Jit in Indian Automobile Industry
The traditional concepts of Quality and customer satisfaction have been challenged in the recent years. Customer choices and perceptions have also been changing continuously. Japanese manufacturers were the first to meet these challenges by introducing many innovations in manufacturing systems and management, one of which is the philosophy of “Just in Time”. Just-in-time (JIT) refers to a collection of practices that is designed to eliminate waste and achieve manufacturing excellence.
These organizational practices encompass the entire logistics flow of materials from purchasing through production and distribution. The elements of JIT may include shared product design with suppliers and customers, movement toward single sourcing, proximate suppliers and customers, reduced set-up times, preventive maintenance, reliance on analytic tools to identify sources of defects and plant optimization layout (re)configurations, among others Just-in-time (JIT) manufacturing systems have attracted the attention of industries all over the world.
The perceptible impact of JIT lies in attaining productivity and quality standards. The real challenge before Indian managers is to establish priorities among potential JIT techniques to achieve best possible advantage of JIT implementation in Indian industries.. With the variety of products on offer increasing with customization and evolving customer needs, it is but important that a manufacturing facility embraces the advantages of JIT in making the operations lean and flexible. Indian Automobile Industry: India currently has approximately 40 million vehicles. In February 2009, monthly sales of passenger cars in India exceeded 100,000 units. Current low penetration, rising prosperity and the increasing affordability of private vehicles along with importance to exports offer a healthy prospectus for the Indian automobile industry. Several Indian automobile manufacturers such as Tata Motors, Maruti Suzuki and Mahindra and Mahindra, have expanded their domestic and international operations.
Order custom essay Jit in Indian Automobile Industry with free plagiarism report
India's robust economic growth led to the further expansion of its domestic automobile market which attracted significant India-specific investment by multinational automobile manufacturers. Due to strong Global competition Indian companies started focusing on adopting new techniques and technologies which enabled manufactures to improve their processes and products
JIT in Automobile Industry of Other Countries
Many countries have got leverage by implementing JIT techniques in their respective automobile industries. Peter Turnbul, analyzes the trends in the UK automotive industry during the 1980’s, giving special focus to the adoption of JIT and TQM principles. This includes development from within the organization and relations between suppliers. Also the implications of adopting Japanese techniques on Information systems have also been looked into. It was found out in the study that Japan was way ahead of UK and US in terms of productivity and Quality in the cars manufactured due to successful implementation of JIT and TQM techniques and US and UK companies are gradually bridging this gap.
Bo Hou, conducted a research on the benefits and difficulties faced in implementing JIT for an automotive company in China. An international automotive company with factory located in China was taken for the Case study, examining the pre and post JIT implementation experiences. In order to collect data Semi-structured interviews were organized. Most interviewee’s support that proper design of information systems could assist JIT systems. According to the interviews, Kanban is a primary management method in the case company’s JIT model.
It was found after the interviews that inventory can be maintained at a reasonably low level. Performance indicators have been employed to examine the achievement of suppliers in quality, on-time delivery etc. , in order to encourage suppliers to participate in the JIT program.
JIT Implementation in India
Several Indian companies have initiated JIT implementation into their systems or are claiming to have implemented many key features if JIT. While studying the implementation of JIT in India the following factors have to be considered. Size of the firm .Indian economy (only opening up in early 1990’s) How MNC’s having manufacturing operations in India are Implementing JIT In a Survey of JIT practices conducted by Mahadevan, Questionnaires were sent to 400 companies but only 43 of them responded usefully. Fourteen critical factors were identified and participating organizations were asked whether these factors were important for JIT implementation in their firms. Quality circles and cellular manufacturing have been rated low while TQM was rated very high. Vikas Kumar , explains the interrelationship between the different JIT elements.
According to him the elements of JIT important to India are Buffer stock removal, Cellular manufacturing, Kanban and Error prevention Garg D conducts a case study in JIT implementation of an Indian tractor assembly. It started implementing JIT purchasing in the mid 1980s. Initially, the company received discouraging results in almost all the areas for several years. Later on everything was streamlined and management began achieving significant results in terms of reductions in inventory, material movement, space, manpower, work in process and lead time, and an increase in productivity and quality.
