Volume Variety Matrix
Volume-variety and design In Chapter 1 the four V’s of operations were described. These were volume, variety, variation and visibility. The first two of these – volume and variety – are particularly important when considering design issues in operations management. Not only do they usually go together (high variety usually means low volume, high volume normally means low variety) but together they also impact on the nature of products and services and processes which produce them. The volume and variety of an operation’s activities are particularly influential in determining the way it thinks about its performance objectives.
The figure below illustrates how the definitions of quality, speed, dependability, flexibility and cost are influenced by the volume-variety position of the operation. [pic] Quality Quality in a low volume-high variety process such as an architects’ practice, for example, is largely concerned with the final aesthetic appearance of the building and the appropriateness of its detailed design. In an exceptionally high volume-low variety process, such as an electricity supply company, quality is exclusively concerned with error-free service – electricity must be constantly available in the correct form (in terms of voltage, frequency, etc. . The meaning of quality has shifted from being concerned primarily with the performance and specification of the product or service towards conformity to a predefined standard, as we move from low volume-high variety operations through to high volume-low variety operations. Speed Speed for the architects’ practice means negotiating a completion date with each client, based on the client’s needs and the architects’ estimates of how much work is involved in each project. Speed is taken to its extreme in the electricity utility where speed means literally instant delivery.
No electricity company could ask its customers to wait for their ‘delivery’ of electricity. Speed therefore means an individually negotiated delivery time in low volume-high variety operations, but moves towards meaning ‘instant’ delivery in some high volume-low variety operations. Dependability Dependability in processes such as the architects’ practice means keeping to each individually negotiated delivery date. In continuous operations, dependability often means the availability of the service itself. A dependable electricity supply is one which is always there.
Order custom essay Volume Variety Matrix with free plagiarism report
So dependability has moved from meaning ‘on-time delivery’ in low volume-high variety operations to ‘availability’ in high volume-low variety operations. Flexibility Flexibility in low volume-high variety processes such as the architects’ practice means the ability to design many different kinds of buildings according to its clients’ various requirements. With the electricity company’s process, the need for product flexibility has disappeared entirely (electricity is electricity, more or less) but the ability to meet almost instantaneous demand changes through volume flexibility is vital if the company is to maintain supply.
Flexibility has moved from meaning product flexibility in low volume-high variety operations to volume flexibility in high volume-low variety operations. Cost Cost, in terms of the unit cost per product or service, varies with both the volume of output of the operation and the variety of products or services it produces. The variety of products or services in low-volume operations is relatively high, which means that running the operation will be expensive because of the flexible and high skill levels employed. Further, because the volume of output is relatively low, a few products or services are bearing the operation’s high cost base.
Also, and more significantly for the operation, the cost of each product or service is different. At the other end of the scale, high-volume operations usually produce similar products or services, output is high, so that whatever the base cost of the operation, it is shared among a high number of products or services. Cost per unit of output is therefore usually low for operations such as the electricity utility but, more significantly, the cost of producing one second of electricity is the same as the next second. Cost is relatively constant. Copyright © 1995-2010, Pearson Education, Inc. Legal and Privacy Terms | [pic] [pic] [pic] [pic] LINE. When product demand is high enough, the appropriate process is the assembly line. Often, this process (along with continuous; both are in the lower-right quadrant of the matrix) is referred to as mass production. Laborers generally perform the same operations for each production run in a standard and hopefully uninterrupted flow. The assembly line treats all outputs as basically the same.
Firms characterized by this process are generally heavily automated, utilizing special-purpose equipment. Frequently, some form of conveyor system connects the various pieces of equipment used. There is usually a fixed set of inputs and outputs, constant throughput time, and a relatively continuous flow of work. Because the product is standardized, the process can be also, following the same path from one operation to the next. Routing, scheduling, and control are facilitated since each individual unit of output does not have to be monitored and controlled.
