Historical Background and Status
Historical background and status of textile engineering industry By: S. Chakrabarty Preamble Industrial Revolution in U. K. during 1750 - 1850 gave birth to Textile Machinery. The dominance of India in the field of cotton textiles produced by very skilled manpower was disturbing the British. Systematic development of textile industry with spinning and powerloom machinery was initiated in Lancashire and Manchester to discourage the Indian weavers. Rest is however known to everybody how the machinery industry was developed and nurtured by the respective Governments in the UK and later by Germany and Switzerland followed by others in Europe.
In India, machinery manufacture started in the 50s, continued and progressed during 60s & 70s and thereafter. The Government policy to ban expansion of the organized weaving sector during late 60s created/ supported the decentralized powerloom sector. Too much of importance to handlooms and low level technology power looms in the subsequent years, keeping a large list of reserved items for handlooms, throttled the mill industry which lost its initiative for creativity as well as production for the masses. Low level of production in handlooms and low quality production in powerlooms made us uncompetitive in the subsequent years.
The Government’s regulative pressures on the Mill Industry continued to play havoc for the weaving industry till the introduction of 1985 Textile Policy and finally revolutionary Industrial Policy in 1991. Development and technology growth in the TEI The Textile Engineering Industry (TEI) during the late 60s, 70s and 80s had received some Government support in the form of foreign collaboration approvals, import assistance by way of phased manufacturing programme and concessional customs duty certification for imported parts and components for manufacture of specified textile machinery.
Order custom essay Historical Background and Status with free plagiarism report
Import duty on components and parts in general was very high at 85% excluding CVD and not conducive for indigenous development. The concessional duty on imported parts, components etc. mentioned above did help the Industry. The then Government’s policy was also supportive that no import of machinery was allowed if there was adequate indigenous production. The local textile industry therefore had no choice but to buy the Indian machinery. This policy helped the TEI to develop and manufacture spinning machinery in the country of the desired quality and quantity. There was no competition from outsider.
Internal competition among various players made the development easier and faster. Foreign manufacturers had no choice but to enter into collaborations with local manufacturers. This happened not only in spinning but also in processing machinery. The following collaborations are worth mentioning: Sr. No. 1 2 3 4 5 6 7 8 Names of Foreign Collaborators M/s. Textile Machinery Makers Ltd. U. K. , Platt Bros. , U. K. M/s. Whitin Machine Works, U. S. A. M/s. Howa, Japan M/s. Zinser, Germany M/s. Marzoli, Italy M/s. Hipi Suiza (Suisse) S. A. , Switzerland M/s. Rieter, Switzerland M/s. Schubert & Salzer, Germany Names of Indian
Manufacturers M/s. National Machinery Mfrs. Ltd. , Bombay* M/s. M M C. , Calcutta M/s. Texmaco, Calcutta* M/s. Texmaco, Calcutta* M/s. M M C, Bangalore* M/s. Indequip Engineering Ltd. , Ahmedabad M/s. LMW, Coimbatore M/s. New Standard Engg. Items Produced Spinning - Cards, Draw Frame, Speed Frame, Ring Frame Spinning – Carding Engines and RH Can Fed Inter Frames Spinning – Flat Revolving Carding Engines, Draw Frame, Speed Frames Spinning – Narrow Gauge Ring Frame Spinning – Entire Range Spinning – Ring Frame Spinning - Entire range Spinning - Blow Room, Cards, 9. M/s. Zinser, Germany M/s. Trutzschler, Germany M/s. Toyota, Japan 10 11 2 M/s. Suessen, Germany * Presently not in operation Co. Ltd. , Mumbai* M/s. Padmatex Engg. , Baroda* M/s. Trumac, Ahmedabad M/s. Kirloskar Toyoda Textile Machinery Pvt. Ltd. , Bangalore M/s. Suessen Asia, Pune Draw Frames Spinning - H. S. Draw Frame Spinning - Blow Room, Cards, Draw Frames Spinning – Ring Frame Spinning - Ring Frame Due to acute and long recession in the Textile Industry, initial higher import content coupled with high rate of import duty, non-transfer of latest technology under collaboration agreements leading to import of machinery etc. , the following Indian Companies were closed down during 80s and early 90s.
