Pipeline Inspection at Petronet, South Africa
Introduction
Petronet, a local company that transports natural gas through underground pipelines across South Africa, had approached MA2K Testing Labs to conduct an investigation on a leakage on the pipeline, which was found during a random leak inspection. The Pipeline operates from Johannesburg to Potchefstroom. Upon inspection a joint was singled out as being a major source of leakage. The affected area was joined using a butt weld and reinforced with a clamp. This section was dissected and inspection revealed that the leakage was due to incomplete fusion in the weld which initiated the formation of hook cracks and cavities in the parent material directly adjacent to the weld. External stresses from the environment may have accelerated the growth of the cavities and cracks yet the clamp increased the strength of the joint aiding in the prevention of any accelerated growths of the defects.
As a short term solution it is advised to replace the damaged section with a new pipe. It must be correctly welded of the same material and as an added precaution to weld an additional sleeve over the newly joined and welded section.
Order custom essay Pipeline Inspection at Petronet, South Africa with free plagiarism report
As a long term solution it is advised to replace the entire pipeline with a new combination of materials.
Background
Petronet, a leading company in South Africa which transports natural gas through underground pipelines conducted a random leak inspection survey on one of their pipelines operating from Johannesburg to Potchefstroom, and it was discovered that there was a gas leak at the specific joint. The pipe carries natural gas and it is imperative that the leak should be fixed, due to the volatile nature of gas as well as the loss of resource, in turn profits. The systems comprised of numerous seamless pipes and connected using a butt weld; these joints were reinforced by clamps bolted on.
MA2K Testing Labs had been approached by Petronet, to inspect the leakage and was employed to identify the true cause of failure and as well as make many suitable recommendations for the repair and prevention of malfunction of the joint. The pipeline was effective since the 20th February 1995; this put the pipeline age in the region of 15 years.
Description
The defective section of the pipe, including the clamp was then marked, cut out and removed from the site for further inspection and analysis. The inspection and analysis was carried out in MA2K Testing Labs in Durban.
Two grade A 106 GR.B SCH40 seamless pipes with outside diameters of 168.3mm and wall thickness of 9mm were butt welded end to end. A butt weld consists of the two pipes heated to a proper fusion temperature then joined by means of force. The joint was further secured by a clamp. The operating internal gas pressure was 2620 kPa (380 psi).
Possibilities Of Failure
Weld Defects
- Penetration is poor at the start of welding
- Ensure the grades of pipes are constant to optimize bonding strength
- Poor quality welds caused by Inaccurate timing
- Incorrect temperature
- Incorrect pressure applied
- Failure due to fatigue (welding lowers fatigue strength)
- Fusion did not occur between weld metal and fusion faces.
- Incomplete penetration
- Weld metal does not extend through the joint thickness
- Exposed to water and contaminants in the gas, such as O2, H2S, CO2, or chlorides.
- A particular gas composition may cause corrosion under some operating conditions
- Oxygen content (oxidizing salts)
- Passing through soils of different mineral content
- Contact of different metals, particularly at valves (galvanic corrosion)
- Normally consists of gouges and dents.
- Generally created by excavation or handling equipment during construction.
- Results from cyclic stresses that are below the ultimate tensile stress, or even the yield stress of the material.
Incomplete Fusion
The pipe surface was required to be cleaned. An acetone solution was used. Liquid Penetrant examination was performed on the weld area of the pipe. Surface discontinuities were visible on the bottom of the pipe. All examinations and analysis was carried out by MA2K Testing Labs. Through inspection it was deduced that a Butt weld was used to join the pipe line and macrostructure images revealed that there were defects on the welded area. Namely weld cracks, improper penetration and incomplete fusion. Cavities were discovered near/adjacent to the welded section of the pipe material.
Surface discontinuities were made visible by the Liquid Penetrant examination. These results further justify the suspicion that there was an improper weld process conducted on the joins of the pipeline and thus the cause of the gas leak. Cavities are visible in the pipe walls. This may be caused by vacancies in the material join in the weld.
