The Simulink Model
The Simulink model were simulated and the result are in the table 4.1, 4.2, and 4.3, below.
Direct torque control (DTC) and fuzzy logic with duty ratio model were designed.
Because we want to control the motor drives in order to reduce the high ripple torque of the motor.
Order custom essay The Simulink Model with free plagiarism report
In the principles of direct torque control of motor, the ripples in the motor can be reduced if the errors of the torque and the flux linkage and the angular region of the flux linkage are sub-divided into several smaller sub-section then the errors should be pick and compared in other to select voltage vector with less ripples, in doing so, a more accurate voltage vector is being selected in the switching of the system hence the torque and flux linkage errors were reduced.
In the ordinary direct torque control, a voltage vector is applied for the entire switching period, and this causes the stator current and electromagnetic torque to increase over the whole switching period. Thus for small errors, the electromagnetic torque exceeds its reference value early during the switching period, and continues to increase, causing a high torque ripple. This is then followed by switching cycles in which the zero switching vectors are applied in order to reduce the electromagnetic torque to its reference value.
The ripple in the torque and flux can be minimize by applying the selected inverter vector for a complete switching period, as in the ordinary direct torque control motor drive, but only for a part of the switching period. The time for which a non-zero voltage vector has to be applied is selected just to increase the electromagnetic torque to its reference value and the zero voltage vector was applied for the rest of the switching period.
During the application of the zero voltage vector, no power was consumed by the machine, and thus the electromagnetic flux is almost constant, it was only decreases slightly. The average input DC voltage to the motor during the application of each switching vector was Vdc. By adjusting the duty ratio between zero and one, it is possible to apply voltage to the motor with an average value between 0 and Vdc during each switching period.
Thus, the Torque ripple will be low compared to when the full DC link voltage was applying for the complete switching period. This increases the demand of the voltage vector, without an increase in the number of semiconductor switches in the inverter.
The duty ratio of each switching period is a non-linear function of the Electromagnetic torque error, stator flux-linkage error, and the position of the stator flux linkage space vector. Therefore, by using a fuzzy-logic-based direct torque control system, it is possible to perform fuzzy-logic-based duty-ratio control, where the duty ratio is determined during each switching cycle. In such a fuzzy logic system, there are three inputs, the electromagnetic torque error, the stator flux-linkage space vector position (??) within each sector assigned with the voltage vectors and the flux error where the output of the fuzzy-logic controller is equal to the value of duty ratio.
There are various types of fuzzy logic controller for this particular application. A Mamdani-type fuzzy logic controller, which contains a rule base, a fuzzifier, and a defuzzifier, is selected. Fuzzification is performed using membership function. The inputs and the output of the fuzzy controller are assigned Gausian membership functions. The universe of discourse for the torque error and the duty ratio is varied using simulations to get acceptable torque ripple reduction.
The attention in the fuzzy rule is to reduce the torque ripple. Generally the duty ratio is proportional to the torque error, since the torque rate of change is proportional to the angle between the stator flux and the applied voltage vector, the duty ratio depends on the position of the flux within each sector. The use of two fuzzy sets is the fact that when the stator flux is greater than its reference value a voltage vector that advance the stator flux vector by two sectors is applied which result in a higher rate of change for the torque compared to the application of a voltage vector that advance the stator flux vector by one sector when the stator flux linkage is lower than its reference value.
The duty ratio is selected proportional to the magnitude of the torque error so that if the torque error is Small, Medium or Large THEN the duty ratio is Small, Medium orLarge respectively. The fuzzy rules are then adjusted to reflect the effects of the flux error, torque error and position of the space vector error. If the torque error is medium and the stator flux lies in sector with magnitude greater than its reference value then the voltage vector Vk+2 is selected.
If the flux position is small, that means there is a large angle between the flux and the selected voltage vector that makes the selected vector more effective in increasing the torque so that the duty ratio is set as small rather than medium, the fuzzy rule is stated as IF (torque error is medium) AND (flux position is small) THEN (duty ratio is small)IF (torque error is large) AND (flux position is small) THEN (duty ratio is medium).
Using the above reasoning and simulation to find the fuzzy rules, the two sets of fuzzy rules are summarized in Table 3.2 below.
