Competitive Advantage in Fast Fashion
Fast fashion is a term used to describe clothing collections that are based on the most recent fashion trends presented at Fashion Week in both the spring and autumn of every year. These trends are designed and manufactured quickly and cheaply to allow the mainstream consumer to take advantage of current clothing styles at a lower price. This chapter highlights the sources of competitive advantage that may exist inside the field of fast fashion. Studying in detail the major players who are part of H&M, Gap, Zara, and Benetton.
SUPPLY CHAIN
A supply chain is a system of organizations, people, technology, activities, information, and resources involved in moving a product or service from supplier to the customer. Supply chain activities transform natural resources, raw materials, and components into a finished product that is delivered to the end customer.
Order custom essay Competitive Advantage in Fast Fashion with free plagiarism report
In sophisticated supply chain systems, used products may re-enter the supply chain at any point where residual value is recyclable. Supply chains are increasingly being seen as integrated entities, and closer relationships between the organizations throughout the chain can bring competitive advantage, reduce costs, and help to maintain a loyal customer base.
There are two main differences to value chains: Supply chains are more detailed since they incorporate not only activities but also connect intra-organizational value chains by products, services, and information flows.
Supply chains underlie value chains because, without them, no producer has the ability to give customers what they want when and where they want it at the price they want. Producers compete with each other only through their supply chains, and no degree of improvement at the producer's end can make up for the deficiencies in a supply chain that reduce the producer's ability to compete.
A typical supply chain begins with the ecological and biological regulation of natural resources, followed by the human extraction of raw materials and includes several production links, such as component construction, assembly, and merging before moving on to several layers of storage facilities of ever-decreasing size and ever more remote geographical locations, and finally reaching the consumer. All organizations have supply chains of varying degrees, depending on the size of the organization and the type of product manufactured. These networks obtain supplies and components, change these materials into finished products, and then distribute them to the customer.
Managing the chain of events in this process is what is known as supply chain management. The Council of Supply Chain Management Professionals (CSCMP) defines Supply Chain Management as follows: “Supply Chain Management encompasses the planning and management of all activities involved in sourcing and procurement, conversion, and all logistics management activities. Importantly, it also includes coordination and collaboration with channel partners, which can be suppliers, intermediaries, third-party service providers, and customers.
In essence, supply chain management integrates supply and demand management within and across companies. Supply Chain Management is an integrating function with primary responsibility for linking major business functions and business processes within and across companies into a cohesive and high-performing business model. It includes all of the logistics management activities noted above, as well as manufacturing operations, and it drives coordination of processes and activities with and across marketing, sales, product design, finance and information technology.
Effective management must take into account coordinating all the different pieces of this chain as quickly as possible without losing any of the quality or customer satisfaction, while still keeping costs down. The first step is obtaining a customer order, followed by production, storage and distribution of products and supplies to the customer site. Customer satisfaction is paramount. Included in this supply chain process are customer orders, order processing, inventory, scheduling, transportation, storage, and customer service.
A necessity in coordinating all these activities is the information service network. In addition, key to the success of a supply chain is the speed in which these activities can be accomplished and the realization that customer needs and customer satisfaction are the very reasons for the network. Reduced inventories, lower operating costs, product availability and customer satisfaction are all benefits which grow out of effective supply chain management.
Furthermore, market demands, customer service, transport considerations, and pricing constraints all must be understood in order to structure the supply chain effectively. These are all factors, which change constantly and sometimes unexpectedly, and an organization must realize this fact and be prepared to structure the supply chain accordingly.
DECISIONS ON THREE LEVELS
Supply chain management decisions are often said to belong to one of three levels; the strategic, the tactical, or the operational level. It shows the three level of decisions as a pyramid shaped hierarchy. The decisions on a higher level in the pyramid will set the conditions under which lower level decisions are made. On the strategic level long term decisions are made. According to Ganeshan and Harrison, these are related to location, production, inventory, and transportation. Location decisions are concerned with the size, number, and geographic location of the supply chain entities, such as plants, inventories, or distribution centers.
The production decisions are meant to determine which products to produce, where to produce them, which suppliers to use, from which plants to supply distribution centers, and so on. Inventory decisions are concerned with the way of managing inventories throughout the supply chain. Transport decisions are made on the modes of transport to use. Decisions made on the strategic level are of course interrelated. For example decisions on mode of transport are influenced by decisions on geographical placement of plants and warehouses, and inventory policies are influenced by choice of suppliers and production locations.
Modeling and simulation is frequently used for analyzing these interrelations, and the impact of making strategic level changes in the supply chain. On the tactical level medium term decisions are made, such as weekly demand forecasts, distribution and transportation planning, production planning, and materials requirement planning. The operational level of supply chain management is concerned with the very short term decisions made from day to day. It 4 shows for each level types of decisions made.
