Blozis Company
Part 1 - Executive Summary
My decision, as the supply manager of the Blozis company, is to implement new processes and procedures in the supply department. One of the changes to be made in the processes and procedures will include having the expediter’s role primarily limited to the expedition of materials. An expediter is the person in charge of scheduling purchases, purchasing and scheduling the delivery of materials and services, as well as checking orders and speeding up the arrival of materials needed to meet production schedules. The current expediter, besides undertaking these responsibilities, is also taking on a number of other responsibilities that are taking away from his abilities to properly complete his core job responsibilities.
In addition, the process for the receiving of products and materials will be improved so that items received into inventory are properly accounted for, as well as properly accounted for once they leave inventory, so that they are charged to the correct departmental budget and are paid for in a timely manner so that early payment discounts are taken advantage of. A current and accurate inventory is necessary in order to properly manage the supply department.
Order custom essay Blozis Company with free plagiarism report
In regards to approval of requisitions, despite the fact the president likes to operate “informally” it is important to ensure that the required signatures are obtained on all requisitions as this helps to hold people accountable for their purchases and to control costs and remain within budget. Even though purchases over $10,000.00 may have technically been approved by the president in the budget, they are not realized purchases and in order to ensure they do fall within budget requirements, the president still should be required to execute these requisitions. As well to ensure managers are informed and can be held accountable to what items are charged to their departments, it is prudent to include on the requisition the signature of the manager of the department for which the purchase is being made.
Finally the engineering department should be required to be as detailed and accurate in their descriptions and specifications on all purchase orders. While the current expeditor has some technical background, all purchase orders should be supplied to the supply department with detailed specifications to ensure the correct materials and parts are purchased and supplied. Even though the main responsibility for this should still fall to the engineering department, there is no reason why the continued process of discussing the details of purchase orders with the expeditor could not continue as well, as this will ensure greater accuracy in the specifications detailed on their purchase orders together with greater accuracy in the fulfillment of the purchase orders.
Part 2 - Immediate Issue with Impact Analysis
Besides expediting parts and materials throughout the company, the expeditor was also writing purchase requisitions and purchase orders. At times the expeditor would just pick up parts and advise suppliers that they would receive “confirming orders” that never followed. This resulted in the supply department at times receiving invoices for items that could not be matched to a corresponding purchase order. In order to control costs, remain within budget and to ensure accurate inventory and purchases, this process cannot continue. The Blozis Company needs to have their expeditor doing just that, expediting items throughout the company and not writing purchase requisitions and orders. The writing of purchase requisitions and orders should be limited to the engineering and production personnel.
The current inventory and purchasing process within the Blozis Company is allowing for inventory to go missing, payments for materials and items received to be missed, as well as the receiving of invoices for payments to suppliers that are not supported by purchase orders. The current processes or lack of processes are not allowing for the proper tracking and accounting of inventory; the control of cost as purchasing discounts are being missed and invoicing is being received and paid for without proper documentation that the items were in fact ordered and received. This lax in documentation and recording of items is also impacting on the ability of each department to remain within budget.
The company, as well, can no longer function without proper processes that are diligently followed in regards to signatures on purchase requisitions. Again this allows for greater control over costs, purchasing accountability and adherence to budget restrictions.
As a whole the company needs to completely overhaul their current processes and procedures in their supply department in order to address the issues as detailed above.
Part 3 – Environmental and Root Cause Analysis
Under the current processes in the supply department the expeditor is spending too much time handling technical orders. While his involvement in technical orders to a degree does assist with greater accuracy in the fulfillment of these purchase orders, it is taking away from his time to expedite materials and items throughout the company. This has resulted in corners being cut which have cost the company money. For example, two special micrometers disappeared within the plant after the Blozis Company had waited six months to receive them.
The supplier of these micrometers was able to prove that Blozis did receive these items as evidenced by a signed bill of lading, but it appears the expeditor, in an attempt to get these items to the engineers as quickly as possible, may have just picked up the micrometers on the receiving dock and taken them directly to the engineers. The expeditor on the other hand claims to never have seen the micrometers. Since no documentation was in place to evidence what happened, it became a he said she said situation, but in the end the two special micrometers were still gone at a financial loss to the company.
In addition, when the expeditor was pressed for time, instead of completing the necessary purchase order, he would just pick up a desired item from a suppler and advise the supplier that they would be receiving a “confirming order” for the item or items he picked up. A number of times the expeditor would forget to ask supply for a confirming order and when the invoice arrived from the supplier for payment, the supply department was faced with an invoice for which they had no confirming order documentation to support the payment of.
Besides the aforementioned issues relating to the lack of completed receiving reports, there was also the issue of suppliers claiming long overdue payments on materials that have been received by the Blozis Company. The supply department would not pass on a bill for payment until they had received the receiving report, which is a good process as this controlled the possibility of paying for materials that were never received. On the other hand, the lax of completion and/or the timely submission of the receiving reports to the supply department resulted in the delay of bills submitted for payment that included sizable discounts for early payment as well as not meeting the net date on several bills.
