The Organizational Implications of Robotics
Forecasts of how many robots will be used In 1990 I- the u-led States range between 75,000 and 150,000 (Hunt & Hunt, 1983). Little Is known, however, about how Individual employees react to the Introduction of robots or about the changes needed In organizations to support robotics. Our research focuses on "deterrents”g the human side of robotics--how Individuals react to robots, how and when organizations should be modified to support robotics, and what effective strategies are for the Implementation of robotics.
The Robot Institute of America defines a robot as a programmable, multifunctional manipulator designed to move objects through variable programmed motions to perform a variety of tasks (Robot Institute of America, 1982). Two characteristics differentiate taboos from most other forms of automation: multiple task capability and programmability. The robots used most frequently in U. S. Factories today, in jobs that involve moving material, welding, drilling, or spray painting, are called level To' first-generation robots.
Researchers are now in the process of developing taboos, known as level II or second-generation robots, with more sophisticated sensing and thinking capabilities. For example, a level II robot that is capable of identifying the location of parts of different shapes and sizes is currently bee”g developed. Other examples of level II robots include those that mine underground coal seams, detect gas leaks, or perform sophisticated I”speciation tasks. Ares and Miller (1983) provide a good description of the current and expected future capabilities of robotics. 2 1:1 this paper. E first develop a GE:learn framework for' the effects of robots I:altitudes and We I:electorate from our field studies of the implementation:l of robotics as well as from other field studies f the Impact of robotics our general framework. The methodology and results of our field studies are described in greater detail In Argots, Goodman, a:old Cascade (1983) a:old Argots and Goodman (1984). We conclude the paper with suggestions for researchers who are analyzing the Implementation of robotics and with recommendations for managers who plan to utilize robotics In their organizations.
Order custom essay The Organizational Implications of Robotics with free plagiarism report
A General Framework The use of robotics may have a profound effect on the organization of work a. 'old on the productivity of tessellations. Robots typically require :lee skills of both reduction and technical support personnel and require closer l:alterations among functional areas (Argots. Goodman, & Cascade, 1983). Robots may displace some Technology Assessment, 1984). Robots may also enable organizations to be more flexible by decreasing set-up times associated WI the product changeovers. Moreover, robots may enable organizations to achieve greater consists:LLC I:l the quality of their products (Ares & Miller, 1983; Guest, 1984).
In this section, we develop a general framework for anticipating these effects of robots on individuals and organizations s well as for predict:leg the conditions under which the use of robots will enhance organizational performance. Organizational Performance L "l order to present our general framework, we first must discuss the concept of organ:location:ala performance. Organizations can be thought of as consisting of three basic components--people, etc”"logy. And structure. 3 It is the compatibility between” these three basic comps”e”TTS of organ”Tioga:l's that determined”sees their Performa”CE (Alleviate, 1965; Emery & Trust, 1973).
Organizational performance is a complex variable with multiple dimensions (Goodman & Pen”inns, 1977; Katz & Kahn, 1978). Examples of performance criteria that are critical in the manufacture:leg environment are productivity, product quality, manufacture:leg flexibility, absenteeism, turnover, and employee motivation and well-bee:leg. These criteria may vary in importance over time and to different constituencies. For example, sales and marketing departments may place a higher premium on manufacturing flexibility than other functional areas because it enables the organization to adapt to customers' needs in a timely fashion.
Similarly, manufacture:leg flexibility may be ore important in early than in late stages off product's life cycle (Kaplan, 1983). Further, these performance crib terra are likely to be interrelate Ted, sometimes complex ways. For example, employee motivation may be positively related to work unit productivity under conditions of uncertain:let that occur, for example, when a machine breaks down, while employee motivation may have little effect on the productivity of capital-I:latencies firms under route”e or programmed condo actions (CB. Goodman, 1979).
