Logistics Management Essay
Logistics Management
Introduction
The management skills and perspective of the 20th century are not sufficient to meet the challenges anticipated for the 21st Century. The requisite paradigm shift described in the literature includes a cross-functional, multidimensional, lifecycle approach that emphasizes the full integration of enterprise infrastructure elements: technology, process, and people. Logistics management methodology applied by logisticians in integrated logistics synthesizes acquisition theory; operational theory, supply chain management theory and uses related models, tools, techniques, and practices. Focusing on this cost-effective requirement often overlooks the need for communication, coordination, and control functions among the components. Meeting this need requires the ability to visualize the overall scope of work, to define all the components, their interfaces and interdependences, the individual and collective deliverables, as well as all life cycle activities, their costs, and performance tracking indicators throughout the project (Rivers).
Order custom essay Logistics Management Essay with free plagiarism report
Logistics is receiving increasing attention in the press and in universities around the globe. Managers once considered the logistics function to be a non-strategic component of the firm. Today more firms are realizing the strategic importance of logistics, both from a cost management standpoint, and as a way to improve customer responsiveness. Logistics practice offers a blended management and leadership approach based on an integrated synthesis of all methodologies, theories, tools, and techniques of management-related specialty disciplines currently available. Logistics theory provides a clear-cut approach for turning ideas into plans and those plans into actions producing entities, which are effective, efficient, sustainable, improve-able, as well as retire-able and/or recycle-able. Today the multi-dimensional model used by logisticians provides the initial planning, funding, and controlling activities that help assure consumers or users will receive products and service which meet all system requirements and can be supported economically and expeditiously throughout its life cycle.
This paper explores a broad area of logistics management. Firstly, it provides the definition and overview of logistics management. Then role of logistics in organization is considered thoroughly from the various aspects. Following, the logistics management strategy is discussed briefly. Finally, some conclusive remarks are presented, stressing the role of logistics manager in organization.
Definition
The first use of "logistics in management was when Alexander the Great used planning during his reign as Macedonian Ruler," according to (Van Mieghw 67). Glaskowsky, Hudson, and Ivie depicts how Swiss Baron Antione-Henry Jomini defined logistics as the practical art of moving armies. They illustrate that as with other management concepts, the origins of the term Logistics as found in the military. Authors state, "evidently the term logistics is in the process and until logistics matures and shapes, content and emphasis it derives from the concrete environment we must accept it." (Glaskowsky, Hudson, and Ivie 324)
Thus, logistics is not susceptible to a single, simple, and permanent definition. It is a broad field of endeavor consisting of many interdisciplinary activities that, when applied together, constitute the art of science of logistics. Jones adds logistics as an ancient art and emerging science. (Jones 324) For most of this period, people have had difficulty in agreeing on its precise definition. Even today, the meaning of logistics is somewhat inexact. Henn further expounds on the definition of logistics as "the integrated design, management, and operation of physical, human, financial and information resources over the lifetime of a product, system, or service (as cited in Glaskowsky et al. 23)." In economic terms, it creates time and place utility in contrast to form utility.
Jones goes further in stating that logistics is a broad field of endeavor consisting of many interdisciplinary activities. The Greek word for logistics deals with mathematical calculations, while its French usage relates to the supplying, quartering and movement of troops The United States gave the word a much broader definition, which is that of total support of a product during its system life cycle (Jones).
SOLE defines logistics as the art and science of management, engineering, and technical activities concerned with requirements, design, supplying and maintaining resources to support objectives, plans and operations of a firm (http://www.sole.org/). Related functions/activities must be performed, managed and organized as integrated systems and subsystems. The depth of knowledge implied for professional personnel involved in logistics is considerable - certainly more than one could reasonably expect to find within a single individual. The necessary systems viewpoint with proper attention to details suggests a team composed to experts (http://www.sole.org/).
