Categories Of Carbon Steel Their Compositions Engineering Essay
'STEEL ' is used for assorted metals of Fe. These vary from each other depending on the content and % of stuff added to the Fe base solution. On must maintain an of import factor in head, all steels contain a % degree of C + Manganese + Silicone + Sulpher. By increasing C to establish solution the stuff will increase strength and hardness therefore improves drastically the harden-ability. On the other manus C reduces the capableness of weld-ability and increases crispness. Several types of steels exist in our markets, the most common being ; field C, chromium steel, alloyed and tool steel.
Carbon steel is one of the largely used steels in several industries. As explained antecedently, its belongingss are dependent largely on the % of C added but the other elements have minor influence excessively. One of import factor sing Plain Carbon Steel, is that this is a type of steel incorporating up to 1.5 % of C. One must foreground that most of the C add-ons in C steel are less than that of 1 % . Some applications of these steels are structural beams, auto frames, etc. ( Capudean, 2003 ) ( Iron Making & A ; Steel MAking, 2008 ) ( Jr. , 2007 )
Harmonizing to the 'Steel Classification Society ' , Carbon steels are sub divided into four chief classs ; -
Order custom essay Categories Of Carbon Steel Their Compositions Engineering Essay with free plagiarism report
Low Carbon Steels /Mild Steels ; these steels have less than 0.25 % of C, and these are the largely used class of C steels. Normally this type being unresponsive to heat interventions, intended to organize a martensitic construction, beef uping is achieved by cold working the portion due to low C content. These are really easy to organize steels with accomplishing popularity largely for not high strength applications. Some belongingss are ; Very tough, inexpensive sing costs ( least expensive to bring forth ) , they are easy machined ( more ductile than high C steels ) and welding belongingss are besides really good. Typically these have 275MPa - output strength, 450 - 550 MPa - tensile strength, and 25 % EL - Ductility. For such a ground, these are normally used in applications as Bridgess due its ability to deform under burden and return to its original. ( B ) ( Capudean, 2003 ) ( Groover, 2010 )
Degree centigrades: UsersNathanielDesktopRoadRailBridges.gif
Medium Carbon Steels ; incorporate 0.25 % up to 0.55 % C. When it comes to belongingss, increasing C besides means a direct influential addition in hardness + tensile strength. On the other manus this besides effects severely the ductileness which makes it more hard to machine. Heat intervention to really thin subdivisions can better such machinability issues. These may be austinized by slaking and annealing afterwards to better such belongingss. These are comparatively stronger than the old class, whilst weaker than the high C steels. One common application of medium C steel is the production of crankshafts where high strength and stiffness is required to defy high tonss and opposition to tire when it comes to uninterrupted tortuosity and bending. Typical values are, 450-580MPa - output strength, 600-750 MPa - tensile strength, and 20-30 % EL - Ductility. ( Corus, 2010 ) ( Jr. , 2007 ) ( Iron Making & A ; Steel MAking, 2008 )
Degree centigrades: UsersNathanielDesktop1108phr-03+383ci-small-block-chevys+pistons-and-crankshaft.jpg
High Carbon Steels ; incorporate 0.6 % up to 1.4 % of C. In a heat treated status it is able to defy high shear and wear hence, these are used in applications where stiffness and hardness play an of import portion such as in rope wire, besides good in prolonging crisp film editing borders. Unfortunately, these are the least malleable and really difficult to weld, in fact preheating and station warming ( commanding of chilling temperature ) is critical in order to obtain good welding sections and accomplish good mechanical belongingss. Since at their maximal hardenable conditions, these are the most brickle devising this a large drawback for this steel. ( B ) ( Jr. , 2007 ) ( Groover, 2010 )
Degree centigrades: UsersNathanielDesktopwire-rope2.jpg
Very High Carbon Steel / Tool Steels ; are a 'sub group ' of high C steels and contain lower limit of 0.8 % C. These have weak welding belongingss and ductileness, but are really good when it comes to strength, hardness and wear opposition that 's why it is really normally used in centre clouts. An of import factor for these sorts of steels is that most of them are used in a hard-boiled + tempered status. ( Jr. , 2007 ) ( Groover, 2010 )
Degree centigrades: UsersNathanielDesktop oolsteel.jpg
P7: Question 2
Select an industry and supply a brief over position of one metal forming technique used.
