Total Quality Management
Total Quality Management – MGT510 VU Lesson # 01 OVERVIEW OF QUALITY MANAGEMENT PROFESSIONAL MANAGERIAL ERA (1950) In our present age of market driven capitalism and futuristic knowledge driven economic markets, the decision are made and the trends are set by the professional managers. Unlike their predecessors, the captains of today’s business do not own their own companies. They must know the whole business but have control over only one small part. They must be product oriented, process conscious, financially responsible, and public spirited. They must be all things to all people, yet still function as only one cog in the wheel.
If the history of management tells us anything, it is that, no matter what happens; peace or war, prosperity or famine, this world will always be in need of good managers . . . the kind who can get society from “where it is” to “where it wants to be. ” Can you be one? What is an Organization? “An entity where two or more persons work together to achieve a goal or a common purpose is called Organization. ” There are so many organizations around us. Daily we visit and see many organizations. Hospitals, Colleges, Factories, Farms and Government offices. Mosque/Church is also an example of an organization.
People go there and say prayers. Activities of praying are to achieve a certain goal. Similarly, any unit in which two or more persons are working together for some purpose is called an organization. Unit of Organization: • People • Purpose • Process • POLCA If there is an organization, then there must be some people. They work as whole for a common purpose, so there must be a defined purpose. If an organization doesn’t have any purpose, it will not survive for long run. To achieve the purposes by using people, the processes are needed. Without any process, you cannot achieve any type of purpose or goal.
Order custom essay Total Quality Management with free plagiarism report
If we see in our daily life, we have some goals. For achieving these goals, we use some processes. So that process is also obvious and important for an organization. The last important thing for any organization is that it requires main pillars of management i. e. POLCA: • • • • Planning Organizing Leading Controlling A manager must perform all theses management functions with Assurance! Quality Focus Approach to Management “There are really only three types of people: those who make things happen, those who watch things happen, and those who say, ‘What happened? ” Copyright Virtual University of Pakistan 1 Total Quality Management – MGT510 VU The total quality concept as an approach to doing business began to gain wide acceptance in the west in the late 1980s and early 1990s. However, individual elements of the concept – such as the use of statistical data, teamwork, continual improvement, customer satisfaction, and employee involvement – have been used by visionary organizations for years. It is the pulling together and coordinated use of these and other previously disparate elements that gave birth to the comprehensive concept known as total quality.
Why Focus on Quality? To understand total quality, one must first understand quality. Customers of businesses will define quality very clearly using specifications, standards, and other measures. This makes the point that quality can be defined and measured. Although few consumers could define quality if asked, all know it when they see it. This makes the critical point that quality is in the eye of the beholder. With the total quality approach, customers ultimately define quality. People deal with the issue of quality continually in their daily lives.
We concern ourselves with quality when grocery shopping, eating in a restaurant, and making a major purchase such as an automobile, a home, a television, or a personal computer. Perceived quality is a major factor by which people make distinctions in the market place. Whether we articulate them openly or keep them in the back of our minds. We all apply a number of criteria when making a purchase. The extent to which a purchase meets these criteria determines its quality in our eyes. One way to understand quality as a consumer-driven concept is to consider the example of eating at a restaurant.
How will you judge the quality of the restaurant? Most people apply such criteria as the following: ¦ ¦ ¦ ¦ ¦ ¦ Service Response time Food preparation Environment/atmosphere Price Selection The example gets at one aspect of quality the results aspect. Does the product or service meet or exceed customer expectations? This is a critical aspect of quality, but it is not the only one. Total quality is a much broader concept that encompasses not just the results aspect but also the quality f people and the quality of processes. How Is Total Quality Different?
What distinguishes the total quality approach from traditional ways of doing business can be found in how it is achieved. The distinctive characteristics of total quality are these: customer focus (internal and external), obsession with quality, use of the scientific approach indecision making and problem solving, long-term commitment, teamwork, employee involvement and empowerment, continual process improvement, bottom-up education and training, freedom through control, and unity of purpose, all deliberately aimed at supporting the organizational strategy.
Each of these characteristics is explained later in this chapter. The Historic Development of Total Quality The total quality movement had its roots in the time and motion studies conducted by Frederick Taylor in the 1920s. Taylor is now known as “the father of scientific management. ” ©Copyright Virtual University of Pakistan 2 Total Quality Management – MGT510 VU The most fundamental aspect of scientific management was the separation of planning and execution.
Although the division of labor spawned tremendous leaps forward in productivity, it virtually eliminated the old concept of craftsmanship in which one highly skilled individual performed all the tasks required to produce a quality product. In a sense, a craftsman was CEO, production worker, and quality controller all rolled into one person. Taylor’s scientific management did away with this by making planning the job of management and production the job f labor. To keep quality from falling through the cracks, it was necessary to create a separate quality department.
Such departments had shaky beginnings, and just who was responsible for quality became a clouded issue. As the volume and complexity of manufacturing grew, quality became an increasingly difficult issue. Volume and complexity together gave birth to quality engineering in the 1920s and reliability engineering in the 1950s. Quality engineering, in turn, resulted in the use of statistical methods in the control of quality, which eventually led to the concepts of control charts and statistical process control, which are now fundamental aspects of the total quality approach. Copyright Virtual University of Pakistan 3 Total Quality Management – MGT510 VU Lesson # 02 TOTAL QUALITY MANAGEMENT AND TOTAL ORGANIZATION EXCELLENCE TRADITIONAL MANAGEMENT AND QUALITY MANAGEMENT: Twentieth-century management has been strongly influenced by Taylor’s scientific management and Weber’s theory of bureaucracy. These approaches have led managers to work within functional hierarchies, with their responsibilities divided according to specialized activities, such as accounting, marketing, engineering, and manufacturing.
