Purchasing and Supply Chain Management
The business suffers from poor organisation in the purchase of supplies. The purchasing of goods and services for the business use is known as Procurement. There are three managers who all participate in the purchase of items; each person purchases items they think necessary often leading to double orders or items not being bought at all.
There are several suppliers used some of which deliver while others operate a cash and carry policy, causing partners to use their own transport. Although several suppliers are utilised, the lack of regular custom by the company causes lack of interest by the suppliers and so the company misses out on priority service and possibly loyalty bonuses sometimes offered by these outlets designed to encourage repeat custom. Webster and wind (1972) Are concerned with sellers being aware of what buyers may be doing but also it should be important that buyers are aware of what seller are likely to do.
A significant amount of stock is wasted due to the haphazard means of stock control. The company likes to have a well filled freezer to protect against low stock levels or unavailability of items, which in turn ties up capital unnecessarily.
Order custom essay Purchasing and Supply Chain Management with free plagiarism report
Solution - Poor Organisation
A solution to this problem could be the hiring of a trained buyer who would control purchases made by the company. The advantage of this would be a single buyer would not order double quantities and excessive or unnecessary stock would not be purchased.
As a result stock control would be easier to manage. Organised purchasing would help to keep stock levels steady and unnecessary goods would not be stock piled, thereby releasing capital allowing money to be used efficiently and cost effectively. Hiring an expert may seem expensive but could save significant amounts of money and time. Possibly one of the managers could take part in a purchase training programme to gain the skills as they already have inside understanding of the company and how it is run. This would prove cost efficient and save money on outsourcing.
To solve the problem, the organisation could hire trained buyers to take over the three manager’s buying work. The advantages of hiring experts on buying stock for the organisation are that when there is only one person managing the buying, stock would be clearer and overlapping or lack of stock would be avoided. This could release the capital as stock would be more organised and money would be used more efficiently. However, hiring experts might be expensive and would be costly efficient for the organisation.
In this case one of the managers could go on purchasing training program to gain skills in terms of buying, meaning the company will have a buying expert, who also knows the business well, and the company will not be wasting capital on hiring an external expert.
Problem - Purchasing Policy Procedures
The company experiences problems with paper work not matching the goods purchased. This has resulted in some suppliers banning the buyers from their establishment and refusing credit facilities as payment may have been overlooked or invoices mislaid and no payment being processed.
The reputation of the company has been spoiled as non payment of invoices has caused it to be branded untrustworthy, subsequently it is not given priority as a respected business would be. Some suppliers expect cash on receipt of goods and this can cause a cash flow problem. Negative word of mouth may be passed around trade fairs or board meetings, which will have a negative impact on suppliers considering entering in to business with `Nessa’s Bar’. A solution to this problem could be a change in the purchasing procedure of the company. In a mechanistic structure, authority is centralised at the summit of the managerial hierarchy and vertical authority is use to control human and material resources. Mechanistic structures operate most effectively in stable environments. ” (Lysons, P158) A management structure needs to be established in which everyone understands their role within the company. Also a system for dealing with paperwork needs to be organised so that a good relationship can be developed between the company and its suppliers. 1. 3. 1Problem - Poor Management
The company wastes a great deal of time on low value goods. Security is very expensive but necessary. The bar employs its own cleaning staff and purchase cleaning materials as needed but these disappear from the stockroom as there is no inventory method in place to control the use of these items. All members of staff have access to the stockroom and as there is no organisation there is no stock checking system. This ultimately leads to confusion with the buying of items as the company is unaware of the exact inventory of goods available for use and what needs to be purchased. To solve the problem, the organisation could introduce VMI (Vendor Managed Inventory) “VMI is a collaborative strategy between a customer and supplier to optimize the availability of products at a minimal cost to the two companies. ” (Baily, P 181) Suppliers take responsibility for managing the stock which is constantly monitored and updated. (Baily, P181) Time could then be utilised on other jobs rather than being spent on low value goods.
This could be a problem as the supplier then controls the stock rather than the company, but any shortfalls would again become the responsibility of the company. “Acronyms for VMI include: CRP (continuous replenishment programs), SAIM (supplier-assisted inventory management), SAIR (supplier-assisted inventory replenishment), ECR (efficient consumer response). ” (Lysons, P357) The organisation could outsource cleaning and security to professional companies as they would be more skilled and knowledgeable than the staff in the organisation. Outsourcing as: The strategic use of outside resources to perform activities traditionally handled by internal staff and resources. ” (Baily, P115) It can be considered that outsourcing both cleaning and security could be expensive and there is no guarantee as to the standards of the work carried out, but the training of staff to carry out these services could cost even more. By outsourcing the less important work more time would become available to be spent on core business operations.