These are M/s. MMC, Kolkata and Bangalore; M/s. Texmaco, Kolkata; M/s. Indequip Engineering, Ahmedabad; M/s. New Standard Engg. Co. Ltd. , Mumbai; M/s. Mafatlal Engg. Co. Ltd. Mumbai; M/s. Textool Co. Ltd. , Coimbatore; M/s. Jeetstex Engg. Ltd. Coimbatore etc. while M/s. LMW, M/s. Trumac, M/s. Zinser India, M/s. Suessen Asia, M/s. Kirloskar Toyoda could manage to stay in production. Why we are better in spinning machinery? There was Government support by way of• • • Restricted import of spinning machinery - virtually no import of spinning machinery of the same technology available indigenously was allowed.
No import of second hand spinning machinery was allowed. Import duty concession on raw materials, parts, components & accessories for production of specified machinery as the import duty in general, was very high. Besides, competition among the machinery manufacturers resulted in production of better quality machines. Reasons for non-development in the Weaving Machinery Sector While the Textile Engineering Industry took up manufacturing of Spinning machinery in full swing with the adequate Government's supportive measures mentioned above, the same did not happen in case of weaving machinery.
During 60s (prior to 1970) the Industrial Policy prohibited the organized mill sector to expand their weaving capacity. This was perhaps to support employment generation in the villages by the decentralized and dispersed handloom sector. It was due to this wrong policy, the unauthorized powerloom clusters started gaining grounds. Even many of the handloom clusters started converting into powerlooms. Since the domestic demand for fabrics was growing fast due to the population growth, the powerloom sector in different parts of the country started growing fast while the handloom sector started shrinking in reality. The fact is still not accepted by the Government). Today, there are over 20 lakh powerlooms but handlooms, may not be more than 8 lakh, if not less! During 70s the organized mill sector was allowed to replace ordinary powerlooms by automatic looms and shuttleless looms on 4:1 basis. However, compulsory manufacture of controlled cloth by the mills sector dampened the spirit of the mills sector. Controlled cloth scheme was done away with during 80s. Expectation of a good demand due to replacement policy prompted the manufacture of automatic looms by M/s.
Cimmco, Gwalior in collaboration with M/s. Sakamoto, Japan and M/s. Mafatlal Engineering Co. in collaboration with M/s. Ruti, Switzerland during 70s. In the late 70s M/s. Lakshmi Automatic Loom Works Ltd. (LALW) started manufacturing Ruti `C’ Type of automatic loom in collaboration with M/s. Ruti, Switzerland. M/s. Cimmco as well as M/s. Mafatlal Engineering Co. tried to manufacture shuttleless looms in collaboration with M/s. Dornier, Germany, Toyoda, Japan and M/s. SACM, France respectively during early 80s. M/s. LALW also started making shuttleless rapier and airjet looms during 80s.
During 80s, the powerloom population which was hardly 7 lakh had grown to more than 10 lakhs. The policy of scrapping of powerlooms of the mill industry after replacement or closure failed miserably, all these powerlooms found their way to the decentralized sector. The Government had no option but to regularize all unauthorised powerlooms due to political pressure after announcement of 1985 Textile Policy and subsequent Textile Control Order 1986, doing away with the age old powerloom permit system. The textile strike during 1980s crippled the Textile mill industry in Mumbai and Maharashtra.
During this period the composite structure of the mill industry broke almost completely. While the spinning sector prospered with the modern machinery, the number of working looms in the organized mills sector shrunk considerably and most of the mills found it profitable to close down their weaving section due to bad market condition, high cost of labour, low productivity and tough competition from the powerloom sector. As a result, there was practically no demand for the shuttleless looms manufactured by the two Companies mentioned above which prompted them to close down their shutters one by one.
In the meantime, due to the pressure from the decentralized powerloom sector the Government was forced to allow import of second hand weaving machinery which added to the woes of indigenous manufacturers of shuttleless looms. M/s. LALW also had to discontinue the production of shuttleless looms subsequently. During 80s and upto 1991 there was protective market for spinning and processing machinery but not for the weaving machinery due to high production cost and import of second hand looms. Initiatives discouraged after liberalization
The Industrial Policy announced in 1991 liberalised the Industry in general to a considerable extent. The market became open to the foreign manufacturers and there was tough competition. The spinning machinery makers came of age technologywise and capacitywise and there was also very high demand for spinning machinery. The weaving machinery could not prosper due to the onslaught of import of second hand machinery. There was no restriction on import of second hand weaving machinery before and after 1991. After 1992, there was no support of the Government either for development of weaving machinery or any other textile machinery.
