Study of Electromagnetic Clutch
ACKNOWLEDGEMENT It gives us great pleasure when a certain task is accomplished with great zeal and enthusiasm. We would like to extend our heartfelt thanks and deep sense of gratitude to all those who helped us in completing this project. First and foremost, we feel greatly indebted to Mr. D. M. SINGH and Mr. UBAID AHMAD KHAN, from the core of our heart for their constant support and valuable guidance time to time, because they encouraged and persuaded us to complete the project. We are also thankful to entire faculty members for their support.
In order to complete the project we have taken help from various sites, books, study material etc. INTRODCTION A clutch is a mechanism for transmitting rotation, which can be engaged and disengaged. Clutches are useful in devices that have two rotating shafts. In these devices, one shaft is typically driven by motor or pulley, and other shaft drives another device. The clutch connects the two shafts so that they can either be locked together and spin at the same speed (engaged), or be decoupled and spin at different speeds (disengaged). The clutch disc (centre) spins with the flywheel (left).
To disengage, the lever is pulled (black arrow), causing a white pressure plate (right) to disengage the green clutch disc from turning the drive shaft, which turns within the thrust-bearing ring of the lever. Never will all 3 rings connect, with any gaps. TYPES OF CLUTCH DOG CLUTCH A dog clutch is a type of clutch that couples two rotating shafts or other rotating components not by friction but by interference. The two parts of the clutch are designed such that one will push the other, causing both to rotate at the same speed and will never slip.
Order custom essay Study of Electromagnetic Clutch with free plagiarism report
Dog clutches are used where slip is undesirable and/or the clutch is not used to control torque. Without slippage, dog clutches are not affected by wear in the same way that friction clutches are. Dog clutches are used inside manual automotive transmissions to lock different gears to the rotating input and output shafts. A synchromesh arrangement ensures smooth engagement by matching the shaft speeds before the dog clutch is allowed to engage. Wet and dry A 'wet clutch' is immersed in a cooling lubricating fluid, which also keeps the surfaces clean and gives smoother performance and longer life.
Wet clutches; however, tend to lose some energy to the liquid. A 'dry clutch', as the name implies, is not bathed in fluid. Since the surfaces of a wet clutch can be slippery (as with a motorcycle clutch bathed in engine oil), stacking multiple clutch disks can compensate for the lower coefficient of friction and so eliminate slippage under power when fully engaged. Cone clutch A cone clutch serves the same purpose as a disk or plate clutch. However, instead of mating two spinning disks, the cone clutch uses two conical surfaces to transmit torque by friction.
The cone clutch transfers a higher torque than plate or disk clutches of the same size due to the wedging action and increased surface area. Cone clutches are generally now only used in low peripheral speed applications although they were once common in automobiles and other combustion engine transmissions. They are usually now confined to very specialist transmissions in racing, rallying, or in extreme off-road vehicles, although they are common in power boats. This is because the clutch doesn't have to be pushed in all the way and the gears will be changed quicker. Centrifugal clutch
A centrifugal clutch is a clutch that uses centrifugal force to connect two concentric shafts, with the driving shaft nested inside the driven shaft. Centrifugal clutches are often used in mopeds, lawnmowers, go-karts, chainsaws, and mini bikes. Fluid coupling A fluid coupling is a hydrodynamic device used to transmit rotating mechanical power. It has been used in automobile transmissions as an alternative to a mechanical clutch. It also has widespread application in marine and industrial machine drives, where variable speed operation and/or controlled start-up without shock loading of the power transmission system is essential.
Torque limiter It is also known as safety clutch. A torque limiter is an automatic device that protects mechanical equipment, or its work, from damage by mechanical overload. A torque limiter may limit the torque by slipping (as in a friction plate slip-clutch), or uncouple the load entirely (as in a shear pin). The action of a torque limiter is especially useful to limit any damage due to crash stops and jams. Torque limiters may be packaged as a shaft coupling or as a hub for sprocket or sheave. A torque limiting device is also known as an overload clutch. Electromagnetism What is an electromagnet?
