Enterprise System Implication
Analyzing Enterprise Resource Planning system implementation success factors in the Engineering-Procurement Construction & Commissioning Industry
Introduction
Back Ground Enterprise Systems (ES), also called Enterprise Resource Planning (ERP) systems, are among the most important business information technologies to emerge in the last decade. While no two industries Enterprise Systems are the same, the basic concept of Enterprise Systems is focused mainly on standardization, synchronization and improved efficiency.
Order custom essay Enterprise System Implication with free plagiarism report
ERP is basically the successor to material resource planning (MRP) and integrated accounting systems such as payroll, general ledger, and billing. The benefits of Enterprise Systems are very significant: coordinating processes and information, reducing carrying costs, decreasing cycle time and improving responsiveness to customer needs [ (Davenport, 2000) ]. MRP is limited to controlling the flow of components and materials, and does not lend itself to more complete production control and coordination.
The next generation of manufacturing software, known as MRP II, was developed to address this shortcoming and to further integrate business activities into a common framework. MRP II divides the production control problem into a hierarchy based on time scale and product aggregation. It coordinates the manufacturing process, allowing a variety of tasks such as capacity planning, demand management, production scheduling and distribution to be linked together. [ (Mendelson, 2000) ] Conventionally, the EPC firms have been faced with the predicament of handling the mega projects.
The issue always is to keep these multimillion dollar projects on schedule, under budget, and safe with the quality specified by the end user. Although the EPC firms are one of the leading contributors to the development of region, yet it faces the challenges of most highly fragmented, inefficient, and geographically dispersed industries in the world. In recent times the emergence of ERP Software has helped such firms to overcome the issues. EPC Companies in the present world are expanding day by day, moving across the globe to open new avenues of business and expand.
These companies also seek diversification in their business and continuously changing and adopting technology to keep pace and maintain their competitive advantage in their prior and newly adopted business sectors. Managing these huge companies need special support of Information Technology to keep a track of activities and handle them accordingly. Companies like BHP Billiton, Nestle etc. have implemented ERP systems around the globe wherever they operate. In our part of the world i. e.
Pakistan companies such as Packages, FFC, Raftan Maize and Descon etc. have all implemented ERP systems to handle their business in a more efficient manner with their growth locally and globally. ERP is a software architecture that facilitates the flow of information among the different functions within an enterprise. Similarly, ERP facilitates information sharing across organizational units and geographical locations. It enables decision-makers to have an enterprise-wide view of the information they need in a timely, reliable and consistent fashion.
ERP provides the backbone for an enterprise-wide information system. At the core of this enterprise software is a central database which draws data from and feeds data into modular applications that operate on a common computing platform, thus standardizing business processes and data definitions into a unified environment. With an ERP system, data needs to be entered only once. The system provides consistency and visibility-or- transparency across the entire enterprise. A primary benefit of ERP is easier access to reliable, integrated information.
A related benefit is the elimination of redundant data and the rationalization of processes, which result in substantial cost savings. [ (Mendelson, 2000) ]. Problem Statement Unfortunately for Nestle USA, they did not heed the failures of others. Throughout the implementation, Nestle USA made several large mistakes that almost doomed the project. When the project began a team of 50 top executives and 10 senior IT professionals was assembled to develop a set of best practices for all Nestle USA divisions.
The goal was to develop these best practices for all functions of the organization. By the time the implementation began in 1999 Nestle already had problems with its employees’ acceptance of the system. Most of the resistance met by the project team was traced back to the fact that “none of the groups that were going to be directly affected by the new processes and systems were represented on the key stakeholder’s team”. This was only the start of Nestle USA’s problems. By early 2000, the implementation had turned into a disaster.
