Bpr Business Process Reenigneering
Introduction
Business process re-engineering is a business management strategy, originally pioneered in the early 1990s, focusing on the analysis and design of workflows and processes within an organization. BPR aimed to help organizations fundamentally rethink how they do their work in order to dramatically improve customer service, cut operational costs, and become world-class competitors.
In the mid-1990s, as many as 60% of the Fortune companies claimed to either have initiated reengineering efforts, or to have plans to do so. BPR seeks to help companies radically restructure their organizations by focusing on the ground-up design of their business processes. According to Davenport (1990) a business process is a set of logically related tasks performed to achieve a defined business outcome. Re-engineering emphasized a holistic focus on business objectives and how processes related to them, encouraging full-scale recreation of processes rather than iterative optimization of sub processes.
Order custom essay Bpr Business Process Reenigneering with free plagiarism report
Business process re-engineering is also known as business process redesign, business transformation, or business process change management.
Overview
Business process re-engineering (BPR) began as a private sector technique to help organizations fundamentally rethink how they do their work in order to dramatically improve customer service, cut operational costs, and become world-class competitors. A key stimulus for re-engineering has been the continuing development and deployment of sophisticated information systems and networks.
Leading organizations are becoming bolder in using this technology to support innovative business processes, rather than refining current ways of doing work. Reengineering guidance and relationship of Mission and Work Processes to Information Technology. Business Process Re-engineering (BPR) is basically rethinking and radically redesigning an organization's existing resources. BPR, however, is more than just business improvising; it is an approach for redesigning the way work is done to better support the organization's mission and reduce costs.
Reengineering starts with a high-level assessment of the organization's mission, strategic goals, and customer needs. Basic questions are asked, such as "Does our mission need to be redefined? Are our strategic goals aligned with our mission? Who are our customers? " An organization may find that it is operating on questionable assumptions, particularly in terms of the wants and needs of its customers. Only after the organization rethinks what it should be doing, does it go on to decide how best to do it.
Within the framework of this basic assessment of mission and goals, re-engineering focuses on the organization's business processes—the steps and procedures that govern how resources are used to create products and services that meet the needs of particular customers or markets. As a structured ordering of work steps across time and place, a business process can be decomposed into specific activities, measured, modeled, and improved.
It can also be completely redesigned or eliminated altogether. Re-engineering identifies, analyzes, and re-designs an organization's core business processes with the aim of achieving dramatic improvements in critical performance measures, such as cost, quality, service, and speed. Re-engineering recognizes that an organization's business processes are usually fragmented into sub processes and tasks that are carried out by several specialized functional areas within the organization.
Often, no one is responsible for the overall performance of the entire process. Re-engineering maintains that optimizing the performance of sub processes can result in some benefits, but cannot yield dramatic improvements if the process itself is fundamentally inefficient and outmoded. For that reason, re-engineering focuses on re-designing the process as a whole in order to achieve the greatest possible benefits to the organization and their customers.
This drive for realizing dramatic improvements by fundamentally re-thinking how the organization's work should be done distinguishes re-engineering from process improvement efforts that focus on functional or incremental improvement.
History
In 1990, Michael Hammer, a former professor of computer science at the Massachusetts Institute of Technology (MIT), published an article in the Harvard Business Review, in which he claimed that the major challenge for managers is to obliterate forms of work that do not add value, rather than using technology for automating it.
This statement implicitly accused managers of having focused on the wrong issues, namely that technology in general, and more specifically information technology, has been used primarily for automating existing processes rather than using it as an enabler for making non-value adding work obsolete. Hammer's claim was simple: Most of the work being done does not add any value for customers, and this work should be removed, not accelerated through automation. Instead, companies should reconsider their processes in order to maximize customer value, while minimizing the consumption of resources required for delivering their product or service.
A similar idea was advocated by Thomas H. Davenport and J. Short in 1990, at that time a member of the Ernst & Young research center, in a paper published in the Sloan Management Review This idea, to unbiased review a company’s business processes, was rapidly adopted by a huge number of firms, which were striving for renewed competitiveness, which they had lost due to the market entrance of foreign competitors, their inability to satisfy customer needs, and their insufficient cost structure.