Table 3.2 Rules for the duty ratio fuzzy controller
- Flux Torque error dT=k1 Small Medium Large
Negative - d?=0 Small Small Small Medium
- Large Small Medium Large
Positive - ?d=1 Small Small Medium Large
- Medium Small Medium Large
- Large Medium Large Large
The fuzzy logic toolbox was used in the implementation of the duty ratio fuzzy controller. The Graphic User Interface included in the toolbox was used to edit the membership functions for the inputs (the torque error and the flux position),the output (the duty ratio). The membership functions and the fuzzy rules were adjusted using the simulation until an acceptable torque ripple reduction was achieved.
Simulate the model above in the Simulink environment and validate the result.
The model that will reduced the high ripple torque in the induction motor were developed.
To enable us study the performance of the conventional direct torque control and fuzzy logic with duty ratio controller for four (4) pole motor torque control and also to simulate for the same and verified for the purpose of reducing the high torque ripple in the motor drive.
The motor data's
Definition of terms
- Pa = Active power per phase
- Qa = Phase reactive power
- Ia = Phase current
- Va = phase voltage
- Rs = Stator winding resistance
- Rr = Rotor winding resistance
- Lm = Magnetizing inductance per phase
- Xis = Stator leakage reactance
- Lis = Stator inductance per phase
- Xir = Rotor leakage reactance
- Lir = Rotor leakage inductance per phase
- Dc = Direct current
- Rdc = Resistance in direct current
- X = Reactance
- Xm = Magnetizing reactance
- Xn = Total reactance
DETERMINATION OF INDUCTION MOTOR DATAS
- The motor is a three phase 158-W, 240-V induction motor (Model 295 Bodine Electric Co.)
- The motor is Y-connected with no access to the neutral point.
- DC Resistance Test:
- To determine R1;
- Connect any two stator leads to a variable voltage DC power supply.
- Adjust the power supply to provide rated stator current.
- Determine the resistance from the voltmeter and ammeter readings.
- As shown in figure 3.7, a DC voltage VDC is applied so that the current IDC is close to the motor rating.
- Because the machine is Y-connected: RS = Rdc/2 = (VDC/IDC)/2.
- From measurement, VDC = 30.6V, IDC = 1.05A.
- Hence, RS = RDC = (31.5/1.04) = 15.14?/phase.2 2
Figure 3.7 Circuit for DC resistance test.
BLOCKED – ROTOR TEST
- To determine X1 and X2
- Determine R2 when combined with data from the DC test.
- Block the rotor so that it will not turn.
- Connect to a variable voltage supply and adjust until the blocked – rotor current is equal to the rated current.
- NO LOAD TEST
- To determine the magnetizing reactance, Xm and combined core, friction, and wind age losses.
- Connect as in block rotor test below.
- The rotor is unblocked and allowed to run unloaded at rated voltage and frequency.
- The set up for no load test and blocked rotor test is shown in the figure below:
Figure 3.8 Circuit for no load and locked rotor test.
- With the motor running at no load, measure V, I and P to find the machine reactance Xn =Xis+Xm
- Table 4.3 Measured value
- Frequency (Hz) 50
- Voltage (V) 230
- Current (A) 1.32
- Real power (W) 158
At no load the per-unit slip is approximately zero, hence the equivalent circuit is as shown in figure 3.9 below.
Figure 3.9 Equivalent circuit of three phase induction motor under no load test.
- The real power P represents,
- Hysteresis and Eddy current losses (core losses)
- Friction and wind age losses (rotational losses)
- Copper losses in stator and rotor (usually small as no load)
Phase voltage:
- Va =V = 220 = 132V
- ?3 ?3
Phase current:
- la = 1.32A
Phase real power:
- Pa = Pa/3 = 138.2 ÷3 = 46.1W
Phase reactive power:
- Q_a = ??(VaIa)2-P2a= ?(((137 x 1.32)2)-(46.1)2)=174.86VAr?_
- Xn = Qa=174.86 =100.36?
- I2a 1.322
- Since S ~ 0,
- Xn~ Xls +Xm
Locked rotor test
With the rotor locked, the rotor speed is zero and per- unit slip is equal to unity. The equivalent circuit is as shown in Figure 3.10 or Figure 3.11.
Figure 3.10 Equivalent circuit of three phase induction motor under locked rotor test.
Figure 3.11 Simplified equivalent circuit of three phase induction motor under locked rotor rest.
Table 4.4 the tested value
- Frequency (Hz) 50
- Voltage (V) 68.52
- Current (A) 1.3
- Real power (W) 105.33
Phase voltage:
- Va =V = 68.52 = 39.56V
- ?3 ?3
Phase current:
- la = 1.3A
Active power per phase
- Pa = P = 105.33=35.1W
3 3
Reactive power phase
- Q_a = ??(VaIa)2-P^2 a= ?(((35.56 x1.3)2)-(35.1)2)=30.08VAr?_
For a class C motor.
