Programmable logic controller Argumentative Essay
Introduction
The Programmable Logic Controller ( PLC ) is an industrial computing machine control system that continuously monitors the province of input devices and makes determinations based upon a usage plan to command the province of end product devices. This is one of the most normally used industrial mechanization techniques in the universe. This is really utile for mill mechanization, procedure control, and fabricating systems. The chief technique used in this scheduling is called ladder logic which allows sequences of logical actions to be set up, inter-linked, and timed.
It can besides be defined as a personal computer that is embedded in or attached to execute operations like exchanging timing, and machine or procedure control undertakings.
Order custom essay Programmable logic controller Argumentative Essay with free plagiarism report
In the past worlds were used to command systems. Then electricity came into usage with the aid of electrical relays. These relays allow power to be switched on and off without a mechanical switch. But the development of the low-cost computing machine has brought the most recent revolution, the programmable logic accountant ( PLC ). The coming of the PLC's began in the 1970s and is the most common pick for fabrication controls.
About any production line, machine map, or procedure can be greatly enhanced utilizing this type of control system. There are many advantages to utilizing PLC's. However, one of the biggest benefits of utilizing a PLC is the ability to alter and retroflex the operation or procedure while roll using and pass on critical information.
Another advantage of a PLC system is that it is modular. That is, you can blend and fit the types of Input and Output devices to outdo suit your application.
History of PLCs
The first Programmable Logic Controllers were designed and developed by Modicon as a relay re-placer for GM and Landis.
- These PLC 'S ( accountants ) eliminated the demand for rewiring and adding extra hardware for each new constellation of logic.
- The new system introduced by the PLC drastically increased the functionality of the controls while cut downing the cabinet infinite that housed the logic.
- The first PLC, theoretical account 084, was invented by Dick Morley in 1969
- The first commercial successful PLC, 184, was introduced in 1973 and was designed by Michael Greenberg.
Advantages of PLC'S
Flexibility: many machines can be run utilizing one individual programmable logic accountant.
Space-efficient: there is a batch of infinite to bring forth more and more contacts, spirals, timers, sequenators, counters, and so on. There can be many figures of timers in an individual PLC.
Correcting mistakes: the rectification of mistakes in a PLC is highly short and cost effectual. In the yesteryear, there were wired relay types and any alterations required clip for rewiring panels. But in a PLC any alteration in circuit design is every bit simple as retyping the logic.
Low cost: these monetary values are cost-efficient and low-cost varying from a few 100s to a few 1000s.
What Is Inside a PLC?
The Central Processing Unit, the CPU, contains an internal plan that tells the PLC how to execute the undermentioned maps:
- Execute the Control Instructions contained in the User's Programs. This plan is stored in "nonvolatilizable'' memory, intending that the plan will non be lost if power is removed
- Communicate with other devices, which can include I/O Devices, Programing Devices, Networks, and even other PLCs.
- Perform Housekeeping activities such as Communications, Internal Diagnostics, etc.
Programmable Logic Controllers or PLC is the hub of many fabrication procedures. These microprocessor-based units are used in procedures every bit simple as packaging machines or bagging equipment to commanding and tracking sophisticated fabrication procedures. They are in virtually all new fabrication, processing, and packing equipment in one signifier or another.
The microprocessor or processor faculty is the encephalon of a PLC system. It consists of the microprocessor, memory integrated circuits, and circuits necessary to hive away and recover information from memory. It besides includes communications ports to other peripherals, other PLC's or scheduling terminus. Today's processors vary widely in their capableness to command existent universe devices. Some control every bit few as 6 inputs and end products ( I/O ) and others 40,000 or more. One processor can command more than one procedure or fabrication line. Processors are frequently linked together in order to provided continuity throughout the procedure. The figure of inputs and end products PLCs can command is limited by the overall capacity of the PLC system
Code Coevals in PLC
Importing I/O list: this tool allows us to work on the I/O list and allows us to make all alterations and so export it to our PLC in few seconds.
Coevals of ladder logic automatically: this package allows us to bring forth 100s of motors and valves in few seconds in a manual manner. It besides creates the chief construction of the plan.
Equipment logic coevals: this package allows us to bring forth motors and valves libraries which can so be imported to our PLC.