This also means that the manager's p of control can increase and less skilled workers can be utilized. The product created by the assembly-line process is discrete; that is, it can be visually counted (as opposed to continuous processes which produce a product that is not naturally divisible). Almost everyone can think of an example of assembly-line manufacturing (automobile manufacturing is probably the most obvious). Examples of assembly lines in services are car washes, class registration in universities, and many fast food operations.
Because the work-in-process equipment is organized and sequenced according to the steps involved to produce the product and is frequently connected by some sort of conveyor system, it is characterized as flowing in a line. Even though it may not be a straight line (some firms utilize a U-shaped assembly line) we say that it has a connected line flow. Also, firms in the lower-right quadrant (line and continuous) are classified as having a product layout. Continuous manufacturing involves lot-less production wherein the product flows continuously rather than being divided. A basic material is passed through successive operations (i. e. refining or processing) and eventually emerges as one or more products. This process is used to produce highly standardized outputs in extremely large volumes. The product range is usually so narrow and highly standardized that it can be characterized as a commodity. Considerable capital investment is required, so demand for continuous process products must be extremely high. Starting and stopping the process can be prohibitively expensive. As a result, the processes usually run 24 hours a day with minimum downtime (hence, continuous flow). This also allows the firm to spread their enormous fixed cost over as large a base as possible.
The routing of the process is typically fixed. As the material is processed it usually is transferred automatically from one part of the process to the next, frequently with self-monitoring and adjusting. Labor requirements are low and usually involve only monitoring and maintaining the machinery. Typical examples of industries utilizing the continuous process include gas, chemicals, electricity, ores, rubber, petroleum, cement, paper, and wood. Food manufacture is also a heavy user of continuous processing; especially water, milk, wheat, flour, sugar and spirits.
Read more: Product-Process Matrix - strategy, organization, system, examples, manager, company, business, competitiveness, system http://www. referenceforbusiness. com/management/Or-Pr/Product-Process-Matrix. html#ixzz24d4V1uTD [pic] [pic] USING THE MATRIX The product-process matrix can facilitate the understanding of the strategic options available to a company, particularly with regard to its manufacturing function. A firm may be characterized as occupying a particular region in the matrix, determined by the stages of the product life cycle and its choice of production process(es) for each individual product.
By incorporating this dimension into its strategic planning process, the firm encourages more creative thinking about organizational competence and competitive advantage. Also, use of the matrix provides a natural way to involve manufacturing managers in the planning process so they can relate their opportunities and decisions more effectively with those of marketing and of the corporation itself, all the while leading to more informed predictions about changes in industry and the firm's appropriate strategic responses. Each process choice on the matrix has a unique set of characteristics.
Those in the upper-left quadrant of the matrix (job shop and batch) share a number of characteristics, as do those in the lower-right quadrant (assembly line and continuous). Upper-left firms employ highly skilled craftsmen (machinists, printers, tool and die makers, musical instrument craftsmen) and professionals (lawyers, doctors, CPAs, consultants). Hence upper-left firms can be characterized as labor intensive. Since upper-left firms tend to utilize general-purpose equipment, are seldom at 100 percent capacity, and employ workers with a wide range of skills, they can be very flexible.
However, there is a difficult trade-off between efficiency and flexibility of operations. Most job shops tend to emphasize flexibility over efficiency. Since efficiency is not a strong point of upper-left firms, neither is low-cost production. Also, the low volume of production does not allow upper-left firms to spread their fixed costs over a wide enough base to provide for reduced costs. Finally, upper-left firms are also more likely to serve local markets. Lower-right firms require production facilities that are highly specialized, capital intensive, and interrelated (therefore, inflexible).
Labor requirements are generally unskilled or semi-skilled at most. Much of the labor requirement deals with merely monitoring and maintaining equipment. Lower-right firms are also more likely to serve national markets and can be vertically integrated. Hayes and Wheelwright relate three areas affected by the use of the product-process matrix: distinctive competence, management, and organization. DISTINCTIVE COMPETENCE. Distinctive competence is defined as the resources, skills, and organizational characteristics that give a firm a comparative advantage over its competitors.