The Council of Logistics Management defines logistics as follows:
Logistics is that part of the supply chain process that plans, implements, and controls the efficient, effective flow and storage of goods, services, and related information from the point of origin to the point of consumption in order to meet customers' requirements (as cited in Bowersox, Closs, and Stank).
;
Yet, teambuilding and other related team skills do not constitute a major portion of the required skill levels and training curricula in logistics programs. Glaskowsky et al. observe that the use of clearly defined terms can provide time savings, but it has taken marketing, production scholars and executives six decades to organize their terminology in a usable, time-saving, and almost universally understandable form.
Logistics means different things to different people. In the United States, the term is recognized in many areas, but the meaning and definitions vary considerably from organization to organization. In countries outside of the United States, in many instances the term is not known, even though there are many activities that are directly comparable. Further, most countries are not organized to implement the integrated approach to logistics marketing management. In essence, logistics is still a relatively new term and is not generally recognized on a universal basis. However, concepts of logistics and the techniques employed to accomplish logistics functions are equally applicable throughout the world (Glaskowsky et al.)
What are some of the Logistics Characteristics that can identify and define influencing skills? They are legitimization, knowledge, reference groups, competency, and openness in communication. The specific competencies that are required for professionals to influence people are a degree of personal security, situational skill, independence and courage of judgment, ability to abstract and conceptualize, mental flexibility, tolerance for ambiguity, ability to analyze and synthesize, and negotiation skills (Bowersox, Closs, and Stank).
Logistics Management
Logistics can be generalized as time and place utility, and value of resources, especially when in a theorized, or unapplied state. Logistics management, on the other hand, relates logistics to a specific system, product or service. In fact, in the absence of a system, product or service, there is no need for the application of Logistics. Logistics managers integrate areas of system, product or service. These essential building blocks include such items as maintenance planning, computer resources support, facilities, supply support, support and test equipment, packaging, handling, storage and transportation, manpower and personnel, training and training systems, and technical data (Bowersox, Closs, and Stank).
Logistics Management Teams are currently used as the mechanism to control and integrate these elements into a greater whole. Integration is essential between the logistics discipline and the other related disciplines that are essential to ensure a successful system. These disciplines include marketing management, cost - both design to cost and life cycle cost, systems engineering, software engineering, test and evaluation, and manufacturing management (Glaskowsky et al.)
Logistics typically is considered to be an operational-level concern, but is often a production and operations sub-function. In some firms, logistics can be important enough to warrant a level of organization that is comparable to other main functions such as manufacturing and marketing. Many strategists seek to identify, develop and guard their firms' core or distinctive competence, that key skill that accounts for the most (and/or most defensible) value found in end products and services (Bowersox, Closs, and Stank).
In identifying best practices among organizations, the benchmarking technique is frequently used. In benchmarking with others, an organization (a) determines how leading organizations perform a specific process, (b) compares their methods to its own, and (c) uses the information to improve upon or completely changes its process(es). Benchmarking is typically an internal process; performed by personnel within an organization who already have a thorough knowledge of the process under review (Glaskowsky et al.)
With the definition of management in mind one can discuss the antecedents and consequences of operational and behavior theory and their relationship in support of the proposition that Logisticians are professional. At the turn of the 20th Century Frederich Winslow Taylor's Principle of Scientific Management held that the task was designed so management was done correctly and motivation was, soldiering. This concept was the way to organize work (Glaskowsky et al.).
Concurrent engineering is the term most U.S. Companies now use as the best practice to accomplish the needed interdisciplinary system integration. A full-time multidisciplinary permanent task force that remains in force throughout the duration of the project, and integrated for the specific timeframe of the systems life cycle should handle each new project. These are conceptual (also known as feasibility, definition, or need) phase, design and development phase, test and evaluation phase, manufacturing/production/construction phase, use (also known as deployment, operations and support) phase, and disposal/recycling phase. An examination of each of these phases in the systems Life cycle reveals that logistics effort and tasks are an integral part of each phase in the systems life cycle as marketing should be. Product definition throughout the systems life cycle remains the unifying theme and area of common interest among all participants. (Hurley et al.)