Even well-established management thinkers, such as Peter Drucker and Tom Peters, were accepting and advocating BPR as a new tool for (re-)achieving success in a dynamic world. During the following years, a fast growing number of publications, books as well as journal articles, were dedicated to BPR, and many consulting firms embarked on this trend and developed BPR methods. However, the critics were fast to claim that BPR was a way to dehumanize the work place, increase managerial control, and to justify downsizing, i. e. major reductions of the ork force, and a rebirth of Taylorism under a different label.
Despite this critique, reengineering was adopted at an accelerating pace and by 1993, as many as 60% of the Fortune 500 companies claimed to either have initiated reengineering efforts, or to have plans to do so. This trend was fueled by the fast adoption of BPR by the consulting industry, but also by the study Made in America, conducted by MIT, that showed how companies in many US industries had lagged behind their foreign counterparts in terms of competitiveness, time-to-market and productivity.
Development after 1995 With the publication of critiques in 1995 and 1996 by some of the early BPR proponents, coupled with abuses and misuses of the concept by others, the reengineering fervor in the U. S. began to wane. Since then, considering business processes as a starting point for business analysis and redesign has become a widely accepted approach and is a standard part of the change methodology portfolio, but is typically performed in a less radical way as originally proposed.
More recently, the concept of Business Process Management (BPM) has gained major attention in the corporate world and can be considered as a successor to the BPR wave of the 1990s, as it is evenly driven by a striving for process efficiency supported by information technology. Equivalently to the critique brought forward against BPR, BPM is now accused of focusing on technology and disregarding the people aspects of change.
BPR Methodology
BPR methodology is a structured sequence of activities that constitutes the typical BPR project. BPR refers to a re-design of business processes by using IT.
Its methodology is to give a guideline or progress of how the business process to be re-designed. There are number of methodologies for an organization to practice. According to S. Muthu, L. Whitman and S. Hossein Cherahhi , there are 5 examples of BPR methodologies. To be simple, a consolidated methodology has been developed from those 5 methodologies. That is similar to the 5 phases mentioned in class: visioning, mobilization, process redesign, implementation and monitoring & maintaining.
This phase is to design the visions and directions that a company should go with in order to improve efficiency of the targeted business processes and customer satisfaction. In this stage, the organization should identify the reengineering opportunities, enabling technologies and direct impact on customers. In this phase, a reengineering team should be formed. The team should outline the performance goals, BPR plan and budget. Processes to be redesigned should be selected. IT people are involved to make assessment on IT infrastructure and provide information for better business process redesign.
This stage is to analyze and compare AS-IS processes and TO-BE processes. After identifying the potential improvements of the existing processes, modeling methods can be used to develop the TO-BE models. Integration can be done afterwards. Training programs are initiated in this stage to provide the skills of fitting the TO-BE processes. IT infrastructure and the organization are also need to be adjusted to fit the TO-BE processes.
The new processes should be monitored and modified on a continuous basis, especially the progress of action and the results. To carry out a good BPR methodology, organizations are recommended to consider each phase carefully. Each phase should be comprehensive enough for execution to drive for a success in achieving the organization’s vision and strategy. Business Process Reengineering Principles
- Organize around outcomes, not tasks .
- Have those who use the output of the process perform the process.
- Subsume information-processing work into the real work that produces the information.
- Treat geographically dispersed resources as though they were centralized.
- Link parallel activities instead of integrating their results.
- Put decision points where the work is performed and build controls into the process.
- Capture information once and at the source.
Advantages and Disadvantages Of BPR
Business process reengineering (BPR) is a program that systemically breaks down the process a business uses and starts over with new, more efficient methods -- basically a redesign or a reboot.
A business process is a collection of procedures, steps or activities the business uses to get the product from development to the customer. Businesses use BPR for various reasons, including cutting costs and improving overall production. Nevertheless, BPR also has its drawbacks. Identifies Waste and Encourages Ideas The aim of BPR is to help businesses pinpoint obsolete steps, items or workers in a business process. For example, if four workers perform a task, the business may discover only two workers can get the job done during reengineering. BPR encourages employee input and participation.
The workers who have familiarity with the processes under study can point out flaws and voice ideas for improvement. Requires Investment and the Right Business Types BPR typically requires an investment, particularly in technology. Outdated methods, such as doing a task by hand, face replacement by computer programs. The programs improve efficiency and reduce errors, but the company must invest in the software and training, a costly option for companies looking to cut expenses immediately.