Simply put, a distinctive competence is the characteristic of a given product that causes the buyer to purchase it rather than the similar product of a competitor. It is generally accepted that the distinctive competencies are cost/price, quality, flexibility and service/time. By using the product-process matrix as a framework, a firm can be more precise about its distinctive competence and can concentrate its attention on a restricted set of process decisions and alternatives and a restricted set of marketing alternatives.
In our discussion, we have seen that the broad range of worker skills and the employment of general-purpose equipment give upper-left firms a large degree of flexibility while the highly specialized, high-volume environment of lower-right firms yields very little in the way of flexibility. Therefore, flexibility would be a highly appropriate distinctive competence for an upper-left firm. This is especially true when dealing with the need for flexibility of the product/service produced. Lower-right firms find it very difficult to sidetrack a high-volume operation because of an engineering change in the product.
An entire line would have to be shut down while tooling or machinery is altered and large volumes of possibly obsolete work-in-process are accounted for. Upper-left firms, however, would have none of these problems with which to contend. It must be noted though that lower-right firms may possess an advantage regarding flexibility of volume. Quality may be defined a number ways. If we define quality as reliability, then lower-right firms could claim this as a distinctive competence. Lower-right firms would have the high volume necessary to quickly find and eliminate ugs in their product, yielding more reliability to the end user. However, if we define quality as quality of design (that is, "bells and whistles"—things that embody status, such as leather seats in an automobile or a handcrafted musical instrument), then quality would be seen as a possible distinctive competence of upper-right firms. Service may also be defined in more ways than one. If one defines service as face-to-face interaction and personal attention, then upper-left firms could claim service as a distinctive competence. If service is defined as the ability to provide the product in a very short period of time (e. . , overnight), then service as a distinctive competence would belong to lower-right firms. Finally, remember that high volume, economies of scale, and low cost are characteristics of firms in the lower-right quadrant of the matrix. Upper-left firms produce low volumes (sometimes only one) and cannot take advantage of economies of scale. (Imagine, for instance, what you would have to pay for a handcrafted musical instrument. ) Therefore, it is obvious that price or cost competitiveness is within the domain of lower-right firms. MANAGEMENT.
In general, the economics of production processes favor positions along the diagonal of the product-process matrix. That is, firms operating on or close to the diagonal are expected to outperform firms choosing extreme off-diagonal positions. Hayes and Wheelwright provide the example of a firm positioned in the upper-right corner of the matrix. This would appear to be a commodity produced by a job shop, an option that is economically unfeasible. A firm positioned in the lower-left corner would represent a unique one-time product produced by a continuous process, again not a feasible option.
Both examples are too far off the diagonal. Firms that find themselves too far off the diagonal invite trouble by impairing their ability to compete effectively. While firms operating in the near vicinity, but not exactly on the diagonal, can be niche players, positions farther away from the diagonal are difficult to justify. Rolls Royce makes automobiles in a job shop environment but they understand the implications involved. Companies off the diagonal must be aware of traps it can fall into and implications presented by their position. Also, a firm's choice of roduct-process position places them to the right or left of competitors along the horizontal dimension of the matrix and above or below its competitors along the vertical dimension of the matrix. The strategic implications are obvious. Of course, a firm's position on the matrix may change over time, so the firm must be aware of the implications and maintain the capability to deal with them appropriately. The matrix can provide powerful insights into the consequences of any planned product or process change. Use of the product-process matrix can also help a firm define its product.
Hayes and Wheelwright relate the example of a specialized manufacturer of printed circuit boards who produced a low-volume, customized product using a highly connected assembly-line process. Obviously, this would place them in the lower-left corner of the matrix; not a desirable place to be. This knowledge forced the company to realize that what they were offering was not really circuit boards after all, but design capability. So, in essence, they were mass-producing designs rather than the boards themselves. Hence, they were not far off the diagonal at all.