Integrated systems management can be applied to all the products, systems and services within a geographic boundary, such as a nation. President Clinton, in the 1994 National Security Strategy, defines our national security as consisting of our military capability and an integrated economic capability. In its Joint Military Logistics Course the Industrial College of the Armed Forces identifies joint strategic level logistics as the application of national resources and our national industrial base to the achievement of national economic strategy (Bowersox, Closs, and Stank).
Jones, in his Integrated Logistics Support Handbook, captures the essence of applied logistics by dividing it into two phases. "Phase I, referred to as Acquisition Logistics or Logistics Engineering, and includes everything that is done to plan and acquire support before a system is delivered to the user. Phase 2, referred to as Tactical/Operational Logistics or Product Support includes the things that are done to support the system while it is being used. He notes actions that occur during phase 1 dictate how well the system will be supported during phase 2." (Jones 324)
Commercial customers are more prone to replace their systems; and commercial manufacturers are more prone to facilitate system replacement. The market manager uses terms such as new and improved product, the newest and latest model, and the all-new model, commercial terms that belie this phenomenon. Longevity, however, still remains the bellwether of a good design. The goal of acquisition logistics management and engineering is the concurrent fielding, and delivery of the product through the achievement of a cost-effective, supportable product and a total system, but this cannot be done in a vacuum - it must work with the other related disciplines that contribute to the total system characteristics such as performance, manufacturability, testability, safety, marketing and cost.
Ben Blanchard addresses "product support in the commercial sector to include such activities as material flow, product distribution, transportation, warehousing, and the like (27)." His more general definition is well-suited to defining product support as the composite of all considerations needed to assure the effective economic support of a system throughout its programmed life cycle. Most modern manufacturers and marketing managers of durable goods realize the importance of a responsible product support organization and the cost of a dissatisfied customer. The goal remains excellent performance in service or at least satisfactory use.
Here one can see the idea confirmed that logistics management has to utilize the total integrated system of management for improvement to gain recognition of Logistics as an element of management. Funds and assets are continually being reduced while there is even more pressure to increase profit margins. This intensifies the pressures exerted on the CEO's of companies, government and military leaders. Logistics managers have created a culture in their management approach to gain more flexibility and improve operations. They have to fulfill their responsibilities as stewards of the organizations.
The Role of Logistics in the Organization
While organizations have long considered logistics as an organizational stepchild (Kiessling, Harvey, and Garrison), the logistics function is increasingly playing a strategic role in organizations (Zacharia and Mentzer). In searching for sustainable competitive advantages, today's organizations increasingly focus on developing and improving their logistics capabilities (Bowersox, Closs, and Stank). Leveraging logistics “allows organizations to achieve customer satisfaction through inventory availability, timely delivery, and less product failure” (Mentzer and Williams 33). Integrating logistics into corporate strategy has a greater effect on customer value than any other process (Bowersox, Closs, and Stank).
Based on an extensive review of previous customer service research, Flint and Mentzer suggest that logistics service capabilities can be leveraged to: increase market share, enable mass customization, create effective customer response-based systems that may out perform anticipatory systems, create value through service performance, complement marketing’s design of customer services, positively affect customer satisfaction and, in turn, corporate performance, provide a differentiating competitive advantage, and segment customers. Logistics plays a strategic role in many companies (Mentzer and Williams).
While there are a number of reasons for the growing influence of logistics in business strategy, one of the main reasons for its increased recognition in organizations is because of its role in providing the flow of valued information into and throughout the organization (Flint et al.). Because of its expanding responsibilities of managing business-to-business relationships and as a boundary pner, logistics is increasingly in the position to collect and provide valued information.
The Role of Logistics as a Relationship Manager
Environmental complexity and global competitive pressures have driven organizations to move away from traditional arms-length exchanges toward closer and long-term interorganizational relationships. Organizations are nurturing these collaborative relationships in order to leverage the resources of other supply chain members (Bowersox et al.). For example, recent research suggests that market oriented firms may form collaborative arrangements to gain access to market intelligence (Martin and Grbac).
