Little Field
After the initial observations of demand for littlefield labs (day 52), one of the first steps we took was to identify the bottleneck in the production chain. This was determined by looking at the rate of utilization of the three machines and the number of jobs in the queue waiting for these machines. It was quickly determined that the machine 1 was our bottleneck, as it was the only machine with 100% utilization and excess number of jobs in the queue. This meant that machine 1 was not able to keep up with the incoming demand and lacked the proper capacity.
We knew that we needed to increase capacity and the decision was made to purchase another machine 1. Following the decision to purchase a machine, our focus shifted to the inventory level and the reorder point. It was obvious that the old reorder point was not going to keep up with the incoming demand level, especially considering the four day lead time. Our initial thinking was to set the reorder point to a level where the inventory would have sufficient level of safety stock to avoid stocking out before the next batch of order came.
Also we needed determine the quantity of inventory to order, making sure to take into account the ordering cost of $1000 as well. One of our initial goal for day 52 was to make sure our system was clear of any bottleneck and to have sufficient level of inventory to last us until day 73. This strategy was in part due to the fact that we did not have much time to analyze and properly forecast the future demand (initially meeting took place at midnight due to the long commute), but also to allow us to have more data about the incoming demand.
Order custom essay Little Field with free plagiarism report
To determine the proper level of order quantity and reorder point, we did a simple forecasting of incoming demand by using a simple linear regression analysis of observed demand for the first 50 days. Using this data we determined that the reorder point must be increased to 45 and the order quantity should be set at 250 kits. When we did meet the following day, our focus was to forecast the demand out to day 120, since we had the knowledge of demand increasing and leveling out after day 120.
Using the excel spreadsheet and looking at the linear regression line, we determined that the approximate level of demand on day 120 would be about 18 kits per day. This number was critical to our overall strategy going forward. Since we knew the demand would average around 18 kits a day, we wanted to have enough capacity in the machines to handle the demand. We figured to calculate the demand capacity of each machines by looking at the level of utilization of each machines on day 1, when the very first order arrived.
Using the percentage of utilization and the actual number of job coming in for the first time, we were able to calculate the capacity of each machine with relative accuracy. It was determined that machine 1 had the capacity of 4. 5 jobs per day, machine 2 with capacity of 12. 5 jobs per day, and machine 3 with capacity of 12jobs per day. This meant that in order for us to accommodate the expected level of demand, we needed to have five units of Machine 1, two units of Machine 2, and two units of Machine 3.
We wanted to have five units of Machine 1 because we did not want to have just 4 and have 100% utilization, causing a bottleneck situation. We also wanted to figure out the optimal reorder point and order quantity using the forecasted average demand of 18 jobs per day. We set the number of reorder point to 95 kits, accounting for the four day lead period and the level of safety stock we wanted to have. Then we determined the order quantity should be set at 500 kits, which would be sufficient level of inventory to last for full day.
Finally, with the changes already made to improve our capacity and production lead time, we set out to maximize our profit margin for each job coming in. We agreed that contract three would be most profitable for us since we predicted out lead time to be cut under half a day, and would not exceed one day with reasonable fluctuation of demand. Also, figuring that we wanted to move out any jobs ready for final processing, we switched the priority of Machine 2 to give priority to step 4.
Cite this Page
Little Field. (2017, Feb 03). Retrieved from https://phdessay.com/little-field/
Run a free check or have your essay done for you
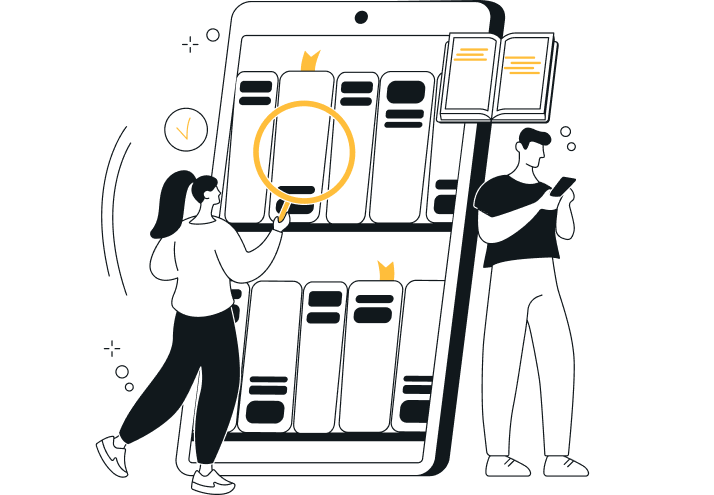