality d. Carrying Costs e. Carrying Costs f. Stockout Costs g. Purchasing Costs h. Ordering Costs i. Costs of Quality j. Shrinkage Costs Diff: 2 Terms: costs associated with goods for sale Objective: 1 AACSB: Analytical skills Objective 20. 2 1) Obsolescence is an example of which cost category? A) carrying costs B) labor costs C) ordering costs
D) quality costs Answer: A Diff: 2 Terms: carrying costs Objective: 2 AACSB: Reflective thinking 2) The costs associated with storage are an example of which cost category? A) quality costs B) labor costs C) ordering costs D) carrying costs Answer: D Diff: 2 Terms: carrying costs Objective: 2 AACSB: Reflective thinking 3) Which of the following is an assumption of the economic-order-quantity decision model? A) The quantity ordered can vary at each reorder point. B) Demand ordering costs and carrying costs fluctuate. C) There will be timely labor costs. D) No stockouts occur. Answer: D Diff: 2
Terms: economic order quantity (EOQ) Objective: 2 AACSB: Reflective thinking 4) The economic order quantity ignores: A) purchasing costs B) relevant ordering costs C) stockout costs D) Both A and C are correct. Answer: D Diff: 3 Terms: economic order quantity (EOQ) Objective: 2 AACSB: Reflective thinking 5) The purchase-order lead time is the: A) difference between the times an order is placed and delivered B) difference between the products ordered and the products received C) discrepancies in purchase orders D) time required to correct errors in the products received Answer: A Diff: 2
Terms: purchase-order lead time Objective: 2 AACSB: Reflective thinking 6) Which of the following statements about the economic-order-quantity decision model is FALSE? A) It assumes purchasing costs are relevant when the cost per unit changes due to the quantity ordered. B) It assumes quality costs are irrelevant if quality is unaffected by the number of units purchased. C) It assumes stockout costs are irrelevant if no stockouts occur. D) It assumes ordering costs and carrying costs are relevant. Answer: A Diff: 3 Terms: economic order quantity (EOQ) Objective: 2 AACSB: Reflective thinking ) Relevant total costs in the economic-order-quantity decision model equal relevant ordering costs plus relevant: A) carrying costs B) stockout costs C) quality costs D) purchasing costs Answer: A Diff: 2 Terms: economic order quantity (EOQ), ordering costs, carrying costs Objective: 2 AACSB: Reflective thinking Answer the following questions using the information below: The Wood Furniture company produces a specialty wood furniture product, and has the following information available concerning its inventory items: Relevant ordering costs per purchase order$300 Relevant carrying costs per year:
Required annual return on investment10% Required other costs per year$2. 80 Annual demand is 20,000 packages per year. The purchase price per package is $32. 8) What is the economic order quantity? A) 2,000,000 units B) 1,414. 21 units C) 150,000 units D) 3,464. 00 units Answer: B Explanation: B) Unit carrying costs = ($32 ? 0. 10) + $2. 80 = $6 EOQ = The square root of [(2 ? 20,000 ? $300) / $6] = 1,414. 21 units Diff: 3 Terms: economic order quantity (EOQ) Objective: 2 AACSB: Analytical skills 9) What are the relevant total costs at the economic order quantity? A) $1,414. 21 B) $4,242. 5 C) $8,485. 28 D) $9,000. 00 Answer: C Explanation: C) Unit carrying costs = ($32 ? 0. 10) + $2. 80 = $6 EOQ = The square root of [(2 ? 20,000 ? $300) / $6] = 1,414. 21 units RTC = [pic]= $8,485. 28 Diff: 3 Terms: economic order quantity (EOQ), ordering costs, carrying costs Objective: 2 AACSB: Analytical skills 10) What are the total relevant costs, assuming the quantity ordered equals 1,000 units? A) $3,000 B) $500 C) $6,000 D) $9,000 Answer: D Explanation: D) RTC = [pic] = $9,000 Diff: 3 Terms: economic order quantity (EOQ), ordering costs, carrying costs Objective: 2
AACSB: Analytical skills 11) How many deliveries will be required at the economic order quantity? A) 1. 00 delivery B) 5. 10 deliveries C) 7. 07 deliveries D) 14. 14 deliveries Answer: D Explanation: D) 20,000 / 1,414. 21 = 14. 14 deliveries Diff: 3 Terms: economic order quantity (EOQ) Objective: 2 AACSB: Analytical skills 12) The annual relevant total costs are at a minimum when relevant: A) ordering costs are greater than the relevant carrying costs B) carrying costs are greater than the relevant ordering costs C) carrying costs are equal to relevant ordering costs
D) None of these answers is correct. Answer: C Diff: 3 Terms: economic order quantity (EOQ), ordering costs, carrying costs Objective: 2 AACSB: Reflective thinking Answer the following questions using the information below: The following information applies to Labs Plus, which supplies microscopes to laboratories throughout the country. Labs Plus purchases the microscopes from a manufacturer which has a reputation for very high quality in its manufacturing operation. Annual demand (weekly demand=1/52 of annual demand)20,800 units Orders per year20 Lead time in days15 days
Cost of placing an order$100 13) What are the annual relevant carrying costs, assuming each order was made at the economic-order-quantity amount? A) $200 B) $1,000 C) $2,000 D) $6,000 Answer: C Explanation: C) Annual carrying costs = annual ordering costs = $100 ? 20 = $2,000 Diff: 2 Terms: economic order quantity (EOQ), carrying costs Objective: 2 AACSB: Analytical skills 14) What is the economic order quantity assuming each order was made at the economic-order-quantity amount? A) 15 units B) 20 units C) 780 units D) 1,040 units Answer: D Diff: 2 Terms: economic order quantity (EOQ)
Objective: 2 AACSB: Analytical skills 15) If Brian Company has a safety stock of 320 units and the average daily demand is 20 units, how many days can be covered if the shipment from the supplier is delayed by 12 days? A) 24. 0 days B) 20. 0 days C) 16. 0 days D) 13. 4 days Answer: C Explanation: C) 320/20 = 16 days Diff: 3 Terms: safety stock, purchase-order lead time Objective: 2 AACSB: Analytical skills 16) If Jackson Collectibles, Inc. has a safety stock of 70 units and the average weekly demand is 14 units, how many days can be covered if the shipment from the supplier is delayed ?