In this regard, the only commendable fact was that we became self-sufficient in Weaving Preparatory Machinery viz. High Speed Sectional Warping, Direct Warping and Sizing matching with world class technology. M/s. Rabatex Industries, Ahmedabad; M/s. Prashant Gamatex Pvt. Ltd. , Ahmedabad, M/s. Amritlakshmi Machine Works, Mumbai and M/s. Jupiter Engineering Co. , Ahmedabad are the most reputed domestic manufacturers. This could happen because there was less import of second hand machinery and the cost differential between domestic and imported machinery was large and the machines were custom built.
The indigenous shuttleless looms (older technology) which have been developed during the late 90s and early 2000, however, could not find a good market due to the adverse policy of the Government i. e. import of second hand shuttleless looms under concessional duty and also under concessional rate of interest under TUF. The situation continues. However, indigenous machinery manufacturers viz. M/s. Aalidhra Weavetech Pvt. Ltd. , Surat; M/s. Bhavin Sales Corporation, Surat; M/s. Dynamic Loom Mfg. Co. , Ahmedabad; M/s. Dinkier Sokerjee Machines, Surat; M/s. Friends Engg.
Works, Panipat; M/s. Himson Textile Engg. Inds. Pvt. Ld. ; Surat; M/s. Industrial Engg. Works, Bangalore; M/s. Lakshmi Automatic Loom Works Ltd. , Coimbatore; M/s. Laxmi Textile Stores, Ahmedabad; M/s. Lifebond Machines Pvt. Ltd. , Surat etc. have developed and are producing crank beat up type shuttleless looms with a speed between 450 – 500 mpm. All latest generation shuttleless looms i. e. Airjet, Waterjet, Projectile & Rapier of European and Japanese origin are high speed, high tech, high productive and energy efficient running at a speed of 500 rpm and above.
This machinery, though at a higher cost, is economically viable due to its quality and productivity, cost of fabric per meter being less than second hand machinery. Since last 4/5 years, all new large textile units as well as existing reputed textile units expanding capacity had been importing these kinds of machinery to make them commercially viable, e. g. Alok Industries, Welspun, GHCL, Vardhman Group, Century, Raymonds, etc. Therefore, machinery, if made/developed indigenously need to be cost competitive in all respects and cost of production per meter of fabric should be same or less with equivalent quality standard.
Then only the manufacturing would be viable and accepted by the Mill Industry/ Organized Sector. Unless there are disincentives for second hand machinery, there is no hope that the decentralized powerloom sector would go in for new machinery. Processing & Finishing Machinery Sector The history of the processing machinery manufacturing sector was somewhat different. During 70s and 80s there were a number of foreign collaborations : M/s. Mather & Platt, U. K. M/s. Reggiani, Italy M/s. Stork, Holland M/s. Gerber, M/s. Menzel and M/s. Eduard Kusters, Germany
Mather & Platt (I) Ltd. * SBM Engg. * ATE (Stovec/Stormac*) Calico Indl. Engineers* M/s. Artos & Benninger, Germany M/s. Famatex, Germany M/s. Obermeaier, Germany M/s. Toshin Kogyo, Japan * Presently not in operation T. Maneklal* Famatex India Ltd. * Dalal Engg. Star Indl. Engg. * Some Companies developed machinery by copying the imported technology viz. M/s. Harish Textile Engineers, M/s. SM Engg. etc. As mentioned earlier, composite structure of the textile industry broke in Europe during 70s. The same happened in India during 80s. This affected the processing sector.
While spinning industry became more organized, competitive and export- worthy, the weaving and processing sectors became uncompetitive, decentralized and export unworthy. Since the Government encouraged low technology for the weaving sector (handlooms and ordinary powerlooms), the organized weaving sector in the mill industry could not come up. Similarly, the decentralized processing sector, which started with second hand machinery from the composite mill industry, did not modernize the units in course of time. The domestic manufacturers which had ollaboration prior to 1991 could not continue with their collaborators after 1991 as the market became open and the foreign manufacturers found it easier to market their machines in India rather than making the same under collaboration. During 80s as well as 90s strenuous efforts were put in by some of the Companies to develop machinery by way of re-engineering. Some of them became successful. However, some of the Companies had to close down their shutters due to tough competition in the open market after 1991. Many manufacturing units came into existence to produce low technology cheap machinery to bridge the gap between demand and supply.