The preciseness metal organizing procedure I will be discoursing is the Powder Formation ( PM ) . This gives an alternate cost effectual range towards stomping, hammering, machined parts and projecting. This is characterized one of the most enforced preciseness metal organizing technique in the modern industry and it is normally found in the automotive industry. Most vehicle parts presents are produced by such a procedure. PM combines pulverization compression with optimum physical belongingss with controlled high temperatures atmosphere sintering. ( Turkish PM )
Degree centigrades: UsersNathanielDesktopimage001.gif
Such a procedure offers ideal benefits that you can non accomplish with using other metal working procedures. Mentioning merely a few, it is really material efficient since the finished portion uses 100 % of the stuff, whilst in other organizing techniques one will hold wastes. The procedure is really good in making intricate forms with minimum cost add-on. Some illustrations could be splines, cogwheels, away centric parts, etc ) . Sometimes this besides reduces assemblies since most of the assembly parts can be produced in a individual formation by PM. The PM clouts and rods produce parts with closer tolerances. A assortment of standard metals are specifically suited for PM processing, nevertheless intermixing can be easy done to run into specific belongings demand. Automatic rhythms make the PM procedure really labour efficient. The lone back draw is to put up the parametric quantities for the tooling, but as this is done, the procedure can bring forth parts at a really efficient rate. High temperature Powder Metal ( HTPM ) , is able to accomplish 88-96 % of the material theoretical denseness. Since every stuff belongingss depends on denseness ( elongation, output strength, etc ) , HTMP outperform other procedures. ( GT.b, 2012 ) ( J, 2011 ) ( Marciniak, 1988 )
The high temperature metal pulverization procedure is divided into 4 chief sectors ;
Blending - here high pureness metals pulverizations and additives are studied so funneled down to choose the optimal pick for the application in order to run into the coveted belongingss to the application. For illustration in the automotive industry, this procedure is used to organize panels. Here aluminum pulverization with anti oxidation additives and silicone for elastic belongingss are added in order to organize the ideal mixture for the door panel. All the pulverizations are assorted with particular lubricators which helps treating the pulverization flow. As mentioned before, blending the pulverizations in a solid province provides new chances to come up with new belongingss unique merely to HTPM.
Compacting - Powdered metal is fed from a hopper into a provender shoe. The provender shoe delivers it into a die pit. Here multiple pulsations compress it into 50 % of its original capacity. Second strength packing forces realign and deform the atoms whilst implementing local mechanical bondings organizing a portion known as 'a green portion ' . These are ejected carefully by automated machines and conveyed to the following measure. Compacting imperativenesss vary from 5 up to 900 tones and are capable of multiple gestures.
Sintering - this involves puting the green portion in temperatures above 1300A°C ( but below runing points ) . By such a procedure a batch of benefits are achieved, metallurgic bonding is enhanced, ductileness and stamina are besides improved. The initial art of the procedure cleans lubricators and surface of the metallic atoms to guarantee perfect mechanical belongingss sing the finished constituent. At the 2nd portion of this procedure ( go forthing portion in high temperatures ) , this allows energy to transform mechanical bonds to metallurgical bonds.
Completing - sizing / coining are post operations that can be used for more complicated and minor tolerance dimensions, ( illustration - engine parts like cylinder valves, linking rods, etc ) . Extra coating assets could be milling, crunching etc. From here it can come on to a connection procedure. After joined this can besides be heat treated and plated. Heat intervention goes up to 550A°C to do a bed of Fe3O4A which acts as corrosion resistant, and increase in hardness. ( N.A. ) ( GT.b, 2012 ) ( J, 2011 ) ( Marciniak, 1988 )
Note- A presentation will be held in category explicating the procedure in more item.