A) 5 days B) 35. days C) 42 days D) 70 days Answer: B Explanation: B) 70/2 = 35. 0 days Diff: 3 Terms: safety stock, purchase-order lead time Objective: 2 AACSB: Analytical skills 17) The optimal safety stock level is the quantity of safety stock that minimizes the sum of the annual relevant: A) stockout costs and carrying costs B) ordering costs and carrying costs C) ordering costs and stockout costs D) ordering costs and purchasing costs Answer: A Diff: 2 Terms: economic order quantity (EOQ), safety stock, stockout costs, carrying costs Objective: 2 AACSB: Reflective thinking 8) The simplest version of the Economic Order Quantity model incorporates only ordering costs, carrying costs, and purchasing costs into the calculation. Answer: FALSE Explanation: Purchasing costs are ignored in the Economic Order Quantity. Diff: 2 Terms: economic order quantity (EOQ) Objective: 2 AACSB: Analytical skills 19) To determine the Economic Order Quantity, the relevant ordering costs are maximized and the relevant carrying costs are minimized. Answer: FALSE Explanation: We minimize both the relevant ordering costs and the relevant carrying costs. Diff: 2
Terms: economic order quantity (EOQ) Objective: 2 AACSB: Analytical skills 20) The Economic Order Quantity increases with demand and carrying costs and decreases with ordering costs. Answer: FALSE Explanation: The Economic Order Quantity increases with demand and ordering costs and decreases with carrying costs. Diff: 2 Terms: economic order quantity (EOQ) Objective: 2 AACSB: Analytical skills 21) The EOQ model is solved using calculus but the key intuition is that relevant total costs are minimized when relevant ordering costs equal relevant carrying costs.
Answer: TRUE Diff: 2 Terms: economic order quantity (EOQ) Objective: 2 AACSB: Analytical skills 22) Safety stock is used as a buffer against unexpected increases in demand, uncertainty about lead time, and unavailability of stock from suppliers. Answer: TRUE Diff: 1 Terms: safety stock Objective: 2 AACSB: Ethical reasoning 23) Due to unprecedented growth during the year, Flowers by Kelly decided to use some of its surplus cash to increase the size of several inventory order quantities that had been previously determined using an EOQ model. Required:
Identify whether increasing the size of inventory orders will increase, decrease, or have no effect on each of the following items. ________________a. Average inventory ________________b. Cost of goods sold ________________c. Number of orders per year ________________d. Total annual carrying costs ________________e. Total annual carrying and ordering costs ________________f. Total annual ordering costs Answer: a. Increase b. No effect c. Decrease d. Increase e. Depends which costs increase/decrease more f. Decrease Diff: 2 Terms: economic order quantity (EOQ) Objective: 2 AACSB: Analytical skills 4) The only product of a company has an annual demand of 4,000 units. The cost of placing an order is $20 and the cost of carrying one unit in inventory for one year is $4. Required: Determine the economic order quantity. Answer: The square root of [(2 ? 4,000 ? $20) / $4 = 200 units Diff: 1 Terms: economic order quantity (EOQ), ordering costs, carrying costs Objective: 2 AACSB: Analytical skills 25) Ralph was in the process of completing the quarterly planning for the purchasing department when a major computer malfunction lost most of his data. For direct material XXX he was able to recover the following: Average inventory level of XXX |200 | |Orders per year |40 | |Average daily demand |48 | |Working days per year |250 | |Annual ordering costs |$4,000 | |Annual carrying costs |$6,000 | Ralph purchases at the EOQ quantity level. Required: Determine the annual demand, the cost of placing an order, the annual carrying cost of one unit, and the economic order quantity.
Answer: Annual demand= 48 ? 250 = 12,000 Cost of placing an order= $4,000/40 = $100 per order Carrying cost of one unit= $6,000/200 = $30 per unit EOQ= The square root of (2 ? 12,000 ? $100)/30 = 283 units Diff: 3 Terms: economic order quantity (EOQ), ordering costs, carrying costs Objective: 2 AACSB: Analytical skills 26) Clothes, Inc. , has an average annual demand for red, medium polo shirts of 25,000 units. The cost of placing an order is $80 and the cost of carrying one unit in inventory for one year is $25. Required: a. Use the economic-order-quantity model to determine the optimal order size. . Determine the reorder point assuming a lead time of 10 days and a work year of 250 days. c. Determine the safety stock required to prevent stockouts assuming the maximum lead time is 20 days and the maximum daily demand is 125 units. Answer: a. The square root of [(2 ? 25,000 ? $80) / $25] = 400 units b. Daily demand = 25,000/250 = 100 units Reorder point = 100 units per day ? 10 days = 1,000 units c. |Maximum demand per day |125 units | |Maximum lead time |? 0 days | |Maximum lead time demand |2,500 units | |Reorder point without safety stocks |1,000 units | |Safety stock |1,500 units | Diff: 2 Terms: economic order quantity (EOQ), reorder point, safety stock Objective: 2 AACSB: Analytical skills 27) An inventory item of XYZ Manufacturing has an average daily demand of 10 units with a maximum daily demand of 12 units. The economic order quantity is 200 units. Without safety stocks, the reorder point is 50 units. Safety stocks are set at 94 units. Required: a.
Determine the reorder point with safety stocks. b. Determine the maximum inventory level. c. Determine the average lead time. d. Determine the maximum lead time. Answer: a. |Reorder point without safety stocks |50 units | |Safety stock |94 units | | Reorder point with safety stocks |144 units | b. |Economic-order quantity |200 units | |Safety stocks |94 units | |Maximum inventory level |294 units | . Average lead time = 50 units at reorder point/10 units a day = 5 days d. Reorder point with safety stocks is 144 Maximum demand is 12 Maximum lead time = 144/12 = 12 days Diff: 2 Terms: economic order quantity (EOQ), reorder point, safety stock Objective: 2 AACSB: Analytical skills 28) For supply item ABC, Andrews Company has been ordering 125 units based on the recommendation of the salesperson who calls on the company monthly. A new purchasing agent has been hired by the company who wants to start using the economic-order-quantity method and its supporting decision elements. She has gathered the following information: Annual demand in units |250 | |Days used per year |250 | |Lead time, in days |10 | |Ordering costs |$100 | |Annual unit carrying costs |$20 | Required: Determine the EOQ, average inventory, orders per year, average daily demand, reorder point, annual ordering costs, and annual carrying costs. Answer: EOQ= The square root of [(2 ? 250 ? $100) / $20] = 50 Average inventory= 50/2 = 25 Orders per year= 250/50 = 5
Average daily demand= 250/250 = 1 unit Reorder point= 10/1 = 10 units Annual ordering costs= 5 ? $100 = $500 Annual carrying costs= 25 ? $20 = $500 Diff: 2 Terms: economic order quantity (EOQ), reorder point, ordering costs, carrying costs Objective: 2 AACSB: Analytical skills 29) Discuss considerations that should be fully taken into account when developing inventory related relevant costs for use in an economic order quantity (EOQ) model. Answer: It is crucial that the costs be incremental. Consider incremental carrying costs. If they are costs that will change with the quantity of inventory held, then they are relevant.