An electromagnet can be made by sending current through a coil of wire wound around an iron core. When current passes through a conductor, magnetic field will be generated around the conductor and the conductor become a magnet. This phenomenon is called electromagnetism. Since the magnet is produced electric current, it is called the electromagnet. In short, when current flow through a conductor, magnetic field will be generated. When the current ceases, the magnetic field disappear. The direction of the magnetic field formed by a current carrying straight wire can be determined by the Right Hand Grip Rule or the Maxwell Screw Rule.
What is magnetic field pattern? A magnetic field pattern can be represented by field lines that show the shape of the field. Magnetic field lines which are closed together represents strong field. Field direction is defined as the direction indicated by a compass needle placed in the magnetic field. Force on current carrying conductor If a current carrying conductor is placed in a magnetic field produced by permanent magnets, then the field due to current carrying conductor and the permanent magnets interact and cause the a force to be exerted on the conductor .
The force on the current carrying conductor in a magnetic field depends on:- 1. The flux density of the field, B teslas 2. The strength of current, I amp 3. The length of the conductor perpendicular to the magnetic field 4. The direction of the field and current When the magnetic field, the current and the conductor are mutually perpendicular to each other then force exerted: F=IBL Newton When the conductor and magnetic field are at an angle, then the force exerted: F=IBLsin? Where; I=current, B magnetic field, L=Length of conductor ?-angle between conductor and magnetic field.
Right Hand Grip Rule Grip the wire with the right hand, with the thumb pointing along the direction of the current. The other fingers give the direction of the magnetic field around the wire. The Maxwell's Screw Rules The Maxwell Screw Rules sometime is also called the Maxwell's Corkscrew Rule. Imagine a right handed screw being turn so that it bores its way in the direction of the current in the wire. The direction of rotation gives the direction of the magnetic field. Electromagnetic clutch Electromagnetic clutches operate electrically, but transmit torque echanically. This is why they used to be referred to as electro-mechanical clutches. CONSTRUCTION A horseshoe magnet has a north and south pole. If a piece of carbon steel contacts both poles, a magnetic circuit is created. In an electromagnetic clutch, the north and south pole is created by a coil shell and a wound coil. In a clutch, when power is applied, a magnetic field is created in the coil. This field (flux) overcomes an air gap between the clutch rotor and the armature. This magnetic attraction, pulls the armature in contact with the rotor face.
The frictional contact, which is being controlled by the strength of the magnetic field, is what causes the rotational motion to start. The torque comes from the magnetic attraction, of the coil and the friction between the steel of the armature and the steel of the clutch rotor. For many industrial clutches, friction material is used between the poles. The material is mainly used to help decrease the wear rate, but different types of material can also be used to change the coefficient of friction (torque for special applications).
For example, if the clutch is required to have an extended time to speed or slip time, a low coefficient friction material can be used and if a clutch is required to have a slightly higher torque (mostly for low rpm applications), a high coefficient friction material can be used. In a clutch, the electromagnetic lines of flux have to pass into the rotor, and in turn, attract and pull the armature in contact with it to complete clutch engagement. Most industrial clutches use what is called a single flux, two pole design. Mobile clutches of other specialty electromagnetic clutches can use a double or triple flux rotor.
The double or trip flux refers to the number of north/south flux paths, in the rotor and armature. This means that, if the armature is designed properly and has similar banana slots, what occurs is a leaping of the flux path, which goes north south, north south. By having more points of contact, the torque can be greatly increased. In theory, if there were 2 sets of poles at the same diameter, the torque would double in a clutch. Obviously, that is not possible to do, so the points of contact have to be at a smaller inner diameter.
Also, there are magnetic flux losses because of the bridges between the banana slots. But by using a double flux design, a 30%-50% increase in torque, can be achieved, and by using a triple flux design, a 40%-90% in torque can be achieved. This is important in applications where size and weight are critical, such as automotive requirements. The coil shell is made with carbon steel that has a combination of good strength and good magnetic properties. Copper (sometimes aluminium) magnet wire, is used to create the coil, which is held in shell either by a bobbin or by some type of epoxy/adhesive.
To help increase life in applications, friction material is used between the poles on the face of the rotor. This friction material is flush with the steel on the rotor, since if the friction material was not flush, good magnetic traction could not occur between the faces. Some people look at electromagnetic clutches and mistakenly assume that, since the friction material is flush with the steel that the clutch has already worn down but this is not the case. Clutches used in most mobile applications, (automotive, agriculture, construction equipment) do not use friction material.
