Toyota Motor Manufacturing
Toyota Motor Manufacturing USA, Inc. , (TMM) is confronted with its rising problem with seat supply and one of the main culprits is the seat defects. Reflected in the decreasing run ratio; as a result there is a growing number of cars sitting off-line with defective seats or no seats at all requiring overtime to make up for the loss production. Another issue worth mentioning is the way TMM handles the defective seats as they deviate towards the Toyota Production System (TPS) norms. The seat supply problem is the major issue because it constricts the company to supply the cars on time to the sales company.
The seat problem resulted with a ten point drop on the run ratio from around 95% down to a meager of 85%. This shortfall is equivalent to 45 cars per shift which will give a potential loss of $73,593,000 / year. This shortcoming requires high overtime for the personnel to cope up with the demand in the market. It notches a 50% premium for overtime, resulting to an additional cost of $7,311,542 per annum. The increasing number of cars sitting off the line with defective seats or with no seats at all, end result to a loss in production because of waiting and rework.
There are 18 vehicles found at the parking area having defects in seats which have an equivalent potential loss in sales with $ 679,320 per annum, based on the 17% pretax profit. Advantage: Immediately address problems at the source 1. (See Appendices for Exhibit 2: Problems Arising from Current Process of Handling Seat - Set Mismatch), aligned with the TPS principles, empower employees to remedy problems therefore preventing inventory of problematic cars sitting at overflow, prevents feedback delay through timely information (See Appendices for Exhibit 3: Simulation of Feedback Delay - Time vs.
Order custom essay Toyota Motor Manufacturing with free plagiarism report
Number of Defects). Disadvantage: Standardizing the new process and will incur additional cost for training. (See Appendices for Exhibit 4: Cost Benefit Analysis). Advantage: This would provide additional flexibility for TMM, minimize waiting time, unloads burden from KFS and helps avoid disruption of processes. Disadvantage: Supplier control, time to train the new supplier to match TMMs way of production, and supplier certification cost.
(See Appendices for Exhibit 4: Cost Benefit Analysis). The group recommends implementing all the alternatives. Process improvement in the assembly line by sending TMM - QC personnel to KFS and adding QC inspector at the receiving dock is a worthy investment amounting to $141,440 as compared to the overtime pay of $7,311,542 (See Appendices for Exhibit 4: Cost Benefit Analysis). TMM needs to improve their current problem handling and recovery system.
This alternative is not only financially rewarding (See Appendices for Exhibit 4: Cost Benefit Analysis) but it also supports TPS concept of being dependent on human infrastructure. Lastly, having an additional supplier is recommended for this will further help lighten the burden on KFS as it deals with volume ramp-up and increasing product variations. This alternative aims to eliminate material defects caused by suppliers.
Cite this Page
Toyota Motor Manufacturing. (2018, Jun 06). Retrieved from https://phdessay.com/toyota-motor-manufacturing-2/
Run a free check or have your essay done for you
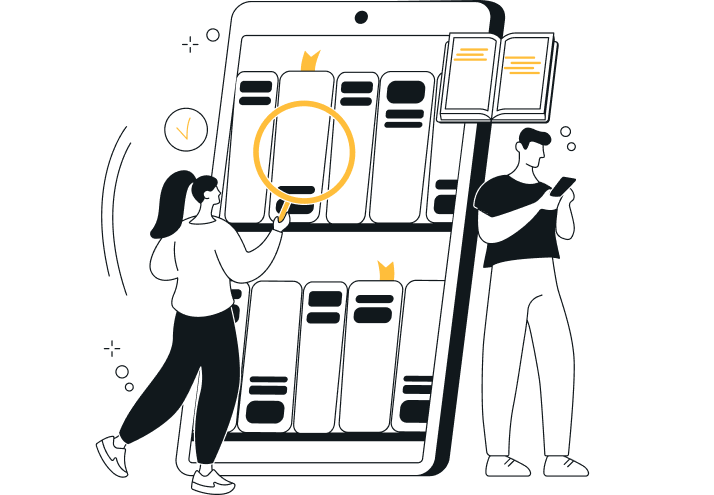