Similarly, productivity, at least measured I” the short tune, may be negatively associated with manufacture:leg flexibility. The complexity of the concept of organizational performance suggests that understanding the impact and effects of :lee technologies requires an appreciation of the interrelationships among the elements of organizations. It also suggests the ”deed for exam”I:leg multiple performance criteria a:old the trade-offs among them. Further research is :leaded to identify how the I”duration:l of robots will affect the elements of an organization a:old the conditions under which these elements may be 4 compatible. He few exists”g meme”kcal studies of the of robots (Argots, Goodman, & Cascade, 983; Argots & Goodman”, 1984; Office of Technology Assessment, 1984) and thee-ethical work on Job design, o”generational SST”structure, o”generational effective”sees, a”d the introduction of change enable us to suggest what these effects a”e likely to be and when the use of ”boots is likely to e”ha”CE manufacture”I”g pee”finance We want to emphasize that us'”g robots does not automatically imply certain consequence”sees for organizations but rather it is the interplay between characteristics of the technology, the manner in which it is I”traduced, the organization's structure, For example, some companies p”ovoid little training of” their robot operators and design the Jobs of operators such that they have little autonomy and are very dependent on technical support staff.
Other comma”sees provide more trait”ins for their operators, design more autonomy into their Jobs, and expect them to be actively involved in patriotism”g the operation of the robots. Our sense is that the latter approach to design”ins the operator's Job results in more motivated operators and a speedier and smoother implement”taxation than the boomer. The technology in each approach is the same. It is the supporting organizational arrangements that are different. Thus, the use of robots does not determine certain consequences for organizations. Instead it is the relationship between characteristics of the robots, the people who operate and maintain the robots, and the organizational arrangements that support the robots that affect the putrescence of o”sanitation”s. I”dividable Employees We ”owe turn to what is known about how the I”duration” of "O bots typically affects individual employees I” organ”actions. The I”duration” of robots usually changes the skills and Job activities of I”dividable employees. In our study off plant in the metal-working industry, the introduction of a robot that performed material handling activities caused a shift in the robot operators' Jobs from primarily manual to primarily mental activities (Argots, Goodman, & Cascade, 1983). The Office of Technology Assessment (TOT) reports a similar change with the introduction of welding robots in the automobile industry: the introduction of the robots removed some of the physical demands from the Jobs of human operators (TOT, 1984).
Thus, the introduction of robots in both studies had a positive effect on employees' work environments: the robots assumed some of the very physically demanding tasks otherwise performed by humans. At the same time, both studies found that the introduction of robots had certain negative effects on employees. Operators in our study reported that they experienced more stress and less control after the robot SASS introduced (Argots, Goodman, & Cascade, 1983). Similarly, the TOT report indicates that direct production employees felt less control with the introduction of the welding robots, because their Jobs were now tied to an assembly line (TOT, 1984).
Repair supervisors in the TOT report also experienced greater stress upon the implementation of robots, apparently due to the pressures of maintaining a complex and highly integrated production system (TOT , 1984). Based on previous research, we expect that if the I”transduction of robots leads to employees experiencing less control over their work environment, then they will be less satisfied, less motivated, and experience more stress upon the introduction of new technologies (Blabber, 6 1964; Hack” & Lawyer, 1971; Hickman & Lolled, 1975; Sutton & Kahn, in press). We also expect that systems that are very complex or characterized by low reliability will be associated with increased stress (Bright, 1958; TOT, 1984). The experience of variety and feedback on the Job promotes employee well-bet”g (Hickman & Lolled, 1975).
If the use of robotics affects the variety and feedback employees experience, then we expect corresponding changes in their satisfaction and motivation. Along these lines, the TOT report I”dictates that mat”tenancy introduction of welding robots: the maintenance workers' Jobs were characterized by greater variety and more challenge (TOT, 1984). The introduction of robotics typically changes the skill requirements of both production and technical support personnel. As noted earlier, the use of robots usually shifts operators' Jobs from manually-oriented to mentally-oriented activities. If these changes are compatible with employees' skills and preferences, employees will feel more satisfied and less stress with the change.