In terms of forming relationships with downstream supply chain members, relationship marketing has emerged as a top priority, such that loyal customers are seen as assets that must be cultivated and leveraged (Kiessling et al.). This requires a market-oriented focus on anticipating and responding to changes in customer’s desired value (Flint, et al.). It has been argued that customer-contact employees other than the marketing employees (e.g., logistics employees) are at the heart of relationship marketing (Min and Mentzer). Logistics, for example, becomes particularly important to relationship marketing when customers need continuous and periodic delivery of services that are important, variable in quality, and/or complex (Min and Mentzer).
In addition, the formation and maintenance of close, long-term interorganizational relationships with upstream and downstream supply chain members are important in developing and implementing time-based competitive strategies, such as just-in-time (JIT), quick-response (QR), vendor-managed inventory (VMI), continuous replenishment programs (CRP), and collaborative planning forecasting and replenishment (CPFR) (Zacharia and Mentzer). Inherent in these interorganizational collaborative supply chain initiatives is the “inter-penetration” of organizational boundaries (Kiessling et al.). In coordinating these complex processes, several organizational boundaries must be crossed and horizontal connections must be made (Zacharia and Mentzer). The involvement of logistics employees is critical to these supply chain initiatives, because it requires organizations to coordinate the manufacturing and logistics processes with those of their supply chain partners to drive cost reduction and increase understanding of customers in order to enhance effectiveness.
Although relationship marketing and time-based competitive strategies add value, the added value arises from and relies on the organization’s intermingling with entities in its external environment (Kiessling et al.). They rely on individual boundary pners from each organization to regularly interact with one another in determining market, industry, and organization specific fluctuations and requirements, maintaining relationships, and gathering market intelligence (Flint et al.).
In particular, business-to-business relationships require a tremendous amount of participation of boundary pning logistics personnel. Relationships with and knowledge of specific entities often are developed by the same set of individuals. Logistics customer service personnel, because of the relationships they develop with multiple distinct sets of customers, often generate unique insight into customers’ backgrounds, behaviors, and propensities.
The Role of Logistics as a Boundary Spanning Function
One of the essential dilemma’s faced by managers is the maintenance of effective internal operations while maintaining a flow of new ideas for continued improvements (Schwab, Ungson, and Brown). To accomplish this, managers must wade into the ocean of events that surround them, actively try to make sense of those events, and react accordingly (Schwab et al.). Individuals within functions attempt to capture and make sense of events that surround them by interacting with other functions within the organization and events that surround them beyond the walls of the organization.
Similarly, the market orientation behavior of generating market intelligence requires individuals within a function to p the boundaries of both their function and their organization. Although some scholars have conceptualized boundary pning as the interaction between an organization and its external environment (Kiessling, Harvey, and Garrison), boundary pning plays a key role in intraorganizational and interorganizational contexts (Rangarajan et al.).
With “over ninety percent of all logistical work taking place outside the vision of any supervisor” (Bowersox, Closs, and Stank 7), frontline logistics employees and the logistics managers they report to act as boundary pners. Each has the opportunity to facilitate the exchange of intelligence derived from the various markets (customer, supplier, competitor, etc.) and, based on such intelligence, assess customer needs (Kiessling, Harvey, and Garrison). Moorman and Rust suggest that the focus of the customer-service delivery connection, the design and delivery actions involved in providing a firm’s goods and services to the customer, “is generally the frontline employee who is involved in moving products from one firm to another,” i.e., the logisticians (184).
Frontline logistics employees have access to important market knowledge through the customer-service delivery connection. In fact, frontline logisticians, such as the motor carrier operator, may spend more time face-to-face with key customer representatives than any other company employee (Bowersox, Closs, and Stank). A motor carrier operator may learn customer and/or competitor information, for example, as he or she is allowed to freely mingle in typically restricted areas while his or her truck is being unloaded (Kiessling, Harvey, and Garrison).
