Metalworks Case
Introduction
Metalwork is a company supplying cabinets and safety boxes. At the moment it has two plants and two warehouses which are “Des Moines” and “Dover”. Metalwork also uses an external supplier in case they can’t meet the demand. However in the case Metalwork has to buy products from supplier it doesn’t make any profit since the selling price $75 for the cabinet and $107 equals the buying price.
Regarding this situation Metalwork has decided to improve its logistic efficiency by either increasing its capacity in “Des Moines” or investing in Juarez, Mexico by building up a new factory. Our job in this condition is to analyze the best option, to optimize the logistic efficiency and help Metalwork make a decision. At first we will see and optimize the current logistic system and then we will try to run the two solutions. And see which one is the best in order to give Metalwork the best possible answer. Baseline scenario 1: without distance constrains and with direct shipment from supplier to customers.
Order custom essay Metalworks Case with free plagiarism report
The first job we had to do was to actualize every data and verify everything was correct. This work consisted in adding the data for the 3 time periods missing (2011-2012-2013). So we added the data regarding warehouse capacity, production capacity, production costs, and customers demand. We allowed direct shipment from the supplier to customers. We also checked the flows between every actor of the logistic process (exhibit 1). We use the Rail Warehouses Midwest between warehouses and ABC fleet carrier from warehouses to customers. Then we made the software run for a first try and saw the results.
So as a result we can see that first the scenario is feasible. Hopefully by the way since it is how the Metalwork is supposed to work. We can see that the total cost (which contains manufacturing, transportation, warehousing, variables, and holding costs) is $321 741 907 75 and total profit of $2 001 748 527 44. So the situation is pretty good since the company realizes profits. We can also see that in this baseline scenario we order 629 398 84 units to our supplier. Units on which we don’t make any profit. So we can clearly see that there is a need to invest in order to meet the demand thanks to our products.
Baseline scenario 2 without distance constrains and without direct shipment from supplier to customers. In this scenario we will try to see if it is possible work without direct shipment from the supplier to the customers. That is why the lane visual changes compared to the first one. The answer in this case is that this scenario is not feasible, because of warehouses capacity. Indeed we begin to see that it is necessary to work with more than 2 warehouses. Baseline scenario with direct shipment and with distance constrains for warehouse to customer. In this scenario we will introduce constraints regarding the maximum distance to customers.
Indeed high quality service and responsiveness is highly important to Metalwork that is why we add a distance constraint of maximum 800 miles to Tier 1 customers and 1000 miles to Normal customers. We keep the same data and the same lanes and logistic system. Except that we allow this time delivery from the supplier to the customers. Because if not we would have add the same problem as in the second scenario since the situation is even harder regarding the distance constraints. That is why we decided to run it with this scenario. So we can see that the two warehouses supply the customers in within the 1000 miles away.
That is why the supplier has to send directly to the other customers and also to supply the rest that is needed by the customers. We can see that only having two warehouses is really not enough. In this situation the supplier has much more importance and that has huge effects on the costs. Dual supply On the diagram bellow we can see that the supplier has a huge importance on the production since it produces even more than the Plant in Dover. So in this situation we can see that the total costs have dramatically increased from $341 741 907 75 to $887 796 558, 11 and the profit has gone down to $1 435 693 607, 07.
The manufacturing cost is really high: 749 750 420 $ compared to 138 145 001$ in the first scenario. Regarding the new constraint we really realize that Metalwork needs to invest in new plant and in new warehouses. Baseline scenario with direct shipment and with distance constrains for warehouse to customer and supplier to customer. The scenario is not feasible because the warehouse capacity is limited and the distance from supplier to some customers is greater than the distance restriction. We decided to apply this restriction because we fought it was necessary to apply the distance constraints to the supplier also.
Indeed the service level must be equal for every product to every customer. Indeed the customer doesn’t need to know and don’t care if the product is from the supplier plant or Metalwork plant. Increased demand scenario in Des Moines We increase capacity of Des Moines. The production capacity of the safety boxes increases by 25% and cabinets by 50%. We set the additional $1 250 000 operation costs. And we decrease the cost for each unit produced in Des Moines by 50 cents. We apply these directives into our data base for every time period. We also add the possibility to go from 2 warehouses to 4 warehouses for the 4 time period.