However there are disadvantages to outsourcing as Lacity and Hirscheim point out that; “…the employee culture is too fragmented or hostile for the organisation to come back together” (Lysons, P402). The employees from the outsourcing company might have a strong employee culture or different work ethics and find it difficult to fit into the working environment of Nessa’s Bar.
Problem - Costs/ Expenses
The majority of expense faced by the company are; rent, staff wages, beverages, food and other consumables. The bar spends approximately ? 00k per annum on beverages with a further ? 60k being spent on foods and other consumables.A possible solution to these problems would be the reduction of staff employed at the business. Should cleaning and security be outsourced then the staff currently employed to carry out these tasks are no longer required and could be laid off. Well managed stock would save the company money as would developing a better relationship with suppliers who might offer discounts on goods and better delivery services. …requiring production when, and not before, a customer requires something, and the pursuit and elimination of waste in production and associated planning and purchasing... ”(Baily, P177) JIT can keep the stock level to be low in the organisation, which can prevent unnecessary capital to be stuck as stock. The utilisation of a VMI system for stock control could prove to be more cost effective for the company as the supplier takes responsibility for stock management. Suppliers have more experience of this kind of system and would ensure the smooth running of the stockroom.
The company would receive higher levels of service as less time would be spent on low value goods and as there would be less stock wastage the company would achieve improved revenue. (Baily, P182)
Conclusion
Currently there are problems with Nessa’s bar as it operates on an inefficient and disorganised system. Basic errors including order duplication, failing to pay suppliers, wasting time on low value goods, and a lack of purchasing knowledge has resulted in a loss of money, time and stock.
Also the non payment of invoices has given the company a bad reputation with suppliers. The company could hire a professional buyer who specialises in purchasing goods thereby eradicating the possibility of mistakes being made when goods are ordered. Time would be saved by orders not being duplicated, items overstocked, or wasted on low value goods. If this is not a viable economic option then one of the three managers could be trained to assume the role and take on the responsibility for these tasks.
One person would then make decisions, an advantage would be that they already have a working knowledge of the company and they are also known to the other managers from the outset. A centralised approach with just one national supplier would make purchasing easier and more cost effective for the company as they will reduce the amount of paperwork by receiving one invoice rather than several. This will assist ease of stock control and management.
Reference
- Baily P. Purchasing Principles and Management, Financial Times/Pitman Publishing (Tenth edition) Lysons K. 2000) Purchasing and Supply Chain Management (5th Edition), Financial Times/Pitman Publishing Webster F and Wind Y (1972) Organisational buying behaviour, Prentice Hall, New York.
- American Marketing Association. (1995). Market research. Available: http://dis. shef. ac. uk/sheila/marketing/research. htm. Last accessed 28. Febuary 2010. R. Srinivasan. (1988). Brand Accounting-An Emerging Concept. Available: www. londonmba. org/... /Brand%20Accounting-An%20Emerging%20Concept_by%20R. %20
- Srinivasan. doc. Last accessed 1 March 2010. 5. 0 Bibliography Kotler, P. & Armstrong, G. (2000) Principles of Marketing (9th edition) Prentice Hall.
Cite this Page
Purchasing and Supply Chain Management. (2018, Feb 05). Retrieved from https://phdessay.com/purchasing-and-supply-chain-management/
Run a free check or have your essay done for you
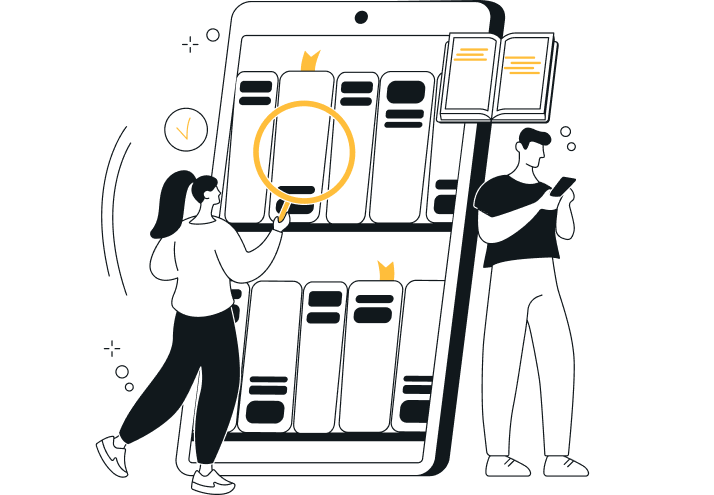