Their cycle requirements tend to be lower than industrial clutches, and their cost is more sensitive. Also, many mobile clutches are exposed to outside elements, so by not having friction material, it eliminates the possibility of swelling (reduced torque), that can happen when friction material absorbs moisture. HOW DOES IT WORKS The clutch has four main parts: field, rotor, armature, and hub (output) . When voltage is applied the stationary magnetic field generates the lines of flux that pass into the rotor. (The rotor is normally connected to the part that is always moving in the machine. The flux (magnetic attraction) pulls the armature in contact with the rotor (the armature is connected to the component that requires the acceleration), as the armature and the output start to accelerate. Slipping between the rotor face and the armature face continues until the input and output speed is the same (100% lockup). The actual time for this is quite short, between 1/200th of a second and 1 second. Disengagement is very simple. Once the field starts to degrade, flux falls rapidly and the armature separates.
One or more springs hold the armature away from the rotor at a predetermined air gap. Engagement time There are actually two engagement times to consider in an electromagnetic clutch. The first one is the time that it takes for a coil to develop a magnetic field, strong enough to pull in an armature. Within this, there are two factors to consider. The first one is the amount of ampere turns in a coil, which will determine the strength of a magnetic field. The second one is air gap, which is the space between the armature and the rotor. Magnetic lines of flux diminish quickly in the air..
Air gap is an important consideration especially with a fixed armature design because as the unit wears over many cycles of engagement the armature and the rotor will create a larger air gap which will change the engagement time of the clutch. In high cycle applications, where registration is important, even the difference of 10 to 15 milliseconds can make a difference, in registration of a machine. Even in a normal cycle application, this is important because a new machine that has accurate timing can eventually see a “drift” in its accuracy as the machine gets older.
The second factor in figuring out response time of a clutch is actually much more important than the magnet wire or the air gap. It involves calculating the amount of inertia that the clutch needs to accelerate. This is referred to as “time to speed”. In reality, this is what the end-user is most concerned with. Once it is known how much inertia is present for the clutch to start then the torque can be calculated and the appropriate size of clutch can be chosen. Most CAD systems can automatically calculate component inertia, but the key to sizing a clutch is calculating how much inertial is reflected back to the clutch or brake.
To do this, engineers use the formula: T = (wk2 ? ?N) / (308 ? t) Where T = required torque in lb-ft, WK2 = total inertia in lb-ft2, ? N = change in the rotational speed in rpm, and t = time during which the acceleration or deceleration must take place. There are also online sites that can help confirm how much torque is required to accelerate a given amount of inertia over a specific time. Circuit design and analysis OBJECTIVE A control circuit is to be designed to control the motor and drive unit. The Design specifications are to be fully implemented.
An incomplete circuit and equipments are given and once it is understood appropriate values for the different components should be decided. These values should allow the circuit to perform as specified. Design Specification A circuit is to be designed which is 1. Allows the angular speed of the motor to build up to a value of 20 revolutions per minute (rpm), in a time of 2 seconds (s). 2. Maintains the angular speed of 20 rpm for a time of 3s. 3. When clutch pedal is pressed it brings the machine to a halt in a time of 1s. 4.
Builds up the angular speed again to 20 rpm, in a time of 2s, except this time in the opposite direction. 5. Maintains the angular speed of 20 rpm for a time of 6s. 6. Brings the machine to a halt in a time of 1s. 7. Repeats the cycle above (1-6) indefinitely when powered on. The motor must not be in dynamic braking mode at the same time as it is being driven. CIRCUIT OPERATION The initial design for the complete circuit is shown below. All references to components refer to this circuit diagram. * ANALOGUE SECTION When power is supplied to the circuit the 555 Timer switches on and its output pulses high.
The initial high pulse is longer because the 555 Timer is initially at 0V. The capacitor C3 usually charges from 1/3Vcc to 2/3Vcc. However initially it has to charge from 0V to 2/3Vcc. The duration of this initial high pulse is ta = 1. 1(R6 + R7)*C3 After the initial high pulse a constant charge time is the capacitor charge time is given as tc= 0. 693(R6 + R7)*C3 (1) The output of the timer is brought up to +5V by R5. Pin 3 of the 555 Timer is at +5V when the output is at logic high.
