Scheduling, loading and sequencing
Scheduling pertains to establishing timing and use of resources (equipment and facilities, human activities and a receipt of materials) within an organization. Loading involves assigning jobs to work centers or machines in the work centers while sequencing is concerned with determining the order in which jobs will be processed. (Sawit, 2005) The process of assigning jobs to work centers or out sources is referred to as loading, sequencing, dispatching or scheduling. Scheduling is a method of determining the quantity and timing of production over a specified period of time.
It does not lower cost, improve quality or assure faster and dependable delivery. A company taking scheduling has to do capacity and aggregate planning before sequencing the job. Forward scheduling is concern with the finished products, jobs with known requirements, component parts, due date, or profit contributions. Scheduling minimizes the customer’s waiting time and is evaluated with average completion time per job, number of jobs in the system, number of late days and the amount of time facility utilized.
The most popular use of linear programming in scheduling is loading, sequencing and dispatching where a task may follow the shortest processing time, first come, first served, earliest due date or the longest processing time. Gantt charts are also useful for these processes. (Sawit, 2005) Managing seasonal demand Chase demand strategy Most services cannot be discovered easily because the demand for services and service capacity is difficult to predict. The services have to be provided at the appropriate place and time where effort is usually the most constraining resources for services.
Order custom essay Scheduling, loading and sequencing with free plagiarism report
A good example of a chase demand strategy is retrenching or hiring new employees to meet the customers demand. Level production and managing demand Level production is producing at a constant rate by use of inventory to absorb fluctuations in demand. To manage demand, companies need to maintaining resources for high demand levels, review work schedules, outsource services from specialists, subcontract and use part-time workers last but not least are able to provide the service or product at a later time period. Different manufacturing approaches. Small batch (Jobbing) and Big batch
This is an intelligent production planning system that facilitates the timely and flexible execution of small production batches. The aim here is to make the solution as cost-effective as possible such as a system that is designed to fully integrate with existing IT systems, and uses standard dynamic hardware and operating systems. Overproduction is making more than the next process in the system requires and is not limited to creation of excessive finished goods inventory. Incase of defects then the economic loss will be greater. The waste of waiting a result of overproduction may be compounded if a defect is discovered.
Continuous production These are on going processes that do not end with implementation, but require continuous review of processes and ongoing system improvements. With the aim of increasing a company’s bottom line profits by reducing overhead costs which can be done offshore or outsourced. Waste in production results from products that do not meet customer specifications for quality. Defective products create costs by wasting inventory, labor, and capacity on products that can not be sold furthermore they create more demand on the labor and capacity used.
Rework of defective parts increases the processing time associated with their production, lengthening lead time and increasing the level of inventory in the system, all contributing to higher costs and lower profitability. (Sawit, 2005) Flexible Production (lean) Strategies Flexible production strategies are incorporated to enhance production of multiple products for maximizing profitability though improvement of efficiency. During the production process the waste is removed at all stages of production. The aim is to reduce unnecessary costs but improvement on the quality of the product remains nonnegotiable.
The method focuses on reduction of faults but makes quality and speed to be better. This entails review of the current processes, Identification of inefficiencies that can be avoided, development of solutions to eliminate wastes then implementation of the solutions. (Sawit, 2005). References: Raturi, Amitabh S. , and Evans J. (2005), Principles of Operations Management. Mason, OH: Thomson South-Western. Sawik T, (1999), Production Planning and Scheduling in Flexible Assembly Systems. Springer publishers, P. 113 Stevenson and William J, (2005), Production and Operations Management. 8th ed. Boston: Irwin/McGraw-Hill.
Related Questions
on Scheduling, loading and sequencing
Cite this Page
Scheduling, loading and sequencing. (2018, Jan 04). Retrieved from https://phdessay.com/scheduling-loading-and-sequencing/
Run a free check or have your essay done for you
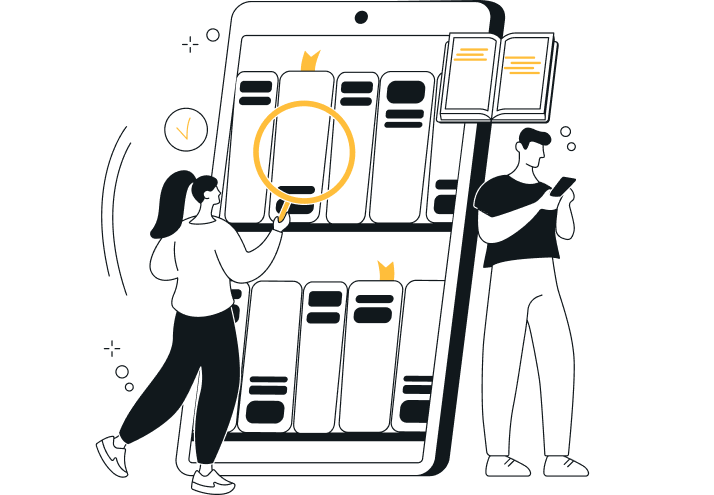