It can be said that in spite of old machinery, the company is sustaining its competitiveness in the tractor market by applying JIT. Vikas conducted a survey on 34 Indian firms with the aim to find: Those elements of JIT that might be difficult to implement in Indian Industry. These have been found to be Buffer stock removal, Error prevention, Frequent and reliable delivery, Kanban system, Multi functional worker, short lead time, Small lot size, Zero defect etc. ) Reason for slow implementation of JIT in India which have been found to be High cost of implementation, Informal and casual Auditing, Lack of support from suppliers, Lack of training, Lack of understanding of JIT techniques, shortage of multi functional workers Garg D explains that the key steps in JIT implementation were: extensive training of employees on pull concepts; identification of key performance parameters; new layouts based on U-shaped cells ( wherever applicable) ; standardization of operations; a maintenance plan for each machine; housekeeping; visual control; and multi-skill training.
Vikas Kumar , Several Indian industries are implementing the JIT with belief that it would be helpful to face the global competition. Yet, its effectiveness would depend upon qualities, attitudes and values of Indian work force. The paper gives focus to work culture of the organization. Some of the elements of work culture desirable for JIT are flexible workforce, Cross training, long term employment, Job enlargement and Labor unions, Work force involvement etc. Benefits
Vikas Kumaridentified that the Potential benefits of JIT include reduced setup cost, labor cost, and move distances According to Chandrathe major benefits of JIT manufacturing system in ascending order are Reduction in inventory, Quality improvement, Increased productivity, Increased profit margin, Improved competitive position. Vikas Kumar Highlights the most expected benefits of JIT which are Improved equipment utilization, improved quality control, worker efficiency, inventory turnover, flexibility, productivity, Profit margin, Team work, Low scrap rate etc Disadvantages of JIT
Some of the disadvantages of JIT as highlighted by Vikas are: * Implementation if JIT does not automatically translate to profits as many direct and indirect costs are involved in JIT implementation. Also JIT requires appropriate fit between manufacturing activities, organizational design, processes etc. * JIT programs need continuous check and control for sustained improvement * The timely of delivery of goods is extremely important which might be difficult to achieve in some parts of India * JIT may demand unrealistic commitment from employees.
With respect to the Indian Automobile Industry JIT purchasing, a few elements of JIT production and JIT Logistics are given focus in this research paper. Purchasing In industries like the automobiles, where the cost of raw material accounts for almost 50-60% of the cost of the final product, Purchasing is a key element to focus for cost reduction . Purchasing involves determining the need, selecting the supplier, and arriving at proper price, terms and conditions, issuing the contract or order and to follow-up to ensure proper delivery on time According to Sultan Singh, Dixit Garg. The traditional approach to purchasing is at the root of many problems that business faces today. High inventory levels, soaring costs, adverse relationships with suppliers and quality issues which either stop production or results in poor products are just a few of the problems with the current way of purchasing JIT Purchasing Sultan Singh.has found that Just-in –Time Purchasing has received an increasing amount of attention throughout the world due to its potential for quality improvement and cost saving.
Jocclyn Drolet found that many studies indicate that the JIT purchasing function is of paramount importance for successful JIT implementation According to Sultan Singh, Dixit Garg. The four basic principles of JIT purchasing are: Elimination of waste . Employees involvement in decision making . Supplier participation Total quality control Sultan Singh. Found that JIT purchasing has been implemented in many industries of several countries such as United States, United Kingdom, Italy, Germany, and Korea etc. Today many reputed Indian industries have also switched to the Japanese JIT Purchasing concept to improve their product quality and productivity. In traditional purchasing importance is given mainly to the price of the product. Supplier relationship building, quality, delivery time, supplier satisfaction etc are in the back seat. Sultan Singh. States that Japanese JIT Purchasing is an uninterrupted flow of 100% acceptable materials delivered on due dates and time at optimal cost 100% of time. In JIT purchasing environment purchasing is carried out in small lots with frequent deliveries in small standard containers used to hold exact quantity and to the required specifications from a nearby local single supplier with a long-term contract. The company relies more on performance specifications Consistent quality and delivery performance is most important parameters in the supplier evaluation while price is an important one.
This area includes supplier’s management, inspection of incoming raw materials/ semi finished / maintenance components etc. The expectations of the buying firm in JIT Purchasing Dixit Garg conducted a survey to identify the important attributes of JIT Purchasing with respect to the Indian Context. The importance of JIT purchasing attributes in a decreasing order as were High Quality, Mutual trust and Co-operation, Reliable delivery, Exact quantity and Increased customer support. Jocclyn Drolet. Stated that the most frequently mentioned benefits are the reduction in lead times, the decrease in inventory levels, waste elimination, and improved quality of incoming parts, raw materials and the delivery process. In fact, these four benefits have been so widely cited in analytical studies, and cross validated in empirical studies, that we believe that they may no longer belong to the domain of hypothetical benefits but must be taken as factual benefits. Sultan Singh, Dixit Garg. States that in JIT Purchasing no percentage of rejects from supplier is acceptable. The supplier is also encouraged to be more innovative.