This lax in the necessity of following process and procedures in order to ensure the correct documentation was in place to record and support purchases, was not only exercised by the supply department. The president of the company liked to operate “informally” and allowed anyone in the company to initiate requisitions with only the signature of the supply manager for any orders up to a value of $10,000.00. Many managers were complaining they were unaware of what was being charged to their departments until the monthly accounting statement came out. Changes need to be made to include, on each requisition, the signature of the manager of the department to which the requisition is being made. This allows for more managerial accountability in the control of their budgets.
Part 4 – Alternatives and/or Options Based on the information that has been provided to the writer, it is their position that the issues are clearly identifiable and that solutions in regards to addressing these issues are contained herein. Despite the fact that specific issues have been identified, as with any process there could be room for more improvement in other areas that are not the subject matter of this report. Bearing this in mind, the supply department may also wish to conduct a process mapping session which will detail the entire process as it exists today and from this be able to indentify other areas of the process that require improvement. I do not believe there are any other viable alternative in regards to the solutions that have been presented herein, but the conducting of a process mapping session will only build upon and possibly lead to the discovery of more issues so that the process can be improved even further.
Part 5 – Recommendation and Implementation In regards to the role of the expeditor, it should be mainly limited to the expediting of materials and items throughout the company. His role in the handling of technical orders should be decreased with more responsibility in this regard falling on the engineering department. If purchase requisitions are written with greater specifications without as much reliance on the expeditor to assist in the writing of same, another individual within the supply department could be trained to assist with these technical orders. The implementation of these changes will begin with the manager of the engineering department meeting with his group as well as the manager of the expeditor meeting with him to ascertain what their current involvement is in regard to technical orders. Once this information is obtained, then all managers will meet in order to discuss how these job responsibilities will be allocated between the engineering department and the expeditor. Once this have been finalized, a further meeting will be held that will include all managers, the engineering department and the expeditor so that everyone can be advised of the changes in their job responsibilities going forward.
In regards to inventory control all products received must be documented and signed off on by the receiving clerk and there must be a matching purchase order to go along with the bill of lading and/or packing slip. No items should be received into inventory in the supply department without a corresponding approved purchase order. The supply department at all times is to receive a receiving report so that they can arrange for the timely payment of invoices in order to take advantage of purchasing discounts. The process for this is to be implemented by the supply manager.
To provide for further control, no one, including the expediter should be allowed to take a product or item out of inventory without providing a requisition for same. Again the process for this will be implemented by the supply manager.
In order to facilitate communication of when products and materials have arrived and are in inventory, the company should purchase inventory software that all interested parties will have access to, so that they can check for themselves when products have arrived. A meeting will be held between all managers of all departments in order to discuss which software will meet their needs and once decided the software will be purchased and put into use.
To assist managers being made aware of what materials are being charged to their departments, all purchase requisitions should also require the signature of the manager of the respective department for which the purchase is made in addition to the supply manager’s. The supply manager should never receive and process a purchase requisition unless the signature of the applicable department manager is contained on the requisitions. This process will be implemented by the supply manager.
Part 6 – Monitor and Control In regards to monitoring and controlling the success of the changes in the job responsibilities of the expeditor, there will be a follow up meetings between all parties affected, within 2 weeks of the changes taking place just to ensure things are still in place and that no one has slipped back into their old roles. After this for a further 6 month period there will again be mnthly meetings to monitor that everything is still on track in regard to the changes.
In regards to the change in the process to bring around greater inventory control, a person outside of the supply department will be assigned various audit responsibilities and will attend in the supply department, initially, on a monthly basis to ensure the controls put in place are being complied with, for example that all necessary documentation has been completed so that all inventory is recorded being received and taken out of inventory. After each audit session the auditor will be required to complete an audit report that will be delivered to the supply manager. The report will detail all areas where they have discovered non-compliance with a time line presented to the area affected to bring the process and department into compliance.
It is the expectation of the writer, that if the recommendations as detailed herein are fully and accurately followed, there will be substantial improvement in the operations of the supply department and within Blozis as a whole.
Cite this Page
Blozis Company. (2017, Mar 20). Retrieved from https://phdessay.com/blozis-company/
Run a free check or have your essay done for you
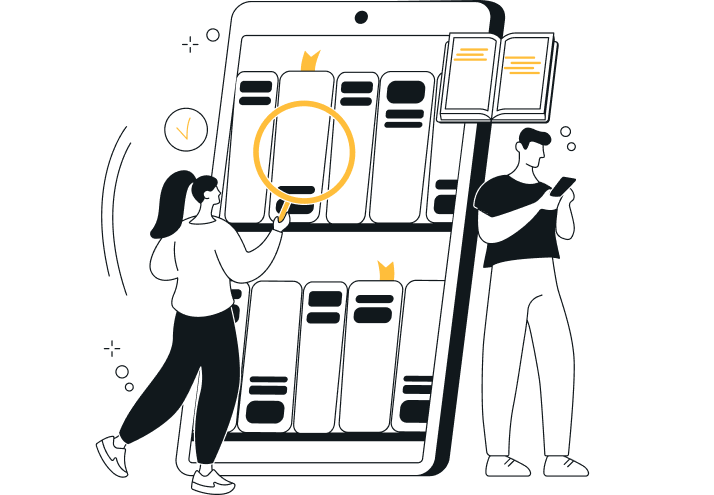