Operation of PLC
There are four basic stairs in the operation of all PLCs; Input Scan, Program Scan, Output Scan, and Housekeeping. These stairss continually take topographic point in a repetition cringle.
1. Input Scan | * Detects the province of all input devices that are connected to the PLC |
2. Program Scan | * Executes the user-created plan logic |
3. Output Scan | * Energizes or de-energize all end product devices that are connected to the PLC. |
4. Housekeeping | * This measure includes communications with scheduling terminus, internal nosologies, etc... |
System Description
Actuator
A mechanism that causes a device to be turned on or off, adjusted or moved. The motor mechanism that moves the conveyer belt is called an actuator. In this Allen Bradley theoretical account, we have five actuators. The first actuator is the upper conveyer belt motor, 2nd actuator is the lower conveyer belt motor, actuator three is used to hit the ring into the pealing chute, actuator four releases rings into assembly country, actuator five rejects the unassembled constituent.
Detector
It can be defined as a device such as a photoelectric cell that receives and responds to a signal or stimulation or a device that measures or detects a real-world status, such as gesture, heat, or visible radiation, and converts the status into a parallel or digital representation. An optical detector detects the strength or brightness of visible radiation, or the strength of ruddy, green and blue for color systems there are eight types of detectors in this procedure. Sensor one detects the nog near to and in the forepart of the solenoid. Sensor two besides detects about the constituent in the forepart of the solenoid. Sensor three detects the constituent at the real underside of the pealing chute beyond the rotary solenoid. Sensor four is a black push button used on the system. Sensor five has a ruddy push button used to close down. Sensor six used to observe the presence of go through complete assemblies. Detectors seven is used as a brooding IR detector. Sensor eight is used to observe the presence and reject the uncomplete assemblies. Sensor nine is usage to feel the complete assembly.
Micrologix
A Programmable Logic Controller, PLC, or Programmable Controller is a digital computing machine used for mechanization of industrial procedures, such as control of machinery on mill assembly lines. Unlike all-purpose computing machines, the PLC is designed for multiple inputs and end product agreements, extended temperature scopes, unsusceptibility to electrical noise, and opposition to quiver and impact. Programs to command machine operation are typically stored in battery-backed or non-volatile memory. A PLC is an illustration of an existent clip system since end product consequences must be produced in response to input conditions within a delimited clip, otherwise unintended operation will ensue
Micrologix 1000 Accountant
Micrologix 1000 brings high velocity, powerful instructions, and flexible communications to applications that demand compact, cost-efficient solutions. The Micrologix 1000 programmable accountant is available in 32-point digital I/O versions. Analog versions are besides available with 20 digital I/O points, with 4 parallel inputs ( two electromotive forces and two current ) and 1 parallel end product ( configurable for either electromotive force or current ).
Sensor figure | Sensor type, location, and map. | PLC Input |
1 | Download-looking brooding IR detector at the upper kind country. Detects the presence of a nog near to and in the forepart of the solenoid at the top of the pealing chute. | I: 0/4 |
2 | Sideways-looking brooding IR detector at the upper kind country. Detects a constituent in the forepart of the solenoid at the top of the pealing chute. | I: 0/1 |
3 | Brooding IR detector at the assembly country. Detects the presence of constituent at the real underside of the pealing chute beyond the rotary solenoid. | I: 0/0 |
4 | Black pushbutton. Used to get down piecing say. | I: 0/18 |
5 | Red pushbutton. Used to end collection, say. | I: 0/19 |
6 | The capacitive detector, near the lower kind country. Detects the presence of go through complete assemblies near the cull solenoid at the motor terminal of the lower conveyor. | I: 0/6 |
7 | Brooding IR detector at capacitive detector near the lower kind country | I: 0/3 |
8 | Brooding IR detector in the lower kind country. Detects the presence of constituents and assemblies in the forepart of the cull solenoid at the motor terminal of the lower conveyor. | I: 0/2 |
9 | Through-beam IR detector, merely after the assembly country. Detects constituents on the lower conveyer go forth the assembly country. | I: 0/5 |
Actuator No. | Actuator type, location, and desired map | PLC Output |
1 | Upper conveyor motor. Drives the upper toothed concatenation conveyer | Oxygen: 0/3 |
2 | Lower conveyor motor. Drives the lower field belt conveyer. | Oxygen: 0/4 |
3 | The solenoid in the upper kind country. Knocks ring into the pealing chute. | O:0/0 |
4 | Rotary solenoid at the underside of the pealing chute before the assembly country. Releases ring into the assembly country. | Oxygen: 0/1 |
5 | Solenoid at the reject country. Cull's unassembled constituents before the complete assembly aggregation tray. | Oxygen: 0/2 |
The theoretical account of plc used in this procedure is ALLEN-BRADLEY MICROLOGIX 1000 PLC and the scheduling package is RSLOGIX 500.