Strategies are suggested later in this chapter for maximizing the fit between employees and their Jobs and for designing the Jobs of employees, both direct and indirect, who must interact with robots. The manner in which robots are implemented may also affect employee reaction to the change. Coco and Fresh's (1948) classic study indicates that introducing change n a participative fashion increases the likelihood that employees will react positively to change. Other researchers have also stressed participation as a key variable in determining the extent to which employees react positively to change (Cotter & Schlesinger, 1979; Deteriorate al. , 1983).
While employees I” the two organizations we studied did ”to participate at all in any decisions surrounding the I”transduction of the robots, employees at both organizations desired more that” they actually had (Argots, Goodman, & Cascade, 1983; Argots & Goodman, 1984). The discrepancy between how much influence they actually had and how much they desired was especially pronounced at the second organization we studied, possibly because the organization was unionized and had a tradition of employee participation. While employees desired more influence, they acknowledged that the implementation of robotics is a complex activity requiring technical expertise that they generally do not possess. Hence, employees did not expect a great deal of influence in decisions regarding robotics.
They did feel, however, that they had some expertise, especially concerning work processes and machines in their department, and that they should be involved in socio” related to their areas of expertise. Another dimension of the implementation process is the method organizations use to communicate with employees about the introduction of robotics. Organizations may use a variety of communication mechanisms, including talks by the plant manager, meetings with first-line supervisors, and demonstrations. L” our research, we examined how effective employees rated the various communication sources their organizations used to introduce robotics. Our results indicate that demonstrations of the operation of robots are [dated by employees as most effective or increasing their understanding of robots (Argots, Goodman. & Cascade, 1983).
This result is corroborated by the finding that the demonstration had a greater impact on employees' beliefs about and attitudes towards robotics than any other communication source the organization used (Argots & Goodman, 1985). 8 How employee motivation, satisfaction and stress affect the performance of firms using robotics remains an open question. Teethe is a growing sense in the business literature that these human resource issues are critical too firm's ability to compete that using robotics and other programmable automation in ways that enhance employee well-being leads to increased organizational efficiency (TOT, 1984). Consequently, it is important that we identify the conditions under which employee motivation, satisfaction, and stress affect the overall performance of firms using robotics.
A” interesting hypothesis developed from previous research is that these human resource variables affect the overall performance of work units when nonprogrammer situations occur, for example, a machine breakdown or the introduction of a new product (CB. Goodman, 1979). Under routine operating conditions, human motivation and attitudes ”ay have little effect on the performance f robotics systems. That is, human resource variables may matter more when tech. ”eulogies are first being implemented, when new products alee being introduced, To' when unexpected problems arise than when systems are operating routinely. Organizational Structures In addition to affecting individual employees, the introduction of robots may also change the basic structures of organizations--communication within and between departments, decision-making responsibilities, role relationships and the like.
In our study, we found that the introduction of a robot led to increased interactions teen production and technical support personnel from engineering and maintenance. Studies of other technologies similar to robots, such as numerical control machines, report similar increases in interaction among production, engineering, and maintenance groups (Williams & Williams, 1964; TOT, 1984). 9 The use of robotics also has the potential to chaw:leg collation:lisps between production a:old markets:leg groups is:lace robots may reduce the time it takes to change from one product to another. This potential could e:label organizations both to accommodate a more varied product mix a:old to response:old more easily to customer demands.
Although we have :lot yet witnessed a:AY empirical evidence of modified relationships between production and marketing due to the introduction of robots, these changes might occur as more robots are put on line and linked in integrated systems. There is some evidence that the use of advanced automation on the factory floor may enable organizations to centralize production scheduling decisions (TOT, 1984). This may reduce the need for technical experts who schedule production as well as eliminate scheduling tasks from supervisors' Jobs. Similarly, intelligent robots that perform inspection tasks may reduce the requirement for facial quality control staff. Indeed the use of intelligent robots may lead to fewer hierarchical levels within organizations as well as too smaller number of direct production workers (Cherty, Dunked, Jordan, & Miller, 1984).