Economic principles for competing in well-defined markets emphasized economies of scale, efficiencies, mass production, and technological innovation. While there had been competition, competitors often played according to a “live and let live” strategy. Because monopolies were precluded by law, companies had little incentive to completely drive competitors from the marketplace. Even when new product technologies created new markets, such as plastics in the 1950s, management practices changed very little.
Managers set goals for productivity, efficiency, and profitability, using management set goals for productivity, efficiency, and profitability, using management by objectives (MBO) to link strategy and operations through the hierarchy. Managers motivated employees to fulfill those goals by inducements such as profit sharing, stock options, and bonuses, or other rewards such as job enrichment or participative management. However, the job of management remained much the same: set goals, define roles, provide technologies, and motivate employees.
Accounting, marketing, engineering, and manufacturing practices also did not change. Occasionally, new techniques were introduced within the traditional functions, such as quality control in manufacturing. But such changes went largely unnoticed by the rest of the organization. No one challenged this approach to management as long as it served society well. While managers in Japan were rewriting the rules of business practice and management and planning to win the world markets by focusing on quality management, U. S. managers continued in the stage of normality.
The US, and western society in general, was focused on another agenda: the cold war in the 1950s and 1960s. The Stage of Replacement: A New Paradigm The stage of replacement means shifting to a new paradigm. Managers must shift to a new paradigm for managing organizations because of the anomalies that threaten their survival and prosperity. To make this shift, however, they must understand the new paradigm and how it differs from the old paradigm. To initiate this understanding, we will contrast the new (but still emerging) paradigm with the old paradigm.
Themes of the New Paradigm The differences between the new and the old paradigm are organized around three themes: customer value strategy, cross-functional systems, and continuous improvement. Theme 1: Customer Value Strategy Customer value is defined as the combination of benefits derived from using a product ( or service) and the sacrifices required of the customer. The customer value strategy is the business plan for offering value to customers, including product characteristics, attributes, mode of delivery, support services, and so on.
The theme of customer value strategy may be addressed in many topics, including quality, measurement, positioning, key stakeholder, and product design. ©Copyright Virtual University of Pakistan 4 Total Quality Management – MGT510 VU Topics Quality Measurement Positioning Key stakeholder Product design Quality Old Paradigm New (emerging) paradigm Meeting specifications, inspected into One component of customer value, product, make tradeoffs among quality, managed into process, seek cost, schedule synergies among quality, cost, schedule.
Internal measures of efficiency, All measures linked to customer productivity, costs, and profitability, not value necessarily linked to customers Competition Customer segments Stockholder, boss Customer segments Customer (other stakeholders are beneficiaries) Internal, sell what we can build External, build what customers need In the old paradigm, managers define quality in terms of meeting specifications. Quality is assured by weeding out the “bad” products before they are shipped to customers. Managers make tradeoffs among quality, cost, and scheduling under the assumption that relationships among these outcomes are fixed.
By contrast, in the new paradigm, managers recognize that product quality is only one component of customer value, and managers seek synergies among quality, cost, and schedule, not just tradeoffs. For example, improving quality by reducing variation in outputs reduces defects, reduces costs, and makes performance to schedule more predictable. Further, quality is more broadly defined than just product quality. Quality applies to every aspect of the organization. It must be managed into processes and systems, and not jut inspected into products.
System thinking included to think of all interdependent parts of the system into one whole. Measurement In the old paradigm, measurement systems are focused on internal measures of efficiency, productivity, costs, and profitability. This is the tradition of management by objectives. Managers do not necessarily understand how these internally focused measures are related to customer value. In the new paradigm, managers may use internally focused measures, but they are linked to customer value in a broader measurement system. Managers interpret measures in terms of the impact on customer value in the long term and short term.
Positioning In the old paradigm, managers make strategic positioning decisions based primarily on warfare models on the competition. In the new paradigm, managers make strategic positioning decisions with a focus on market segmentation and customer needs, wants and demands. Key Stakeholder In the old paradigm, the key external stakeholder is the stockholder, and the key internal stakeholder is one’s boss. All other stakeholders, such as customers, employees, suppliers, and business partners, are pawns to serve the goals of the key stakeholders.
In the new paradigm, the key stakeholders are customers, both internal and external customers. Providing value to customers is the key to serving all other stakeholders over the long term. Product Design In the old paradigm, the product design process is internally driven, based on the assumption that “we know what is bet for the customer. ” Managers enact a “push” strategy that aims to “sell what we can build. ” In the new paradigm, managers develop products after first determining what customers need. ©Copyright Virtual University of Pakistan 5 Total Quality Management – MGT510 VU
Managers both react to improve products in existing markets and actively seek to create new markets with new products. Theme 2: Organizational Systems Organizational systems are the means that provide customer value. These systems broadly include material and human inputs, process technology, operating methods and work practices, streams of work activity, information flows, and decision making. The approaches to managing these systems in the old and new paradigms are discussed below. Topics Cross-functional approach Technology Employee involvement Human resource management Role definition
Culture Old Paradigm Negotiation across functional interfaces to obtain cooperation To deal with complexity, to eliminate people problems Focused on hygiene factors Regarded as a staff responsibility, administration of personnel hiring, firing, handling complaints Task and job descriptions set limits Social and emotional issues are suppressed, politics and power dominate Specialization, tall hierarchy with functional emphasis New (emerging) paradigm Cross-functional systems defined, owned, and optimized To reduce complexity, source of optimization for customer value Focused on strategic factors Regarded as a critical resource, managed as system input Vision inspires flexibility Connect with individual sense of purpose, emotions, and social meaning Integration, flat hierarchy with team emphasis Structure Cross-Functional Approach The old paradigm does not acknowledge systems that cut across functional or unit boundaries.