This had resulted in manufacture of poor quality machines and poor quality processing of textiles thereof. The encouragement given by the Government to the hand processing sector was misused and low technology prevailed. The prominent processing machinery makers who developed quality machines during 80s and 90s were: 1. M/s. Calico Indl. Engineers, Mumbai* 2. M/s. Dalal Engg. Pvt. Ltd. , Mumbai 3. M/s. Devrekha Engineers, Surat 4. M/s. Harish Textile Engineers Ltd. , Mumbai 5. M/s. Mather & Platt (I) Ltd. , Mumbai* 6. M/s. Primatex Machinery Ltd. , Mumbai* 7. M/s. SLM Maneklal Ind. Ltd. , Mumbai* 8. M/s.
SM Energy & Electronics, Mumbai 9. M/s. Standard Fabricators (I) Pvt. Ltd. , Mumbai 10. M/s. Stovec Industries Ltd. , Ahmedabad 11. M/s. Texprint Engineers Pvt. Ltd. , Ahmedabad * Presently not in operation In the latter half of 90s again saw acute demand recession from the Textile Industry which continued upto 2002. During this period the Textile Engineering Industry started looking beyond the domestic demand. Export which was never more than Rs. 100 crore until 1988-89 started increasing and reached the level of Rs. 406 crore during 2002-03. There were exports of spinning as well as processing machinery.
Some of the manufacturers could compete with the European manufacturers in processing machinery abroad with their high quality machines. Improved Demand The demand for textile machinery started picking up slowly after 2002 as the Technology Upgradation Fund Scheme became popular by then. The Textile Industry was also expecting a better market after the st liberalized Quota Free Regime under WTO from 1 January, 2005. Major demand for machinery started after 2004 which has prompted the Textile Engineering Industry to increase its production from the level of Rs. ,341 crore during 2003-04 to Rs. 2,780 crore during 2006-07. However, this happened mainly in spinning machinery and weaving preparatory machinery and to some extent in weaving and processing machinery. The weaving and processing machinery sectors though increased their capacity to a considerable extent, has a long way to go. The processing sector started competing with foreign manufacturers since 1991 though sporadically. They have improved their technology and their machines are now capable of producing fault free processed fabrics in short as well as continuous lots.
The domestic demand for such machinery has also increased. M/s. Dhall Enterprises & Engineers Pvt. Ltd. , Ahmedabad, M/s. Harish Enterprises Pvt. Ltd. , Mumbai, M/s. Tex-Fab Engineers (India) Pvt. Ltd. , Navi Mumbai produced continuous dyeing plants with latest technology for long length of fabric processing which are running successfully in the mills. The following manufacturers have exported their processing machines and earned a good name: 1. 2. 3. 4. 5. 6. 7. M/s. Dalal Engineering Pvt. Ltd. , Mumbai M/s. Devrekha Exports (Bhagyarekha Engineers Pvt. Ltd. ), Surat M/s.
Dhall Enterprises & Engineers Pvt. Ltd. , Ahmedabad M/s. Harish Enterprise Pvt. Ltd. , Mumbai M/s. Kusters Calico Machinery (P) Ltd. , Vadodara M/s. Lakshmi Card Clothing Mfg. Co. Pvt. Ltd. , Coimbatore M/s. Yamuna Machine Works Pvt. Ltd. , Mumbai These manufacturers are in a position to make many high quality processing machines and compete with foreign manufacturers. Knitting/Hosiery Machinery Knitting/Hosiery Industry as well as Garment Industry was reserved for the small scale sector. Both these sectors thrived initially with imported second hand machinery.
Both Woven Garment and Hosiery Garment put together the total export of the country was only Rs. 5 crore during 1970-71. The exports increased to Rs. 500 crore in 1980 and today it is above Rs. 17,000 crore, thanks to the removal of quota shackles under WTO, implemented by the Government couple of years back. Decentralised character of the Garment industry did not enthuse the TEI to take up the manufacture of knitting machinery. As such this sector remained neglected altogether. Some efforts were made to manufacture knitting machinery by two Companies viz. M/s.
