Thermal Coating
Among the components exposed to heat load, piston of internal combustion engine is subject to maximum thermal stress. The large temperature gradient the piston will cause structural deformation deterioration of lubricant and increase the clearance between the cylinder liner and piston there by causing more noise, vibration degrees in the engine service life, the non- uniform temperature gradient arise owing damage of piston especially crown region. Experimental study is conducted on single cylinder 5hp diesel engine in order to find the improved performance when a ceramic coating is given especially in the piston crown.
Among the ceramics, Yttria partially stabilized Zirconia (YPSZ) is being favoured for diesel engines since its co efficient of thermal expansion is close to those of metals used in piston. This avoids problems relating to difference in thermal expansion between metallic and thermal parts which also increases its durability. Compared to the conventional engine (without coating over the piston crown) the modified engine (with ceramic coating over the piston crown) did not produce any observable knock in the engine, no significant wear of piston crown.
Various graphs are drawn to check the improved performance of the engine when it is at with and without ceramic coating on the piston crown, and found that there is 5-6% decrease in SFC, 4-5% increase in brake thermal efficiency and 8-9% increase in mechanical efficiency.
Order custom essay Thermal Coating with free plagiarism report
Introduction
Thermal barrier coatings were originally developed for air craft engine applications in 1940; only recently have they been modified and tested for use in diesel engines.
Although diesel engines has greater compressive loads and more frequent thermal shocks, in additional, diesel TBC’s must cope with contaminants (Sodium, Vanadium, Sulphur ) often found in lower grade fuels. If these difference in engine operating conditions are ignored when choosing and applying a T. B. C premature failure of the coating can result. Diesel TBC’s are coating systems metallic bond coat and ceramic topcoat applied by the plasma thermal spray process; control of total coating thickness is critical. If not maintained within 0. 8mm, spallation of the coating can occur due to uneven heating and cooling of the process of the topcoats, Robotic thermal spraying provides the required thickness and compare values with established standards. Basically, there are three techniques of thermal spraying. The basic principle is the same for all (i. e. ) material is melted and propelled as finely atomized towards the target as the particle strike the surface they flatten and form thin platelets that conform and adhere to the irregularity of the prepared surface and to each other.
The three techniques differ essentially in the fuel and the method of heating/ melting used. These differences give to the advantage and limitations which to considerable extent govern their range of applications. Thermal spraying infact is a group of processes i. e. , 1. Surface preparation and 2. Thermal spraying Both are basically important as far as quantity of the coating is concern. Coating of a material on a substance is made to serve in the specific environment and service conditions.
It is possible only if the coating is adherent to the surface of the component, on which it is sprayed, tthroughout its useful life. If the coating flakes off or leaves the surface, the entire effort will go waste. The adhesion and other properties of the coating mainly depend on the surface condition of the substrate.
Cite this Page
Thermal Coating. (2018, Aug 28). Retrieved from https://phdessay.com/thermal-coating/
Run a free check or have your essay done for you
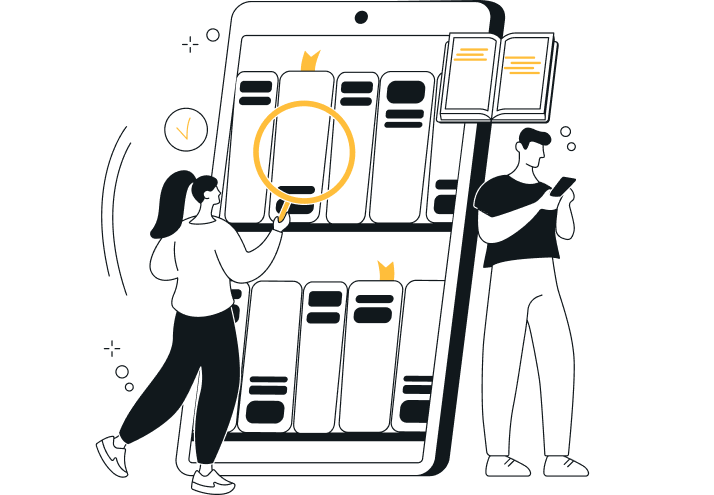