Managers simply negotiate across functional interfaces to obtain minimal cooperation. In the new paradigm, managers define, own, and optimize cross-functional systems for customer value. Technology In the old paradigm, managers use technology to help them deal with the overly complex systems that have grown up in the organization. Also, they use technology to eliminate people problems (robots don’t talk back). In the new paradigm, managers prefer to eliminate complexity rather than automate it or computerize it. Managers use technology only to optimize systems for customer value. Employee Involvement In the old paradigm, employee involvement programs are implemented without a focus to contribute to systems.
Employee involvement in improvement programs tends to focus on quality of work life issues and some limited operational changes. In the new paradigm, employee involvement is strategically focused and contributes to system purposes. Human Resource Management In the old paradigm, managers regard human resource management (HRM) as a staff responsibility. HR specialists process paperwork to hire and fire, and handle personnel complaints. In the new paradigm, line managers regard human resources as critical resources and strategically manage them as inputs to systems. ©Copyright Virtual University of Pakistan 6 Total Quality Management – MGT510 VU
Role Definition In the old paradigm, managers use task and job descriptions to prescribe and set limits to personal responsibilities. In the new paradigm, managers convey a vision to lead and inspire flexibility. Employees participate in any activities required to provide superior value to customers. Culture In the old paradigm, managers suppress social and emotional issues that are regarded as irrational and sources of distraction away from goals and objectives. Power and politics dominate the culture, with individuals jockeying for personal gain. In the new paradigm, managers connect organizational mission and purpose with each individual’s sense of purpose, emotions, and social meaning.
Individuals channel their needs for pride in workmanship toward strategic purposes. Structure In the old paradigm, organizational structure is based on specialization of tasks. The hierarchy is tall, with many levels of managers, and it emphasizes functional lines of authority. In the new paradigm, the hierarchy is flat, with fewer levels of managers, and it emphasizes teamwork to serve super ordinate objectives. Theme 3: Continuous Improvement To keep pace with the changes in the external environment, managers have to change the organization. Managers have always made improvements. However, with rates of change increasing in the external environment, managers must improve differently and more frequently than in the past.
They must pursue continuous improvement, which is a constant striving to change and make things better. Topics Occasion Old Paradigm Focused new product development, episodic, reactive to problems, big breakthroughs only Trial and error Punish, fear, cover-up, seek people fix, employees are responsible Individual political expediency, short term Administer and maintain status quo, control other Top-driven via rules and policies Business results through quotas and targets Scoring, reporting evaluating Delegated by managers to staff and subordinates New (emerging paradigm Focused on broader systems, unending, proactive to opportunities, big breakthroughs and small teps Scientific method Learning, openness, seek process/system fix, management is responsible Strategic, long-term, purposeful for organization Challenge status quo, prompt strategic improvement Customer-driven through vision, enablement, and empowerment Business results through capable systems, means tied to results Statistical study of variation to understand causes Owned by managers who lead staff and subordinates Approach Response to error Decision-making perspective Managerial roles Authority Focus Control Means Occasion In the old paradigm, the occasions for improvement were primarily new product development and reaction to salient problems. Mangers mostly looked for big breakthroughs to get improvement. In the new paradigm, the occasions for improvement are everywhere, every day. Managers improve ©Copyright Virtual University of Pakistan 7 Total Quality Management – MGT510 VU roactively at every opportunity, even in the absence of salient problems. Managers improve all aspects of the organization’s systems through both big breakthroughs and small steps. Approach In the old paradigm, managers accomplish improvements through trial and error. In the new paradigm, managers use the scientific method to study proposed changes and their effects. Response to Error In the old paradigm, if they care at all, managers are intolerant of error. They regard error as a personal failure, and they respond with punishment to instill fear in those blamed. The result is fear and cover-up in the future. In the new paradigm, error is not desired; however, managers view error as an opportunity for learning.
People openly acknowledge error because managers do not assign personal blame, but seek to fix a process or system. Decision-Making Perspective In the old paradigm, managers make decisions that are politically expedient or that serve short-term personal objectives. In the new paradigm, managers make decisions that serve long-term strategic purposes. Managerial Roles In the old paradigm, managers primarily administer existing systems and maintain the status quo. In the new paradigm, managers challenge the status quo for strategic improvement to meet future demands. At the same time, they consistently execute existing systems to meet current demands.
Authority In the old paradigm, managers impose authority from the top down via rules and policies. In the new paradigm, top managers still hold authority but they impose it by communicating a vision, enabling people wit systems, and empowering them to make the vision real. Focus In the old paradigm, managers focus on improving business results through the imposition of quotas and targets. They delegate responsibility, often without giving real authority to change broader systems that constrain results. In the new paradigm, managers focus on improving business results through improving the capabilities of systems. They focus on the means as well as the results, because they have retained responsibility for improving systems.
Control In the old paradigm, managers control the organization through scoring individual performance, reviewing regular reports, and evaluating performance as either good or bad. In the new paradigm, managers statistically study variation to understand the causes of poor performance and make changes in systems to improve performance. Means In the old paradigm, managers delegate the means of improvement to staff and subordinates who must figure out how t meet established targets. In the new paradigm, managers assume responsibility for the means of improvement. They lead improvement by staff and subordinates. ©Copyright Virtual University of Pakistan 8 Total Quality Management – MGT510 VU
The Relationship between Quality and Competitiveness At each successive level of competition the quality of the competitors increased. A similar phenomenon happens to businesses in the marketplace. Companies that used to compete only on a local, regional, or national level now find themselves competing against companies from throughout the world. Some of these companies find the competition to be more intense than any they have ever encountered. Only those who are able to produce world-class quality can compete at this level. In practical terms, it is extremely important for a country’s businesses to be able to compete globally. When they can’t, jobs are lost and the quality of life in that country declines correspondingly. ©Copyright Virtual University of Pakistan 9
Total Quality Management – MGT510 VU Lesson # 03 INTEGRATING PEOPLE AND PERFORMANCE THROUGH QUALITY MANAGEMENT VIEWS ON QUALITY The total quality philosophy introduced a whole new way of looking at performance of a company through people and managing the quality of products and processes. The traditional view of quality measured process performance in defective parts per hundred produced. With total quality the same measurement is thought of I parts per million. The traditional view focused on after-the-fact inspections of products. With total quality the emphasis is on continuous improvement of products, processes, and people in order to prevent problems before they occur.
