Old Joe Case Report
In the spring of 2012, our management group, group 7, was assigned to take over a business as top level management. With the only guideline of creating a drastically more capable and profitable organization within a year, we had a lot of work ahead. The business belonged to Old Joe, an absolute genius engineer who was lacking in business management skills, Fred, a failed engineer with underlying personal issues resulting in counterproductive activity, and Netty, Old Joe’s wife. This division of the business specializes in the creation of medical products, and has customers globally.
The backwards situation the business was in cannot be overstated. There was a huge set of order back logs, quality problems, inventory issues, social and culture problems within the company, and several others. With the business in such a dire state, we began our work. Organization Chart Opening Day Q1 * Establish Positions as boss by doing 2 things: * Introduce ourselves to all the current managers * Sending out a warning shot by giving the managers a one hour time frame to try and settle their differences. * This will make it clear to the managers that henceforth there will be no tolerance for social bickering. Begin working on the delinquent backorders worth roughly $16million. By the end of quarter one, at least 70% of the orders will be complete. A lot of overtime is going to be required for this to happen. This will address problem #3. * Fire Yolanda. She is simply terrible. This will address problem #10. * Demand that Bob apply himself better for job related issues. However, knowing that he is going to strive to work against the company goals, the extraction of information from Bob will be the goal. Once this is done, Bob will also be fired, which is roughly after 40 days.
Promote a well qualified worker to bobs position * Hire a new Human Resources Manager (HRM) to replace Yolanda. The new HRM, Jenny, will be given 2-3 weeks to settle in, and get to know what the state of the company is, and what is required on his part. * We need to start on the paycheck errors right away. Unfortunately, we don’t believe we have the time to fix the problem all together, but we can reduce the amount of errors. We need to reduce the 3 way to “punch in” into one single method. We feel that written time cards would be the best way for now. It is quick and can be managed quite easily.
Order custom essay Old Joe Case Report with free plagiarism report
We need to have the person fill out their time card which must be legible. If the time card is not legible, then the employee doesn’t get paid for that week until they can prove they worked those hours. The time card must be then signed and reviewed by a supervisor to make sure there are no errors on it. We can then hold the employee and the supervisor accountable for any errors that occur. This can even go through the new HR if problems still occur. This will address problem #15. * We need to have Ed work closely with the new HR that we hired to keep the paycheck errors under control.
We are in a position where we need to first minimize the problem, until we have the time and resource to completely fix it. This will address problem #15. * Fred gets put on tight leash right away and given no leeway. His job will be laid out for him step by step and to ensure he is doing his job, we would keep up to date on his problems. Fred will have to answer forecasts directly to us and he will not be allowed on the production floor. That way he won’t be down yelling at people and he’ll be more focused on his job. Fred is high in the company and should know how to do his job even though he is not trained for his position.
We will keep tabs on Fred ourselves and give him no leeway. I expect him to be a big part of this company getting back on track and his forecasting will help immensely. This will let him know he’s on thin ice and make him work harder. He should know how to make a sales forecast so we will push him for better work for now but he will be terminated if he does not shape up. This will address problem #24. * With Bob gone, issues will eventually be solved. Have Ed put aside issues with Harry for working purposes. With bob fired the problems between Ed and Harry will lessen.
We need to call them into office together and talk to them face to face. Tell them each that work is work and differences need to be settled. Let them talk out whatever problems they have right then and there because when they leave our office it will be settled. With them working together more efficiently, quality checks will occur and the right products will be made and be made right. - This will address problem #1. * Ed will also start to documenting processes on how to make products in a detailed step by step fashion as they are needed by company.
We want to limit the steps of a process to as simple as 20 steps or under. * All manuals will be step by step detailed processes but easy to follow. Everything will be laid out for laborers. This will address problem #11. * For the labor grievances, we think that after firing Bob and Yolanda, we should select the 10 most pressing grievances from the stack of 450, and tell the Union we will be willing to discuss only those grievances in full. This will address problem #16. * If they do not to budge, continue to press the issue calmly and ask them whether it is not reasonable to do this.