Employees did not understand how to use the new system and did not understand the new work processes they were being forced to adopt. Divisional executives were just as confused as their employees as they had been left out of the planning and development of the new system and were less than willing to assist in straightening out the mess that had developed. The result of this was that morale plummeted and turnover skyrocketed [ (Dieringer, 2004) ]. Nestle learned the hard way that an enterprise-wide rollout involves much more than simply installing software. When you move to SAP, you are changing the way people work," Dunn says. "You are challenging their principles, their beliefs and the way they have done things for many, many years. " [ (Worthen, 2002) ] While it’s true that successful implementation of an enterprise resource planning system is a task of Herculean proportions, it’s not impossible. If your organization is to reap the benefits of ERP, it must first develop a plan for success. But prepare to see your organization reengineered, your staff disrupted, and your productivity drop before the payoff is realized.
In a recent survey, information technology managers identified three primary reasons for the failure of all IT-related projects: poor planning or poor management (cited by 77 percent), change in business goals during the project (75 percent), and lack of business management support (73 percent). Since ERP is an IT-related project, the above are valid reasons for explaining ERP implementation failures. For managers who have struggled with incompatible information systems and sub-optimum operating practices, the promise of ERP to solve the problem of business integration is enticing.
But the price of securing the benefits of ERP may be high. The cost of a modest ERP implementation can range from $2 million to $4 million, depending on the size of the organization and the specific products and services purchased from vendors. The cost of a full-blown implementation in a large organization can easily exceed $ 100 million. [ (Umble, 2002) ] Research Objectives The objective of this research is to identify factors that influence ERP implementation, providing factors associated with the success of ERP systems in EPC firms.
The research brings to limelight the factors associated with the success or failure of ERP implementation, and scrutinize these factors according to the level of significance in affecting the success of ERP systems. The primary research objectives: 1) Identify the factors responsible for the success or failure of ERP implementation? a. Identify factors that can motivate users to adopt the ERP System and make the project successful. b. Also to discuss relationship between these factors. ) What marks the success of an ERP implementation and how to avoid the failure of implementation? Literature Review EPC Companies such as Descon, Hyundai, Bechtel, Petronas and Foster Wheeler etc. face frequent challenges of managing project schedules, budgets, safety, and quality to meet requirements provided by the end user / customers across the globe. The proper utilization of internal and external resources is essential if construction companies are to make the best business decisions, maximize business goals, and survive in the competitive environment (Shi, 2003).
Recently, an appreciable number of major EPC companies decided to implement enterprise resource planning (ERP) systems, an integrated information technology IT solution, to better integrate various business functions and resources, particularly those related to project accounting procedures and practices (Boo Young Chung, 2008). Enterprise resource planning systems, also called enterprise systems ES are among the most important business information technologies that emerged during the last decade.
While no two industries’ ERP systems are the same, the basic concept of ERP systems is focused on standardization and synchronization of information, and as a result, improved efficiency. The benefits of ERP systems include coordinating processes and information, reducing carrying costs, decreasing cycle time, and improving responsiveness to customer needs (Davenport, 2000). Major EPC firms are starting to recognize the benefit of ERP systems, however, they are often hesitant to invest and adopt these systems due to high cost and risks associated with ERP system implementation.
Many factors must be considered for successful implementation, but construction firms have little to guide them in identifying key success factors (Boo Young Chung, 2008). The ERP Systems are not limited to just financial and accounting, they have the whole system embedded in them. The ERP modules such as SAP comprise of modules for Supply Chain Management, Human Capital Management, Material Management, Finance etc. The main modules of an ERP System are as follows
- Finance & Controlling (FI & CO)
- Quality Management (QM)
- Material Management (MM)
- Human Capital Management (HCM) .
- Project Systems (PS)
- Production Planning (PP)
- Sales & Distribution (SD)
- Treasury (TR)
- Plant Maintenance (PM)
- Customer Relationship Management (CRM)
Currently, many construction firms have implemented their ERP systems adopting a best-of-breed approach in which separate software packages were selected for each process or function rather than using full packages of major ERP vendors (Tatari, 2007). EPC Companies selected different modules like material management, quality management from major ERP vendors and clubbed together with their customized software.
