Procurement and Inventory management at Nestle
The procurement life cycle followed by Nestle is broken up into several integrated components in the business and involves large number of intermediary processes like purchase requisition, purchase order, vendor involvement, goods receipt and inventory management and accounts payable. All this processes make together the life cycle of procurement process.
Each time an inventory item is received or issued from the inventory at one of the Nestle locations, the system automatically updates stock quantities and values, and reduces inventory. Time consuming tasks are simplified through determining optimum source of supply, analyzing and comparing vendor pricing, issuing purchase orders, managing the authorization for purchase requisitions, processing invoices for payment and recording the same. The efficient supply chain at Nestle requires all stock planning and operational activities to be integrated into a uniform business-process flow.
At the inventory management there are three types of Goods Movements namely goods receipt, goods issue and transfer posting. As soon as the goods movement is entered stocks are updated, material documents are created to record the event and accounting documents are created when change in valuation area occurs.
Order custom essay Procurement and Inventory management at Nestle with free plagiarism report
At Nestle, sending a purchase order to a supplier, it is necessary to have some internal agreement on what is required, together with an audit trail of approvals for that requirement. A Purchase Requisition (PR) provides this facility and is an internal request to purchasing. Once it has been electronically signed off (workflow), it can be used to generate a Purchase Order, which is an external request to the Nestlé’s supplier.
A purchase requisition is an internal request at Nestle to purchasing. You ask the buyer to provide a certain quantity of a material or service on a certain date. A purchase requisition can be created automatically by MRP or manually created. The MRP controller can also convert a planned order into a purchase requisition. Source determination is a separate function. The buyer receives proposals if, for example, fixed vendors or outline agreements exist for the material.
The material requirements planning, inventory, production, and procurement processes all work together to orchestrate a smooth flow of high quality material. Workflow events are configured to Nestlé’s requirements by taking into consideration the degree to which automated or manual controls are required. Vendors quotation and selection processing is also done with great focus on the SAP implemented for that purpose at Nestle. The materials requirement planning system at Nestle usually makes good a calculated definition about the requirements for a particular territory and at all locations over the enterprise. The stock management system collaborates with the inventory system in the SAP system to manage its products.
Related Questions
on Procurement and Inventory management at Nestle
Cite this Page
Procurement and Inventory management at Nestle. (2018, Jan 01). Retrieved from https://phdessay.com/procurement-and-inventory-management-at-nestle/
Run a free check or have your essay done for you
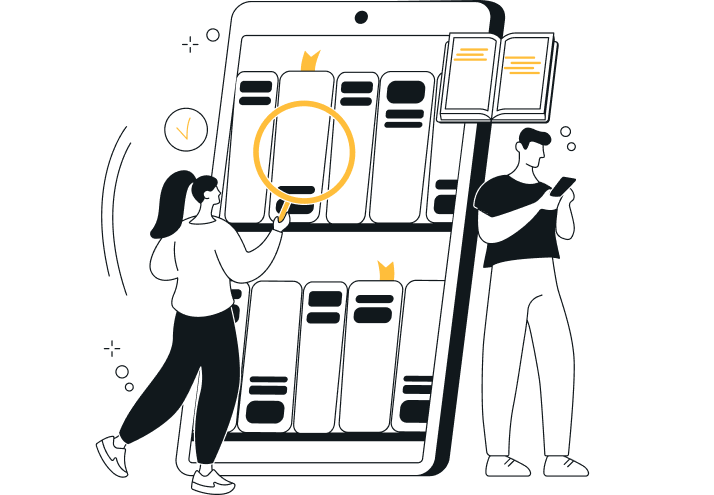