This is because intelligent systems alee capable of performing many activities, both manual and mental, traditionally performed by supervisors and certain support staff as well as by direct production workers. There are already examples of organizations where the use of programmable automation has led to the elimination of one layer of supervisors Chem.., Sisley, Liker, Earthman, & Thomas, 1984). At the same time, the use of intelligent robots may require more individuals with expertise maintaining and programming robots. R Thus far, we have focused on describing how the use of robotics is likely to change these structural changes may be associated with improved manufacturing performance.
As noted earlier, the use of 10 robotics typically I”creases the I”trepanned”CE of activities performed by member's of different functional groups. He”CE the use of robotics usually requires more interaction among these functional areas. We have observed companies where the increased interactions went extremely smoothly, a”d all groups were motivated to cooperate in the implementation of the ”ewe technology. We have also observed companies where the increased interaction was characterized by hostility, impede”g the implementation. What differentiates these two situations? In their analysis of interdepartmental conflict in organizations, Walton and Dutton (1969) discuss the conditions under which interdenominational relationships are characterized by conflict.
These conditions include: a reward structure that emphasizes the performance of separate roofs; asymmetric interdependence in which one group is more dependent on the other; communication obstacles such as different locations or specialized languages; and aggressive individuals. Applying these findings to the implementation of robotics provides insight in predicting when the increased interactions required by the use of robotics are likely to be smooth and when they are likely to be confliction. If a company's reward structure emphasizes the putrescence of separate groups, we expect the introduction of robotics to be characterized by conflict. This might occur, for example, if production groups are threaded according to short-term efficiency figures while engineering groups are rewarded for the number of ”ewe equipment pieces they introduce. Asymmetric interdependence is also likely to contribute to conflict.
This situation characterizes most introductions of new technology where, at least in certain stages of the implementation, production is more dependent on engineering for hardware and software then engineering is dependent on production. The effect of asymmetric needs on conflict is 11 moderated by the company's reward system. A reward system that emphasizes the performance of operate groups will only amplify the conflict potential of asymmetric interdependence. Instead, a reward system that has a more global and long-term orientation may foster cooperation and reduce the potential for conflict caused by asymmetric interdependence. When the functional groups that must interact to implement new technology are located in different areas or use different terminologies, conflict is likely to surround the process.
Conversely, if the different groups are located near each other, sit in on each other's meetings to understand each other's goals and constraints, and use a common language, then we expect the interactions required by the introduction of robotics to be more graceful. Finally, the nature of people who play key roles in the introduction, such as the lead engineer, affects the level of conflict. When key positions are occupied by . ”aggressive, authoritarian individuals concerned primarily with their own careers, the probability of conflict increases. The behavior of these individuals also will be affected, of course, by the company's reward sys tem. &”other structural issue raised by the implementation of robotics concerns the balance between centralization and decentralization in a organization. Current
Cite this Page
The Organizational Implications of Robotics. (2017, Nov 15). Retrieved from https://phdessay.com/the-organizational-implications-of-robotics/
Run a free check or have your essay done for you
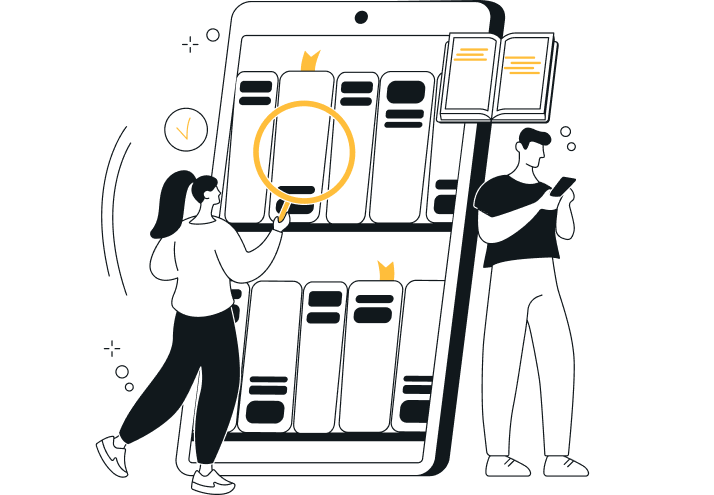