ORGANIZATION. Firms organize different operating units so that they can specialize on separate portions of the total manufacturing task while still maintaining overall coordination. Most firms will select two or more processes for the products or services they produce. For example, a firm may use a batch process to make components for products, which are constructed on assembly lines. This would be especially true if the work content for component production or the volume needed was not sufficient for the creation of a dedicated line process.
Also, firms may need separate facilities for different products or parts, or they may simply separate their production within the same facility. It may even be that a firm can produce the similar products through two different process options. For example, Fender Musical Instruments not only mass produces electric guitars (assembly line) but also offers customized versions of the same product through the Fender Custom Shop (job shop). Again, the matrix provides a valuable framework for diagnostic use in these situations.
OTHER USES OF THE PRODUCT-PROCESS MATRIX Additional uses of the matrix include: • Analyzing the product entry and exit. • Determining the appropriate mix of manufacturing facilities, identifying the key manufacturing objectives for each plant, and monitoring progress on those objectives at the corporate level. • Reviewing investment decisions for plants and equipment in terms of their consistency with product and process plans. • Determining the direction and timing of major changes in a company's production processes. Evaluating product and market opportunities in light of the company's manufacturing capabilities. • Selecting an appropriate process and product structure for entry into a new market. It should be noted that recent empirical research by Sohel Ahmad and Roger G. Schroeder found the proposed relationship between product structure and process structure to be significant but not strong. In general terms, they found that as the product life cycle changes the process life cycle also shifts in the consistent direction, but not necessarily along the diagonal.
Some 60 percent of the firms studied did not fall on the diagonal. The researchers propose that this occurred because new management and technological initiatives have eliminated or minimized some of the inherent trade-offs found on the Product-Process Matrix. They classify these initiatives as processing technology, product design and managerial practice (e. g. , TQM and JIT). Therefore, Ahmad and Schroeder recommend that the matrix be conceptualized as having three axes instead of two.
They propose an x-axis (product life cycle stages), a y-axis (process life cycle stages), and a z-axis that represents an organization's proactive effort towards adopting and implementing these innovative initiatives. As a firm moves away from the origin along the z-axis, it becomes able to minimize some of the trade-offs seen in the Product-Process Matrix framework. Read more: Product-Process Matrix - strategy, organization, system, examples, manager, company, business, competitiveness, system http://www. referenceforbusiness. com/management/Or-Pr/Product-Process-Matrix. h tml#ixzz24d4lyOQ5 [pic] [pic] [pic] [pic] [pic] [pic] [pic] [pic]
Related Questions
on Volume Variety Matrix
Cite this Page
Volume Variety Matrix. (2018, Jul 30). Retrieved from https://phdessay.com/volume-variety-matrix/
Run a free check or have your essay done for you
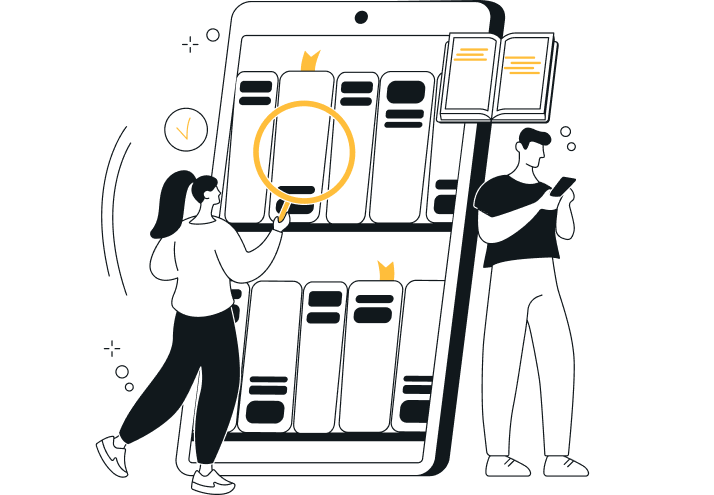