The traditional view of quality saw employees as passive workers who followed orders given by supervisors and managers. It was their labor, not their brains that was wanted. With total quality, employees are empowered to think and make recommendations for continual improvement. They are also shown the control boundaries within which they must work and are given freedom to make decisions within those boundaries. The traditional view of quality expected one improvement per year per employee. Total quality organizations expect to make at least 10 or more improvements per employee per year. Organizations that think traditionally focus on short-term profits. The total quality approach focuses on long-term profits and continual improvement.
The following statements summarize some of the major differences between the traditional view of quality and the total quality perspective: ¦ Productivity versus quality. The traditional view is that productivity and quality are always in conflict. You cannot have both. The total quality view is that lasting productivity gains are made only as a result of quality improvement. ¦ How quality is defined. The traditional view is that quality is defined solely as meeting customer specifications. The total quality view is that quality means satisfying customer needs and exceeding customer expectations. ¦ How quality is measured. The traditional view is that quality is measured by establishing an acceptable level of nonconformance and measuring against that benchmark.
The total quality view is that quality is measured by establishing high-performance benchmarks for customer satisfaction and then continually improving performance. ¦ How quality is achieved. The traditional view is that quality is inspected into the product. The total quality view is that quality is determined by product design and achieved by effective control techniques. ¦ Attitude toward defects. The traditional view is that defects are an expected part of producing a product. Measuring defects per hundred is an acceptable standard. The total quality view is that defects are to be prevented using effective control systems and should be measured in defects per million (Six Sigma) ¦ Quality as a function.
The traditional view is that quality is a separate function. The total quality view is that quality should be fully integrated throughout the organization – it should be everybody’s responsibility. ¦ Responsibility for quality. The traditional view is that employees are blamed for quality. The total quality view is that 80 percent of quality problems are management’s fault. ¦ Supplier relationships. The traditional view is that supplier relationships are short term and cost driven. The total quality view is that supplier relationships are long term and quality oriented. ©Copyright Virtual University of Pakistan 10 Total Quality Management – MGT510 VU
Lesson #04 FUNDAMENTALS OF TOTAL QUALITY AND RATERS VIEW Total quality–a comprehensive, organization-wide effort to improve the quality of products and service–applies not only to large manufacturers, but to small companies alike. All organization–large and small, manufacturing and service, profit and not-for-profit-can benefit from applying the principles of total quality. During the 1990s, health care, government, and education began to pay increased attention to quality. As more public and government attention focuses on the nation’s health care system, its providers turn toward quality as a means of achieving better performance and lower costs. One hospital, for example, lowered its rate of post-surgical infections to less than one-fifth of the acceptable national norms through the use of quality tools.
Although quality initiatives focused initially on reducing defects and errors in products and services through the use of measurement, statistics, and other problem-solving tools, organizations began to recognize that lasting improvement could not be accomplished without significant attention to the quality of the management practices used on a daily basis. Managers began to realize that the approaches they use to listen to customers and develop long-term relationships, develop strategy, measure performance and analyze data, reward and train employees, design and deliver products and services, and act as leaders in their organizations are the true enablers of quality, customer satisfaction, and business results.
In other words, they recognized that the “quality of management” is as important as the “management of quality. ” As organizations began to integrate quality principles into their management systems, the notion of total quality management, or TQM, became popular. Quality took on a new meaning of organization-wide performance excellence rather than an engineering-based technical discipline. As quality principles have matured in organizations, attention to quality as “something new” has faded, and the term “total quality management (TQM),” which was popular throughout the 1980s and early 1990s has all but fallen out of the business vernacular. Critics suggested that “TQM is as dead as a pet rock” (Business Week, June 23, 1997, p. 47).
Perhaps it is unfortunate that a three-letter acronym was chosen to represent such as powerful management concept. It is equally unfortunate that people point to the demise of faddish terminology as a generalization of the concepts themselves. Reasons for failure of quality initiatives are rooted in organizational approaches and systems. As the editor of Quality Digest put it: “No, TQM isn’t dead. TQM failures just prove that bad management is still alive and kicking. ” The most successful organizations have found that the fundamental principles of total quality are essential to effective management practice, and continue to represent a sound approach for achieving business success.
The real challenge today is to ensure that managers do not lose sight of the basic principles on which quality management and performance excellence are based. The global marketplace and domestic and international competition has made organizations around the world realize that their survival depends on high quality. Many countries, such as Korea and China, are mounting national efforts to increase quality awareness, including conferences, seminars, radio shows, school essay contests, and pamphlet distribution. Spain and Brazil are encouraging the publication of quality books in their native language to make them more accessible. These trends will only increase the level of competition in the future.
Even the tools used to achieve quality a decade ago are no longer sufficient to achieve the performance levels necessary to compete in today’s world. Many organizations are embracing highly sophisticated, statistically based tools as part of popular “Six Sigma” initiatives. These require increased levels of training and education for managers and frontline employees alike, as well as the development of technical staff. As Tom Engibous, president and chief executive officer of Texas Instruments commented on the present and future importance of quality in 1997: Quality will have to be everywhere, integrated into all aspects of a winning organization. ©Copyright Virtual University of Pakistan 11 Total Quality Management – MGT510 VU
The Concept of Quality People define quality in many ways. Some think of quality as superiority or excellence, others view it as a lack of manufacturing or service defects, still others think of quality as related to product features or price. Followings are some of many ways to look at quality. 1. 2. 3. 4. 5. 6. 7. 8. 9. perfection consistency eliminating waste speed of delivery compliance with policies and procedures providing a good, usable product doing it right the first time delighting or pleasing customers total customers service and satisfaction6 Today most managers agree that the main reason to pursue quality is to satisfy customers.