Arbitration for those 10 will remain on the table if no median can be reached. This will address problem #16. * Priorities related to the accounts payable and accounts receivable issue: * As we have stated in the outline and using some of the ideas discussed in class we must empower Donna to contact customers and tell them we need to get their invoices and payments into us sooner, preferably in a period of about 30-35 days. This process will occur over all periods until we decrease it until our target time. This will address problem #13. Slow down the account payables rate by several days with better accuracy of the materials and services traced to the specific accounts. This is a continuous process and will be performed throughout all quarters. We will achieve this by having Donna call our suppliers and telling them we will now pay according to normal business schedules. This will address problem #14. * Work on fencing off inventory room, with only one entrance and have personnel in supply room to check everything going in and out. Fix supply room and make it so it is flowing.
No dead ends, color coordinate, One entrance, useful products stay lower on shelves and more convenient to get. Products that are not used at much can stay higher up or farther back in stock room. - This will address problem #9. * Harry will be asked to implement some quality measures, Total Quality Management, Quality at the Source, implementing some better use of preventative costs among other things could be used after he helps to implement and empower the proper workers in the quality department. Value-added measurements should also be implemented in the quality metrics so that waste can be eliminated.
Also it is imperative to document all processes throughout the plant. This is a continuous effort, and will not end as long as the company is in business. This will address problem #1. * As for future hires, Harry would be best to implement organized training procedures while the new head of HR grows accustomed to company procedures and requirements.. He will work with the new HR manager to give orientations of what the company is about and what is expected by us, the customers, and the company. Harry will also create metrics for determining what qualities are expected from future employees.
This will address problem #1. Metrics Ending Q1 Time by Quarter (x) No. of Grievances (y) Time by Quarter (x) Percentage of Employees Exposed to Orientation (y) Time by Quarter (x) Order Backlog Remaining in Dollar Value in millions (y) Time by Quarter (x) Inventory Accuracy Percentage (y) Time by Quarter (x) Payroll Errors / week (y) Time by Quarter (x) AP / AR Days (y) Time by Quarter (x) Percentage of Process Documentation (y) Time by Quarter (x) R&D projects incomplete / ongoing from Q1 (y) Organization Chart End Q1 Q2 * By Q2, we as the new bosses need to be the bottleneck for the company.
Everything that goes through Howard needs to be prioritized by us until the company gets back up to par with all the back orders and other issues that it’s dealing with. * Howard needs to start documenting all the current information and putting it into a computer system that can be accessed by different department supervisors across the company. This will eliminate any mistakes that could possibly occur with the handwritten process that is currently in place. * Request that Harry and Ivan work together to develop metrics in qualifying suppliers- This will address problem #23. As we have stated in the outline and using some of the ideas discussed in class, we must empower Donna to contact customers and tell them we need to get their invoices and payments into us sooner, preferably in a period of about 30-35 days. This process will occur over all periods. * Slow down the account payables rate by several days with better accuracy of the materials and services traced to the specific accounts. This is a continuous process and will be performed throughout all quarters. Have Donna call suppliers to slow notify them we are slowing the process in advance. This will address problem #14. Harry should then focus on the supplier metrics with Ivan and develop a scorecard. The scorecard should include total costs of ownership measures-from order to disposal-, delivery time from suppliers, and a more subjective measure of sorts on how integrated the supplier is in the process. Have these systems up and running by the end of quarter 2. This will address problem #1. * Harry will implement some quality measures, Total Quality Management, Quality at the Source, implementing some better use of preventative costs among other things could be used after he helps to implement and empower the proper workers in the quality department.