In the past, contacts between organizations were limited to lower-level sales representatives calling on buyers who emphasized prices, quantities, and deals (Rangarajan et al.). With the blitz of relationship management and time-based competitive strategies, however, logistics analysts, managers, and executives have gained the responsibilities of harmonizing interorganizational systems, sharing logistics and product movement information with suppliers and customers, and joint interorganizational planning for promotional activity and product changes (Rangarajan et al.). Also, while carrying out the purchasing and procurement activities, logistics professionals may learn about a competitor’s supply issues during visits to major suppliers’ facilities and share that intelligence throughout his or her organization to develop a campaign that takes advantage of the competitor’s supply issue.
The logistics boundary pner’s role has extended beyond the traditional transaction type mentality (i.e., truck driver, material handler, purchaser) to relationship development, understanding customer value, and market intelligence collector (Bowersox, Closs, and Stank). As organizations increasingly extend their boundaries globally and, thus, physically distance themselves with customers and suppliers, the logistics boundary pner becomes even more central to identifying and responding to market intelligence. Furthermore, the alleviation of many of the traditional front-line logistics employee responsibilities as a result of automated technology innovations and the removal of many routine managerial activities from advances in information technology has pressed the logistician to evolve “into an innovative, knowledge gatherer” (Kiessling et al. 99).
Logistics Management Strategy
Chow, Heaver, and Henriksson, for example, studied the relationship between strategy, structure, and firm performance as a means of expanding the logistics literature. The improved integration of logistics and key decisions of the firm, including strategy and structure, is important to firm efficiency and continued success. Their general management strategy was operationalized using Porter's typologies. Chow et al., defined logistics strategy "as a pattern of action plans designed for the purpose of achieving logistics goals" (296). In their framework, logistics strategy used the Bowersox, Daugherty et al. typology because it allowed the assessment of "organizational mechanisms rather than only performance objectives" (295). They argued that uncertainty about which organizational structure to select required additional research. They conceptualized structure as including centralization, formalization, and integration. By including integration the authors hoped to be able to expand their research efforts to capture information related to supply chain activities.
Bowersox, Daugherty et al., examined the concept of logistics strategy in their evaluation of leading edge firms. Logistics strategy deals with management objectives regarding the firm's relationships with other firms, which includes daily contact with customers along with channel members and service providers (101). Assessing firm strategy necessitated asking manufacturer, retailer, and wholesaler managers how they would classify their company's logistics strategy. The respondents generally reported that they were concerned with flexibility and responsiveness, which are closely related. Logistics strategy is described using three strategic orientations for the logistics function of a firm — process, market, or channel. Specific definitions are provides in Table 2.1.
In this research, Bowersox, Daugherty et al. found that more of the manufacturing firms responded with a process strategy, than either of the other two. Specifically, 58% selected process, 28% selected market, 9% selected channel, and the remaining 9% opting for "other" (104). More recently, this construct has generated similar results in research conducted by Bowersox, Closs, and Stank. The process strategy garnered 50.0%, market 25.5%, and channel 15.4%, with 9.1% selecting "other."
Table 2.1: Logistics Strategies
Process
A process-based strategy is concerned with managing a broad group of logistics activities as a value added chain. Emphasis is on achieving efficiency from managing purchasing, manufacturing, scheduling, and physical distribution as an integrated system.
Market
A market-based strategy is concerned with managing a limited group of logistics activities for a multi-division single business unit or across multiple business units. The logistics organization seeks to make joint product shipments to common customers for different product groups and seeks to facilitate sales ad logistical coordination by a single order-invoice. Often the senior sales and logistics executives report to the same manager.
Channel
A channel-based strategy is concerned with managing logistics activities performed jointly with dealers and distributors. The strategic orientation places a great deal of attention on external control. Significant amounts of finished inventory are typically maintained forward or downstream in the distribution channel.