The American National Standards Institute (ANSI) and the American Society for Quality (ASQ) define quality as "“the totality of features and characteristics of a product or service that bears on its ability to satisfy given needs. ” The view of quality as the satisfaction of customer needs is often called fitness for use. In highly competitive markets, merely satisfying customer needs will not achieve success. To beat the competition, organizations often must exceed customer expectations. Thus, one of the most popular definitions of quality is meeting or exceeding customer expectations. Quality in Manufacturing Well-developed quality systems have existed in manufacturing for some time. However, these systems focused primarily on technical issues such as equipment reliability, inspections, defect measurement, and process control.
The transition to a customer-driven organization has caused fundamental changes in manufacturing practices, changes that are particularly evident in areas such as product design, human resource management, and supplier relations. Product design activities, for example, now closely integrate marketing, engineering, and manufacturing operations. Human resource practices concentrate on empowering workers to collect and analyze data, make critical operations decisions, and take responsibility for continuous improvements, thereby moving the responsibility for quality from the quality control department onto the factory floor. Suppliers have become partners in product design and manufacturing efforts. Many of these efforts were stimulated by the automobile industry, which forced their network of suppliers to improve quality.
Manufactured products have several quality dimensions including the following: 1. 2. 3. 4. 5. 6. 7. 8. Performance: a product’s primary operating characteristics. Feature: the “bells and whistles” of a product. Reliability: the probability of a product’s surviving over a specified period of time under stated conditions of use. Conformance: the degree to which physical and performance characteristics of a product match pre-established standards. Durability: the amount of use one gets from a product before it physically deteriorates or until replacement is preferable. Serviceability: the ability to repair a product quickly and easily. Aesthetics: how a product looks, feels, sounds, tastes, or smells.
Perceived quality: subjective assessment resulting from image, advertising, or brand names. Most of these dimensions revolve around the design of the product. ©Copyright Virtual University of Pakistan 12 Total Quality Management – MGT510 VU Quality control in manufacturing is usually based on conformance, specifically conformance to specifications. Specifications are targets and tolerances determined by designers of products and services. Targets are the ideal values for which production strives; tolerances are acceptable deviations from these ideal values. For example, a computer chip manufacturer might specify that the distance between pins on a computer chip should be 0. 95 + 0. 005 inches. The value 0. 090 and 0. 100 would be acceptable. Quality in Services Service can be defined as “any primary or complementary activity that does not directly produce a physical product–that is, the non goods part of the transaction between buyer (customer) and seller (provider). ” A service might be as simple as handling a complaint or as complex as approving a home mortgage. Service organizations include hotels; health, legal, engineering, and other professional services; educational institutions; financial services; retailers; transportation; and public utilities. Today services account for nearly 80 percent of the U. S. Singapore and Sweden workforce. The importance of quality in services cannot be underestimated, as statistics from a variety of studies reveals: • • • • The average company never hears from more than 90 percent of its unhappy customers. For every complaint it receives, the company has at least 25 customers with problems, about one-fourth of which are serious. Of the customers who make a complaint, more than half will do business again with that organization is their complaint is resolved. If the customer feels that the complaint was resolved quickly, this figure jumps to about 95 percent. The average customer who has had a problem will tell nine or ten others about it.
Customers who have had complaints resolved satisfactorily will only tell about five others. It costs six times more to get a new customer than to keep a current customer. So why do many companies treat customers as commodities? In Japan the notion of customer is equated with “honored guest. ” Service clearly should be at the forefront of a firm’s priorities. The service sector began to recognize the importance of quality several years after manufacturing had done so. This can be attributed to the fact that service industries had not confronted the same aggressive foreign competition that faced manufacturing. Another factor is the high turnover rate in service industry jobs, which typically pay less than manufacturing jobs.
Constantly changing personnel makes establishing a culture for continuous improvement more difficult. The production of services differs from manufacturing in many ways, and these differences have important implications for managing quality. The most critical differences are: 1. 2. Customer needs and performance standards are often difficult to identify and measure, primarily because the customers define what they are, and each customer is different. The production of services typically requires a higher degree of customization than does manufacturing. Doctors, lawyers, insurance salespeople, and food-service employees must tailor their services to individual customers. In manufacturing, the goal is uniformity.
The output of many service systems is intangible, whereas manufacturing produces tangible, visible products. Manufacturing quality can be assessed against firm design specifications, but service quality can only be assessed against customers’ subjective, nebulous expectations and past experiences. Manufactured goods can be recalled or replaced by the manufacturer, but poor service can only be followed up by apologies and reparations. Services are produced and consumed simultaneously, whereas manufactured goods are produced prior to consumption. In addition, many services must be performed at the ©Copyright Virtual University of Pakistan 13 3. 4. Total Quality Management – MGT510 VU 5. 6. 7. convenience of the customer.
Therefore, services cannot be stored, inventoried, or inspected prior to delivery as manufactured goods are. Much more attention must therefore be paid to training and building quality into the service as a means of quality assurance. Customers often are involved in the service process and present while it is being performed, whereas manufacturing is performed away from the customer. For example, customers of a quick-service restaurant pace their own orders, carry their food to the table, and are expected to clear the table when they have finished eating. Services are generally labor intensive, whereas manufacturing is more capital intensive. The quality of human interaction is a vital factor for services that involve human contact.