If there are costs that would be unchanged regardless of how much inventory was in the warehouse (such as a clerical salary or material handler who was working at below full capacity), then those costs are not relevant for decision-making purposes. Relevant carrying costs are likely to be costs like shrinkage, breakage, obsolescence, and costs of hiring extra employees (or having existing employees work overtime) if higher levels of inventory will make those costs increase. Consider incremental opportunity cost of capital. If there is a decision to carry more inventory, then there will be money spent to purchase the inventory.
The opportunity cost of capital is what would the other most beneficial use of the money be if it wasn't needed to purchase the higher level of inventory. It is calculated by multiplying the company's required rate of return by the per unit costs and then by the number of units purchased for the inventory and incurred at the time the units are received. Stockout costs require an estimate of the lost contribution margin on sales lost because of a stockout. Ordering costs are only those that change with the numbers of orders placed. Diff: 2 Terms: economic order quantity (EOQ), ordering costs, carrying costs Objective: 2
AACSB: Reflective thinking Objective 20. 3 1) Video Images is a distributor of DVDs. Quick-Disk Mart is a local retail outlet which sells blank and recorded DVDs. Quick-Disk Mart purchases tapes from Video Images at $3. 00 per DVD. DVDs are shipped in packages of 20. Video Images pays all incoming freight, and Quick-Disk Mart does not inspect the DVDs due to Video Images reputation for high quality. Annual demand is 104,000 DVDs at a rate of 4,000 DVDs per week. Quick-Disk Mart earns 20% on its cash investments. The purchase-order lead time is two weeks. The following cost data are available: Relevant ordering costs per purchase order$90. 0 Carrying costs per package per year: Relevant insurance, materials handling, breakage, etc. , per year$ 4. 50 What is the required annual return on investment per package? A) $60. 00 B) $2. 50 C) $12. 00 D) $0. 60 Answer: C Explanation: C) 20 DVDs ? $3. 00 =$60. 00 $60. 00 ? 0. 2 = $12. 00 Diff: 3 Terms: ordering costs, carrying costs Objective: 3 AACSB: Analytical skills Answer the following questions using the information below: Digital Goods is a distributor of DVDs. DVD Mart is a local retail outlet which sells blank and recorded DVDs. DVD Mart purchases tapes from Digital Goods at $10. 0 per DVD; DVDs are shipped in packages of 25. Digital Goods pays all incoming freight, and DVD Mart does not inspect the DVDs due to Digital Goods' reputation for high quality. Annual demand is 208,000 DVDs at a rate of 4,000 DVDs per week. DVD Mart earns 15% on its cash investments. The purchase-order lead time is one week. The following cost data are available: Relevant ordering costs per purchase order$94. 50 Carrying costs per package per year: Relevant insurance, materials handling, breakage, etc. , per year$ 3. 50 2) What is the economic order quantity? A) 384 packages B) 475 packages C) 146 packages D) 196 packages Answer: D
Explanation: D) EOQ = The square root of [(2 ? (208,000/25) ? $94. 50) / ($37. 50+ $3. 50)] EOQ = 196 packages Diff: 2 Terms: economic order quantity (EOQ) Objective: 3 AACSB: Analytical skills 3) What are the relevant total costs? A) $5,697 B) $2,829 C) $8,029 D) $2,868 Answer: C Diff: 3 Terms: economic order quantity (EOQ), ordering costs, carrying costs Objective: 3 AACSB: Analytical skills 4) How many deliveries will be made during each time period? A) 86. 7 deliveries B) 72. 0 deliveries C) 138. 0 deliveries D) 42. 1 deliveries Answer: A Explanation: A) EOQ = The square root of [(2 ? (208,000/25) ? $94. 50) / ($37. 0+ $3. 50)] EOQ = 196 packages [(208,000 / 25) / 196 = 86. 7 deliveries Diff: 3 Terms: economic order quantity (EOQ) Objective: 3 AACSB: Analytical skills Answer the following questions using the information below: Short Grass Incorporated is a distributor of golf balls. Martin's Golf Supplies is a local retail outlet which sells golf balls. Martin's purchases the golf balls from Short Grass Incorporated at $0. 75 per ball; the golf balls are shipped in cartons of 72. Short Grass Incorporated pays all incoming freight, and Martin's Golf Supplies does not inspect the balls due to Short Grass' reputation for high quality.