Degree centigrades: UsersNathanielDesktopcycle.jpg
P8: Question 3
Distinguish between merger & A ; non merger, besides select one procedure and discuss. Finally supply one application and besides discuss.
Welding is a procedure to bring forth high strength lasting articulations between two ( or more ) parts that need to be connected with each other by agencies of a weldment ( metallurgic fall ining subdivision ) . There are assorted ways to obtain such a connexion and with today 's engineering we are accomplishing better belongings results when it comes to post welding belongingss. Chiefly the procedure involves heating a portion, runing the portion / base metal ( depending on which procedure is adopted ) and connection of the stuff occurs as temp start to chill down. Thus the procedure required relies chiefly on the application of heat and force per unit area. One common welding factor is that the metallurgic construction of any metal will be changed station to welding. This could take to a station welding heat intervention procedure. ( T, 2010 ) ( Key to metals, 2007 )
Welding is divided into two chief groups, depending on the physical province of the base metal during the procedure that of the base metal being in liquid province or in solid province. These procedures are better known as merger and non merger welding techniques. In order to choose which welding procedure demands to be selected one should first analyze both the welding procedures and addition information sing pre dyer's rockets and station dyer's rockets. ( YA±lmaz, 2007 )
Fusion / Liquid State Welding ; this is the most common type of welding found in the industry due that the dyer's rocket produced is really strong. In this sort of fall ining procedure, the base metal is melted in order for the dyer's rocket to happen. Apart from the heat beginning a filler stuff ( consumable electrode ) may be fed besides into the welding pool. This procedure may besides utilize a protective bed between our environing atmosphere and the liquefied metal ( gas shield or flux ) . This protection consequences in a scoria on top of the welded seam which subsequently on solidifies and can be removed. There is a assortment of merger welding processes that can be used holding a different belongings result. ( Marinov )
Three major classs of merger welding are found which are bomber divided into different procedures ;
Arc Welding: in this sort of procedure warming and thaw of the stuff is done by an electric discharge. Some illustrations of discharge welding could be ; Shield metal discharge welding, , Gas tungsten arc welding, Plasma discharge welding, Gas metal discharge welding, Flux cored arc welding, Submerged discharge welding, Electroslag welding.
Gas Welding ; for this sort of welding the gas produces a fire that melts the basal stuff. An illustration of such procedure is ; Oxyacetylene welding
High energy beam welding ; here a high energy beam is shot between the two parts held together under force per unit area. As the temperature starts diminishing after the beam Michigan, the parts start to bond together. Some illustrations of this procedure are ; Electro beam welding & A ; Laser beam welding.
Basically all the procedures reference antecedently for merger has the same principals. A heat / energy beginning is concentrated on a really little country and a weld pool is produced. These heat beginnings for merger are arc, high energy beams and gas. Obviously the power denseness rises from gas fire to an electric discharge to a high energy beam. For the classs mentioned below we can analyze a graph demoing the heat input to the work piece vs power denseness of heat beginning. It is reasonably obvious that as the power of the heat beginning additions, the heat input to the welded portion decreases. Therefore the less the power denseness of the beginning the larger the affected country. Excessive clip for heating can do harm to the work piece, by changing the belongingss including deformation and weakening. ( Schwartz, 1979 )
Degree centigrades: UsersNathanielDesktopUntitledff.png
Therefore one of the advantages on power denseness increaser is deeper incursions, optimum welding qualities, and less exposure clip for the welded portion. This procedure is besides various, and adaptable for confined infinites. On the other manus some disadvantages are, it is non every bit productive as uninterrupted wire applications, current bounds are critical to find the joint potency. ( Liverpool, 2000 )
Non Fusion / Solid State Welds ; for this type of welding heat is applied merely for the base metal to soften in its solid province in order to ease fictile distortion or rush up the solid province diffusion. As the name provinces, in non merger welding the stuffs are joined together without the demand of runing the base metal. Here the stuffs to be joined are brought together at equilibrium spacing for fictile distortion through high temperatures ( below runing point ) and force per unit areas. Some of the chief non merger welding techniques are ;
Cold welding: In this procedure the dyer's rocket is achieved by the force per unit area and little lift in temperature due to cold working. Some typical illustrations are ; Press welding & A ; Roll Welding.