Value-added measurements should also be implemented in the quality metrics so that waste can be eliminated. Also it is imperative to document all processes throughout the plant. Instantly and continuous. This will address problem #1. Metrics Ending Q2 Time by Quarter (x) Inventory Accuracy Percentage (y) Time by Quarter (x) Payroll Errors / week (y) Time by Quarter (x) Order Backlog Remaining in Dollar Value in millions (y) Time by Quarter (x) AP / AR Days (y) Time by Quarter (x) R&D projects incomplete / ongoing from Q1 (y) Time by Quarter (x) Percentage of Process Documentation (y)
Organization Chart Ending Q2 Q3 * In Q3, train Howard to what the company needs most that way he can have an understanding of what the company needs first which will allow for us to be taken out of the picture, thus eliminating the bottleneck for this department of the company. * Howard needs to set up a communication system such as email for many of the supervisors or managers of the company which will greatly increase communication within the departments. This could have a significant effect on sale and engineering which would lead to new products being developed or at least thought about. Once the errors have been minimized, we can then work with Howard to install a way for the employee to punch in using a computer that can only be accessed by management. With this process in place, there will be no errors with the paychecks, freeing up time for everyone for not having to deal with these problems anymore. * As we have stated in the outline and using some of the ideas discussed in class, we must empower Donna to contact customers and tell them we need to get their invoices and payments into us sooner, preferably in a period of about 30-35 days.
This process will occur over all periods. This will address problem #13. * Metrics for the company’s performance should be created last, only because we need to wait for the actions to be taken, and should include financial measures including gross profit, value-added measurements on the whole process, cycle counting. This way we can find what process are waste and unnecessary, and perhaps some ROI on the new investments made in R&D to potentially expand product lines and fortify their complementary products. This will address problem #1. * Physical inventory count will start. 3 day weekend, overtime will be handed out to those who come help with the count) * Two people will be hired for cycle counting after the physical inventory count has been completed. Katt and Ivan will be working together, utilizing the cycle counting as a form of checks and balances to ensure that the purchases do not step out of line with the predictions. This will address problem #9. Metrics Ending Q3 Time by Quarter (x) Payroll Errors / week (y) Time by Quarter (x) Inventory Accuracy Percentage (y) Time by Quarter (x) AP / AR Days (y) Time by Quarter (x) R&D projects incomplete / ongoing from Q1 (y)
Time by Quarter (x) Percentage of Process Documentation (y) Organization Chart Ending Q3 Q4 * At this point, the company should be running fairly smoothly. Majority if not all of the problems would have been solved. The company will focus more on R&D at this point in order to increase profitability in the future. Metrics will play a large role in quality management of both processes and employees. Metrics Ending Q4 Time by Quarter (x) Inventory Accuracy Percentage (y) Time by Quarter (x) AP / AR Days (y) Time by Quarter (x) Percentage of Process Documentation (y) Organization Chart Ending Q4
Cite this Page
Old Joe Case Report. (2017, May 02). Retrieved from https://phdessay.com/old-joe-case-report/
Run a free check or have your essay done for you
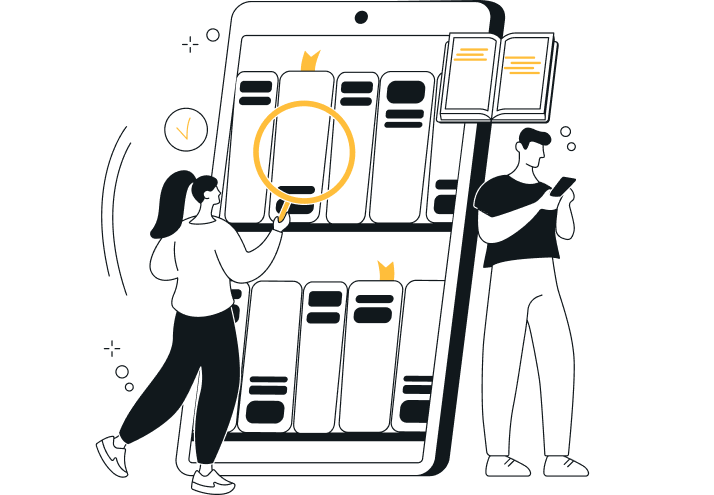