Relay: A switch operated by an electromagnet is a relay.
Counter: Digital counters in the signifier of relay contact when a preassigned count value is reached.
Timer: A timer consists of an internal clock, a count value registry, and a collector is used for clocking intent.
Ladder diagram: A ladder diagram is an agency of graphical stand forcing the logic required in relay logic system.
Requirements of the PLC Diagram:
- Ladder diagram
- Structure text scheduling
- Functional block scheduling
- Instruction list
- Consecutive functional chart.
PLC Ladder Diagram Instructions:
- Relay,
- Timer and counter,
- Program control,
- Arithmetic,
- Data use,
- Data transportation, and
- Others, such as sequenators.
Functional Block Scheduling
A functional block is a well-packaged component of a package that can be reused in different parts of an application or even in different undertakings. Functional blocks are the basic edifice blocks of a control system and can hold algorithms written in any of the IEC linguistic communications.
Instruction Manuals List
A low degree linguistic communication holding a construction similar to an assembly linguistic communication. It is simple and easy to understand and ideally for little manus held programming devices. Each line of the codification is divided into four they are label, operator, operand, and remark.
Consecutive Map Chart
A graphics linguistic communication used for picturing consecutive behavior. An SFC is indicated as a rectangular box connected by perpendicular lines. Each measure represents the province of the system being controlled. A horizontal saloon indicates status. Each measure has a figure of action. Action qualifier causes the action to act in certain ways and the index variable is optional.
Requirements & Constraints
Requirements:
- Conveyor belts should be kept traveling during the operation.
- The actuator 3 should strike hard merely the ring when detector 1 senses it.
- The ring should non come in the nog chute or frailty versa.
- Excess rings should be collected in the excess rings box.
- The nog chute and the pealing chute should be clean for the ring and nog to skid in that.
- Unassembled constituents should be knocked down by the actuator 5.
- Constraints
- The actuator shouldn't strike hard the ring when there are more than 5 rings in the chute if there are more rings 5 rings so the motion will be blocked.
- The country between the actuator 4 and the detector 3 should be clear for the following nog to busy the infinite.
- The actuator 3 can non strike hard if there are more than 5 rings in the ring chute.
Merely if the nog moves past the pealing the assembly will be over.
Constraints:
- The actuator shouldn't strike hard the ring when there are more than 5 rings in the chute if there are more rings 5 rings so the motion will be blocked.
- The country between the actuator 4 and the detector 3 should be clear for the following nog to busy the infinite.
- The actuator 3 can non strike hard if there are more than 5 rings in the ring chute.
- Merely if the nog moves past the pealing the assembly will be over.
Explanation of Plan
In this plan, there are 23 stairs called rungs. These rounds help us to accomplish the aim of our assignment.
0000
B3:1/1 is the starting flag which is a black push button in on province and I:0/19 which is a ruddy push button in off province. If this is the status the flag B3:1/1 is latched and runs the following direction otherwise flag is unbarred.
0001
If B3:1/1 is latched so it enters the following flag B3:1/2 and so actuator 3 and actuator 4 holding references O:0/3 AND O:0/4 are enabled severally such that the upper and lower conveyor motors will be running.
0002
Here we check that I:0/19 is pressed or non. If it is pressed so B3:1/2 flag is latched if it is unbarred so it will be the flag B3:1/2.
0003
Here the starting flag is B3:2/1 where detectors 2 ( I:0/1 ) and sensor 1 ( I:0/4 ) are used. Sensor 2 detects a constituent in the forepart of the solenoid at the top of the pealing chute and detector 1 detects the nog. Here sensor 1 is away and sensor 2 is on.