Jocclyn Drolet stated that some of the success factors of JIT purchasing are JIT supplying Partnership, Restructuring supplier network, Quality of purchased products, Long term and exclusive agreement with suppliers, Proximity etc. He emphasizes that partnership is a catalyst for other JIT purchasing success factors Problems encountered in JIT purchasing implementation in India Sultan Singh. Found that most serious problems, however, are not operational in nature. They are “people problems”- stemming from attitude and orientation, past experience and practices, and the passive factors of interpersonal relations. The suppliers may not fully support JIT purchasing program because of following reasons: Lack of incentives for suppliers to adopt JIT delivery. Lack of commitment from buyers. Considerable strain on suppliers on JIT delivery. Sultan Singh. Has found Evidences which shown that JIT purchasing can be beneficial in Indian context. The supplier is encouraged to be more innovative. He is given “loose specifications “. The company relies more on performance specifications than on product design. Counting and receiving inspection of incoming parts is eliminated.
Formal paper work is reduced to minimum delivery schedule or quantity can be changed by simple telephone calls/fax/telex message. Supplier is evaluated by consistence in quality, delivery performance and price. It can be concluded that JIT Purchasing is a key element for the successful implementation of JIT. The benefits of JIT purchasing can be summarized as reduction in lead time and inventory levels, improved quality of raw materials and better delivery process. Also there are increased supplier participation and employee involvements.
Many companies in different countries have successfully implemented JIT purchasing. Some of the problems which Indian companies encountered were Lack of support from suppliers, Lack of support and commitment from Top management, Low product Quality, Employees resistance to change and Lack of communication. Maruti is focusing on Supplier development and sharing its quality and manufacturing practices with them. Mahindra and Mahindra is now working to minimize supply constraints through advanced capacity planning, long term contract with suppliers and capacity enhancement.
JIT Production
According to Vikas[4], The major elements of JIT production in Indian context include Buffer stock removal, Cellular manufacturing, Kanban, Error prevention and others. In this research paper the attributes taken for study are Cellular Manufacturing and Kanban. Cellular Manufacturing Mahadevan infers that there has been an increasing demand for more variety in the recent years thereby pushing volumes down. It is estimated that 70 % of manufacturing industries will have mid-volume, mid-variety scenario. Cellular manufacturing provides a solution for the mentioned situation.
According to Frost ; Sullivan Cellular manufacturing is based on the Group Technology concept and involves the use of work cells. A Work Cell is a group of equipment and workstations arranged in the logical sequence of production, which can produce a product (or part of a product). To successfully maintain One-piece flow in manufacturing cells companies employ quick change over techniques The key factors that affect the design of an efficient cell can be grouped broadly as the number of process required, number of products that fit into the cell, market segments/requirement, and degree of automation.
Mahadevan mentions the benefits of Cellular Manufacturing as: Production planning and control become easier as it is similar to breaking the Manufacturing process into smaller units which are independent and more manageable. Material handling and traceability becomes easier as materials seldom go outside the respective cells for processing. Work enrichment: Employees would be in a position to better relate to the workplace and make improvements The benefits as mentioned by Frost ; Sullivan are: improved resource [both man and machine] utilization reduced lead times, improved product quality, better space utilization, lesser blocked capital in inventory, and an overall improved work space. Timothy identifies the disadvantages of cellular manufacturing as: Increased capital expenditure * Decreased machine utilization. A breakdown can cause work stoppage in cell Shishir Bhat analyses the impact of cellular manufacturing in a Gear manufacturing Machine shop.
The evaluation was done based on two outputs, throughput and flow time. It was found that the average monthly throughput for Main Gears before implementation of Cellular Manufacturing was 59. 5 and that after implementation was 90. 5. Also the average flow time [man hours a product spends on shop floor for main gears reduced from 58 to 30. The paper shows that when a job shop manufactures a group of products with similar characteristics and stable demand, Cellular Manufacturing is an effective way for performance improvements.