The extracted sample was investigated by method of etching. A Nital solution was used to etch the pipe material. Nital is a solution of alcohol and nitric acid commonly used for routine etching of metals. It is especially suitable for revealing the microstructure of carbon steels. The alcohol can be methanol, ethanol or methylated spirits. By viewing the etched sample under a Scanning Electron Microscope it was revealed that there was an overlap of material and as a result, it was discovered that there is an irregularity or there is a non-uniform overlap or join of material. This could cause a weakness in the join due to variants in material or state of the material. The non-uniform joint of material gives weak point on the structure of the pipeline and thus resulted in a leak.
Results
Before the pipe was sectioned for detailed examination, a radiographic examination was performed on the premises of MA2K Testing Labs. The following image was revealed on the radiographic film. The radiograph picture shows the microstructure of the material and identifies the weld overlap with the parent material. There are clear indications of variant material or states which cause weakness in the join when added stress is applied. There are cut out root cavities visible in the radiograph which could be the cause of leakage in the pipeline.
In figure 6.3 below: The longitudinal cross section of the pipe showed the weld structure inside the pipeline. This revealed defects in the weld structure and cavities in the wall of the pipeline and a clear indication of the crack and fracture lines that could cause a leak in the pipeline. These defects occurred in the joining of the pipe and together with possible external stresses that act on it due to the environment, no corrosion had occurred and pipe was designed to withstand pressure of the gas within the pipe.
Longitudinal samples were taken from the extracted piece. Cuts were made across the weld line, to define the differences in the material used in the weld and the parent material.
The two cross sections through the wall thickness of the pipe was polished and etched with Nital. The one macroscopic image (Figure 6.4) revealed a clear leakage path through the wall thickness of the pipe. This shows that there was a weakness in the join between the weld material and the parent material. Further fracture and strain caused the weld to split at the join between the weld material and the parent material. Figure 6.5 shows that there was a lack of side wall fusion in the pipe and that there was another weld bead on the left, this had been made to try to fill the vacancies produced from the lack of fusion.
Conclusions
After thorough investigation of the defective area of the pipe it was found that the leakage was due to improper weld process and lack of fusion, lack of fusion causes cavities. Cavities form cracks over a period of time. Due to this hook cracks were formed and leakage had occurred. Therefore, the components used contain no post installation defects as there was no internal or external corrosion to the material. The design of the material is suited to the environment as it was able to withstand cyclic loading, fatigue stresses and no signs of hydrogen blistering was present on the material. Mechanical damage may have aided or accelerated the growth of the crack size. The clamp made detecting the source of the leak more difficult and may have helped in the prevention or retarded the rate in which the cracks had grown. The condition of the pipe or clamp base steel compositions or microstructures was as expected for the working life of the system. No softening was found associated with the weld and pipe Heat Affected Zone.
Cite this Page
Pipeline Inspection at Petronet, South Africa. (2019, Mar 08). Retrieved from https://phdessay.com/pipeline-inspection-at-petronet-south-africa/
Run a free check or have your essay done for you
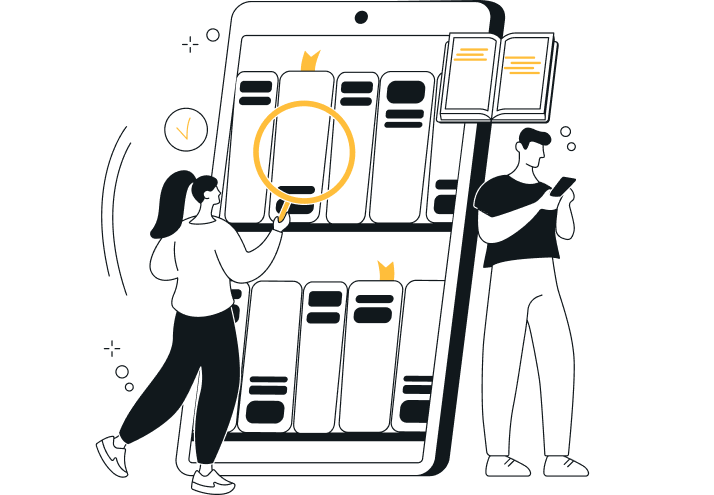