Components of facilities decisions are:
Location: centralize to gain economies of scale (major efficiency) or decentralize to be more responsive. Other issues include quality and costo f workers, costo f facility, infrastructure, taxes, quality of life,etc. Capacity: excess capacity allows a company to be more responsive to changes in the level of demand (major flexibility), but at the expensive of efficiency. Manufacturing methodology: decisions between a product or functional focus, between flexible or dedicated capacity. Warehousing methodology: choose between:
SKU storage: stores all of one type of product together, Job lot storage: stores different products together to satisfy a particular customer or job, cross-docking: product is not actually warehoused in the facility, instead the facility is used to house a process where trucks from suppliers arrive and unload large quantities of different products. These large lots are then broken down into smaller lots. Smaller lots of different products are recombined according to the needs of the day and quickly loaded onto outbound trucks that deliver the product to their final destination.
Inventory
Inventory encompasses all the raw materials, work in process, and finished goods within a supply chain. Changing inventory policies can dramatically alter the supply chain’s efficiency & responsiveness. There are three basic decisions to make regarding the creation and holding of inventory: Cycle Inventory: this is the amount of inventory needed to satisfy demanf for the product in the period between purchases of the product. Safety Inventory: inventory that is held as a buffer against uncertainly.
If demand forecasting could be done with perfect accuracy, then the only inventory that would be needed would be cycle inventory. Seasonal Inventory: this is inventory that is built up in anticipation of predictable increases in demand that occur at certain times of the year. Inventory has different impacts: Can increase amount of demand that can be met by increasing product availability Can reduce costs by exploiting economies of scale in production, transportation, and purchasing. Can be used to support a firm’s competitive strategy.
More inventory increases responsiveness, less inventory increases efficiency (reduces cost). Can significantly affect material flow/cycle/throughput time because if you move your inventory faster, you don’t need as much inventory (inventory velocity). Transportation Transportations entails moving inventory from point to point in the supply chain. Components of transportation decisions are: Mode of transportation: is the manner in which a product is moved (air, truck,rail, ship, pipeline,eletronic). Each mode differs with respect to speed, size of shipments, cost, and flexibility.
Routes and networks selection: are respectively paths along which a product can be shipped and a collection of locations and routes. In house or out source the transportation function. Many companies use third-party logistics provider (3PL) to perform some or all of their transportation activities. Usually companies outsource the distribution. Faster transportation allows a supply chain to be more responsive but generally less efficient. Less than full truckloads allows a supply chain to be more responsive but generally less efficient.
Transportation can be used to support a firm’s competitive strategy. Customers may demand and be willing to pay for a high level of responsiveness. Information Information serves as the connection between various stages of a supply chain, allowing them to coordinate & maximize total supply chain profitability. It is also crucial to the daily operations of each stage in a supply chain for a production scheduling system. Components of information decisions are: Push versus pull: push systems (like MRP) need information on anticipated demand to create production and purchasing schedules.
Pull systems (like JIT) need accurate qnd quick information on actual demand to move inventory and schedule production in the chain. Enabling technologies: many technologies exist to share and analyze information in the supply chain: EDI: electronic data interchange. ERP: enterprise re source planning. SCM software: Supply Chain Management Software Internet Forecasting & planning to anticipate and meet future demands. Available information is used to make tactical forecasts to guide the setting of monthly and quarterly production schedules & time table Coordination and information sharing
Information allows supply chain to become more efficient and more responsive at the same time (reduces the need for a trade-off)
SCOR
The Supply Chain Operations Reference Model (SCOR Model) is one of the very few dedicated methods for supply chain modelling and has also a high relevance for many industries. The model has been developed by The Supply-Chain Council (SCC), an independent not-for-profit firm with more than 1,000 corporate members.
It was first introduced in 1996 and is now available in version 8. 0. In contrast to generic process modelling methods, SCOR is actually a reference model, because it defines activities that can be found in any supply chain. In that sense, it can be regarded as a successor to the value chain model by Porter. The SCOR model covers the followings levels of abstraction: Top level ( level 1) Configuration level (level 2) Process element level (level 3) Implementation level
SCOR defines five core management processes called process types that are relevant for all firms in a supply chain (scope of the model). Three of these process types form a sequence of source, make, and deliver. The process types are: Source (S) Processes that procure goods and services to meet planned or actual demand. Make (M) Processes that transform a product or service to a finished state to meet planned or actual demand. Deliver (D) Processes that provide finished goods and services to meet planned or actualdemand, typically including order management, transportation management,and distribution management.
