Manufacturing and service organisations
Operations Management is present in many occupations as well as those of manufacturing and service industries. I belive it to be present in daily duties of any person although they may never notice. With this in mind I see operations management as a skill anyone has with an aim of achieving an outcome of something they are working towards in a logical process with thought of awareness of a system structure. Operations management has been around for some time yet it was Christopher Polhelm (Sweden) first recognised a skill and recorded that ‘Nothing increases demand so much as low prices.
Therefore there is a great need of machines and appliances which will diminish the amount or intensity of heavy work’ (Extract from text book Operations Management – supplied by DMU for open learning please see bibliography) this was around 1700. There are cases in many history books and stories passed down that operations management was present before this yet not identified as operations management. From 1700 business development has grew significantly and seems to have been a notable point of operations management to present day.
In a more modern look operations management has grew and become a dedicated service in its own right as organisations now employ individuals to develop, implement and complete operations management as a specific role. From the next page I will appraise the role of operations management in a manufacturing & retail environment. The Role of Operations Management in both Manufacturing & Retail: The role of ‘Operations Management’ is a collection of successful systems for operations in any organisation.
Order custom essay Manufacturing and service organisations with free plagiarism report
In order for operations to be effective and efficient, the systems must also be effective and efficient. Michael Porter (1985) the strategic inventor of the ‘Porter Value Chain’ constructed a chain effect understanding that every business should implement for logical understanding and awareness of its inputs and outputs as a business. He separated the business functions into primary and secondary methods, primary being dedicated to the product or service and secondary being supportive methods to aid the primary. (Please view Appendix 1) Porters (Michael Porter 1985) Value Chain (VC).
From Appendix 1 the model suggests, that no matter how many operational units that are involved in the process of generating customer value; these primary activities can be conceptualised into five generic stages. The five primary stages are inbound logistics, operations, outbound logistics, marketing and sales, and service. These primary stages are supported by the firms’ infrastructure, human resource management, technology development, and purchasing and procurement. The stages within the VC should not be seen in isolation but looked at in a wider context and include the interactions between stages not just within the processes.
The relationship between sales, operations and procurement for instance can determine how much stock is to be carried and therefore reflected in cost of inventory held. Operations as systems implement the needs and practice of systems within an organisation. These systems must be understood with a thought of how the system operates its inputs and its control methods and/or output required. Systems are often described as closed or open systems or relatively closed or open systems. Closed systems have no inputs, no interactions within its environment and no output.
Open systems are known as unpredictable inputs with free interactions with its environment that has a varied output as it is known to change. Relatively closed or open systems are known as controlled systems with predicted inputs that are controlled within its environment having a predictable output. The transformation process is a system to note for understanding of the systems and their need to be present as in basic terms; an input will be transformed into an output and is commonly known as the black-box of operation systems.
The 6 Ps of operation are more commonly known as the operation mix. The origin of the 6 Ps is unclear yet Professor Keith Lockyer of Bradford Management Centre (1988) developed an early version to apply a logical thought process to the implementation of operations. In operations management we can apply this mix to new or revised operations for reference. The 6 Ps are: Product/Service, Process, Place, Programs, Procedures & People.
Cite this Page
Manufacturing and service organisations. (2020, May 12). Retrieved from https://phdessay.com/manufacturing-and-service-organisations/
Run a free check or have your essay done for you
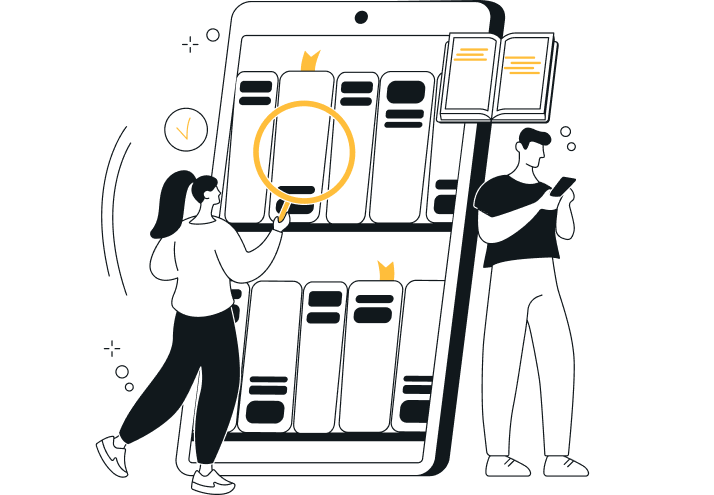