Two of the warehouses are fixed. One in Des Moines and one in Dover. So in this scenario we can see that the total cost has decreased compared to the first baseline scenario. Now we have a total cost of $248 104 881 97 and a profit of $2 075 385 283 22 which is much higher than in the first baseline scenario. We can also notice that with these investments the supplier is no longer needed. So the objective achieved. Plus we have 100% of the demand met. We clearly see that the Plant in Des Moines is the main motor of Metalwork. Plus even with the distance constraint we see that the scenario is feasible.
This is able thanks to the 2 more warehouses available. So as we see on the map bellow, all the customers are supplied and the 4 warehouses are dispatched on every side of the United States. Plus there are only a few customers supplied by two warehouses, because of warehouse capacity. So clearly the result is conclusive. The demand is met the costs go down and the profit rises. Double supply Mexican Plant scenario In this scenario the objective of Metalwork is to improve the network of its plants and also to relocate its investment into a low labor cost country.
The opening cost of this plant opening is $5 000 000. In order to make this scenario work we had to reset the data for the 4 time period, that is to say cancel the downsize in costs and production capacity in Des Moines. We also forbid the direct shipment from supplier to customer if needed. And used the railway West transportation for Railway warehouses West to supply our products to the warehouses. But we still have the same problem as in the previous scenario that is to say that some customers are supplied by two warehouses.
Double Supply
As we can see can see in the chart below, our total cost is $ 243 950 541 68 which is smaller than in the previous scenario. The profit is also a little bit higher, with $2 079 539 623 51. 100% of the demand is met so we can say that the objective is met. And with better results on every side whether it is financial or quality we can say that we would recommend this investment rather than the first one. However this also depends on the image the brand wants to have, something such as made in America and avoid social problems in the plants.
When the activity is relocated. We can see on the last chart that the production almost equally balanced between Des Moines and Juarez. The good thing is that the supplier is no longer needed. So every unit sold makes the company make profit.
Conclusion
- After comparing the different scenarios based on the guidelines we had, we found that the scenario that involved building a plant in Juarez, Mexico turns out to be the best one.
- While comparing the increased capacity scenario and the “Mexico” scenario we found that they are nearly the same. In both of these scenarios we find that we don’t need an external supplier, we would be able to supply the demand on our own.
- Compared to the baseline scenario we can see that increasing the number of warehouses decreases the overall total costs.
- While optimizing the solution, we figured out that having to use two given warehouses might not be the optimal choice, those two warehouses should be catalogued as potential, the maximum number of warehouses should be increased.
- We observed baseline scenarios can’t compete with the improved capacity scenario or the “Mexico” scenario since the cost of buying from a supplier is too high.
Cite this Page
Metalworks Case. (2017, Apr 19). Retrieved from https://phdessay.com/metalworks-case/
Run a free check or have your essay done for you
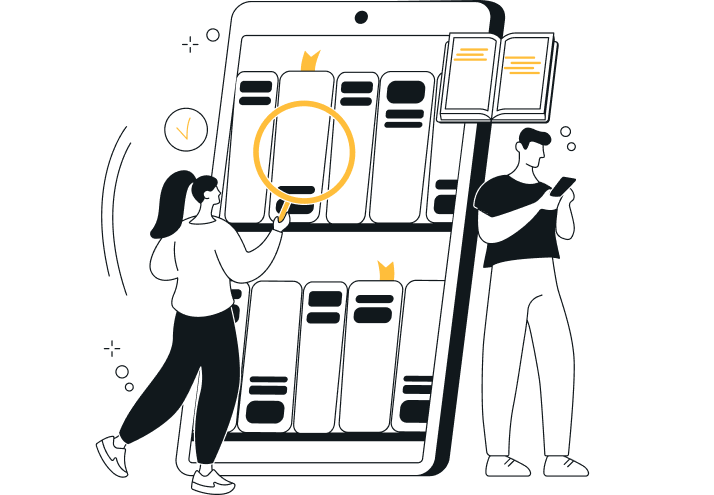