Lakshmi Automatic Loom Works Ltd. , Coimbatore and M/s. Himson Textile Engineering Industries Pvt. Ltd. , Surat in late 80s. However, after liberalization of the Industrial Policy in 1991, imported machines became cheaper technology wise than the Indian machines due to which obviously there was no demand. Therefore, manufacture of knitting machinery had to be discontinued. Testing & Monitoring Equipments Sector As regards the Testing & Monitoring equipments are concerned, the textile industry was dependent on imported testing and monitoring equipments in 60s and early 70s.
The Textile Engineering Industry started developing such testing & monitoring equipments in the late 70s and today all kinds of high quality latest generation testing and monitoring equipments are being manufactured in the country. Some of the items are: • • • • • Air Jet Weaving Machine Controller Centralised Computerised Operation of Group of dyeing Machines with Dyeing Data Management Software Package Fully Automatic High Volume Fibre Tester for Length, Strength, Micronaire, Colour, Trash and Maturity module Multi-Channel Pre-Set Yarn Length Indicator & Controller for Winding/Texturising/TFO Machines with Software Package
Yarn Evenness Tester Some names of the Companies manufacturing different categories of such instruments are under:• • • • • • Paramount Instruments Pvt. Ltd. Pioneer Instruments & Innovations Premier Evolvics Pvt. Ltd. Semitronik Instruments Tex Lab Industries Thymas Electronic Pvt. Ltd. Growth of the Parts & Accessories Sector The growth of the textile industry along the length and breadth of the country initiated the manufacture of parts and accessories for their machinery. Today, barring a few critical items of equipments and accessories lmost all kinds of parts and accessories of high quality are manufactured in the country. The number of such manufacturers could be around 800. Some of the important items manufactured here are: Blow Room beaters, card clothing, cross-roll attachment for cards, top rollers for high speed draw frame, flyers for speed frames, rings, spindles, inserts, cots and aprons and variable drives for ring frame, production of monitoring data in spinning and weaving online quality checking systems, cloth guides, web straighteners in processing, etc. etc.
The TEI not only fulfills the demand for spares from the domestic textile industry but also exports its products to Asia, Africa, the Middle East, Far East, Europe, America and other countries as well. The following table shows data on production of Textile Machinery Parts & Accessories during the last 15 years: Year 1985-86 1990-91 1999-2000 2004-05 2006-07 Rs. in Crores 83. 43 208. 59 288. 79 276. 44 339. 68 Synthetic Yarn and Fabric Processing Machinery Sector Synthetic weaving sector of the textile industry which was scattered in different parts of the country in early 70s became localized in Surat, Bhiwandi, Belgaum.
During 80s and 90s the synthetic sector was dominantly established in and around Surat, Gujarat. This simultaneously necessitated the development of synthetic yarn and fabric processing machinery. As a result the Textile Engineering Industry located in and around Surat and Mumbai developed draw texturising machines, draw twisters, two-for-one twisters for filament yarn, zero-twist filament sizing machines, rewinders, precision cone winding machines, etc. etc. More successful manufacturers are M/s. Himson Textile Engineering Industries Pvt. Ltd. , M/s. Aalidhra Textile Engineers Pvt. Ltd. Meera Industries, etc. The synthetic mechanical processing machinery was being imported during 70s and 80s. However, with the development of such machinery indigenously, we are not only catering to the domestic demand but also exporting the same. More and more developments are taking place due to the demand for such machinery. Conclusion Thus the Textile Engineering Industry could develop all types of textile machinery except garment machinery, high speed sophisticated knitting machinery, high speed shuttleless loom (rapier and air jet) and some of the latest generation processing and finishing machinery.
The reasons for not developing these machinery have been categorically explained in the foregoing paras. What the TEI expects and aspires Under the above background it is felt that there is a real need to develop and manufacture all kinds of textile machinery in the country as per the existing and expected demand. Government should encourage these efforts and should come forward to help this Rs. 3,000- 4,000-crore capacity industry in a comprehensive and systematic manner with short and long term policy measures. It should take note of the developments of textile machinery made by China during the last 10 years.