The customization of these ERP Systems have been a major issue as all companies try to mend these modules in to their own processes which makes the implementation very difficult. For this reason, regardless of the agreed upon implementation approach, any integrated corporate system in which all the necessary business functions are pieced together for the company is considered the ERP system in this study. The main reason of using this approach is that construction processes are less standardized than manufacturing: each project has a different owner, is managed by a different project team, requires different specifications, etc.
Therefore, success or failure factors and their significance for ERP implementation in the construction industry may be different from those in the manufacturing industry. (Boo Young Chung, 2008). We can classify ERPs benefits as:
- improvement of information flow between sub-units by standardization and integration of activities,
- centralization of administrative activities such as accounts payable and payroll,
- reduction of IS aintenance costs and increased ability to deploy new IS functionality,
- transformation enablement from inefficient business processes to accepted best-of-practice processes (Ayyub Ansarinejad1, 2011)
Variables in the ERP Model The main variables in ERP Success model are
- Output
- Job relevance
- Image
- Result demonstrability
- Compatibility
- System Reliability
- Internal Support
- Function
- Consultant Support
- Subjective Norm
- Perceived Usefulness
- Perceived ease of use
- Intention to use
- ERP Benefits
- Project Success / progress
- Project success / quality
Bibliography
- Ayyub Ansarinejad1, M. -S. A. (2011). Evaluating the critical success factors in ERP Implementation using Fuzzy AHP approach. Internation Journal of Academic Reserach , 65-80.
- Boo Young Chung, M. J. (2008). Anaylzing Enterprise Resource Planning System Implementation Factors in the Engineering-Construction Industry. Journal of Computing in Civil Engineering , 373-382.
- Davenport, T. (2000). Mission Critical : Realizing the promise of Enterprise Systems. Harvard Business School Press Boston . Dieringer, D. S. (2004). ERP Implementation at Nestle.
- Mendelson, H. (2000). ERP Overview. Graduate School of Business, Stanford University, Stanford, CA . Shi, J. J. (2003). Enterprise Resource Planning for Construction Business Management. Journal for Construction Engineering and Management , 214-221.
- Tatari, O. C. -L. (2007). Current state of construction enterprise information system: Survey Research. Construction Innovation , 310-310.
- Umble, E. J. (2002). Avoiding ERP Implementation Failure. Industrial Management, Industrial Management Society , 25-33. Worthen, B. (2002, May 15th). Nestle's ERP Odyssey.
Cite this Page
Enterprise System Implication. (2018, Oct 10). Retrieved from https://phdessay.com/erp-system-implication/
Run a free check or have your essay done for you
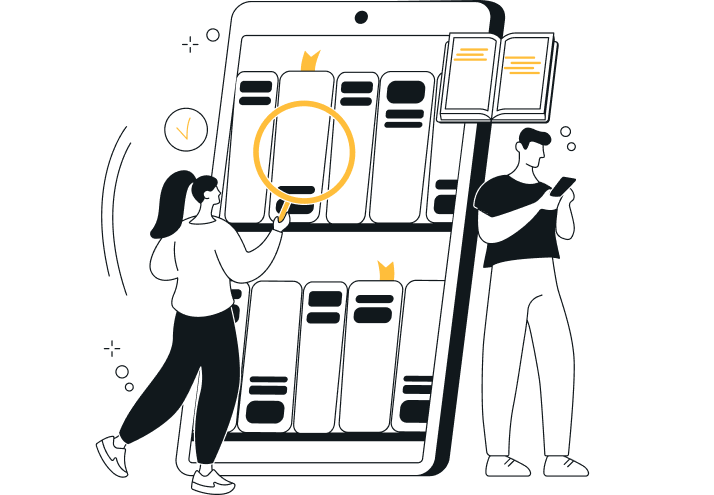