Overview of 3D Printing Technology and Applications
Rapid prototyping 3D printers 3D printing is a form of additive manufacturing technology where a three dimensional object is created by laying down successive layers of material. 3D printers are generally faster, more affordable and easier to use than other additive manufacturing technologies. 3D printers offer product developers the ability to print parts and assemblies made of several materials with different mechanical and physical properties in a single build process. Advanced 3D printing technologies yield models that closely emulate the look, feel and functionality of product prototypes.
A 3D printer works by taking a 3D computer file and using and making a series of cross-sectional slices. Each slice is then printed one on top of the other to create the 3D object. The cost of 3D printers has declined. The technology also finds use in the jewellery, footwear, industrial design, architecture, engineering and construction (AEC), automotive, aerospace, dental and medical industries. A large number of competing technologies are available to do 3D printing. Their main differences are found in the way layers are built to create parts.
Some methods use melting or softening material to produce the layers (SLS, FDM) where others lay liquid materials that are cured with different technologies. In the case of lamination systems, thin layers are cut to shape and joined together. Selective laser sintering (SLS) Selective laser sintering (SLS) is an additive manufacturing technique that uses a high power laser (for example, a carbon dioxide laser) to fuse small particles of plastic, metal (Direct Metal Laser Sintering), ceramic, or glass powders into a mass that has a desired 3-dimensional shape.
Order custom essay Overview of 3D Printing Technology and Applications with free plagiarism report
The laser selectively fuses powdered material by scanning cross-sections generated from a 3-D digital description of the part (for example from a CAD file or scan data) on the surface of a powder bed. After each cross-section is scanned, the powder bed is lowered by one layer thickness, a new layer of material is applied on top, and the process is repeated until the part is completed. Compared to other methods of additive manufacturing, SLS can produce parts from a relatively wide range of commercially available powder materials.
These include polymers such as nylon, (neat, glass-filled or with other fillers) or polystyrene, metals including steel, titanium, alloy mixtures, and composites and green sand. The physical process can be full melting, partial melting, or liquid-phase sintering. And, depending on the material, up to 100% density can be achieved with material properties comparable to those from conventional manufacturing methods. In many cases large numbers of parts can be packed within the powder bed, allowing very high productivity. SLS is performed by machines called SLS systems.
SLS technology is in wide use around the world due to its ability to easily make very complex geometries directly from digital CAD data. While it began as a way to build prototype parts early in the design cycle, it is increasingly being used in limited-run manufacturing to produce end-use parts. One less expected and rapidly growing application of SLS is its use in art. [pic] The picture above is made using SLS and is a very intricate design which would be very difficult to imagine if it was only drawn on paper. Digital Light Processing (DLP)
In DLP, or Digital Light Processing, a vat of liquid polymer is exposed to light from a DLP projector under safelight conditions. The exposed liquid polymer hardens. The build plate then moves down in small increments and the liquid polymer is again exposed to light. The process repeats until the model is built. The liquid polymer is then drained from the vat, leaving the solid model. The ZBuilder Ultrais an example of a DLP rapid prototyping system Laminated object manufacturing (LOM) Laminated object manufacturing (LOM) is a rapid prototyping system developed by Helisys Inc. Cubic Technologies is now the successor organization of Helisys) In it, layers of adhesive-coated paper, plastic, or metal laminates are successively glued together and cut to shape with a knife or laser cutter.
FDM works on an "additive" principle by laying down material in layers. A plastic filament or metal wire is unwound from a coil and supplies material to an extrusion nozzle which can turn on and off the flow. The nozzle is heated to melt the material and can be moved in both horizontal and vertical directions by a numerically controlled mechanism, directly controlled by acomputer-aided manufacturing (CAM) software package. The model or part is produced by extruding small beads of thermoplastic material to form layers as the material hardens immediately after extrusion from the nozzle.
Several materials are available with different trade-offs between strength and temperature properties. As well as acrylonitrile butadiene styrene (ABS) polymer, polycarbonates, polycaprolactone, polyphenylsulfones and waxes, a "water-soluble" material can be used for making temporary supports while manufacturing is in progress, this soluble support material is quickly dissolved with specialized mechanical agitation equipment utilizing a precisely heated sodium hydroxide solution. In the picture above the support material is easy recognised and can be broken away easily.
Cite this Page
Overview of 3D Printing Technology and Applications. (2017, Mar 07). Retrieved from https://phdessay.com/3d-printers/
Run a free check or have your essay done for you
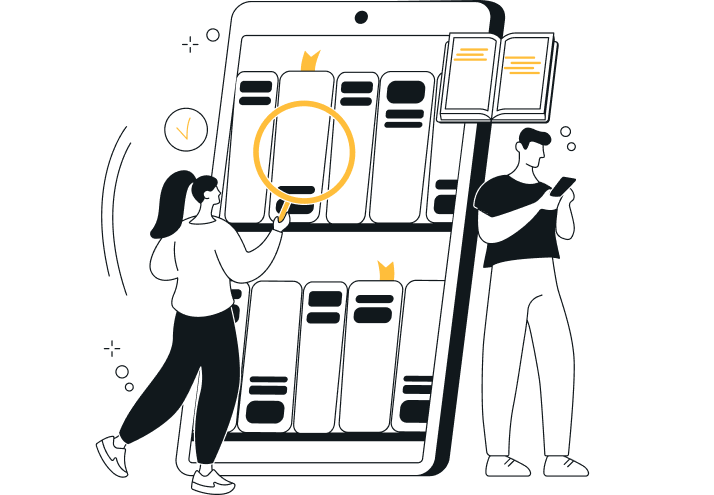