TR2 is then forward biased due to the fact that it is a NPN transistor and its collector is grounded. TR2 has a base current limiter R4. TR1 has a base current limiter R2. Transistor TR1 is now reversed bias (i. e. it is open circuited) and C1 now charges up via resistor R1. As a result the motor turns on. If suitable values of resistor R1 and capacitor C1 are used then the required waveform will be obtained for the analogue output. The duration of this low pulse is td= 0. 693(R7)*C3 (2) Pin 3 of the 555 Timer goes to 0V.
TR2 is then reverse biased due to the fact that it is a NPN transistor and its collector is at +5V. Transistor TR1 is now forward biased (i. e. it is short-circuited) and C1 now discharges. The motor is now switched off. * Digital Section The voltage at the collector of TR2 provides the input clock pulse for IC2, which is configured so that it is triggered on the rising edge. Both the inputs A1 and A2 are always grounded. When the output from pin 3 of the 555 Timer is high the transistor TR2 forward biased. Therefore the input to IC2 is high. It is seen that when this occurs the output Q is high.
This in turn becomes a clock signal for the J-K flip- flop (IC3) and provides Logic 1 on one of the OR-gate inputs of IC4. After IC2 is triggered, it remains high for a time determined by the formula tw= C2*R8*ln2 (3) C2 and R8 control the length of time of braking as well as switching the direction of the motor. When IC2 is reset a pulse is sent to the negative edge triggered J-K flip-flop (IC3). From the Data sheet for (IC3) it is seen that with the clear high and both the inputs J and K high the JK toggles.
Assuming that the initial state of (IC3) is Q = 1 and Q = 0, A is initially at logic 0 and B is at logic 1. Therefore the motor will rotate to the left in an anti-clockwise direction. When IC 2 is being triggered logic 1 will be applied to both of the OR-Gates of IC4. As a result A and B will be high. The motor will now be in dynamic braking mode. When the IC 2 is reset, Q now is logic zero and Q is logic high. Therefore A will be high and B will now be zero. The motor will now run in a clockwise direction. When the IC 2 is re-triggered it will again be in dynamic braking mode.
Circuit Simulation PSpice Before building the circuit that the group had modified and it was necessary to simulate its operation to see if the design we had would work correctly i. e. within the parameters. The simulation was carried out in an electrical simulation package Pspice. Pspice is a useful design tool that allows the testing of electrical circuits without the necessity to build them. It allows designs to be modified quickly and easily so that new ideas and improvements can be incorporated, before the circuit is constructed.
This saves time and a considerable part of the effort when de-bugging the wiring and operation of the circuit. There were a number of reasons that the group simulated the circuit before going to the actual building stage. The main advantage was that Pspice allowed us to use theoretical values for components so we could get the timing of the circuit-very important in this case- exactly right. Although this does not mean that ‘ideal’ components may be used in practice it allowed us to narrow the range of available components that were required. This saved time when building and testing the circuit.
Another advantage was that the wiring of ICs (Integrated circuit) was made simpler because we could use the Pspice schematics as a visual aid COMPONENTS USED Resistors The resistor's function is to reduce the flow of electric current. This symbol is used to indicate a resistor in a circuit diagram. There are two classes of resistors; fixed resistors and the variable resistors. They are also classified according to the material from which they are made. The typical resistor is made of either carbon film or metal film. There are other types as well, but these are the most common.
Fixed ResistorsA fixed resistor is one in which the value of its resistance cannot change. Carbon film resistorsThis is the most general purpose, cheap resistor. Usually the tolerance of the resistance value is ±5%. Power ratings of 1/8W, 1/4W and 1/2W are frequently used. Carbon film resistors have a disadvantage; they tend to be electrically noisy. Metal film resistors are recommended for use in analog circuits. The physical size of the different resistors is as follows. METAL FILM RESISTOR| | Metal film resistors are used when a higher tolerance (more accurate value) is needed.