Annual demand is 155,520 golf balls at a rate of 2,991 balls per week. Martin's Golf Supplies earns 12% on its cash investments. The purchase-order lead time is one week. The following cost data are available: Relevant ordering costs per purchase order$125. 00 Carrying costs per carton per year: Relevant insurance, materials handling, breakage, etc. , per year$ 0. 77 5) If Martin's makes an order (1/12 of annual demand) once per month, what are the relevant total costs? A) $1,500 B) $652. 50 C) $2,152. 50 D) $3,000. 00 Answer: C Explanation: C) Order Quantity = Annual Demand / 12 =12,960 balls/month = 180 cartons per month
RTC = Ordering Costs + Carrying Costs Carrying Cost per carton = price ? invest rate + insurance/handling Carrying Cost per carton = ($. 75 ? 72 ? 12%) + $0. 77 = $7. 25 RTC = (12 ? $125. 00) + ((180/2) ? $7. 25) =$2,152. 50 Diff: 3 Terms: economic order quantity (EOQ), ordering costs, carrying costs Objective: 3 AACSB: Analytical skills 6) What is the economic order quantity? A) 180 cartons B) 273 cartons C) 270 cartons D) 360 cartons Answer: B Explanation: B) Annual Demand / 155,520 / 72 =2,160 cartons Carrying Cost per carton = ($. 75 ? 72 ? 12%) + $0. 77 = $7. 25 EOQ = The square root of [(2 ? (155,520/72) ? $125. 0) / ($7. 25)] EOQ = 272. 9 cartons - round to 273 Diff: 2 Terms: economic order quantity (EOQ) Objective: 3 AACSB: Analytical skills 7) Purchasing at the EOQ recommended level, how many deliveries will be made during each time period? A) 2 deliveries B) 6. 0 deliveries C) 7. 91 deliveries D) 12 deliveries Answer: C Explanation: C) Annual Demand / 155,520 / 72 =2,160 cartons Carrying Cost per carton = ($. 75 ? 72 ? 12%) + $0. 77 = $7. 25 EOQ = The square root of [(2 ? (155,520/72) ? $125. 00) / ($7. 25)] EOQ = 272. 9 cartons - round to 273 Deliveries = Annual Demand / EOQ = 7. 91 Diff: 3 Terms: economic order quantity (EOQ)
Objective: 3 AACSB: Analytical skills 8) Purchasing at the EOQ recommended level, what are the relevant total costs? A) $1,500. 00 B) $1,978. 60 C) $989. 37 D) $3,000. 00 Answer: B Explanation: B) Annual Demand / 155,520 / 72 =2,160 cartons Carrying Cost per carton = ($. 75 ? 72 ? 12%) + $0. 77 = $7. 25 EOQ = The square root of [(2 ? (155,520/72) ? $125. 00) / ($7. 25)] EOQ = 272. 9 cartons - round to 273 989. 37+989. 26 RTC = [pic] + [pic]= $1,978. 60 (Your solution might be slightly different based on rounding. ) Diff: 3 Terms: economic order quantity (EOQ), ordering costs, carrying costs Objective: 3
AACSB: Analytical skills 9) The reorder point is simplest to compute when: A) both demand and purchase-order lead times are known with certainty B) the number of units sold varies C) the safety stock amount never varies D) the relevant ordering costs and the relevant carrying costs are equal Answer: A Diff: 2 Terms: economic order quantity (EOQ), reorder point Objective: 3 AACSB: Reflective thinking 10) What are the major relevant costs in maintaining safety stock? A) carrying costs and purchasing costs B) ordering costs and purchasing costs C) ordering costs and stockout costs D) stockout costs and carrying costs
Answer: D Diff: 2 Terms: safety stock Objective: 3 AACSB: Reflective thinking 11) The annual relevant carrying costs of inventory consists of the sum of the: A) ordering costs and carrying costs B) stockout costs and carrying costs C) incremental costs plus the opportunity costs of capital D) incremental costs plus the carrying costs Answer: C Diff: 2 Terms: carrying costs Objective: 3 AACSB: Reflective thinking 12) Party Animals sells stuffed tigers. Products, Inc. , manufactures many different stuffed animals. Party Animals orders 10,400 tigers per year, 200 per week, at $10 per tiger.
The manufacturer covers all shipping costs. Party Animals earns 12% on its cash investments. The purchase-order lead time is 3 weeks. Party Animals sells 210 tigers per week. The following data are available (based on management's estimates): Estimated ordering costs per purchase order$10 Estimated insurance, materials handling, breakage, and so on, per year$3 Actual ordering costs per order$15 What is the economic order quantity using the estimated amounts? A) 119 stuffed tigers B) 223 stuffed tigers C) 273 stuffed tigers D) 325 stuffed tigers Answer: B Explanation: B) EOQ = The square root of [(2 ? 10,400 ? 10) / ($3 + (0. 12 ? $10))] EOQ = 223 units Diff: 3 Terms: economic order quantity (EOQ) Objective: 3 AACSB: Analytical skills 13) A conflict between the EOQ model's optimal order quantity and the order quantity the purchasing manager, evaluated on conventional accounting numbers, regards as optimal is considered a(n): A) problem for the chief financial officer to resolve B) problem for the performance evaluation system to resolve C) goal congruence D) opportunity cost Answer: B Diff: 2 Terms: economic order quantity (EOQ) Objective: 3 AACSB: Analytical skills 14) Just-in-time purchasing requires:
A) larger and less frequent purchase orders B) smaller and less frequent purchase orders C) smaller and more frequent purchase orders D) larger and more frequent purchase orders Answer: C Diff: 2 Terms: just-in-time (JIT) purchasing Objective: 3 AACSB: Analytical skills 15) Increases in the carrying cost and decreases in the ordering cost per purchase order result in: A) smaller EOQ amounts B) larger EOQ amounts C) larger relevant total costs D) smaller relevant total costs Answer: A Diff: 2 Terms: economic order quantity (EOQ), ordering costs, carrying costs Objective: 3 AACSB: Analytical skills 6) The annual relevant carrying costs of inventory consist of incremental costs plus the opportunity cost of capital. Answer: TRUE Diff: 3 Terms: carrying costs Objective: 3 AACSB: Analytical skills 17) Relevant opportunity cost of capital is the return forgone by investing capital in inventory rather than elsewhere. Answer: TRUE Diff: 2 Terms: relevant opportunity cost of capital Objective: 3 AACSB: Analytical skills 18) Video Boy has one particular product that has an annual demand of 2,000 units. Total manufacturing costs per unit total $20. Ordering costs for the product total $25 per purchase order.
Currently, the carrying costs per unit are 25% of manufacturing costs. Required: Determine the economic manufacturing order quantity. Answer: The square root of [(2 ? 2,000 ? $25) / $5] = 141. 42 units Diff: 2 Terms: economic order quantity (EOQ), ordering costs, carrying costs Objective: 3 AACSB: Analytical skills 19) The IBP Grocery orders most of its items in lot sizes of 10 units. Average annual demand per side of beef is 720 units per year. Ordering costs are $25 per order with an average purchasing price of $100. Annual inventory carrying costs are estimated to be 40% of the unit cost.