Clash welding: For this procedure the dyer's rocket is achieved due to the heat produced due to using force per unit area between the parts i.e making clash. Some illustrations are ; Radial Friction welding & A ; Orbital Friction Welding.
Diffusion Welding: here both parts are held together under changeless force per unit area, promoting the temperature somewhat and left invariable for a peculiar clip frame ( depending on the stuff ) . Some illustrations are ; Conventional Diffusion welding & A ; Deformation Diffusion welding
Solid State Deposition Welding: Chemical reaction bounding.
Degree centigrades: UsersNathanielDesktopspwmtfeb2001f1.jpg
The first advantage of such a procedure is that low heat is required, hence minimum disruptors in crystalline construction are noticed since no thaw temperatures are required. This could besides be applied for stuffs within the same category or even within different categories due that no intermixing is involved. The chief disadvantage is that for such a procedure big, fixed machineries are required and this is a consequence for big capital financess to purchase the equipment required. Another disadvantage is that this procedure is non really feasible to be applied for little graduated table applications since its complicity. ( Jr, 2004 ) ( Lancaster, 1999 )
Describing one peculiar welding method, the method I will be discoursing is the 'Hyperbaric Welding Process ' normally known as under H2O welding. This procedure falls under the class of Fusion welding. This is a really good illustration of welding in an unusual, critical environment. For such a procedure the welder must be an A class welder plus a commercial frogman in order to defy the harsh and unsafe sea conditions nature has to offer. ( Mukund, 1974 )
Degree centigrades: UsersNathanielDesktop2071602_f520.jpg
In order to delegate instantly the procedure with an application mentioning advantages, disadvantages, equipment, restrictions and safeguards, the underwater welding is a procedure used in the offshore industry. The offshore industry covers the fixs of vass ( any kind ) , boring platforms ( jack up rigs, semi submergible rigs, self propelled rigs ) , Bridgess, etc. These constructions face terrible conditions conditions and are invariably flexing in multi conditional environments, hence the hazard of harm and failure is far greater. Basically this sort of welding is ideal and it is really flexible since the work could be done under the water line, therefore the natation works could be repaired in place without the demand of docking the platform to obtain dry conditions. This consequences in less sweeps and loss of valuable boring clip. Restrictions of such a procedure for our boring platform application are that the system is necessarily bulky and expensive to run.
For such an application normally low to intercede C steels are used. Steels are designed as CT and a figure after to demo the C content. The most common steel found in this industry is CT3. Low and intermediate C steels are ideal since these have high malleability and sensible dyer's rocket ability. A The weld ability of depends on their C + manganese content in concurrence with their dross degrees. At low C degrees that of less than 0.15 % , the steels are non difficult and the dyer's rocket ability is excellent.A For the medium C type, 0.30 - 0.60 % C is found and these can be welded easy by agencies of discharge welding. Unlike the surface normal discharge welding, where such intermediate C have higher hardness and martinsite formation, in dry conditions pre warming and station warming are required. For deep sea dyer's rockets alternatively of pre warming and station warming, the dyer's rocket is non performed at one spell but with intermediate intermissions. ( Martikainen ) ( Sacrificial Metal, 2012 )
Degree centigrades: UsersNathanielDesktopcorrosion_drill ( 1 ) .jpg
Basically there are two categorizations to execute submerged welding. The choice of the proper method is selected after an submerged structural / hull study and the parametric quantities of the submerged environment. The welding categorizations are 'Dry Welding ' & As ; 'Wet welding ' .
