Case Study of Kalon
Introduction
There has been a drastic change in the way logistics operate today. Today, logistics is about economics of scope than economics of scale. What this means is that more and more companies are now concerned about the scope for development rather than volume. Quality is what is foremost on the agenda of logistic operators.
Business is characterized as evolving away from the earlier objective of single exchange transactions towards a long-term buyer-seller relationship of mutual benefit. These strategic relationships generate managed supply chains.
Order custom essay Case Study of Kalon with free plagiarism report
Today, logistics involves the cooperation through economic networks for mutual benefits. In other words, individualism has given way to collectiveness. That’s right! Logistics is about total solution under one roof. This way, companies manage their business with lesser paperwork, less tracking and negotiations, and shared responsibilities. What brought about this transformation? Consumers; that’s right! Consumers today seek greater product variety at high quality level and obviously, reliability. Product availability is mandatory. Thus, the huge containers that used to carry high volumes of consignments have now been cut to size to accommodate quicker and easier handling, thereby accommodating faster and efficient services, plus continuity. In order to attain such professionalism, global corporate houses have become centres of corporate structures, centred on the principles of co-operation and partnership; outsourcing of logistics functions. Kalon is one among them.
Globalization and outsourcing has opened new vistas for logistic operators in relatively all areas of operations, be it shipping lines, forwarders, terminal operators, road haulers, or rail operators. The integration of these services under a single umbrella is what corporate managers seek today. Together, this integration provides new value-added services as an integrated package.
Kalon, the UK paint company, achieved impressive growth to become one of the major forces and one of the best financial performers in the UK paints industry in 1995. Financial analysts attributed this success at least in part to efficient logistics systems which had produced benefits in terms of both costs and customer service. Kalon’s other key achievements had been to position itself very well in two key paint market sectors – the professional decorators’ market and the production of own label paints for leading retailers. Depressed trading conditions and strong competition in the late 1990s reduced the profitability of the company. This called for improved effort in logistics and corporate strategies to allow the company to grow rapidly, and at the same time, maintain a highly professional, yet competitive logistic operational cost.
Kalon’s success can be put down to astute acquisitions, a series of well-judged strategic decisions regarding the future direction of the business and efficient management, not least in the area of logistics. To quote Ian Hamilton Fazey of the Financial Times, in the paint industry, “independents can survive, but they have to very good, such as Kalon its forte is good logistics to ensure just-in-time distribution” (Hamilton Fazey, 1994).
Company Overview and Strategy
ICI Dulux remained the top manufacturer’s brand in the market place. Akzo Nobel produced the Crown brand for the retail market, but also produced trade ranges such as Permaglaze as well as retailers’ own label paints.
In order to understand the logistics required to strengthen Kalon’s market presence and ensure better profitability, it is necessary to study the company and its product range. Kalon retail brands such as Homecharm were less well known but the company was a major producer of trade paints (the Leyland range) and was the largest supplier of retailers own label paints in the UK. Own label products were made by Kalon not only for some of the main DIY superstore chains, but also for significant numbers of smaller and regional retailers.
As its strategy developed, Kalon found contrasting requirements in its two main market segments. The supply of large paint volumes to the major retail multiples enabled Kalon to develop very efficient logistics systems for this part of its business. Operating in this market was not without its risks, however. It was the downturn of the DIY market that slowed growth in Kalon sales and profits in 1994.
When Superstore operators reduced the average prices for their own label paints, and also ran a series of promotions on key items in the brand ranges such as Dulux and Crown, sales of the Kalon range of products ran into difficulty. Added to this was the problem of certain DIY chains making strategic decisions not to source own label products from manufacturers used by their main competitors. This could hamper future business scope when these chains were taken over.
Confirmation of the Sainsbury takeover of Texas Homecare DIY group in January 1995 adversely affected Kalon’s share price, because Texas Homecare had been a Kalon customer, whilst Sainsbury’s Homebase had sourced most own label paints from Akzo Nobel (Clark, 1995).
In contrast to this experience in the retail market, the success of Leyland in the trade paints market was not without its costs in terms of logistics complexity. A very large product range was offered, and there was a need to service the growing network of Decorator Centers, as well as large numbers of often small deliveries to hundreds of builders and decorators’ merchants, wholesalers and other specialist suppliers. This called for greater flexibility and continuity in supplies, depending on the product demand. Kalon had no other option but to rethink its logistic operations to beat competition.