0004
Since detector 2 is on, actuator 3 ( O:0/0 ) detects the rings coming from the conveyor belt and force them into the pealing chute. Here we start a timer on hold ( T4:0 ) to 0.01 sec and preset to 50 which enables O:0/0.
0005
If B3:2/2 is on and timer 0 ( T4:0 ) decrementing is on so we unlatch B3:2/2 and latch B3:2/3.
0006
If B3:2/3 is on so we have to get down timer 2 ( T4:1 ) to 0.01 sec and preset to 20.
0007
When B3:2/2 is on so timer 2 is decremented and B3:2/4 is latched and B3:2/3 is unbarred.
0008
When B3:2/4 is on so a counter ( C5:0 ) is on and preset to 5.
0009
When B3:2/4 is on, so counter ( C5:0 ) is started and so we unlatch B3:2/4 and B3:2/1 is latched.
0010
Here B3:3/1 is get downing flag and we use sensor 3 ( I:0/0 ) which detects the constituent at the underside of the pealing chute. Here we besides check the figure of rings in the collector and if B3:3/3 is on, we have to latch B3:3/2 and B3:3/1 is unbarred.
0011
If B3:3/2 is on, so we have to put timer 3 ( T4:2 ) to 0.01 sec and preset to 50 and we have to enable O:0/1 which is actuator 4 used to let go of the rings into the assembly country.
0012
When B3:3/2 is on so the timer 3 ( T4:2 ) is decremented and we have o latch B3:3/3 and B3:3/2 is unbarred.
0013
When B3:3/3 is on, so counter ( C5:0 ) is decremented.
0014
If B3:3/3 is on and input 0 ( I:0/0 ) is non-true so latch B3:3/4 AND UNLATCH B3:3/3.
0015
When B3:3/4 is on we have to enable the detector 5 ( I:0/19 ) and we have to latch B3:3/1 and B3:3/4 is unbarred.
0016
When B3:4/1 is on so we have to enable detector 9 ( I:0/5 ) which detects constituents on lower conveyor belt go forth assembly country and we have to latch B3:4/2 and B3:4/1 is unbarred.
0017
When B3:4/2 is on we have to enable detector 8 ( I:0/2 ) which detects the presence of constituents and assembles in forepart of the cull solenoid at the motor terminal and we have to latch B3:4/3 and B3:4/2 is unbarred.
0018
If B3:4/3 is on so detector 8 ( I:0/2 ) is disabled and we have to latch B3:4/1 and unlatch B3:4/3.
0019
When B3:4/1 is on, the detector 8 ( I:0/2 ) is enabled and we have to latch B3:4/4 and unlatch B3:4/1.
0020
When B3:4/4 is on so we have to enable actuator 5 ( O:0/0 ) which is a solenoid at the reject country. It rejects unassembled constituents before the complete assembly aggregation tray.
0021
If B3:4/4 is on so we have to sensor 8 ( I:0/2 ) is ff and we have to latch B3:4/1 and B3:4/4 is unbarred.
Cite this Page
Programmable logic controller Argumentative Essay. (2018, Jul 24). Retrieved from https://phdessay.com/programmable-logic-controller-2/
Run a free check or have your essay done for you
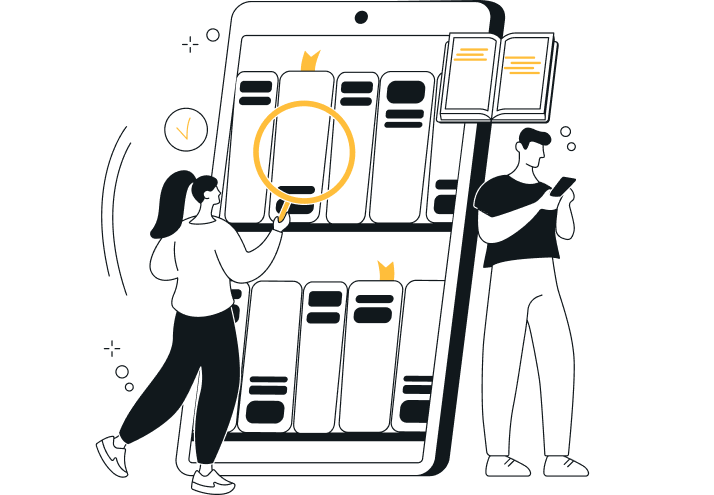