Wet Welding ; here the welding is performed to the direct exposure of the wet conditions. Here the 'Manual Metal Arc ' procedure is used. The principals of such a procedure are fundamentally the same as that of Arc Welding on dry land but in this instance a particular H2O cogent evidence electrode is required in order to protect the electrode 's nucleus. This is the most efficient and cost effectual welding method found amongst all under H2O welding. For this method the power supply is located on the surface of the H2O ( dry conditions ) and the overseas telegrams and hosieries are fed to the frogman via overseas telegram defenders ( big flexible piping ) .
The power supply provenders direct current ( DC ) 300 - 400 As through overseas telegrams with negative mutual opposition. If positive mutual opposition is used in DC electrolysis will occour and causes rapid impairment of the metallic constituents in the electrode manus held holder. DC currents are used alternatively of AC ( Alternating ) due to electrical safety and the trouble of keeping the discharge in wet conditions. Motor generator welding machines are normally used. For the moisture type welding it is of import that the circuit includes a knife switch ( Positive type ) . This sort of switch is operated on the surface but eventually commanded by the frogman for optimal safety. This switch should be capable of interrupting the full welding current and stops the dyer's rocket ax the switch is non-operated. As mentioned antecedently, even the electrode itself should hold a particular coating of waterproofing. Basically all connexions should be insulated in order that no H2O comes in contact with any metal parts. If this insularity is damaged, current will leak and will non be available in the discharge. ( Levi, 2010 )
This method is low cost compared to dry welding, it is besides an onsite occupation i.e. no demand of complex equipment an the frogman can make places of the offshore construction that could non be reached by other types of welding. Some disadvantages are that there is an immediate quench of the welded articulation due to environing Waterss ( additions tensile strength - decreases ductileness & A ; increasure in porousness and hardness ) .large sums of H is present taking to disruptions. H2 dissolves in heat affectional zone and the welded articulation could check. The chief disadvantage is the safety issue sing visibleness and currents
Degree centigrades: UsersNathanielDesktopWelding.Programs.jpg
Hyperbaric Dry Welding ; here the dyer's rocket is done in a certain chamber. This chamber is normally filled up with He incorporating 0.5 saloon of O at positive force per unit area somewhat above ambient. These dyer's rockets are somewhat higher in quality that of moisture welding and run into X-ray cryptography demands. For such a procedure the 'Manual Metal Arc ' is used or the 'Gas Tungsten Arc ' welding is used ( depending on the welder accomplishments ) . The welding is done in dry conditions but at hydrostatic force per unit areas of the deepness of the environing sea. For the dry dyer's rocket procedure the welding power generator could be AC and DC.
Degree centigrades: UsersNathanielDesktopCommercialDryBell.jpg
Some advantages of dry welding are that the frogman is safer since the dyer's rocket is performed in an enclosed chamber, hence no direct distractions from currents, and visibleness is much better than moisture welding since the chamber is illuminated. Good quality dyer's rockets are achieved comparable to come up welding and H2 degrees are much lower than H2O dyer's rockets, not distructave proving could be performed in the chamber. Some disadvantages are that the procedure requires much more capital and support at the surface as the method is much more complex, the cost additions with deepness, and the procedure is non every bit flexible as the unfastened H2O dyer's rocket as the connection subdivisions should suit the enclosed chamber. ( Akers, 2012 )
To depict the procedure of Manual Arc Welding, the work that is traveling to be welded should be straight connected to the positive side of the electric circuit via overseas telegrams. Sometimes the Earth overseas telegram incorporates more than 1 connexion in order to obtain the best circuit continuity for the land. A flux ( plus H2O proofing ) electrode is connected to the manus held holder via another overseas telegram which are connected to a power welding coevals beginning. When the tip of the electrode touches the work piece, the current discharge from the spread and causes a flicker which melts the base metal and the electrode organizing a dyer's rocket puddle.
Degree centigrades: UsersNathanielDesktopwelding-circuit.gif
Comparing both diagrams we can detect some differences. For the moisture procedure, DC current, a knife switch and dual insularity overseas telegrams are required. The mutual opposition is -ve, whilst the circuit is fundamentally the same.