They are much more accurate in value than carbon film resistors. They have about ±0. 05% tolerance. They have about ±0. 05% tolerance. Resistors that are about ±1% are more than sufficient. Ni-Cr (Nichrome) seems to be used for the material of resistor. The metal film resistor is used for bridge circuits, filter circuits, and low-noise analog signal circuits. From the top of the photograph 1/8W (tolerance ±1%) 1/4W (tolerance ±1%) 1W (tolerance ±5%) 2W (tolerance ±5%)| Rough size| Rating power (W)| Thickness (mm)| Length (mm)| | | 3| 1/4| 2| 6| 1| 3. 5| 12| 2| 5| 15| |
VARIABLE RESISTORThere are two general ways in which variable resistors are used. One is the variable resistor which value is easily changed, like the volume adjustment of Radio. The other is semi-fixed resistor that is not meant to be adjusted by anyone but a technician. It is used to adjust the operating condition of the circuit. Capacitors The capacitor's function is to store electricity, or electrical energy. The capacitor also functions as a filter, passing alternating current (AC), and blocking direct current (DC). This symbol is used to indicate a capacitor in a circuit diagram.
The capacitor is constructed with two electrode plates facing each other, but separated by an insulator. When DC voltage is applied to the capacitor, an electric charge is stored on each electrode. While the capacitor is charging up, current flows. The current will stop flowing when the capacitor has fully charged. Electrolytic Capacitors (Electrochemical type capacitors) The most important characteristic of electrolytic capacitors is that they have polarity. They have a positive and a negative electrode. [Polarised] This means that it is very important which way round they are connected.
If the capacitor is subjected to voltage exceeding its working voltage, or if it is connected with incorrect polarity, it may burst. It is extremely dangerous, because it can quite literally explode. Make absolutely no mistakes. Generally, in the circuit diagram, the positive side is indicated by a "+" (plus) symbol. Electrolytic capacitors range in value from about 1µF to thousands of µF. Ceramic capacitors Ceramic capacitors are constructed with materials such as titanium acid barium used as the dielectric. Internally, these capacitors are not constructed as a coil, so they can be used in high frequency applications.
Typically, they are used in circuits which bypass high frequency signals to ground. These capacitors have the shape of a disk. Their capacitance is comparatively small. TRANSISTORSThe transistor's function is to amplify an electric current. Many different kinds of transistors are used in analog circuits, for different reasons. This is not the case for digital circuits. In a digital circuit, only two values matter; on or off. The amplification abilitiy of a transistor is not relevant in a digital circuit. In many cases, a circuit is built with integrated circuits(ICs). Transistors are often used in digital circuits as buffers to protect ICs.
For example, when powering an electromagnetic switch (called a 'relay'), or when controlling a light emitting diode. (In my case. ) Two different symbols are used for the transistor. PNP type and NPN type INTEGRATED CIRCUITSAn integrated circuit contains transistors, capacitors, resistors and other parts packed in high density on one chip. Although the function is similar to a circuit made with separate components, the internal structure of the components are different in an integrated circuit. The transistors, resistors, and capacitors are formed very small, and in high density on a foundation of silicon.
They are formed by a variation of printing technology. There are many kind of ICs, including special use ICs. DIODEA diode is a semiconductor device which allows current to flow through it in only one direction. Although a transistor is also a semiconductor device, it does not operate the way a diode does. A diode is specifically made to allow current to flow through it in only one direction. Some ways in which the diode can be used are listed here. A diode can be used as a rectifier that converts AC (Alternating Current) to DC (Direct Current) for a power supply device.
Diodes can be used to separate the signal from radio frequencies. Diodes can be used as an on/off switch that controls current. This symbol is used to indicate a diode in a circuit diagram. The meaning of the symbol is (Anode)(Cathode). Current flows from the anode side to the cathode side. RELAYThe relay takes advantage of the fact that when electricity flows through a coil, it becomes an electromagnet. The electromagnetic coil attracts a steel plate, which is attached to a switch. So the switch's motion (ON and OFF) is controled by the current flowing to the coil, or not, respectively.