For example, the quality of hospital care depends heavily on interactions among the patients, nurses, doctors, and other medical staff. Hence, the behavior and morale of service employees is critical in delivering a quality service experience. Many service organizations must handle very large numbers of customer transactions. For example, on a given business day, the National Bank of Pakistan might process more than 5. 5 million transactions for 7. 5 million customer through 1,600 branches and more than 3,500 banking machines, and TCS or Fed Ex might handle more than 1. 5 million shipments across the globe. Such large volumes increase the opportunity for error.
These differences have made it difficult for many service organizations to apply total quality principles. Many service organization have well-developed quality assurance systems. Most of them, however, are based on manufacturing analogies and tend to be more product-oriented than service-oriented. Many of the key dimensions of product quality apply to services. For instance, “on time arrival” for an airline is a measure of service performance; frequent flyer awards and “business class” sections represent features. A typical hotel’s quality assurance systems focus on technical specifications such as properly made-up rooms. However, service organizations have special requirements that manufacturing systems cannot fulfill.
The most important dimensions of service quality include the following; you may remember the most important ones by RATER: • • • • • • • • Reliability: How much reliable is the service provider? Accessibility and convenience: Is the service easy to obtain? Timeliness: Will a service be performed when promised? Completeness: Are all items in the order included? Consistency: Are services delivered in the same fashion for every customer, and every time for the same customer? Tangibility: after the service is over, is there any thing to take home to remind the service experience? Empathy or Courtesy: Do frontline employees greet each customer cheerfully?
Responsiveness: Can service personnel react quickly and resolve unexpected problems? Service organizations must look beyond product orientation and pay significant attention to customer transactions and employee behavior. Several points that service organizations should consider are as follows: • The quality characteristics that a firm should control may not be the obvious ones. Customer perceptions are critical although it may be difficult to define what the customer wants. For example, speed of service is an important quality characteristic, yet perceptions of speed may differ significantly among different service organization and customers.
Marketing and consumer research can play a significant role. Behavior is a quality characteristic. The quality of human interaction is vital in every transaction that involves human contact. For example, banks have found that the friendliness of tellers is a principal factor in retaining depositors. Image is a major factor in shaping customer expectations of a service and in setting standards by which customers evaluate that service. A breakdown in image can be as harmful as a breakdown in ©Copyright Virtual University of Pakistan 14 • • Total Quality Management – MGT510 VU • • delivery of the service itself. Top management is responsible for shaping and guiding the image that the firm projects.
Establishing and measuring service levels may be difficult. Service standards, particularly those relating to human behavior, are often set judgmentally and are hard to measure. In manufacturing, it is easy to quantify output, scrap, and rework. Customer attitudes and employee competence are not as easily measured. Quality control activity may be required at times or in places where supervision and control personnel are not present. Often work must be performed at the convenience of the customer. This calls for more training of employees and self-management. These issues suggest that the approach to managing quality in services differs from that used in manufacturing.
However, manufacturing can be seen as a set of interrelated services, not only between the company and the ultimate consumer, but within the organization. Manufacturing is a customer of product design; assembly is a customer of manufacturing; sales are a customer of packaging and distribution. If quality is meeting and exceeding customer expectations, then manufacturing takes on a new meaning, far beyond product orientation. Total quality provides the umbrella under which everyone in the organization can strive to create customer satisfaction. Quality in ICT Sector Quality in IT and IS was taken seriously only after SW Engineering principles were established.
SWE Institute at CM University developed the CMM levels to indicate the maturity levels of an organization taking care of RATER along with issues of Configuration Management, Verification and Validation issues along with Scalability and Reusability issues. Principles of Total Quality A definition of total quality was endorsed in 1992 by the chairs and CEOs of nine major U. S. corporations in cooperation with deans of business and engineering departments of major universities, and recognized consultants: Total Quality (TQ) is a people-focused management system that aims at continual increase in customer satisfaction at continually lower real cost.
TQ is a total system approach (not a separate area or program) and an integral part of high-level strategy; it works horizontally across functions and departments, involves all employees, top to bottom, and extends backward and forward to include the supply chain and the customer chain. TQ stresses learning and adaptation to continual change as keys to organizational success. The foundation of total quality is philosophical: TQ includes systems, methods, and tools. The systems permit change; the philosophy stays the same. TQ is anchored in values that stress the dignity of the individual and the power of community action. There probably are as many different approaches to TQ as there are businesses.
However, most share some basic elements: (1) customer focus, (2) a process orientation, (3) continuous improvement and learning, (4) empowerment and teamwork, (5) management by fact, and (6) leadership and strategic planning. Customer Focus The customer is the judge of quality. Understanding customer needs, both current and future, and keeping pace with changing markets requires effective strategies for listening to and learning from customers, measuring their satisfaction relative to competitors, and building relationships, Customer needs–particularly differences among key customer groups – must be linked closely to an ©Copyright Virtual University of Pakistan 15 Total Quality Management – MGT510 VU organization’s strategic planning, product design, process improvement, and workforce training activities.
Satisfaction and dissatisfaction information are important because understanding them leads to the right improvements that can create satisfied customers who reward the company with loyalty, repeat business, and positive referrals. Creating satisfied customers includes prompt and effective response and solutions to their needs and desires as well as building and maintaining good relationships. A business can achieve success only by understanding and fulfilling the needs of customers. From a total quality perspective, all strategic decisions a company makes are “customer-driven. ” In other words, the company shows constant sensitivity to emerging customer and market requirements. This requires an awareness of developments in technology and rapid and flexible response to customer and market needs.
Customer-driven firms measure the factors that drive customer satisfaction. A company close to its customer knows what the customer wants, how the customer uses its products, and anticipates the needs that the customer may not even by able to express. It also continually develops new techniques to obtain customer feedback. Customer opinion surveys and focus groups can help companies understand customer requirements and values. Some companies require their sales and marketing executives to meet with random group of key customers on a regular basis. Other companies bring customers and suppliers into internal product design and development meetings.