Adpted from: Bowersox, Daugherty, Droge, Rogers, and Wardlow 103
After examining the literature, the basic distinction between process, market, and channel logistics strategies is the context of the logistics effort. Process logistics strategy, for example, deals internally within a single organization. It requires logistics managers to work closely with other functional areas within a single firm to ensure logistics efficiencies are achieved. Market strategy, however, requires logistics managers to consider other business units and their logistics activities, to make decisions that benefit the entire corporation. An effort to consolidate shipments across several divisions of a larger organization ensures more efficient transportation, as well as a more unified "face" to the customer. This strategy necessitates balancing both an internal and external focus to be effective. Channel strategy expands the logistics manager's scope and entails coordination with other supply chain members. It requires firms to work closely with suppliers and potentially customers to achieve logistics efficiencies. In general, the Bowersox, Daugherty et al. typology places logistics strategy on a continuum from an internal to external focus.
The process-market-channel typology is not the only logistics strategy classification scheme. McGinnis and Kohn originally developed their own typology for logistics strategy. They cluster analyzed their data and determined that four strategies: intensive logistics strategy, integrated logistics strategy, low integration logistics strategy, and low effectiveness logistics strategy. However, in a later work McGinnis and Kohn abandoned their previous typology and reverted to the process, market, and channel typology.
In their research, McGinnis and Kohn noted that the process-market-channel typology is "worthy of research" and indicated "additional research is needed to develop further the logistics strategy scales, and to explore linkages of logistics strategy with organizational strategy and organizational environment" (20). Clinton and Closs in their article "Logistics Strategy: Does It Exist?" examined Bowersox, Daugherty et al. and McGinnis and Kohn logistics strategy typologies. They concluded that the McGinnis and Kohn strategies were really a subset of the process-market-channel strategies (Clinton and Closs 23) and used the process-market-channel typology. Logistics strategy can be operationalized in many ways, as alluded to above. The process-market-channel typology provides a way to operationalize logistics strategy to evaluate its impact, both internally and externally.
Conclusion
Logistics is becoming increasingly important to firms around the globe. In the past, the logistics function was often viewed as a cost center, i.e., a function that had to be done to carry out business. Today, managers are elevating logistics to a strategic role in the company. Managers realize that improvements in logistics can provide competitive advantage through cost containment and enhanced customer service (Bowersox et al.). An important step in achieving these goals is to examine the importance of information technology on the success of the logistics function.
One of the essential dilemma’s faced by managers is the maintenance of effective internal operations while maintaining a flow of new ideas for continued improvements. The logistics manager must use physical production processes, products, process design, information systems, management technology and product material technologies as interdependent elements in their strategies to enable the three critical management tasks of problem solving, information management, streamlining of the cost factor, scheduling and performance goals.
Bibliography
Blanchard, B.S. Logistics Engineering and Management. 3rd Ed. Englewood: Prentice-Hall, 1986.
Bowersox, Donald J., David J. Closs, and Theodore P. Stank. 21s' Century Logistics: Making Supply Chain Management a Reality. Oak Brook, IL: Council of Logistics Management, 1999.
Bowersox, Donald J., Patricia J. Daugherty, Cornelia L. Droge, Dale S. Rogers, and Daniel L. Wardlow. Leading Edge Logistics: Competitive Positioning for the 1990s. Oak Brook, IL: Council of Logistics Management, 1989.
Chow, Garland, Trevor D. Heaver, and Lennart E. Henriksson "Strategy, Structure, and Performance: A Framework for Logistics Research," Logistics and Transportation Review, 31.4 (1995): 285-308.
Clinton, Steven R. and David J. Closs. "Logistics Strategy: Does It Exist?," Journal of Business Logistics, 18.1 (1997): 19-44.
Hurley, R. F., Church, A.H., Burke, W.W., & Van Eynde, D.F. "Tension, Change and Values in 00," O D Practitioner. 24 (1992)
Flint, Daniel J. and John T. Mentzer. "Logisticians as Marketers: Their Role When Customers' Desired Value Changes," Journal of Business Logistics, 21.2 (2000): 19- 47.