A very useful feature of a relay is that it can be used to electrically isolate different parts of a circuit. It will allow a low voltage circuit (e. g. 5VDC) to switch the power in a high voltage circuit (e. g. 100 VAC or more). The relay operates mechanically, so it can not operate at high speed. | WIRING MATERIALWire is used to electrically connect circuit parts, devices, equipment etc. There are various kinds of wiring materials The different types of wire can be divided largely into two categories: single wire and twisted strand wire, single wire is used to connect devices (resistors, capacitors etc. together on the PWB. It is also used for jumper wiring. Twisted strand wire can bend freely, so it can be used for wiring on the PWB, and also to connect discrete pieces of equipment. If single wire is used to connect separate equipment, it will break soon, as it is not very flexible. It is convenient to use the single tin coated wire of the diameter 0. 32 mm for the wiring of PWB. If the diameter is larger, soldering becomes a little bit difficult. And if the diameter is too thin, it becomes difficult to bend the wire the way you want it to stay.
DiscussionsElectro-Magnetic CompatibilityElectromagnetic compatibility is a field which is becoming ever more important in the modern world as the use of electronic devices becomes even more widespread. It refers to the effect of electromagnetic waves on an electrical device and the degree to which this device affects other devices in the neighbourhood. This interference can act in a number of ways. Conduction – the interference occurs because of a current flow into the circuit from an external source or from one part of the circuit to another via an unintended path. e. g. a loose wire.
Inductive coupling – the interference is caused by a magnetic field in the neighbourhood of the device. This can affect the electrons flowing in the wires of the device. Capacitive coupling – the interference is caused by an electric field in the vicinity of the device. This also affects the current flowing in the device. Radiation – this type of interference is caused by waves in the electromagnetic spectrum. One example of this is radio waves being affected by radiation from a nearby mobile phoneIn the control circuit for the de-burring machine there were very few sources of EM interference.
The voltage levels used meant that any waves generated would probably not be of sufficient power to affect external devices. The time was not available to measure the interference being generated by the control circuit but if a real company was planning to develop this product they would have to test it thoroughly to ensure that no compatibility problems would exist under normal operating conditions. For example in a factory environment it is possible that the circuit could be placed near sensitive devices such as computers.
The reverse is also true the manufacturer must check to ensure that the circuit is not adversely affected by the other forms of EM interference generated in the workplace by devices such as robots, air conditioning systems and motors. One advantage of the control circuit for the de-burring machine is that it is very compact so it would therefore not be too expensive to construct a case which would shield the device from external sources of EM waves and also contain any emissions generated by the device. It would also be possible to put a filter on the analogue output from the circuit to remove any noise being picked up by the circuit.
This would ensure that the analogue output was not seriously affected; however it is not really necessary. The analogue output level for the device was chosen to be 1. 2V because this gives a relatively low RPM however it could be raised so that any noise picked up would only alter the analogue output by a very small percentage. The gearing could then be adjusted to give the correct speed. The largest source of EM emissions from the de-burring machine would probably be the motor itself. This is because of the magnetic fields generated by the rotor and stator coils.
As stated on the motor data sheet no testing has been carried out on the EMC of the motor but no effect has been noticed on the circuit. The simplest solution to any problems caused by the motor would be to place some form of shielding around the motor or to place the motor a distance away from the control circuit. GearingThe motor and control unit used in the construction of the circuit was not suitable for operation at the low RPM required for the drum of the de-burring machine. The lowest voltage possible speed input to the control unit was 500 rpm when the input voltage was 1V.
In order to scale down the speed of the drum it was decided to use a gearing unit. In order to meet the specifications of the design brief it is required to drop the speed of the motor to 20rpm. Given the current design of the circuit the output voltage of 1. 2V gives a speed of 800rpm. This means that a gear ratio of 800:20 or 40:1 is required. This can be achieved by using two gear wheels with diameters in the ratio 40:1 but this would not be practical as it would require one wheel to be a great deal larger than the other. Using 2 gear wheels would also result in the drum turning in the opposite direction and this is undesirable.
Gear TrainsAnother possible gear combination to achieve the required reduction in speed would be to use three cogs. The first two would be in the ratio 8:1 and then the second two in the ratio 5:1. To achieve this a ‘gear train’ would have to be formed as shown in figure 5. 1. This would save space and also correct the problem of the drum rotating in the wrong direction as the second cog would reverse the direction then the third would return it to normal. Planetary GearingAn even more compact method of gearing would be to use what is known as a planetary gear.