Kanban is a system of continuous supply of components, parts and supplies, such that workers have what they need, where they need it, when they need it. Kanban facilitates elimination of waste and is one of the most powerful tools of the “Toyota Production System”. Kanban is designed for quick response to actual consumption and ensures material availability at all times even in the face of temporary demand swings. Improved material availability helps achieve agility and flexibility in production. Kanban Systems are usually custom designed for each client and each item.
A good design takes cognizance of all relevant factors such as consumption level, lead time, transit time, optimum shipping lot, and desired delivery frequency. It can be quickly adjusted in response to seasonality of demand. Inventory reduction is regarded as one of the key strategic levers to improve productivity and profitability of the firm in theory and practice (Lieberman and Demeester 1999, Chen et al, 2005). Kanban which facilitates visual control was originally designed for manual operation. This encourages employee involvement at all levels.
However it can be integrated with any ERP system. Many tasks can then be automated, thus increasing the speed of material flow and accuracy of transactions. B. Vijaya Ramnath,C. Elanchezhian and R. Kesavan wrote a paper which deals with implementation of lean manufacturing in Engine valve machining cell in a leading auto components manufacturing industry in the South India. The main objective of the paper was to present an overview of manufacturing wastes and introduce the tools and techniques that are used to transform a company into a high performing lean enterprise.
Value stream mapping was a main tool used to identify the opportunities for various lean techniques. One of the methods used for reduction of waste was the Kanban system. A Kanban job Flow is arrived at which is used for building the future state of Value stream mapping. The elimination and or reducing of wastes is by making the process improvements in the current manufacturing line by adopting some lean tools like JIT, set up time reduction, WIP reduction etc. JIT Logistics Today Indian Automobile players seek to increase their global footprint and supply chain for many of these companies extends across several countries.
Hence Logistics is a key area Indian Automobile companies are focusing on. According to Kee-hung Lai. [17] Just-in-Time (JIT) which has been effective in manufacturing operations can also contribute to cost and service advantages in Logistics. However, the potential of JIT has not been widely recognized in logistics. Kee-hung Laihas identified the major areas in Logistics in which JIT can be applied such as
- Transportation management
- Order processing
- Inventory management
- Customer service, and a number of supporting lements including materials handling, packaging, purchasing and warehousing.
Transport Management
Typically materials were ordered in large lot shipments to obtain economies of scale. Similarly full truckloads or railcars were more efficient. For less than full truckloads loads of different companies having similar destinations were combined. Ken alternburg. States that In JIT Transport all the three parties i. e. the supplier, the carrier and the customer work more closely with one another. One option is formation of Transport partnerships just like supplier partnerships.
The carriers would be single source for a family of businesses that will treat these carriers as in-house carriers. In some JIT Environments the parts manufacturing facility is constructed at or near the final assembly plant, allowing small deliveries of parts to be made with greater control over timeliness. Ken alternburg. Suggests that where local manufacturing is not feasible, closed loop transportation is employed in which delivery trucks make stops at various suppliers on a predetermined schedule.
Disposable packaging can be replaced with reusable containers and racking compatible with assembly line use, eliminating the costs of removing and disposing of packaging materials and simplifying and speeding the loading and unloading processes Materials can be unloaded at or near final point of use in JIT System as inspection is eliminated. Costs associated with equipment used to speed the delivery process, such as specially configured trucks, containerization, and unloading equipment, are offset by improvements in efficiency as implied by Ken alternburg.
Ken alternburg States that JIT environment has affected transportation providers, requiring them to change and streamline their methods of operation, and make long-term investments in technology, Order Processing: According to Kee-hung Lai. JIT adopts technologies such as Logistical Information System [LIS], often in the form of Electronic Data Interchange [EDI], Internet, Value Added Network etc so that different parties in the logistics processes can gain access to the needed information for decision making Customer service: Kee-hung Lai states that In JIT logistics, all the activities that take up motion time, for example, order picking, shipment arranging, transporting and so on, need to be managed efficiently. The aim is to meet customer service requirements at the lowest possible cost KPMG conducted a survey on the Indian Automotive supply chain to analyze the key challenges faced by different sections of the Industry, identify the areas that need attention and also identify opportunities. A primary survey was done among the heads of supply chain of some major Indian Auto companies.The participants of the survey identified the following as the key challenges in order of priority: Integrating the end-to-end supply chain and managing it as a single integrated entity: While past efforts of OEMs have been focused on streamlining and improving different areas of the supply chain independently, through efforts in dealer management, operations planning, vendor rationalization, IT package implementation etc, it is expected that the linking up of these activities is expected to provide significant benefits to players Managing Inbound Logistics/JIT Supplies: is a key concern which faces challenges related to reliability of data, lead time and absence of quality logistics players on the upstream side. Respondents felt that as OEM and Auto component players become more global in nature it would have a significant impact on automotive supply chain. Managing costs: Cost, Quality and Timely delivery continue to become the key concern area for players.