Flint, Daniel J., Everth Larsson, Britta Gammelgaard, and John T. Mentzer, “Logistics Innovation: A Customer Value-Oriented Social Process,” Journal of Business Logistics, 26.2 (2005): 113-147.
Glaskowskey, N., Hudson, D. & Ivie, R. Business Logistics. Fort Worth: The Dryden Press, 1992.
Jones, J. Integrated Logistics Support Handbook. New York: McGraw-Hill, 1978.
Kiessling, Timothy, Michael Harvey, and Garry Garrison. “The Importance of Boundary-Spanners in Global Supply Chains and Logistics Management in the 21st Century,” Journal of Global Marketing, 17.4 (2004): 93 – 112.
Martin, James H. and Bruno Grbac. “Using Supply Chain Management to Leverage a Firm's Market Orientation,” Industrial Marketing Management, 32.1 (2003):25-38.
McGinnis, Michael A. and Jonathan W. Kohn. "Logistics Strategy, Organizational Environment, and Time Competitiveness," Journal of Business Logistics, 14.2 (1993): 1-23.
Mentzer, John T. and Lisa R. Williams. “The Role of Logistics Leverage In Marketing Strategy,” Journal of Marketing Channels, 8 (2001): 29-47.
Min, Soonhong and John T. Mentzer. "The Role of Marketing in Supply Chain Management," International Journal of Physical Distribution and Logistics Management, 30.9 (2000): 765-783.
Moorman, Christine and Roland T. Rust. “The Role of Marketing,” Journal of Marketing, 63.4 (1999): 180-197.
Rangarajan, Deva, Lawrence B. Chonko, Eli Jones, and James A Roberts. “Organizational Variables, Sales Force Perceptions of Readiness for Change, Learning, and Performance Among Boundary-Spanning Teams: A Conceptual Framework and Propositions for Research,” Industrial Marketing Management, 33.4 (2004): 289-205.
Rivers, E. Logistics: A Significant Component Of Strategic Management. SOLEtech 2.10 (Oct 1999): 1-2.
SOLE. The International Society of Logistics <http://www.sole.org>.
Schwab, Robert C., Clerardo R. Ungson, and Warren B. Brown. “Redefining the Boundary Spanning-Environment Relationship,” Journal of Management, 11.1 (1985): 75-86.
Van Mieghw, T. "Lessons Learned from Alexander the Great." Quality Progress (1968): 31-1.
Zacharia, Zach G. and John T. Mentzer. "Logistics Salience in a Changing Environment," Journal of Business Logistics, 25.1 (2004): 187-210.
Cite this Page
Logistics Management Essay. (2018, Aug 26). Retrieved from https://phdessay.com/logistics-management-3/
Run a free check or have your essay done for you
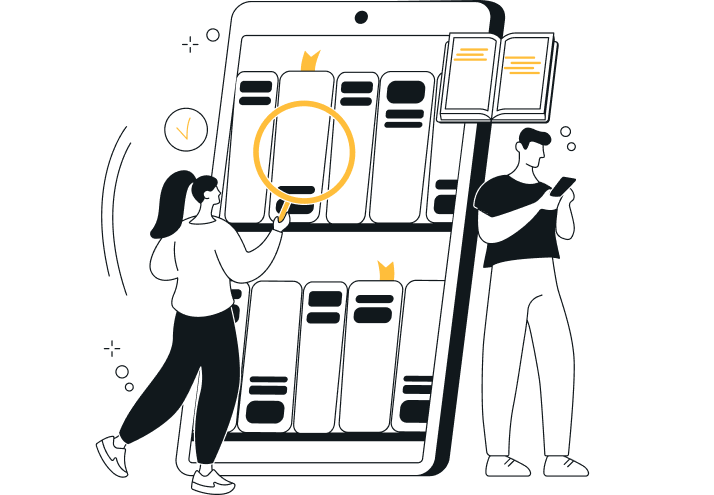