Logistics
Marston Book Services handles UK, European and worldwide distribution of publications. In 1994 the company embarked on the construction of a new, purpose designed administration and warehousing unit of 50,000 sq ft, which includes an additional 10,000 sq ft mezzanine floor. In 2002, it extended its logistics operation with the creation of a second separate warehouse of 40,000 sq ft, also equipped with a 10,000 sq ft mezzanine floor, increasing total warehouse space to 110,000 sq ft. This has allowed Marston to extend the range of services to its clients, most importantly, the inclusion of a dedicated “pick and dispatch” facility for those clients who operate their own host systems. Also central to the success and smooth running of any logistics operation is the warehouse management system (Torexretail, 2007).
Logistics refers to the systematic management of various activities required to move a product or from the production/manufacture plant to the customer. It encompasses more than just movement of goods; it involves timing, cost, location, availability, and support systems (Kent N. Gourdin, p.2, 2001).
With globalization, competition at regional and international level has become even more intense, and cost and availability are prime concern for the end-user. Most companies therefore are forced to rethink their logistic operations to maintain stability on all fronts.
While we saw that in the 1980s and 1990s companies tried to out beat competition through improved production and reduced costs (cheap labour being one), technological advancement negated this advantage and forced companies to look for alternatives. Time is a constraint in today’s business world. Time spent on execution of orders has led to legal entanglement and business loss. This is the biggest worry in the world of supply-chain management. There is a growing demand for time-based logistics management, where customers are increasingly sophisticated and value time as money. To ensure quick and efficient streamlined flow of goods from the producer/supplier to the customer, companies now track factors that cause delay and try to eliminate them (Kent N. Gourdin, p.9, 2001).
Efficiency and durability are trade mark of a successful logistic operation. Using state-of-the-art network modeling tools to determine how well the distribution network serves the customers, logistics should include, inbound to outbound facilities, inventory, and service, employing all modes of transport (air, sea, rail, and road). Another important aspect of logistics is to analyze variables, such as inventory cost, time-in-transit, and service by product, industry, and location (Dynamic Logistics, 2007).
Warehouse Management System
The evolution of warehouse management systems (WMS) from that of controlling the movement and storage of materials within a warehouse, to include light manufacturing, transportation management, order management, and complete accounting systems; WMS has come a long way. According to Dave Piasecki in Warehouse Management Systems, there is a thought whether the introduction of WMS into a warehouse-focused ERP system is a good or not. What is clear is that the expansion of the overlap in functionality between Warehouse Management Systems, Enterprise Resource Planning, Distribution Requirements Planning, Transportation Management Systems, Supply Chain Planning, Advanced Planning and Scheduling, and Manufacturing Execution Systems will only increase the level of confusion among companies looking for software solutions for their operations (Dave Piasecki, Inventoryops.com).
The primary purpose of a WMS is to control the movement and storage of materials within an operation and process the associated transactions to derive at a consensus on costs vs. process. WMS helps in automated data collection, which in all probability give the company increased accuracy, reduction in labor costs, and a greater ability to service the customer by reducing cycle times, a great feature in the context of today’s supply chain management.
As mentioned, WMS helps reduce labour and labour costs, improving production and inventory efficiency, first-in-first-out, cross-docking, automated pick replenishment, wave picking, lot tracking, yard management, and automated data collection. These features add to the systematic improvement of logistics (Dave Piasecki, Inventoryops.com).
Supply Chain Management
What do the Internet, e-tailing and electronic commerce have in common? All three play an important role in logistics, and their importance can be traced to dramatic changes in the corporate world of supply chain management. Together, they have gained importance in bringing gains and sustaining competitive advantage. Of the technology options, Logistics Execution Systems (LES) plays a vital role in the order fulfillment and product delivery.
Companies need to meet challenges, and to do this successfully, they spend time and money developing solutions in-house that will enable them to accurately identify, track, manage and report on material flow as well as efficiently allocate resources to related tasks throughout the pipeline. In order to achieve this, companies need to focus on:
- Centralized distribution centers
- Channel-specific distribution center design
- Repackaging, labeling and pricing at the distribution point
- A move to more conventional or hybrid warehousing with on-line, real-time computer-based warehouse management systems
- Compliance as well as supplier labeling and price marking
- Increased use of standard bar code for product, packaging and ship container identification to facilitate warehouse management, shipment tracking and POS transaction monitoring
- Supplier’s retail store level inventory (VMI).