In this type of gearing mechanism the smaller cogs are fitted inside the larger cogs as shown in figure 5. 2 below. The red cogs are held stationary and the yellow gear is connected to the input. This saves space by having the input and output on the same axis and also makes the mechanism more robust by using three central gears instead of one. This would reduce the servicing required by the machine which is an important consideration in industry. The red and yellow gears would be in the ratio of 5:1 and the blue and red gears would have to be in the ratio 8:1 to give the required 40:1 reduction.
Worm GearsThe final type of gear to be considered is the worm gear (figure 5. 3). In this system the reduction factor can be very large which would allow one cog to make the 40:1 reduction? Worm gears also have the useful property of being one way. The angle between the worm and the gear teeth is such that the worm can turn the gear but the gear cannot be used to turn the worm. This would be particularly useful as an additional form of braking for the drum of the de-burring machine however the circuit would have tobe re-designed to slow the analogue output from its full voltage to zero gradually.
If this were not done the gears would lock when the motor stopped and the sudden jerk would place a great stress on the components. If the circuit was to be re-designed as suggested the dynamic braking of the motor would be redundant. Improvements to DesignAfter completion of the circuit it was evident that a number of improvements could be made to the design that would make the circuit more versatile or better suited to its task. These will be covered in this section with the aim of showing possible routes for further development of the circuit. Had time permitted some of these could have been tried in the laboratory.
Perhaps the simplest of the possible routes for improving the circuit is the replacement of resistors R6 and R6 with variable resistors. This would allow the forward and reverse times for the drum spinning to be altered. In this way the most suitable length of time for the parts to be de-burred can be found without the need to re-build the circuit. It would also mean that different components, requiring different lengths of time, could be de-burred in the same machine, although not at the same time. This would allow the machine to be more flexible and save the company money.
By using variable resistors the times could also be fine tuned to compensate for any errors in the timing caused by the tolerances of the components used and also any extra resistance caused by the non-ideal nature of the components. Another improvement to the design would be to eliminate the extended first pulse from the 555 timer which causes the drum to rotate longer on its first cycle. Because the pulse is part of the operation of the 555 timer it is hard to alter before it affects the analogue out so one solution would be to have some form of clutch system between the drum and motor.
This would disengage the drum from the motor at start-up and not allow the drum to be turned until after the first cycle. Some form of circuit could be designed to control the clutch and only engage the motor after the first cycle has passed. Another alternative would be to have the clutch only engage after a set time equal to the duration of the first cycle. This could either be a mechanical or electrical timer and would be required to engage the clutch after 7. 746... +1+8=16. 75sec. Some form of switch could also be incorporated into the circuit to reset the JK flip-flop each time the circuit is switched on.
This ensures that the flip-flop always starts in the correct state and that the motor is always turning in the right direction for its first rotations. This switch would also allow the cycle to be restarted without turning the power off. Such a function could be simply implemented by connecting the reset pin to +5V via a switch. A final consideration when improving the circuit would be to alter the switching circuit for R6 in such a way that one resistor is always connected and connecting a second resistor in parallel with it alters the total resistance as shown in figure A.
A-Alternative Switching CircuitPractical ConsiderationsWhile the motor circuit worked as required in the laboratory test, a number of other factors must be brought into consideration when the circuit is being designed for use in industry. One of the major factors has already been discussed in the section on EMC but there are many more will be briefly covered in this section. One of the most obvious differences between the test equipment and an industrial system is the motor being driven.
For safety reasons the motor connected to the circuit was a low power motor but to drive a large drum a larger motor with a higher torque would be required. While the controller card used can only support motors with an operating voltage up to 30V, a similar controller could be designed to operate at much higher output voltages while still being run off of the same circuit. Another possibility would be to run a number of motors off of on control circuit. This would allow a much greater number of parts to be de-burred without the need for an exceptionally large drum. This would introduce the problem of fan-out however.
The relatively low analogue output voltage of 1. 2V would have to be increased if a large number of controller cards were to be driven. The same is true of the voltages from the OR gates controlling direction. This is problem is easily rectified by using op-amps to boost the voltage. When the system is being used in a factory environment there are also a number of environmental issues to be deal with. There could be a great deal of dust or fine particles of metal in the air from the de-burring process, it is also possible that in an automated process the factory may not be heated.