Required: a. Determine the economic order quantity. b. Determine the annual cost savings if the shop changes from an order size of 10 units to the economic order quantity. c. Since the shelf life is limited, the IBP Grocery must keep the inventory moving. Assuming a 360-day year, determine the optimal lot size under each of the following: (1) a 20-day shelf life and (2) a 10-day shelf life. Answer: a. The square root of [(2 ? 720 ? $25) / $40] = 30 units b. |Current 10-unit order: | | | | Ordering costs ($25 ? 20/10) |$1,800 | | | Carrying costs ($100 ? 0. 40 ? 10/2) |200 |$2,000 | |EOQ 30-unit order: | | | | Ordering costs ($25 ? 720/30) |600 | | | Carrying costs ($100 ? 0. 40 ? 30/2) |600 |1,200 | |Annual savings | |$ 800 | c. Average daily demand = 720 / 360 = 2 per day
Average days' supply in EOQ = 30/2 = 15 days (1) 20-day shelf life allows for up to 40 units (20 ? 2), EOQ is acceptable. (2) 10-day shelf life allows for up to 20 units (10 ? 2), EOQ is not acceptable Diff: 3 Terms: economic order quantity (EOQ) Objective: 3 AACSB: Analytical skills 20) The executive vice president of Robotics, Inc. , is concerned because the cost of materials has not been in line with the budget for several periods, even after implementing an EOQ model. The company has the normal direct material variance computations of price and efficiency at the end of each month.
The price variance of the direct materials used is usually near expectations. The vice president does not understand how the budget differences are always larger than the material price variances. Required: What explanation can you give for the evaluation problems presented? Answer: An EOQ model does not solve all inventory related problems. The first problem is the timing of material price variance computations. They should be at the time of purchase, not at the time of usage. By changing when the variance is computed, the responsibility is placed where it should be, in purchasing, not in production.
Also, the timing of when materials are used could explain the difference between the budget variances and the material price variances. Materials may be purchased in one period and not used until another period. Also, material usage may include items purchased during several previous periods. Diff: 2 Terms: inventory management, economic order quantity (EOQ) Objective: 3 AACSB: Reflective thinking Objective 20. 4 1) Flashdrive Company sells 200 flash drives per week. Purchase-order lead time is 1-1/2 weeks and the economic-order quantity is 450 units. What is the reorder point? A) 200 units B) 300 units C) 750 units
D) 1,125 units Answer: B Explanation: B) 200 ? 1. 5= 300 units Diff: 2 Terms: economic order quantity (EOQ), reorder point Objective: 4 AACSB: Analytical skills 2) Wilson's Deli can predict with virtual certainty the demand for its products. Wilson's sells 30 hams per week. Purchase-order lead time is 3 weeks and the economic-order quantity is 75 hams. What is the reorder point? A) 30 hams B) 75 hams C) 90 hams D) 100 hams Answer: C Explanation: C) 30 ? 3= 90 hams Diff: 2 Terms: economic order quantity (EOQ), reorder point Objective: 4 AACSB: Analytical skills Answer the following questions using the information below:
Owen-King Company sells optical equipment. Lens Company manufactures special glass lenses. Owen-King Company orders 5,200 lenses per year, 100 per week, at $20 per lens. Lens Company covers all shipping costs. Owen-King Company earns 30% on its cash investments. The purchase-order lead time is 2. 5 weeks. Owen-King Company sells 125 lenses per week. The following data are available: Relevant ordering costs per purchase order$21. 25 Relevant insurance, materials handling, breakage, and so on, per year$ 2. 50 3) What is the economic order quantity for Owen-King Company? A) 325 lenses B) 297 lenses C) 210 lenses
D) 161 lenses Answer: D Explanation: D) EOQ = The square root of [(2 ? 5,200 ? $21. 25) / (($20 ? 30%) + $2. 50)] EOQ = 161 lenses Diff: 2 Terms: economic order quantity (EOQ) Objective: 4 AACSB: Analytical skills 4) What is the reorder point? A) 220. 5 lenses B) 312. 5 lenses C) 397. 5 lenses D) 415. 5 lenses Answer: B Explanation: B) 125 lenses ? 2. 5 weeks = 312. 5 lenses Diff: 2 Terms: reorder point Objective: 4 AACSB: Analytical skills 5) The ________ describes the flow of goods, services, and information from the initial sources of materials and services to the delivery of products to consumers.
A) customer list B) enterprise requirements plan (ERP) C) material requirements plan (MRP) D) supply chain Answer: D Diff: 2 Terms: supply chain Objective: 4 AACSB: Reflective thinking 6) When using a vendor-managed inventory system to enhance the features of supply chain management, a challenging issue is: A) problems of communication and trust B) the sharing of accurate, timely, and relevant information about sales forecasts C) potentially incompatible information systems D) all of the above Answer: D Diff: 2 Terms: supply chain Objective: 4 AACSB: Reflective thinking ) Just-in-time purchasing is guided solely by the economic order quantity. Answer: FALSE Explanation: Inventory management also includes purchasing costs, stockout costs, and quality costs. Diff: 2 Terms: just-in-time (JIT) purchasing, economic order quantity (EOQ) Objective: 4 AACSB: Analytical skills 8) Companies that implement JIT purchasing will switch their suppliers when another supplier offers a lower price. Answer: FALSE Explanation: Companies that implement JIT purchasing choose their suppliers carefully and develop long-term supplier relationships. Diff: 3 Terms: just-in-time (JIT) purchasing
Objective: 4 AACSB: Reflective thinking 9) Just-in-time purchasing describes the flow of goods, services, and information from the initial sources of materials and services to the delivery of products to consumers, regardless of whether those activities occur in the same organization or in other organizations. Answer: FALSE Explanation: Supply chain describes the flow of goods, services, and information from the initial sources of materials and services to the delivery of products to consumers, regardless of whether those activities occur in the same organization or in other organizations. Diff: 3
Terms: supply chain Objective: 4 AACSB: Reflective thinking 10) The manufacturing manager of New Technology Company is concerned about the company's newest plant. When the plant began operations three years ago, it had the best of everything. It had modern equipment, well-trained employees, engineered work and assembly stations, and a controlled environment. During the first two years, the evaluation results were very good with almost all cost variances being favorable. However, recently, things have turned negative. In recent months, everything seems to be operating in a crisis management mode.
Although most cost variances remain favorable, the plant's segment contribution is declining and customers are complaining about poor quality and slow delivery. Several customers have suggested that they may take their business elsewhere if things do not improve. The shop floor is in continual turmoil. In-process inventory is everywhere, production employees have difficulty finding jobs that need to be worked on, and scheduling has requested a larger computer to keep track of work in process. The vice president of sales does not know where to begin with solving the customers' problems.
It seems that everyone is working very hard and the plant has the best facilities and trained employees in the industry. Required: What is the nature of the plant's problems? What recommendation would you make to help improve the situation? Answer: The basic problem appears to be too much work-in-process inventory and a lack of control over the flow of this inventory. Since the plant had two good years of production, it may be that increased demands are pushing the plant near its capacity and management has lost control of how to manage a near-capacity situation.