- Trading partner communication
- Growing use of decision support, modeling and simulation tools
- Employee empowerment through tools to increase operational efficiency and productivity
In warehousing operations, an increasing number of companies have grown cautious about investments in large scale, opting instead for more flexible, fully conventional approaches or hybrids that combine mechanised and conventional alternatives (John N. Hill, p.2-3, 2003).
Initially, LES were introduced to permit real-time material tracking and resource management in conventional warehouses, using bar codes for material tracking, a broader array of radio data terminals for industrial applications, and a dramatically improved computer performance at lower cost and a variety of software tools to relational data base management.
Warehouse Management Systems had clearly come of age. Industry leaders began to see results as revenue grew at better than 20% annually and initiated programs to add functionality in the areas of labor (LMS) and transportation (TMS) management. LES (logistics execution systems) emerged as the new acronym for systems that managed material and data flow in the supply chain (John N. Hill, p.4, 2003).
There are three basic forms of outsourcing with regard to supply chain management. These are other methods used to improve production, quality and inventory. They are:
- The outsourcing of the production of components. Global Corporate develop long-term relationships with a number of suppliers on the basis of mutual trust.
- Value-Added Logistics (VAL). VAL implies that production and distribution of a supply chain integrates into one.
- The outsourcing of transportation, warehousing and distribution. Third-party Transportation, warehousing and distribution activities are fast growing outsourcing businesses.
Though the above methods have been successfully used and managed by a few corporate, in the case of Kalon, the third option, outsourcing of transport, warehouse and distribution should be the ideal situation. Kalon could put more effort into R&D and realize a quality product within the reach of its customers in the shortest possible time.
Conclusion
With the advancement of technology, corporate giants have been vying with each other for supremacy. Paint is a highly competitive market and with lots of small players trying to stake a claim in small segments of the market. Logistics plays an important part in truncating cost escalation, reducing overheads, and thereby lower production costs. Software packages that overlook inbound to outbound facilities, inventory, and service, employing all modes of transport (air, sea, rail, and road) were discussed as suitable options available to curb unnecessary cost and waste. Measures to analyze variables, such as inventory cost, time-in-transit, and service by product, industry, and location were also discussed. The paper concluded that for a company like Kalon, outsourcing of transport, warehouse and distribution would be an ideal solution to cutting overheads and maintaining good supply-chain management.
References
- Torex retail Plc, Case Study: Marston Book Services, www.torexretail.com/english/download/case_study/Marston_Case_Study.pdf
- Dynamic Logistics, Services, 2000-2010, www.dynamiclogistics.com
- Kent N. Gourdin, Global Logistics Management: A Competitive Advantage for the New Millennium, Blackwell Publishing, Google Book Search, 2001
- Dave Piasecki, Warehouse Management Systems (WMS), Inventoryops.com, www.inventoryops.com/warehouse_management_systems.htm
- John M. Hill, White Paper, Logistics Execution Systems Perspective, Supply Chain Forum, www.idii.com/wp/ESYNC_LES_Perspective.pdf 2003
Cite this Page
Case Study of Kalon. (2018, Feb 03). Retrieved from https://phdessay.com/case-study-of-kalon/
Run a free check or have your essay done for you
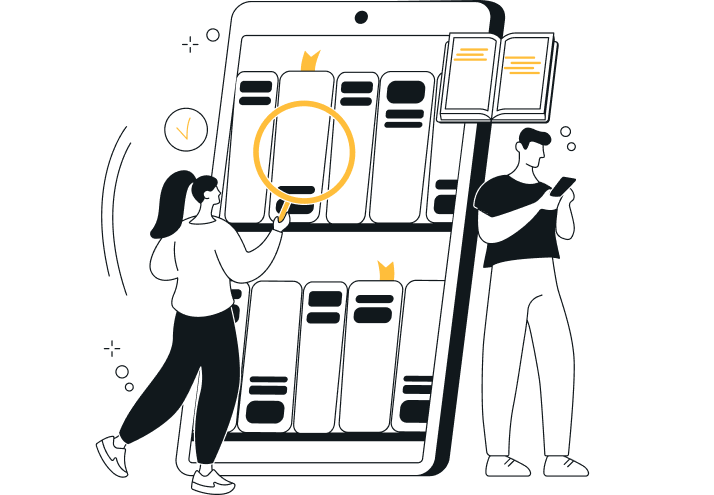