As the discharge is moved off from the work piece, the pool solidifies and the articulations are fused together. This welding pool is controlled by changing the current which flows through the discharge being produced and by altering the electrode diameters. Typical temperatures are those of 5000°C. by such a procedure a consequence of metallurgical bonding is achieved through the work piece. At these elevated temperatures, metals are 'active ' and if it comes in contact with air it rusts immediately and the mechanical belongingss of the joint fail. For such a ground the discharge welding provides agencies of screening to the dyer's rocket pool ( gas, scoria ) . This is known as metallic discharge shield and is accomplished by the flux covering the electrode nucleus. The scoria produced as the pool cools and solidifies has its map to minimise contact of dyer's rocket to air until temp lessenings.
The discharge creates a little pit formed inside the flux. This is for the flux to fire slower than the metal barrel i.e. helping in the protection and control of the metal sedimentation that leave the electrode. For the welding procedure this is a critical in order to keep a changeless discharge and weld articulation. Even in hapless under H2O visibleness, the frogman needs to maintain force per unit area on the electrode to keep a changeless good provender rate. In under H2O welding in is really of import to advert that the discharge behaves otherwise than it does in air. In H2O gas bubbles are a really of import factor as these create an unstable discharge for good welding conditions. In concurrence with this, it is much more hard to command the dyer's rocket puddle. The frogman must put currents by test and mistake depending on the Waterss conditions ( temp, salt, etc ) . Apart from this there is no difference between surface and under H2O welding. ( Kaets, 2000 )
Degree centigrades: UsersNathanielDesktopshielding-weld-arc.gif
When compared to other welding procedures Manual discharge welding is normally used because the equipment is comparatively easy to utilize and inexpensive ( compared to other types ) , it is flexible, portable, and ideal for the frogman to utilize in confined infinites, no gas shield is required and eventually it is suited for about all sort of metals and metals. Some disadvantages of discharge welding are that the electrode needs to be replaced often ( more exposed to daze ) , the scoria should be removed after the dyer's rocket is performed, and the procedure is somewhat slower since the rate of deposition is slower than continuously fed electrode procedure ( Gas Tungsten Arc ) . ( Kaets, 2000 )
One last note sing under H2O welding ; there is a procedure non normally used which features a specially built keeping torch which sprays a changeless cone made of high force per unit area H2O, with protective gas under force per unit area to insulate the welded are from the H2O during the dyer's rocket is performed. Besides a recent development was done affecting under H2O optical maser beam welding. This method is still being improved but will shortly be applicable for the offshore industry. ( Clutter, 2012 )
Cite this Page
Categories Of Carbon Steel Their Compositions Engineering Essay. (2018, Aug 12). Retrieved from https://phdessay.com/categories-of-carbon-steel-their-compositions-engineering-essay/
Run a free check or have your essay done for you
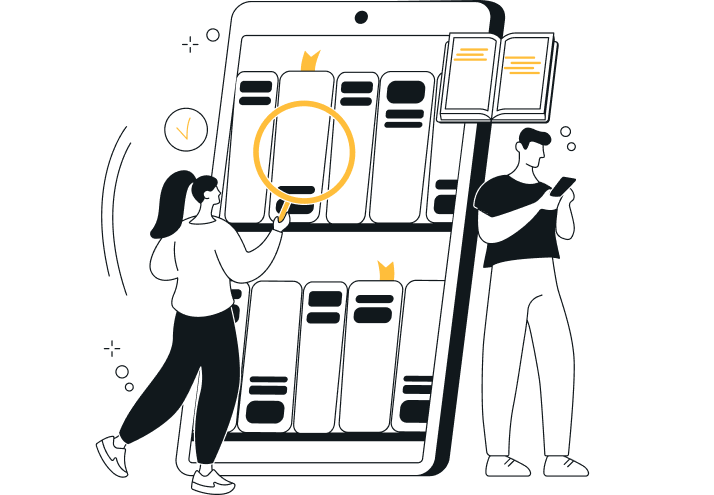