A firm also must recognize that internal customers–the recipients of any work output, such as the next department in a manufacturing process or the order-picker who receives instructions from an order entry clerk – are as important in assuring quality as are external customers who purchase the product. Failure to meet the needs of internal customers will likely affect external customers. Employees must view themselves as customers of some employees and suppliers to others. Employees who view themselves as both customers of and suppliers to other employees understand how their work links to the final product. After all, the responsibility of any supplier is to understand and meet customer requirements in the most efficient and effective manner possible. Customer focus extends beyond the consumer and internal relationships, however.
Society represents an important customer of business. A world-class company, by definition, is an exemplary corporate citizen. Business ethics, public health and safety measures, concern for the environment, and sharing quality-related information in the company'’ business and geographic communities are required. In addition, company support–within reasonable limits of its resources–of national, industry, trade, and community activities and the sharing of nonproprietary quality-related information demonstrate farreaching benefits. Customers may be of following types: 1. 2. 3. 4. External Customer Internal Customer Investor Customer Social or Society Customer
Process Orientation The traditional way of viewing an organization is by surveying the vertical dimension – by keeping an eye on an organization chart. However, work gets done (or fails to get done) horizontally or crossfunctionally, not hierarchically. A process is a sequence of activities that is intended to achieve some result. According to AT, a process is how work creates value for customers. We typically think of processes in the context of production: the collection of activities and operations involved in transforming inputs-physical facilities, materials, capital, equipment, people, and energy-into outputsproducts and services. Common types of production processes include machining, mixing, assembly, filling orders, or approving loans.
However, nearly every major activity within an organization involves a process that crosses traditional organizational boundaries. For example, an order fulfillment process might involve a salesperson placing the order; a marketing representative entering it on the company’ ©Copyright Virtual University of Pakistan 16 Total Quality Management – MGT510 VU computer system; a credit check by finance; picking, packaging, and shipping by distribution and logistics personnel; invoicing by finance; and installation by field service engineers. A process perspective links all necessary activities together and increases one’s understanding of the entire system, rather than focusing on only a small part.
Many of the greatest opportunities for improving organizational performance lie in the organizational interfaces – those spaces between the boxes on an organization chart. Continuous Improvement and Learning Continuous improvement is part of the management of all systems and processes. Achieving the highest levels of performance requires a well-defined and well-executed approach to continuous improvement and learning. “Continuous improvement” refers to both incremental and “breakthrough” improvement. Improvement and learning need to be embedded in the way an organization operates. This means they should be a regular part of daily work, seek to eliminate problems at their source, and be driven by opportunities to do better as well as by problems that need to be corrected.
Improvements may be of several types: • Enhancing value to the customer through new and improved products and services; • Improving productivity and operational performance through better work processes and reductions in errors, defects, and waste; and • Improving flexibility, responsiveness, and cycle time performance. Management by Fact Organizations needs performance measures for three reasons: • • • To lead the entire organization in a particular direction; that is, to drive strategies and organizational change, To manage the resources needed to travel in this direction by evaluating the effectiveness of action plans, and To operate the processes that make the organization work and continuously improve. 21 Data and information support analysis at all organizational levels.
The types of information and how it is disseminated and aligned with organizational levels are equally vital to success. At the work level, data provide real-time information to identify assignable reasons for variation, determine root causes, and take corrective action as needed. This might require lean communication a channel consisting of bulletins, computerized quality reports, and digital readouts of part dimensions to provide immediate information on what is happening and how things are progressing. At the process level, operational performance data such as yields, cycle times, and productivity measures help manager determine whether they are doing the right job, whether they are using resources effectively, and whether they are improving.
Information at this level generally is aggregated; for example daily or weekly scrap reports, customer complaint data obtained from customer service representatives or monthly sales and cost figures faxed in from field offices. At the organization level, quality and operational performance data from all areas of the firm, along with relevant financial, market, human resources, and supplier data, form the basis for strategic planning and decision making. Such information is highly aggregated and obtained from many different sources throughout the organization. A company should select performance measures and indicator that best represent the factor that lead to improved customer, operational, and financial performance. These typically include • • • •
Customer satisfaction, Product and service performance, Market assessments, Competitive comparisons, ©Copyright Virtual University of Pakistan 17 Total Quality Management – MGT510 VU • • • Supplier performance, Employee performance, and Cost and financial performance. A comprehensive set of measures and indicators tied to customer and company performance requirements provides a clear basis for aligning all activities of the company with its goals. Leadership and Strategic Planning Leadership for quality is the responsibility of top management. Senior leadership must set directions; create a customer orientation, clear quality values, and high expectations that address the needs of all stakeholders; and build them into the way the company operates.
Senior leaders need to commit to the development of the entire workforce and should encourage participation, learning, innovation, and creativity throughout the organization. Reinforcement of the values and expectations requires the substantial personal commitment and involvement of senior management. Through their personal roles in planning, reviewing company quality performance, and recognizing employees for quality achievement, the senior leaders serve as role models, reinforcing the values and encouraging leadership throughout the organization. If commitment to quality is not a priority, any initiative is doomed to failure. Lip service to quality improvement is the kiss of death.
Many companies have a corporate quality council made up of top executives and managers, which sets quality policy and reviews performance goals within the company. Quality should be a major factor in strategic planning and competitive analysis processes. Many of the management principles and practices required in a TQ environment may be contrary to long-standing practice. Top managers, ideally starting with the CEO, must be the organization’s TQ leaders. The CEO should be the focal point providing broad perspectives and vision, encouragement, and recognition. The leader must be determined to establish TQ initiatives and committed to sustain TQ activities through daily actions in order to overcome employees’ inevitable resistance to change.