Many OEM’s have implemented JIT inbound logistics which is not by increased visibility across the supply chain and improved planning, it has only resulted in the burden of inventory getting shifted from OEMs to their Tier-I vendors. The Key initiatives taken up by the companies to address these challenges according to KPMG [19]) are: Increased Investment in IT and processes: Implement Integrated IT systems [such as ERP], but survey revealed that they were not able to leverage on such systems as their business process were not streamlined or aligned with the needs of the IT System. Vendor/Dealer rationalization: Many respondents agreed that Indian Industry has not evolved into fully tierized structure where Tier-I vendors take on responsibility for modules / sub-assemblies
Outsourcing to logistics service providers: Outsource key activities along the supply chain to logistics players, in an effort to reduce costs and increase focus on their customers and core activities. Most OEMs and large Tier-I suppliers have already outsourced their outbound logistics activities. These activities include carrying out ‘milk runs’ to collect and deliver parts to OEMs on a daily basis, transferring materials across hubs and warehousing/inventory management. Key logistics players have started maintaining warehouses in close proximity to OEMs’ plants, and supplying materials on a JIT basis. Related services being provided by large third party logistics service providers (3PLs) include consolidation of materials, packaging, incoming inspection, cleaning, etc (KPMG [19]) JIT at Maruti Udyog Limited:
Maruti was the first Indian company where Japanese Manufacturing culture was implemented from top to bottom. At the Maruti factory in Gurgaon the eight typical wastages at each operational point (over-production, man movement, material movement, idle time of operator, work-in-process, machine availability, waiting time and needless processing) had been measured by observation and even videos. The bottlenecks have been identified and a lot of work has been done to streamline the process. In 1995, when Maruti had 4,800employees, it was producing at the rate of 730 cars a day. Later with 4,500 employees, the plant was producing at the rate of 1,700 cars a day. Simultaneously, the supply chain system is being modified.
A delivery instruction system places orders with the vendors for the next day's production target. Maruti is now working with an inventory of four hours maximum for local items and six days average for imported materials. The inventory to sales turnover ratio, on the scale of 100 in 1999-2000, is now down to 41. Maruti has also started working with its vendors to reduce their cost of production so that its own cost can be reduced. It has also launched a quality enhancement scheme, called the Quality Gate system. Maruti has implemented JIT for some of its major suppliers. Some others are in the process of doing so. There is a stress on quality in this highly competitive industry.
The bargaining power of suppliers of some components is high, because of capacity constraints. This makes them accept only large orders, and therefore makes it difficult for assemblers to implement.
Conclusion
With India emerging as one of the important markets for Automobiles it is imperative for Automobile manufactures to gain production and cost efficiency. JIT would help the companies in achieving this end. The Japanese had perfected the implementation of JIT. Based on research material available it can be concluded that JIT has been successfully implemented in Automobile companies of many other countries such as United States, United Kingdom, China to name a few.
Indian Manufacturing environment has huge prospects of advancement through JIT. Some of the key aspects of JIT important for the Indian industry are Total Quality management [TQM], Cellular Manufacturing, Kanban, Error Prevention to name a few. Some of the reasons for slow implementation of JIT in India can be concluded as High cost of implementation, Lack of support from suppliers, Lack of understanding or conviction in JIT techniques leading to non effective implementation. Also work culture plays a crucial role for JIT. JIT would require a work force that is flexible, can engage in cross training, and would be committed to their work on providing long term employment prospects.