Not all business types benefit from BPR. For example, a manufacturing company may not have the option of edesigning processes without sacrificing safety or product quality. Cuts Costs and Improves Functionality Removing unnecessary steps cuts down on time and confusion among workers. Assigning tasks that multiple workers would typically handle to one worker gives customers a clear point of contact for help or service. Even by investing more money in technology at the start, companies typically save money over time with the redesigned methods. For example, improving or updating electronic components incurs an up-front cost, but saves money over time by eliminating errors due to outdated components.
Lowers Worker Morale Some workers may not adapt to the BPR changes, and those assigned new responsibilities can become overwhelmed. Other workers become obsolete if their primary function is eliminated as part of a process overhaul. Management must provide support and guidance during BPR. Failure of the management team to assist workers and set an example during the BPR process may lead to failure, disorganization and staff problems.
- Advocates report failure rates of 50% to 70%
- Sutcliffe [1999] reviewed difficulties
- Employee resistance to change
- Inadequate attention to employee concerns Inappropriate staffing
- Inadequate tools
- Mismatch of strategies & goals
- Lack of oversight
- Failure of leadership commitment
Case Study- II
Mahindra & Mahindra: Implementing BPR Abstract: The case examines the reasons behind automobile major Mahindra & Mahindra's decision to implement a Business Process Reengineering (BPR) program. The case explores in detail the implementation procedure at the company and the benefits that accrued from the BPR program. In addition, the case discusses the concept of BPR, its benefits, and the steps that need to be taken to ensure the success of such initiatives.
Issues: Examine the benefits that a BPR program can offer to an organization when it is effectively implemented M;M's Problem Plants In the mid-1990s, India's largest multi utility vehicle (MUV) and tractor manufacturer M;M was facing serious problems at its Igatpuri and Kandivili plants in Maharashtra. The plants were suffering from manufacturing inefficiencies, poor productivity, long production cycle, and sub-optimal output. The reason: highly under-productive, militantly unionized, and bloated workforces.
The company had over the years been rather lenient towards running the plants and had frequently crumbled under the pressure of union demands. The work culture was also reportedly very unhealthy and corruption was widespread in various departments. Alarmed at the plant's dismal condition, Chairman Keshub Mahindra tried to address the problem by sacking people who allegedly indulged in corrupt practices. M&M also tried to implement various voluntary retirement schemes (VRS), but the unions refused to cooperate and the company was unable to reduce the labor force.
Business Process Reengineering
During this period, M&M was in the process of considering the implementation of a Business Process Reengineering (BPR) program throughout the organization including the manufacturing units. Because of the problems at the Igatpuri and Kandivili plants, M&M decided to implement the program speedily at its manufacturing units. The program, developed with the help of the UK-based Lucas Engineering Systems, was first implemented on an experimental basis at the engine plant in Igatpuri. Simultaneously, an exercise was initiated to assess the potential benefits of implementing BPR and its effect on the unions.
M&M's management was not surprised to learn that the unions expressed extreme displeasure at the decision to implement BPR and soon went on a strike. However, this time around, the management made it clear that it would not succumb to union demands. Soon, the workers were surprised to see the company's senior staff come down to the plant and work in their place. With both the parties refusing to work out an agreement, observers began casting doubts on the future of the company's grand plans of reaping the benefits of BPR. Background Note
Mahindra ; Mahindra Ltd. (M;M) was the flagship company of the Mahindra group, one of the top ten industrial houses in India. The company's history dates back to 1945, when two brothers, J. C. Mahindra and K. C. Mahindra, decided to start a business of general-purpose utility vehicles. The brothers formed a company, Mahindra & Mohammed Ltd. , in association with their friend Ghulam Mohammed. In October 1947, the first batch of 75 jeeps was released for the Indian market. In 1948, the company was renamed Mahindra & Mahindra Ltd.
Over the next few decades, the group promoted many companies in areas as diverse as hotels, financial services, auto components, information technology, infrastructure development and trading to name a few (Refer Exhibit I for M&M's history). Though M;M had established itself in the markets and was among the leading players in many of the segments it operated in, it realized that some of its businesses were not closely related to its core business. This realization marked the beginning of the biggest change exercise since the company's inception. In 1994, a major restructuring exercise was initiated as part of a BPR program.
