Safety in the Manufacturing Industry
Safety is the state of being free from harm or danger of any kind. Safety is usually achieved through careful planning and the removal of all vulnerable sources of danger or any other that are prone to arise. The first step in the management of any environment to ensure that safety is achieved involves the identification of the potential sources of danger. An array of all the panic triggers is usually made and each is tackled single-handedly. Failure to identify all the potential sources of danger may cause a lot of unforeseen harm (Stellman, 1998).
In any workplace, there lie very many potential causes of harm and injury. The repercussions are likely to be very serious given that many places of work usually have hordes of people going about their business and most of the times many are oblivious of any form of lurking danger. In case of any accident that may occur, the number of casualties in many places of work is likely to be very high. The effects of such accidents can however mitigated by the careful consideration of all factors by the planners and the devising of ways to deal with the accidents prior to their occurrence.
Many of the hazards that may occur in most working places and cause loss of lives and damage of property includes fire, floods, chemical explosions, release of poisonous gases and the risk of being shred by machines and being cut by very sharp objects (Moi, 1993). Manufacturing Industries: Manufacturing industries are the type of industries that are involved with the production of goods for the end user markets. Such industries produce these goods in large masses; mass production, and the raw materials are brought to these industries in bulk.
Order custom essay Safety in the Manufacturing Industry with free plagiarism report
A lot of machines and are used in various processes within these industries and a lot of manpower is also incorporated in order to increase the production by these industries. All the processes, right from the offloading of the raw materials to the packing of the finished products involve a lot of manpower and machines and many accidents that jeopardize the workers’ safety are likely to happen in any of these stages. Different manufacturing industries usually have different strategies of ensuring their employees’ safety and reducing the occurrence of accidents. Safety in the manufacturing industries:
It is mandatory for all industries to ensure that their employees are safe and are free from any kind of harm in the course of duty at these industries. There exists a set of laws that govern how al industries ensure the safety of their employees while at work in the industries. The employees are also obligated to follow the policies, procedures and the directives that are set out in these laws, to the letter. They are also expected to be on protective gear provided by the industry at all times. They are expected to adhere to all the safety rules that are laid out by their employers.
The employers are on the other hand expected to give directives to their employees that would be implemented in case of any tragedy and even put signs at strategic places within these industries. The signs must be brief and clear to the employees in order to avoid any confusion whenever there is an accident of any kind (Poltev, 1986). The Passing of the Safety Act: It is estimated that about six thousand workers in the USA die every year due to workplace injuries, another fifty thousand workers die because of exposure to workplace hazards and millions of others die because of non-fatal injuries sustained at their workplaces.
This was estimated to be depriving American businesses about one hundred and twenty five billion dollars per year. The government is in all ways trying to curb the occurrence of such by ensuring the safety of every employee at his or her place of work. Safety at the workplace goes a long way to see the cultivation of a good and better job culture at the place of work. The Occupational Safety and Health Act (OSHA), was passed by the congress in 1970. This act was passed in order to ensure that each and every worker in the nation of USA was working under conditions that are safe physically and even health wise.
Some states, however, have enacted their own laws to protect the workers from any physical or health risks at their places of work though they also do ensure that these laws are as effective as those set in the federal law. The OSHA covers all employees except those who are self-employed and public employees in the state and local government. Responsibilities of the manufacturing industries (employer): According to the OSHA website - www. osha. gov, the Occupational Safety and Health Act stipulates that:
The manufacturing industry should provide its employees with well-maintained tools and equipment. This serves to ensure that the probability of the occurrence of an accident due to the ineffectiveness of the equipment. The industry officials should ensure that faulty equipment is replaced or repaired immediately to avoid any casualties of any kind resulting from any accident. The industry should also offer the employees with appropriate protective equipment and clothing in order to protect these workers from bodily harm from the various things that they handle within a day.
This facilitates the reduction of the occurrence of accidents and the effects of any hazardous substances that the employee may come in contact with. The manufacturing industries must also take their employees for medical examinations prior to and after any activity that may be involving any hazardous substances (Rabinowitz, 2002). In case of any signs of infection, the treatment and medication should be administered on the patient immediately in order to lower the chances of the employee becoming severely affected.
The employees should also be granted access to their medical and exposure records. Such records should always be at their disposal so that they can be always updated about their health status and take any personal measures necessary. The industries must provide training to their employees prior to handling any equipment that may be hazardous. The training should be done as per the standards set by the OSHA. This serves to ensure that the employees are well acquainted with the type of equipment that they use for any particular task that the employer bestows upon them.
This kind of training also ensures that there is a reduction in the number of accidents that occur in these industries. The standardized training also ensures that there is uniformity in the way accidents are dealt with and this avoids confusion in case of such accidents occurring abruptly. Accidents should be reported to OSHA within the first eight hours of their occurrence. Those accidents that cause lots of casualties should also be reported within this period. Accidents that leave more than three people hospitalized should also be reported to OSHA within this same period.
This facilitates the investigation and evaluation into the cause of the accident and the necessary measures are taken in order to reduce such accidents in future and thus increase safety in the workplace. The employer is also obligated with the duty of posting the OSHA poster (OSHA 3165), which informs the employees of their rights and responsibilities. No discrimination is allowed upon an employee who goes forward to address some grievances to OSHA regarding the workplace. The industries are also obligated to keep records of work-related accidents, injuries, illnesses and their causes.
They should also post OSHA citations and abatement verification notices to a worksite. They should also abate cited violations within the set prescribed period. The Responsibilities of the Employee: The employee should review the employer provided OSHA standards, regulations and requirements in order to be well conversant with them and follow them accordingly and report any flaws in order to avoid accidents and other mishaps. The employee should also request for information from the employer regarding emergency procedures so as to avoid confusion at the time of tragedy.
The employee should observe each and every directive accordingly (Harms-Ringdahl, 2001). The employee should try and grasp the safety and health training provided by the employer as per OSHA standards. Such training should be administered in cases where some toxic substances are involved. All other procedures set for emergencies should also be carefully studied. If carefully observed and followed to the letter, these rules and regulations can spare many lives and save lots of others in the manufacturing industries (Taylor and Hegney, 2004).
Cite this Page
Safety in the Manufacturing Industry. (2017, May 08). Retrieved from https://phdessay.com/safety-manufacturing-industry/
Run a free check or have your essay done for you
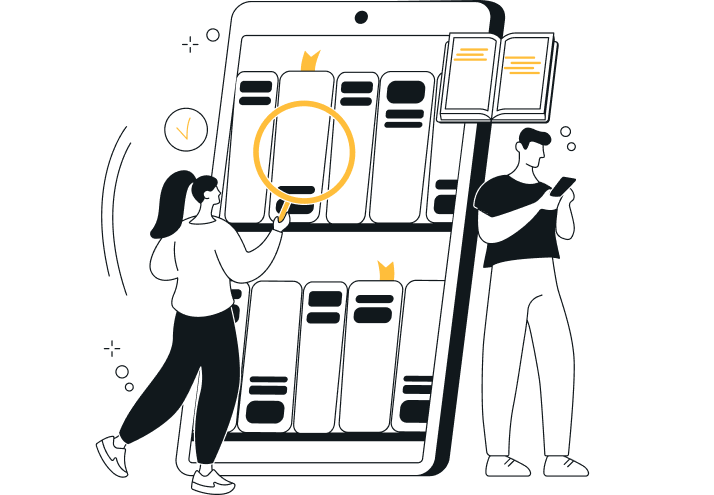