Return (R) Processes associated with returning or receiving returned products for any reason. These processes extend into post-delivery customer support. The top level, however, can not be instantiated, thus this level defines only the scope of the SCOR model. The modelling of actual or planned supply chains starts on the next level. Configuration level beyond the five main processes, there is a further classification of processes into three categories: Planning: processes that plan resources to meet demand in appropriate time intervals. re repeated periodically and have a great influence on the response time of the supply chain.
Execution: processes as executive involved in the activities of scheduling, sequencing, processing, testing, and handling of products, affecting the cycle time of the order fulfillment. Enable: processes involving information and managerial aspects that affect the other two processes From five main processes the SCOR model identifies 26 processes of second level, each belonging to one of three process type defined above. For instance, categories for ‘source’ are:
S1 ‘source stocked product’: The procurement, delivery, receipt and transfer of raw material items, subassemblies, product and/or services. S2 ‘source make-to-order product’: The procurement and delivery of a product that is built to a specific design or configured based on the requirements of a particular customer order. S3 ‘source engineer-to-order product’: The negotiation, procurement and delivery of engineer-to-order assemblies or specialized product or services that are designed and built based on the requirements or specifications of a particolar customer order or contract.
By selecting the relevant process categories, a firm can represent its operational strategy. For instance, the relevant source categories need to be selected and mapped to respective products and/or services (thus a firm can implement multiple source categories reflecting diverse sourcing strategies). Process element level The process element level decomposes the process categories by adding process element definitions, process element information inputs/outputs, process performance metrics, and best practices.
SCOR does not define functions and organizational entities for these elements, thus it strictly focuses processes. Implementation level Implementation level aims to implement management practices, defining the elements necessary to gain a competitive advantage and adapt to changes. METRICS SCOR defines metrics that measure effectiveness and efficiency of a supply chain. For this purpose, metrics form a hierarchy along the SCOR levels: Level 1 metrics relate to the overall planning of a supply chain (thus these metrics are differentiated to source, make etc. ).
Level 2 and 3 metrics decompose the level 1 and 2 metrics respectively. Each level 1 metric contribute to realising a performance attribute. A performance attributes is a characteristics of the supply chain that permits it to be analysed and evaluated against other supply chains with competing strategies. For instance, a supply chain is reliable to a certain degree or not. The level 1 metrics and associated performance attributes are defined as follows.
This first stage in developing supply chain agility takes into consideration what and how many products to produce, and what, if any, parts or components should be produced at which plants or outsourced to capable suppliers. These strategic decisions regarding production must also focus on capacity, quality and volume of goods, keeping in mind that customer demand and satisfaction must be met. Operational decisions, on the other hand, focus on scheduling workloads, maintenance of equipment and meeting immediate client/market demands. Quality control and workload balancing are issues which need to be considered when making these decisions.
Supply Next, an organization must determine what their facility or facilities are able to produce, both economically and efficiently, while keeping the quality high. But most companies cannot provide excellent performance with the manufacture of all components. Outsourcing is an excellent alternative to be considered for those products and components that cannot be produced effectively by an organization’s facilities. Companies must carefully select suppliers for raw materials. When choosing a supplier, focus should be on developing velocity, quality and flexibility while at the same time reducing costs or maintaining low cost levels.
In short, strategic decisions should be made to determine the core capabilities of a facility and outsourcing partnerships should grow from these decisions.
PUSH VS PULL
KEY INTERNATIONAL COMPETITORS
Fast-fashion specialty retailers with exceptional speed-to-market have outperformed department stores and less nimble specialty stores not only in their profit argins, but also in their pace of revenue growth, according to a study by The Sage Group LLC’s Apparel and Retail Group. The mayor comparable players that compete in fast fashion at international level are: Inditex -Zara Benetton H&M Gap Each of them has a vertical scope. Zara owned much of its production and most of its stores, the Gap and H&M, which were the two largest specialist apparel retailers in the world, ahead of inditex, owned most of their stores but outsourced all production. Benetton, in contrast, has invested relatively heavily in production, but licensees ran its stores.
The four competitors were also positioned differently in product space from Inditex’s chains. Inditex’s flagship brand, Zara, is relatively perceived as more fashionable than all the other three ann prices less than Benetton and Gap but higher than H&M. In these fuor competitors, Benetton and Gap place a relatively less fashionable and higher price, while Zara and H&M is more fashionable and price lower.
Meanwhile, the major Italian player ‘Benetton’ marched on high street with, offering colorful designer clothing for the whole family. Their strategy resulted affirmative with noticeably contemporary window showcase in all stores with independent units. The company was successful in Britain, however, having a long standing in the market, they witnessed failure to keep up pace with the accelerated high fashion pressure by the other European competitors, which are now the known as Mango, H&M and Zara. The rise of these competitors on high street has been witness successful because of a higher demand for fast fashion.