The Major benefits identified by the implementation of JIT are Improved Quality, reduction in inventory, increased productivity and flexibility. There is enough evidence to prove that Indian companies who have implemented JIT [at least partly] successfully have reaped the benefits. The Case study of Tractor assembly factory and Maruti are testimony for the same. Also Mahindra and Mahindra had implemented JIT techniques during the 1990’s to their advantage. To gain the benefit of JIT, Indian Automobile Industry must be willing to modify their procedures and processes
References
- Peter Turnbul, Nick Oliver, Barry Wilkinson (1989), “Recent Developments in the UK Automotive Industry: JIT/TQC and Information systems”, Technology and Strategic Management, Vol 1 No. 2, pp. 09
- Bo Hou, Hing Kai Chan, and Xiaojun Wang (2011), “A Case study of Just-In-Time System in the Chinese Automotive Industry”, Proceedings of the World Congress on Engineering, Vol I
- B Mahadevan, (1997),“Are Indian Companies ready for Just In Time”, Manage Rev, July-September, pp. 85-92
- Vikas Kumar, (2010), “JIT Based Quality Management: Concepts and Implications in Indian Context”, International Journal of Engineering Science and Technology Vol. 2(1), 2010,pp. 40-50
- Dixit Garg, S. G. Deshmukh (1999), JIT Purchasing: Literature review and implications for Indian Industry, Production Planning and Control, Vol 10 , No 3, pp. 276-285
- Vikas Kumar, Dixit garg, N P Mehta(2004), “JIT Practices in Indian Context: A survey”, Journal of Scientific and Industrial Research, Vol 63 ,pp. 55-662
- Chandra, Kodali (1997),”Implementation if JIT manufacturing System: An Overview”, Productivity, Vol 38, pp. 312-321 8) Haritha Saranga, Arnab Mukherji & Janat Shah, “Determinants of Inventory Trends in the Indian Automotive Industry: An Empirical Study”, Indian Institute of Management Bangalore, India
- Sultan Singh, Dixit Garg (2011),” Comparative analysis of Japanese Just-in-Time Purchasing and Traditional Indian Purchasing System”, International Journal of Engineering Science and Technology (IJEST), vol. 3, no. 3
- Sultan Singh, Dixit Garg ,” Attributes in JIT Purchasing”, Akgec Journal Of Technology, vol. 2, no.
- Jocclyn Drolet, Rene Gelinas, Real Jacob (1996),” Just-in-Time purchasing and the partnership strategy”, European Journal of Purchasing & Supply Management , vol. 2, no. 1, pp. 39-45 12) B. Mahadevan (2010),” Operations Management : Theory and Practice”
- Frost & Sullivan , (2010), “Cellular Manufacturing makes Plant Operations Lean and Flexible”, http://www. frost. com/prod/servlet/press-release. pag? docid=202718293
- Timothy J. Greene , Randall P. Sadowski ,” A review of cellular manufacturing assumptions, advantages and design techniques”
- Shishir Bhat, (2008), “Cellular manufacturing-the heart of Lean manufacturing”, Advances in Production Engineering and Management, Vol 3 , No 4
- B. Vijaya Ramnath,C. Elanchezhian and R. Kesavan, (2010) Application of kanban system for implementing lean manufacturing (a case study), Journal of Engineering Research and Studies, Vol. I/Issue I/July-Sept. 17) Kee-hung Lai and T. C. E. Cheng , “Just-in-Time Logistics”
- Ken alternburg, Debbie griscom, Jack hart, Frank smith, Gary wohler [1999],” Just-in-time logistics support for the Automobile industry”, Production and inventory management journal—second quarter
- KPMG (2006), “Indian Automotive Supply Chain KPMG”
- http://amitsinghbisht. articlesbase. com/marketing-articles/maruti-udyog-limited-managing-competition-successfully-723310. html
Cite this Page
Jit in Indian Automobile Industry. (2018, Jan 10). Retrieved from https://phdessay.com/jit-in-indian-automobile-industry/
Run a free check or have your essay done for you
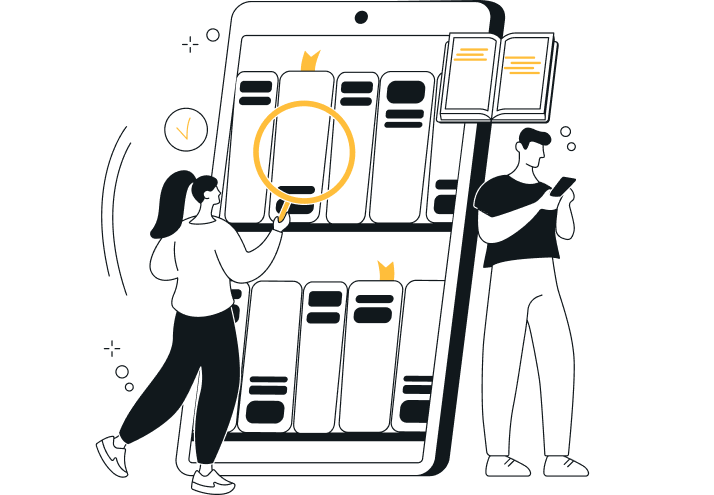