M&M introduced a new organizational model, in which various divisions and companies were regrouped into six distinct clusters of related businesses, each headed by a president. M&M's core activities, automotive and tractors were made autonomous business units. The other activities of the group were organized into infrastructure, trade and financial services, telecommunication and automotive components. According to company sources, the whole exercise was intended to develop a conceptual map to provide direction for the future growth of various business lines.
It was decided that, in future, the group would confine its expansion to the identified thrust sectors. The two main operating divisions of the company were the automotive division, which manufactured UVs and LCVs, and the farm equipment division, which made tractors and farm implements. The company employed over 17,000 people and had six state-of-the-art manufacturing facilities spread over 500,000 square meters. The plants were situated at Kandivili (MUVs and Tractors), Nasik (MUVs), Zaheerabad (LCVs, Voyager, three-wheelers), Igatpuri (Engines) and
Nagpur (Implements and tractors) Excerpts About BPR The concept of BPR was popularized in the early 1990s by Michael Hammer and James Champy in their best-selling book, 'Reengineering the Corporation. ' The authors said that radical redesign and reorganization of an enterprise was necessary to lower costs and increase the quality of service. According to them, IT was the key enabler for that radical change. Hammer and Champy felt that the design of the workflow in most large corporations was based on assumptions about technology, people and organizational goals that were no longer valid.
They recommended seven principles of reengineering for streamlining work processes and, consequently, achieving significant levels of improvement in quality, time management and cost (Refer Table I)... M;M's Experience with BPR By the mid-1990s, BPR had become a popular tool globally, with many leading organizations implementing it. However, when M&M undertook the exercise, it was still a new concept in India. M&M's workforce, as mentioned earlier, resisted this attempt to reengineer the organization.
Soon after the senior staff began working on the shop floors, the first signs of the benefits of BPR became evident. Around a 100 officers produced 35 engines a day as compared to the 1200 employees producing 70 engines in the pre-BPR days. After five months, the workers ended the strike and began work in exchange for a 30% wage hike. As the situation returned to normalcy, BPR implementation gained momentum. M;M realized that it would have to focus on two issues when implementing the BPR program: reengineering the layout and method of working, and productivity... The Future
Summing up the company's BPR experience, Anand Mahindra said, "Let me put it in a simple way. If we have facilities in Kandivili today, which are not just surviving but thriving, it is all due to BPR.
Conclusion
The reengineering profoundly changes all aspects of business and people. Part of the organization is easy to change by reinventing a way to work. However, the other part, people, is very difficult to change. In particular, it requires not only jobs and skills change but also people's styles - the ways in which they think and behave - and their attitudes - what they believe is important about their work. These are indispensable factors to determine whether reengineering succeeds or not. Leaders must help people to cope with these changes.
References
- Business Process Change: Reengineering Concepts, Methods, and Technologies by Varun Autor Grover and William J. Kettinger
- Business Process Reengineering: Breakpoint Strategies for Market Dominance by Henry J. Johansson
- Business Process Reengineering: An Executive Resource for Implementation by Harold S. Resnick
- www.bus.iastate.edu/ for case study references.
Cite this Page
Bpr Business Process Reenigneering. (2017, Apr 27). Retrieved from https://phdessay.com/bpr-business-process-reenigneering/
Run a free check or have your essay done for you
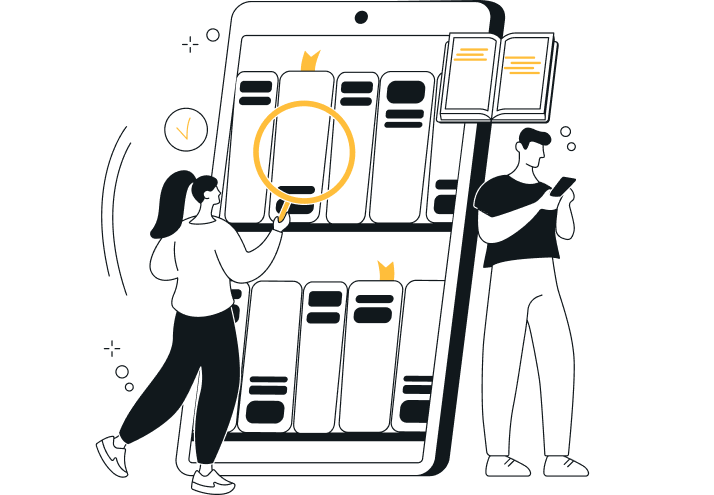