- Xls = 0.3 x Qa= 0.3 x 30.08 = 5.34?
I2a 1.32 - Xlr = 0.7 xQa = 0.7 x 30.08 = 12.46?
12a 1.32 - From the no – load test, Xn = 100.36?, so
- Xm = Xn – Xls = 100.36 - 5.34 = 95.02?
- R = Pa = 35.1 = 20.77?
12a 1.32
From figures 3.11,
- R2 = R – Ris= 20.77 – 5.34 = 1 5.43?
Comparing figures 3.10 and 3.11,
- R2 + jX2 = (Rr + jXir) x jXm
- (Rr + jXir) + jXm
- R2 =Rr X2m
- Rr + (Xlr + Xm)2
- Rr = R2 x (Xir + Xm)2 = 15.43 x (12.46 + 95.02)2 = 19.74?
- Xm 95.02
Summarizing,
- Stator winding resistance Rs = 15.14?/phase
- Rotor winding resistance Rr = 19.74?/phase
- Magnetizing reactance Xm = 95.02?/phase
The magnetizing inductance per phase is
- Lm = Xm = 95.02 = 0.3024H
- 2?f 2? x 50
Stator leakage reactance Xls= 5.34?/phase
The stator inductance per phase is
- Lls = Xls= 5.34 = 0.0169H.
- 2?f 2nx50
Rotor leakage reactance Xlr = 12.46?/phase,
The rotor leakage inductance per phase is
- Llr = Xlr =12.46 = 0.0396H.
- 2?f 2?x50
Table 4.5: Motor parameters
- Rated voltage 240V
- Maximum torque 1.5N-m
- Poles 4
- Rated speed 1440rpm
- Stator resistance 15.14?
- Rotor resistance 19.74?
- Stator leakage inductance 0.0169H
- Rotor leakage inductance 0.0396H
- Mutual inductance 0.3024H
IMPLEMENTATION
MATLAB fuzzy logic tool box was used in the implementation of the duty ratio fuzzy controller. The graphic user interface included in the tool box was used to edit the membership functions for the inputs (the torque error and the flux position), the output (the duty ratio). A Mamdani type fuzzy inference engine was used in the simulation. The membership functions and the fuzzy rules were adjusted using the simulation until a particular torque ripple reduction was achieved.
To know the performance of the duty ratio controller, the simulation was run at switching frequency of 5KHz. The difference between the conventional DTC and DTC with duty ratio fuzzy control was clearly realized by monitoring the switching behavior of the stator voltage and the electric torque. The selected voltage vector is applied for the complete sampling period and the torque keeps increasing for the complete period, then a zero voltage is applied and the torque keeps decreasing for the complete sampling period and these results in high torque ripple.
The selected voltage vector is applied for part of the sampling period and removed for the rest of the period. As a result, the electric torque increases for part of the sampling period and then starts to decrease. By adjustment of the duty ratio, the desired average torque may be continuously maintained. The duty ratio controller smoothly adjusts the average stator voltage.
Cite this Page
The Simulink Model. (2019, Jul 29). Retrieved from https://phdessay.com/the-simulink-model/
Run a free check or have your essay done for you
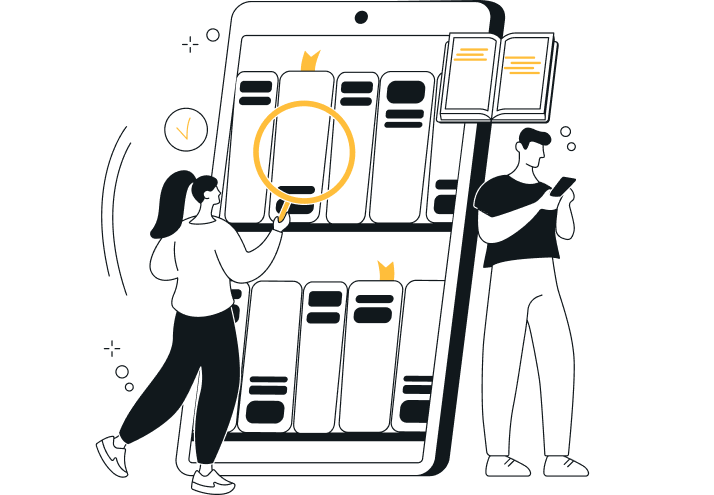