Materials Requirements Planning
A material requirement planning is a soft ware based planning and inventory system used in management of manufacturing system. It simultaneously meets three main objectives: plan manufacturing activities, deliver schedules and purchasing activities; it ensures that materials and products are available for production and delivery to customers; it also maintains the lowest levels of inventory.
At the same time, it also schedules procedures for production process with several levels of production. When fed with the information describing the production requirements for finished goods of the system, the structures of the production system and the inventory for each operation, the material requirements planning determines raw materials purchasing and schedules for the operations (Friedman 1997,pg 16).
In business activities, it should be realized that, time is money. Material requirements planning come up with dynamic decision technologies. It acts as a necessary tool for applying to a wider range of managerial decisions successfully whereby time and money are directly related. With increased technology, the normal divisions between manual and intellectual labor are collapsing. This has been due to the fact that many industries are moving towards controlling and mediating work using computerized tools.
Order custom essay Materials Requirements Planning with free plagiarism report
A greater number of workers are being compelled to conceptualize on a very different level of abstraction than before. Materials requirements planning describes how decision making is done through analyzing three level of workers in a large manufacturing factory. The important issue may not be identification of which should or can learn the system but how learning occurs. The main concern here is to explore how workers ways of thinking and understanding are affected by changes in the nature of work and work place organization.
Through application of this new technology in business, the decision making would be very easy because MRP would be doing the critical part of work. What is more important is only to feed the required production information to the material requirements planning.
Bill of materials is module that is part of the manufacturing software solutions. It is designed to create and maintain the parts needed in completion of end products. Such includes all sub assemblies, and assemblies and also shipping supplies if required. Bill of materials can be created as products are ordered, designed, build or maintained. In material requirements planning, bill of material describes the part list of components required to complete a saleable end item. BOMs are naturally hierarchical where the top level represents the sub assembly or the end term.
Modular Bill of materials defines the component materials, parts, documents and engineering drawings required to complete sub-assembly (Friedman 1997,pg 56). (MPS) Master Production Schedule operates within a single level of the BOM. If the MPS is run on a material, it implies that necessary orders one planned at that certain level. If any dependant requirements they are placed on the next Bill of materials level down and the process stops. The master production scheduling is a form of material requirements planning that stresses planning on the parts of products that have great influence on company profits or which dominates the entire process of production through raking critical resources.
These items are marked as “A” parts and are planned with extra attention. The items selected for a separate MPS ran before the MRP ran. The Master Production scheduling ran is conducted without a bill of materials exposed so that the material requirement planning controller can ensure that the master schedule items are planned correctly before the running of the detailed material requirement planning takes place. Once the changes in MPS occurs in any business, loses are bound to be incurred because company relies on this part for entire process of production through critical resources.
At the same time, a change in lot size should create a negative impact in the production. Better protection for larger lots can be justified by that, for large lots, the rejecting cost is good where by the cost of accepting bad lots are higher. When the lot size reduces, it then implies that the cost will reduce thus reducing the profits.
Case ii. What is the relationship between inventory and MRP? What is the relationship between capacity and MRP?
The relationship between inventory and MRP is that, inventory refers to the list of materials and goods or those goods and materials themselves, which are held available by any business. They are held in order to manage and hide the consumer so that the manufacture’s delay is no longer than the delivery delay. They also serve the purpose of easing the effect of imperfections in production process. On the other hand, MRP is a method of effective planning of all resources of any manufacturing organization of company (Friedman 1997, pg 67).
The relationship between capacity and MRP is that, capacity is the point of production at which an organization either industry or firm’s average cost or per unit begin to raise due to fixed factors which are land or capital. Its relation with MRP is in that, economically both stress on production where by MRP can be used in improvement of capacity in the firm.
Case iii. Why is it important to have MRP reflect what you actually want to build? How can we use information about the material parent/child relationship and pegging in MRP and PAC (Production Activity Control)? Material requirements planning should reflect what is actually indented to be built. This is because it integrates many fields of manufacturing enterprise in to a single entry for planning and control purpose. It builds on closed loop material requirement planning through adoption of feedback principle and extending it to additional areas of the primarily manufacturing related enterprise.