Placing the control circuit in a sealed container can resolve some of these issues, as this will prevent dust from affecting its operation. It would also be possible to incorporate shielding into this casing to improve EMC. The temperature issue is not very important, as it is unlikely that the operating ranges of the IC would be exceeded. For 74 series chips this is in the region of 0-70? C and 54 series chips have an operating range of about –50-120? C. The final consideration when constructing a system for industry would be ease of manufacture.
If a large number of these machines were required the circuit would have to be laid out in such a way that it could be easily constructed on printed circuit boards. There are computer programs available to aid the designer in this process and it would be unlikely to cause a major problem. ConclusionsHaving designed and constructed the circuit it was felt that it met all of the given specifications although there were still a number of improvements that could have been made. These improvements have been covered briefly in the discussion section and given more time they could have been implemented in the circuit.
As already mentioned the only specifications not met were that on start-up the machine should rotate for 3 seconds in one direction before braking and reversing. Using the clutch method mentioned in the discussions could solve this but the design brief given did not extend to cover the drum so has not been included in the final design. During the course of the project a number of other points became evident which greatly ease the process of designing an electronic circuit. Simulation using a computer package such as Pspice saves a considerable amount of time by allowing the circuit to be easily laid out and tested.
Any changes required can be made easily without disturbing the rest of the circuit. Another advantage of Pspice is the ability to produce graphs of the outputs from the circuit, which can then be scaled, formatted and printed as required. To do this for the actual circuit requires very specialised and expensive equipment. In conclusion, the group felt that all objectives had been met and that the final circuit was successful in fulfilling its role. A number of important lessons were learned about the problems involved in designing a circuit to meet a real-world need and ways of overcoming these problems were found.
BILL OF MATERIALS S. NO. | ITEMS| Quantity| PRICE | 1. | motor| 1| | 2. | Diode | | | 3. | capacitor| | | 4. | 555 timer| | | 5. | Relay switch| | | 6. | Coils| | | 7. | resistances| | | 8. | transformer| | | 9. | Wiring materials| | | 10. | Integrated circuit| | | 11. | Wiring board| | | References[1] Schematic Capture with Microsim Pspice Herniter Prentice Hall 3 Ed. Rd P250-252[2] http://www. emclab. umr. edu/An Introduction to EMCUniversity of Missouri-Rolla EMC laboratory[3] http://reality. sgi. com/csp/scvemc/emcdef. tmlEnsuring Compatibility Between the Electromagnetic Environment and Electric and Electrical Devices Kimball William, Chairman, IEEE EMC Education Committee[4] http://www. howstuffworks. com/gears. htmHow gears Work[5]www. scribd . com[6]www. mechanicalprojects. comBackground Reading * Digital Fundamentals Floyd Prentice Hall 7 Edition t h. * Introductory Circuit Analysis Boylestad Prentice Hall 9 Edition t h. * Machine Design - R. K. Rajput. * Kinematics Of Machine – R. S. khurmi. * Automobile Engineering – R. K. Rajput | | |
Cite this Page
Study of Electromagnetic Clutch. (2017, Jan 29). Retrieved from https://phdessay.com/study-of-electromagnetic-clutch/
Run a free check or have your essay done for you
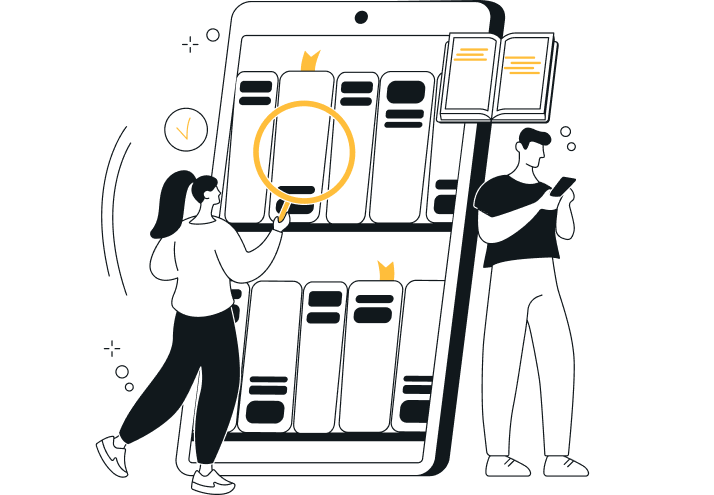