Although the employees are well trained and skilled in what they do, that is not enough to ensure the production process runs smoothly. All activities must be organized to be efficient. A beginning recommendation is to implement a materials required planning system where each workstation controls what it produces, and pushes it to the next workstation. This can be accomplished by tighter controls over the scheduling of production units by workstation. This would be incorporated with a master production schedule, bill of materials, and timely inventory system. Diff: 2
Terms: inventory management, material requirements planning (MRP) Objective: 4 AACSB: Communication 11) What is a supply chain, and what are the benefits of a supply chain analysis? Provide an example of these benefits. Answer: The supply chain describes the flow of goods, services, and information from the initial sources of materials and services to the delivery of products to customers, regardless of whether these activities occur in the same organization or in other organizations. Utilizing supply chain analysis allows companies to coordinate their activities and reduce inventories throughout the supply chain.
An example of the benefits of supply chain analysis might be the emergence of supplier or vendor-managed inventories such as the relationship between Procter & Gamble and Walmart. Diff: 2 Terms: inventory management Objective: 4 AACSB: Reflective thinking Objective 20. 5 1) A push-through system that manufactures finished goods for inventory on the basis of demand forecasts is referred to as: A) just-in-time purchasing B) materials requirements planning C) relevant total costs D) economic order quantity Answer: B Diff: 1 Terms: material requirements planning (MRP) Objective: 5 AACSB: Reflective thinking ) A demand-pull system in which each component in a production line is produced immediately as needed by the next step in the production line is referred to as: A) just-in-time purchasing B) materials requirements planning C) relevant total costs D) economic order quantity Answer: A Diff: 1 Terms: just-in-time (JIT) purchasing Objective: 5 AACSB: Reflective thinking 3) The management accountant aids in MRP by: A) doing journal entries as requested B) preparing plant appropriation requests C) maintaining accurate records of inventory and its costs D) contacting vendors to make sure they can deliver the materials in time Answer: C
Diff: 1 Terms: material requirements planning (MRP) Objective: 5 AACSB: Reflective thinking 4) A "push-through" system, often described as a just-in-time system, emphasizes simplicity and close coordination among work centers. Answer: FALSE Explanation: The narrative describes a Materials Requirement Planning system. Diff: 2 Terms: just-in-time (JIT) production Objective: 5 AACSB: Communication 5) Costs of setting up a production run are analogous to ordering costs in the Economic Order Quantity (EOQ) model. Answer: TRUE Diff: 2 Terms: ordering costs Objective: 5 AACSB: Analytical skills ) A "demand-pull" system, often described as a materials requirement planning system, focuses first on the forecasted amount and timing of finished goods and then determines the demand for materials components and subassemblies at each of the prior stages of production. Answer: FALSE Explanation: The narrative describes a push-through system. Diff: 2 Terms: material requirements planning (MRP) Objective: 5 AACSB: Reflective thinking 7) Just-in-time (JIT) production, is a "demand-pull" manufacturing system that manufactures each component in a production line as soon as, and only when, needed by the next step in the production line.
Answer: TRUE Diff: 2 Terms: just-in-time (JIT) production Objective: 5 AACSB: Reflective thinking 8) Just-in-time systems are similar to materials requirement planning systems in that both systems are demand-pull systems. Answer: FALSE Explanation: Just-in-time systems are not similar to materials requirement planning systems in that just-in-time production is a demand-pull system and materials requirements planning is a push-through approach. Diff: 2 Terms: just-in-time (JIT) production, materials requirements planning (MRP) Objective: 5
AACSB: Analytical skills 9) Kretzinger Company makes extensive use of financial performance reports for each of its departments. Although most departments have been reporting favorable cost variances with the company's current inventory system, management is concerned about the overall performance of the purchasing department. For example, the following information is for the purchasing of materials for a product the company has been manufacturing for several years: Purchase Year |Quantity Used |Average Inventory |Price Variance | |20X1 |40,000 |8,000 |$ 1,000 F | |20X2 |60,000 |15,000 |10,000 F | |20X3 |60,000 |20,000 |12,000 F | |20X4 |50,000 |12,500 |20,000 U | |20X5 |54,000 |18,000 |8,000 F | |20X6 |58,000 |23,200 |9,500 F |
Required: a. Compute the inventory turnover for each year. Can any conclusions be drawn for a yearly comparison of the purchase price variance and the inventory turnover? b. Identify problems likely to be caused by evaluating purchasing only on the basis of the purchase price variance. c. What recommendations will improve the evaluation process? Answer: a. |Year |Quantity used | |Average inventory |Turnover | |20X1 |40,000 |divided by |8,000 |5. | |20X2 |60,000 |divided by |15,000 |4. 0 | |20X3 |60,000 |divided by |20,000 |3. 0 | |20X4 |50,000 |divided by |12,500 |4. 0 | |20X5 |54,000 |divided by |18,000 |3. 0 | |20X6 |58,000 |divided by |23,200 |2. 5 |
Favorable purchase prices appear to be associated with decreases in inventory turnover and increases in average inventory levels. Decreases in inventory turnover are a possible signal of the buildup of excess inventory. Excess inventory will reduce return on investment of the company and the above information indicates a need for a just-in-time inventory system. b. To achieve quantity discounts and favorable materials price variances, purchasing may be ordering excess inventory, thereby increasing subsequent storage, obsolescence, and handling costs.
To obtain a low price, purchasing may be ordering from a supplier whose goods have inferior quality which may, in turn, lead to increased inspection, rework, and, perhaps, dissatisfied customers. c. It appears that two items may help improve the situation. First, consider the change to a just-in-time inventory system that would greatly improve the inventory turnover and reduce the amount of inventory carried. Second, additional measures should be used in the evaluation of the purchasing department. Either different financial measures should be used or the addition of nonfinancial measures should be implemented.
Diff: 3 Terms: inventory management, just-in-time (JIT) production Objective: 5 AACSB: Analytical skills 10) Minnesota Ore Company mines iron ore for production into various metal products. During recent years, the company has had large fluctuations in its inventories of metal ingots. Much of the volatility of the inventory levels is due to the variability of demand by the company's largest customers, automobile manufacturers. For large orders, the company has the technology to quickly shift production from one product to another. Required:
Explain how the company can improve its inventory control system and give the advantages of whatever you recommend. Answer: The company can probably benefit from changing to a just-in-time system for inventory control. This would allow the company to be responsive to actual needs rather than finished goods inventory building. The advantages would be: 1. Lower inventory requirements; 2. Reductions in carrying and handling costs of inventories; 3. Reduction in risks of obsolete inventories; 4. Reduction in total manufacturing costs; and 5. Reductions in paperwork.