Styles showed in magazines and other advertorials are what people wish to wear. Top designers have created collection extensions, which cater people who can afford to spend their hard earned cash on triple figure. This resulted success to the affordable collection of European fashion brands A Swedish player, H&M offered readymade clothing stores – stocked with fashionable collection at reasonable costs. Its successful strategy was its own slogan ‘fashion & quality at the best price’ innovative design, reasonably priced and competent logistics.
Based in Stockholm, a team of 100 fashion designers assures that nothing has been imitated from the runway platforms. They are mostly inspired from street-trends, movies, magazines and exhibitions. Impressively, the designs reach retail shelves within 2-3 weeks. H&M’s high profile designer tie-ups with Karl Lagerfield and Stella McCartney have resulted entire collections available to the mass people at lower prices. This strategy is supported by huge advertising campaigns, which easily compete with the major brand.
In a world of advertisements and promotions, there is one store that has made strategy to not to spend penny on advertising, “Zara”, a wing of Europe's biggest, rapidly evolving and most triumphant fashion clothing retailers, Grupo Inditex. Other well popular stores in similar chain are Massimo Dutti, Bershka and Pull and Bear. Inditex operates business via more than two thousand stores in 56 countries. The first Zara shop was launched in 1975 at La Coruna, Galicia and at present it operates more than four hundred owned stores globally.
In the previous five years they have witnessed sales up by 25 percent year on year. Zara runs its own design and production unit in La Coruna, Spain, which leads cancellation of the large out-sourcing operations, like H does in over nine hundred firms. It is modern, offering up-to-date lifestyle yet standard clothing lines for men, women and children. Zara offers reasonably priced, radical clothing, however, not of the top quality, which will last only for some seasons. As same as Zara, H can also put designs on retail shelves within three weeks.
Its product assortment is cheap and small yet frequent, offering consumers huge selection that results repeated visits to their stores to find “What’s New”. Hitherto, Zara has launched over ten thousand new designs and most of these will just be attainable for few weeks. Another Spanish player, Mango is a reputed multinational brand devoted to designing, producing and selling fast fashion and accessories only for women. Its clothing line includes Suit, Casual Sport, and Mng Jeans. It might not be as huge as H or Grupo Inditex, but has played excellent particularly in the UK.
No shopping malls resemble absolute with exclusive of these three brands. The pace of these companies in responding to changing consumer demands is an ideal proof to the retailing, producing and logistics skills needed in latest fashion industry. These new strategies are set up to develop aptitude to take advantage of the challenges of a competitive world market. Besides the diversification in product assortments there is one thing common in all these brands that is “intelligent logistics”. Well-organized communication between sales staff directly to the headquarters and producers lead them to match steps with high speed turnover.
The fact is that buyers are becoming preference savvy and smarter in order to what they shop. Even though they always have their preferred designer, they are also acquainted that a throwaway piece of fast fashion from a retail chain store will complete their outfit choices. At so reasonably priced all of these retail perceptions play on Friday nights when people feels they have nothing to wear. Retailers are sent in a scuffle to make-out the major catwalk trends from the drawing sheets to the sales shelves as fast as possible.
Cite this Page
Competitive Advantage in Fast Fashion. (2018, Feb 16). Retrieved from https://phdessay.com/competitive-advantage-in-fast-fashion/
Run a free check or have your essay done for you
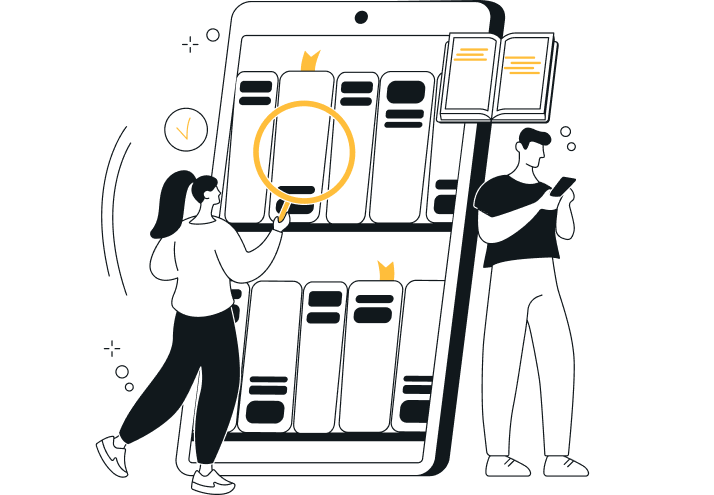