McDonalds: Inventory Management Practice and its Advantages
McDonalds is one of the most popular fast food chains with a worldwide presence. It can be found in 119 countries and has about 31,000 restaurants. It employees about 1. 5 million people. It is one of the largest fast food chains, serving 47 million customers daily (2). Most restaurants offer both counter service and drive through service with indoor seating (and sometimes outdoor seating too! ). McDonalds has become an emblem of globalization. It’s main line of business is hamburgers. It primarily sells cheeseburgers, hamburgers, French fries, chicken products, ice-creams and soft drinks.
Inventory management in McDonalds:
McDonalds follows a Just in Time (JIT) system of inventory management. JIT, as the name suggests, is the system of supplying products to customers as soon as they have ordered for it, with minimal delay between placing the order and getting it in hand. McDonalds doesn’t begin to cook or assemble or preheat their stuff until they receive a customer order.
Order custom essay McDonalds: Inventory Management Practice and its Advantages with free plagiarism report
This was not the case earlier. They had a different approach to inventory management wherein they used to pre-cook a batch of hamburgers and sit under heat lamps. It used to keep them under the lamps for as long as possible and eventually discard whatever they couldn’t sell. Hence customers couldn’t enjoy freshly made food. The only way it could happen was by the customer giving a special order. Hence McDonalds moved to the JIT system of inventory management. This shift was possible because of the new burger making technology that enabled them to make burgers faster and keep the time between placing an order and receiving it as miniscule as possible. This results in the finished product sitting in the inventory for as little as possible. This enables proper inventory management and reduces wastage while giving maximum satisfaction to the customer. The customer is made to wait for a very short period and this is a huge factor while going for such a system of inventory management. Thus, the customer is happy. But it has also lead to a huge decrease in costs for McDonalds and this is what has made JIT system such a success.
Higher customer satisfaction and reduced costs
- Improved quality of food: The burgers are made fresh for the customer and thus provide maximum satisfaction. There is no chance of offering stale food to the customer. Higher customer satisfaction leads to customer retention and increased sales. The customer resists the impulse to try out rival brands till he is deriving maximum satisfaction from the brand in question.
- Better customer service: McDonalds earlier used to make special orders for customers while dishing out precooked burgers from the inventory to most customers. Hence such special orders were dreaded by the staff and used to freak them out. The staff, now after introduction of the JIT system, is more calm and composed and offers better service to the customers. This higher customer service is subject to the ability to produce faster burgers. McDonalds are able to handle the demand a lot better. They don’t have to waste time in calculating the estimated sales hour by hour and maintain an inventory.
- Better costs: The holding costs for the raw material like bread, beef, cheese, chicken is fairly high because of their spoilage costs. Under the old system, McDonalds used to maintain a high inventory leading to faster orders but this resulted in a lot of unsold food because of the low shelf life of beef etc. after being cooked. The food was then forced to be sold at a higher price to cover up for the losses in scrapping unsold food. This resulted in lower costs to McDonalds.
- Better Raw Material handling: With the new system, McDonalds does not need to procure the raw materials in bulk advances. This reduces daily expenses considerably and ensures fresh and high quality raw material all the time. High holding costs and low ordering costs were the factors that drove the Just in Time system to the market. The ability to lower the operating costs makes JIT a highly feasible solution. It has also led them to reduce drastically the safety costs. Safety time exists due to variability in demand and variability in lead times from suppliers.
JIT helps reducing the lead times and hence safety stock. JIT provides for an attractive and cost cutting mechanism but it is very important to weigh the risks and analyze the associated consequences that might happen. A very fast burger making technology makes JIT a viable option for McDonalds but this might not be the case in other organizations and they might face problems in handling bulk orders through JIT system.
Related Questions
on McDonalds: Inventory Management Practice and its Advantages
Cite this Page
McDonalds: Inventory Management Practice and its Advantages. (2018, Jan 01). Retrieved from https://phdessay.com/mcdonalds-inventory-management-practice-and-its-advantages/
Run a free check or have your essay done for you
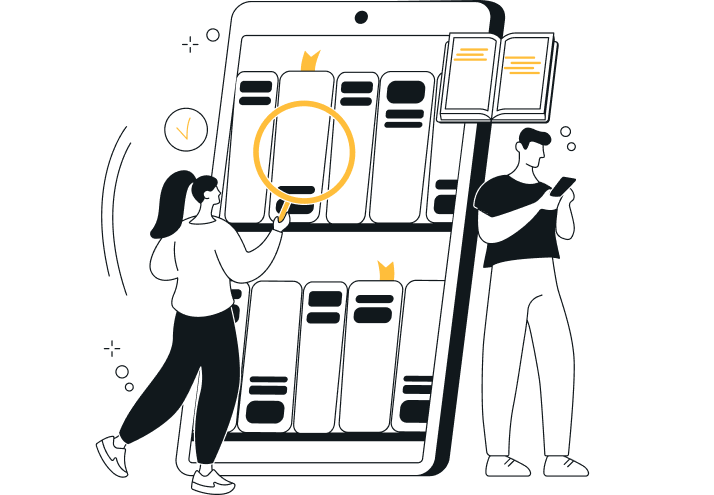