Diff: 2 Terms: inventory management, just-in-time (JIT) production Objective: 5 AACSB: Reflective thinking Objective 20. 6 1) A grouping of all the different types of equipment used to make a given product is referred to as: A) total quality management B) materials requirements planning C) manufacturing cells D) economic order quantity Answer: C Diff: 1 Terms: manufacturing cells Objective: 6 AACSB: Reflective thinking 2) The time required to get equipment, tools, and materials ready to start production is referred to as: A) setup time B) manufacturing lead time
C) pass-through time D) None of these answers is correct. Answer: A Diff: 1 Terms: lean production Objective: 6 AACSB: Reflective thinking 3) The time from when an order is received by manufacturing until it becomes a finished good is referred to as: A) work-in-process time B) manufacturing lead time C) pass-through time D) None of these answers is correct. Answer: B Diff: 1 Terms: lean production Objective: 6 AACSB: Reflective thinking 4) All of the following are potential financial benefits of just-in-time EXCEPT: A) lower investments in inventories
B) lower investments in plant space for inventories C) reducing the risk of obsolescence D) reducing manufacturing lead time Answer: C Diff: 1 Terms: just-in-time (JIT) production Objective: 6 AACSB: Analytical skills 5) A system that comprises a single database that collects data and feeds it into software applications supporting all of a company's business activities is known as a(n): A) economic order quantity (EOQ) system B) enterprise requirements planning (ERP) system C) just-in-time (JIT) system D) material requirements planning (MRP) system Answer: B
Diff: 2 Terms: enterprise resource planning (ERP) system Objective: 6 AACSB: Use of Information Technology 6) One DISADVANTAGE of an enterprise resource planning (ERP) system is: A) the use of standard costing systems is not allowed B) these systems are not in accordance with Generally Accepted Accounting Principles (GAAP) C) the systems must often be customized to fit the strategic needs of the user D) the systems increase lead times when purchasing material from a supplier Answer: C Diff: 2 Terms: enterprise resource planning (ERP) system Objective: 6
AACSB: Reflective thinking 7) A financial benefit of a just-in-time system is that inventory carrying costs are reduced. Answer: TRUE Diff: 2 Terms: just-in-time (JIT) production, just-in-time (JIT) purchasing Objective: 6 AACSB: Reflective thinking 8) In a just-in-time system, suppliers are selected primarily on the basis of their ability to provide materials and products at the lowest possible price. Answer: FALSE Explanation: In a just-in-time system, suppliers are selected on the basis of their ability to deliver quality materials in a timely manner. Diff: 2
Terms: just-in-time (JIT) production, just-in-time (JIT) purchasing Objective: 6 AACSB: Reflective thinking 9) An Enterprise Resource Planning (ERP) System comprises a single database that collects data and feeds it into software applications supporting all of a company's business activities. Answer: TRUE Diff: 2 Terms: enterprise resource planning (ERP) system Objective: 6 AACSB: Use of Information Technology 10) The Jarvis Corporation produces bucket loader assemblies for the tractor industry. The product has a long term life expectancy. Jarvis has a traditional manufacturing and inventory system.
Jarvis is considering the installation of a just-in-time inventory system to improve its cost structure. In doing a full study using its manufacturing engineering team as well as consulting with industry JIT experts and the main vendors and suppliers of the components Jarvis uses to manufacture the bucket loader assemblies, the following incremental cost-benefit relevant information is available for analysis: The Jarvis cost of investment capital hurdle rate is 15%. One time cost to rearrange the shop floor to create the manufacturing cell workstations is $275,000.
One time cost to retrain the existing workforce for the JIT required skills is $60,000. Anticipated defect reduction is 40%. Currently there is a cost of quality defect assessment listed as $150,000 per year. The setup time for each of the existing functions will be reduced by 67%. Currently the forecast for setup costs are $225,000 per year. Jarvis will expect to save $200,000 per year in carrying costs as a result of having a lower inventory. The suppliers will require a 15% premium over the current level of prices in order to position themselves to supply the material on a smaller and more frequent schedule.
Currently the materials purchases are $1,500,000 per year. Required: Determine whether it is in the best interest of Jarvis Corporation to install a JIT system. Answer: 1. Initial Investment = $275,000 + 60,000 = $335,000 2. Annual Savings: Defect Cost Reduction = 40% of $150,000 = $60,000 Setup Cost Reduction = 67% of $225,000 = $150,750 Carrying Cost reduction = $200,000 Total Savings = (60,000 + 150,750 + 200,000) = $410,750 3. Annual Increased Costs: Vendor Premium = 15% of $1,500,000 = $225,000 4. Net Annual Savings = (410,750 - 225,000) = $185,750 5.
Savings/Initial Investment = (185,750 / 335,000) = 55 % Since the net savings is returning 55% per year on the initial investment (which is far in excess of the companies hurdle rate of 15%), the JIT project should be implemented. Diff: 3 Terms: just-in-time (JIT) production Objective: 6 AACSB: Analytical skills 11) What are five features of a just-in-time manufacturing system? Answer: A just-in-time (JIT) system has many positive features. It organizes production in manufacturing cell groups which allow for all equipment used for a given product to be grouped together.
This reduces material handling costs and sequences the production process. A second feature of a JIT system is that workers are trained to be multiskilled. They are trained to operate various machines as well as to do light maintenance and repairs on the machines. A third feature of JIT is that it aggressively works to eliminate defects. Because there is a tight link between the steps, defects are quickly noticed in the next step and addressed before large numbers of units become backlogged. A fourth feature of a JIT system is that it reduces setup time and manufacturing lead time.