Unfortunately, many organizations do not have the commitment and leadership of their top managers. This does not mean that these organizations cannot develop a quality focus. Improved quality can be fostered through the strong leadership of middle managers and the involvement of the workforce. In many cases, this is where quality begins. In the long run, however, an organization cannot sustain quality initiatives without strong top management leadership. Achieving quality and market leadership requires a strong future orientation and a willingness to make long-term commitments to key stakeholders-customers, employees, suppliers, stockholders, the public, and the community.
Strategic business planning should be the driver for quality excellence throughout the organization and needs to anticipate many changes, such as customer’s expectations, new business and partnering opportunities, the global and electronic marketplaces, technological developments, new customer segments, evolving regulatory requirements, community / societal expectations, and strategic changes by competitors. Plans, strategies, and resource allocations need to reflect these influences. Improvements do not happen overnight. The success of market penetration by Japanese manufacturers evolved over several decades. ©Copyright Virtual University of Pakistan 18 Total Quality Management – MGT510 VU
Lesson# 05 TOTAL QUALITY MANAGEMENT AND GLOBAL COMPETITIVE ADVANTAGE Bringing TQ to Life at ABC Engineering Company: ABC is a contract manufacturer of precision sheet metal and machined components for telecommunications semi-conductor, and medical equipment industries. Some of the ways it exemplifies the principles of TQ are described below. Customer Focus ABC made a strategic decision to carefully select customers that support its values–particularly a systematic approach to business and performance management, desire for long-term partnerships, and global leadership. Management and Tam Leaders work with each customer to establish current requirements and future needs, and each customer is assigned a three-person Customer Service team that is on call 24 hours a day for day-to-day production issues.
Process Orientation Processes such as prototype development, scheduling, production setup, fabrication, assembly, and delivery have process owners responsible for maintaining the process to customer requirements. A Quality Assurance team member works with manufacturing teams to create process documentation. Continuous Improvement and Learning Teams use a structured approach to evaluate and improve their processes, documenting them, and presenting a status report of improvements to senior leaders and the ABC Steering Committee. Teams benchmark competitors, “best practice” companies, and customers to learn from others. Empowerment and Teamwork Production and delivery processes are designed around cell manufacturing.
Teams are responsible for knowing their customer’s requirements and producing according to those requirements. Teams are empowered to change targets recommended during strategic planning if they believe it will help them achieve higher performance, as well as to schedule work, manage inventory, and design the layout of their work areas. Management by Fact Team analyzes defect data, customer-reported problems, and control charters generated during production to identify problems and opportunities for improvement. Every business goal and project has defined methods for measurement, and senior leaders meet weekly to review company performance and ensure alignment with directions and plans. Leadership and Strategic Planning Senior Executive Leaders. SELs) and the Leadership Committee (LC) set the strategic direction of the company, and communicate and reinforce values and expectations through performance reviews, participation in improvement or strategic projects, regular interactions with customers and team members, and recognition of team member achievements. All this has contributed to an annual average increase in sales growth of 35 percent from 1995 to 2000, and high levels of customer and employee satisfaction, and quality and operational performance. TQM and Strategic Focus ©Copyright Virtual University of Pakistan 19 Total Quality Management – MGT510 VU The nature of TQ differs from common management practices in many respects. 1. Strategic Planning and Management In traditional management, financial and marketing issues such as profitability, return on investments, and market share drive strategic planning. Quality planning activities are delegated to the “quality control” department.
Long-term quality initiatives are viewed as being costly and not contributing to the ultimate performance measure – profit. Quality planning and strategic business planning are indistinguishable in TQ. Quality goals are the cornerstone of the business plan. Measures such as customer satisfaction, defect rates, and process cycle times receive as much attention in the strategic plan as financial and marketing objectives. 2. Changing Relationship with Customers and Supplier In traditional management, quality is defined as adherence to internal specifications and standards. Quality is defined as adherence to internal specifications and standards.
Quality is measured only by the absence of defects. Inspection of people’s work by others is necessary to control defects. In TQ, quality is defined as products and services beyond present needs and expectations of customers. Innovation is required to meet and exceed customers’ needs. Traditional management places customers outside of the enterprise and within the domain of marketing and sales. TQ views everyone inside the enterprise as a customer of an internal or external supplier, and a supplier of an external or internal customer. Marketing concepts and tools can be used to assess internal customer needs and to communicate internal supplier capabilities. 3.
Organizational Structure Traditional management views an enterprise as a collection of separate, highly specialized individual performers and units, loosely linked by a functional hierarchy. Lateral connections are made by intermediaries cl
Cite this Page
Total Quality Management. (2017, Jan 08). Retrieved from https://phdessay.com/total-quality-management-88375/
Run a free check or have your essay done for you
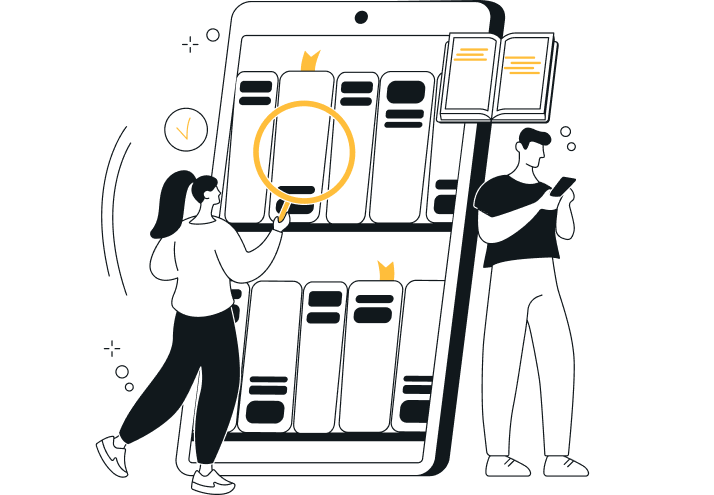