What China did? 1. Forced the foreign manufacturers to start manufacturing their brands in China by not allowing the import of machines from abroad. 2. Financed the domestic manufacturers for setting up the complete plants with large capacities. 3. No second hand machinery import 4. Incentives given for replacement of old machinery with new machinery. Incidentally, it may be mentioned that China had 6 lakhs ordinary powerlooms/automatic looms prior to 2002. Today, they have shuttleless looms (2, 50, 000 to 3,00,000 approx. ). There may be few ordinary powerlooms in villages and automatic shuttle looms in some corners.
No estimate of such looms is available. They have installed large machinery manufacturing capacities and are also exporting all kinds of textile machinery at a cheaper price. Therefore, the following measures are needed to improve the present condition of the Indian TEI A) Policy Measures • • Scheme for Modernisation, technology upgradation and productivity advancement of the Textile Engineering Industry (TEI). The interest remission under the scheme should be 5% with one time 10% Capital Subsidy over & above interest remission (Similar Schemes are available for the Textile Industry).
Scheme to support Research & Development. o o • • • • • • • Suitable capital grants and annual recurring grants for the existing R Centre at IIT, Powai, Mumbai. Suitable capital grants for the R Institutions located at Surat, Ahmedabad, Coimbatore, Delhi, Panipat and Ludhiana willing to take up R for textile machinery. Capital grant for indigenous development of machinery to the new projects as well as existing projects which got delayed due to lack of funds. Tax break/holiday for the manufacture of High Speed Shuttlelesss Looms/High-tech processing and finishing machinery for a period of five years.
To allow import of complete sophisticated machinery in CKD/ SKD condition at concessional rate of import duty for a minimum period of three years without any restrictions for manufacturing textile machinery under collaboration/joint venture/import of designs and drawings or by way of reengineering. Ban import of machinery where similar technology machines are available indigenously e. g. shuttleless rapier loom “crank beat-up type”, water jet Looms (800 rpm) etc. Import of textile machinery in second hand condition should not be allowed under the Technology Upgradation Fund Scheme/20% CLCS Scheme.
Ban on import of second hand shuttleless looms with weft insertion rate less than 800 mtrs. per minute. Revival of TIFAC scheme for development of textile machinery with 90% loan component and softer rate of interest of 3%. B) Fiscal Measures • • • • • • Reduction of excise duty from 14% to 8% Excise duty on parts, components and accessories of the machines be reduced to 8%. Maintaining the floor level customs duty on textile machinery at 7. 5% without any exemptions Uniform rate of customs duty for complete machinery and raw materials, parts, components & accessories
Uniform treatment to the domestic suppliers of machinery to EPCG license holders. 150% weighted Income Tax deduction for R expenditure made by the Textile Engineering units. If the above measures are taken seriously, the TEI aspires to make available modern machinery and equipment both in quantum and quality to meet the future needs of the textile industry at short delivery periods coupled with effective and prompt after-sales-service. About the Author: The author is the Secretary of The Textile Machinery Manufactures Association.
Cite this Page
Historical Background and Status. (2017, Apr 18). Retrieved from https://phdessay.com/historical-background-and-status-of-textile-engineering-industry/
Run a free check or have your essay done for you
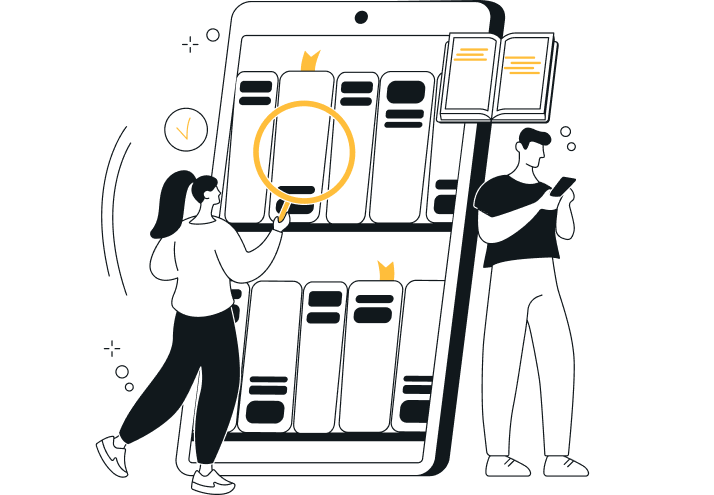