Reduced setup costs make it more practical to produce smaller batches and react faster to changes in customer demand. A fifth feature of a JIT system is the firm only uses suppliers who are capable of meeting delivery demands in a timely fashion. This also causes an increase in the quality of the goods being received by the firm. Diff: 2 Terms: just-in-time (JIT) production Objective: 6 AACSB: Reflective thinking Objective 20. 7 1) Traditional normal and standard costing systems use: A) backflush costing B) delayed costing C) post-deduct costing D) sequential tracking Answer: D Diff: 2 Terms: backflush costing
Objective: 7 AACSB: Reflective thinking 2) A costing system that omits recording some or all of the journal entries relating to the cycle from purchase of direct materials to the sale of finished goods is called: A) dependent costing B) synchronous costing C) sequential costing D) backflush costing Answer: D Diff: 2 Terms: backflush costing Objective: 7 AACSB: Reflective thinking Answer the following questions using the information below: Games R Us manufactures various games. For March, there were no beginning inventories of direct materials and no beginning or ending work in process.
Conversion costs is the only indirect manufacturing cost category currently used. Journal entries are recorded when materials are purchased and when conversion costs are allocated under backflush costing. Conversion costs ? March$ 400,000 Direct materials purchased ? March$1,070,000 Units produced ? March58,800 Units sold ? March41,800 3) Which of the following journal entries properly records the purchase of direct materials? A) Accounts Payable Control1,070,000 Inventory: Raw and In-Process Control1,070,000 B) Inventory: Raw and In-Process Control1,070,000 Accounts Payable Control1,070,000
C) Inventory: Raw and In-Process Control1,070,000 Conversion Costs1,070,000 D) Conversion Costs1,070,000 Inventory: Raw and In-Process Control1,070,000 Answer: B Diff: 3 Terms: backflush costing, trigger point Objective: 7 AACSB: Analytical skills 4) Which of the journal entries properly records conversion costs? A) Conversion Costs400,000 Various Accounts400,000 B) Various Accounts400,000 Conversion Costs400,000 C) Conversion Costs400,000 Inventory: Direct Materials400,000 D) Inventory: Direct Materials400,000 Conversion Costs400,000 Answer: A Diff: 2 Terms: backflush costing Objective: 7 AACSB: Analytical skills ) Which of the following entries properly records the cost of goods sold for the month? A) Finished Goods1,045,000 Work in Process1,045,000 B) Cost of Goods Sold1,045,000 Finished Goods1,045,000 C) Finished Goods1,045,000 Cost of Goods Sold1,045,000 D) Cost of Goods Sold1,045,000 Work in Process1,045,000 Answer: B Diff: 3 Terms: backflush costing Objective: 7 AACSB: Analytical skills Answer the following questions using the information below: Complete Digital Products manufactures digital cameras. For October, there were no beginning inventories of direct materials and no beginning or ending work in process.
Conversion costs is the only indirect manufacturing cost category currently used. Journal entries are recorded when materials are purchased and when units are sold. Conversion costs - October$ 45,200 Direct materials purchased - October$125,200 Units produced - October40,000 units Units sold - October37,500 units Selling price$10 each 6) Which of the following journal entries properly reflects the purchase of materials in a JIT environment? A) Inventory: Raw and In-Process125,200 Accounts Payable Control125,200 B) Accounts Payable Control125,200 Allocated Costs: Direct Materials125,200
C) Accounts Payable Control125,200 Materials Inventory125,200 D) Allocated Costs: Direct Materials125,200 Inventory: Raw and Material125,200 Answer: A Diff: 3 Terms: backflush costing Objective: 7 AACSB: Analytical skills 7) Which of the following journal entries would be recorded when units are sold for the month? A) Cost of Goods Sold159,750 Inventory: Raw and In-Process159,750 B) Cost of Goods Sold159,750 Inventory: Raw and In-Process117,375 Conversion Costs Allocated42,375 C) Inventory: Raw and In-Process117,375 Conversion Costs Allocated42,375 Cost of Goods Sold159,750 D) Cost of Goods Sold159,750
Inventory: Raw and In-Process114,750 Conversion Costs Allocated45,000 Answer: B Explanation: B) Direct materials ($125,200/40,000)$3. 13 Conversion costs ($45,200/40,000)1. 13 Total$4. 26 37,500 ? $4. 26= $159,750 37,500? $3. 13= $117,375 37,500 ? $1. 13= $42,375 Diff: 3 Terms: backflush costing Objective: 7 AACSB: Analytical skills 8) Which of the following entries would occur if the only trigger point is the production of finished units? A) Cost of Goods Sold159,750 Inventory: Raw and In-Process Control114,750 Conversion Costs Allocated45,000 B) Inventory: Raw and In-Process Control117,375
Conversion Costs Allocated42,375 Cost of Goods Sold159,750 C) Finished Goods170,400 Accounts Payable Control125,200 Conversion Costs Allocated45,200 D) Accounts Payable Control125,200 Conversion Costs Allocated45,200 Finished Goods170,400 Answer: C Explanation: C) 40,000 ? $4. 26= $170,400 40,000 ? $3. 13= $125,200 40,000 ? $1. 13 = $45,200 Diff: 3 Terms: backflush costing Objective: 7 AACSB: Analytical skills 9) Companies that would benefit from backflush costing include companies: A) which have fast manufacturing lead times B) whose inventories vary from period to period C) companies that require audit trails
Cite this Page
Inventory Management And Simplified Costing Methods Objective. (2017, Feb 14). Retrieved from https://phdessay.com/inventory-management-and-simplified-costing-methods-objective/
Run a free check or have your essay done for you
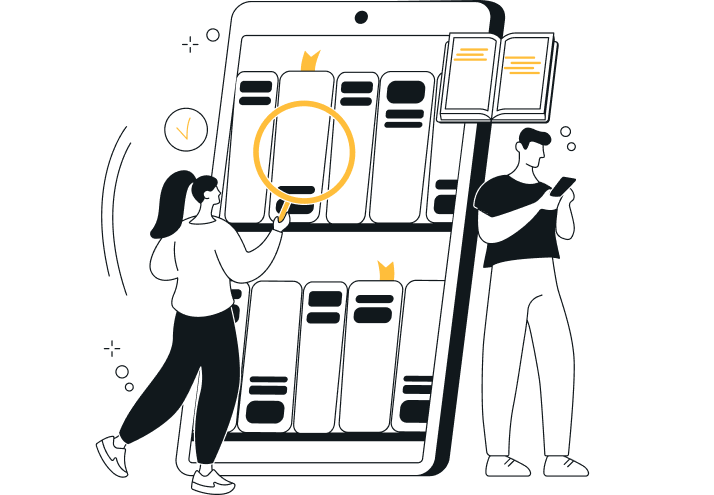