Material requirement planning and production activity control are measures used in company’s production which aims at maximization of incomes. The information about the material parent/child relationship can be only be applicable to these measures if at all they are business oriented and aims to improve production. Such a relationship should be large enough for the practices to be carried within the firm otherwise they cannot work in small firms.
Case iv. How do set-ups impact capacity planning? How can capacity planning support operational strategies and decision making?
Capacity planning is the process that determines the production capacity required by a firm so to sustain the changing demands for its products. When set ups are put in place, they affect the process of capacity planning because at early age, it is very difficult to determine the firms output and its changes in demand. Once a new firm has been set up, it should be given some duration so as to gain establishment to the clients. During this period, capacity planning cannot be applicable to such a firm.
Capacity planning can support operational strategies and decision making in an organization through various ways. Because it aims at minimizing the discrepancy, any factors that may lead to failure in the firm are noted (McCarthy 2002, pg 34). Because capacity is increased through introduction of equipment and material, new techniques, increased number of workers and machines, increased number of shifts or acquiring extra production facilities, it is very easy to identify where there is a loophole through use of capacity planning and make the required change in decision making.
Case v. In Production Activity Control, why are their multiple ways to prioritize work to be done? How are they different? What are their advantages and disadvantages?
In production activity control, multiple ways to prioritize work to be done are applied. This is because with increasing concentration on optimizing capacity to planning, drive down costs and controlling shop floor an activity is a must. Production activity control ensures provision of the flexibility to structural standards expectations and quick adjustments to unexpected changes. By display of all work orders currently in the process, and ready to be processed in the work centre, not unless multiple ways are employed to prioritize the work, accuracy cannot be arrived at (McCarthy, pg 89).
Production activity control differs form one another through the size of firm being dealt with. For instance the measures employed in a small scale manufacturing enterprise cannot be compared with the ones applied in a large organization. Although they may serve the same purpose their scope is quite different. The advantages of production activity control include that, there is flexibility in re-prioritization on the fly ensured production competition in accordance with customer deadline.
There is also quick adjustment to the temporary adverse circumstances which are eliminated. Also there is enjoyed long-term effect of production bottle necks. On the other hand, some of the disadvantages include availability of complete new sales orders of products which demand client within a limited deadline.
Case vi. How does variation in performance to anticipated standards of set-up, run and availability of equipment/people impact the schedule, inventory levels, customer service and costs?
Once a new set up is established the inventory level definitely goes up so as to meet the requirements for the new customers. In the organization the schedules also has to change so as to manage the large number in the market. The main role of inventory planning is to translate the plan of production in to a detailed component orders. It determined the items to be produced and when such productions should be done. This enables the customers to get what they want at the right time.
The inventory program also has a function of recommending order priorities thus making capacity requirements planning easier. It assumes that adequate capacity will be available when needed. Suppliers encounter problems due to schedule instability. As a result suppliers have to react to the unexpected changes in requirements. This problem in turn results to high costs because of increased time. As a result, increasing uncertainties and dynamics in the environment of planning system should react to unexpected developments. The variation in performance to anticipated standards of set up and availability of equipments and people impact the schedule inventory levels, consumer services and costs (McCarthy, pg 132).
This happens in that, once new set ups are established definitely the inventory levels should go up so as to meet the demand of new consumers. The schedules should also change in order to be able to handle large number in the market. The customer service should be improved also to have more customers through use of motivations.
Work Cited.
Friedman L, (1997). The Developmental Psychology of Planning: Why, How, and When Do We Plan? Mahwah.
McCarthy B, (2001).Human Performance in Planning and Scheduling. London.
Cite this Page
Materials Requirements Planning. (2017, Feb 13). Retrieved from https://phdessay.com/materials-requirements-planning/
Run a free check or have your essay done for you
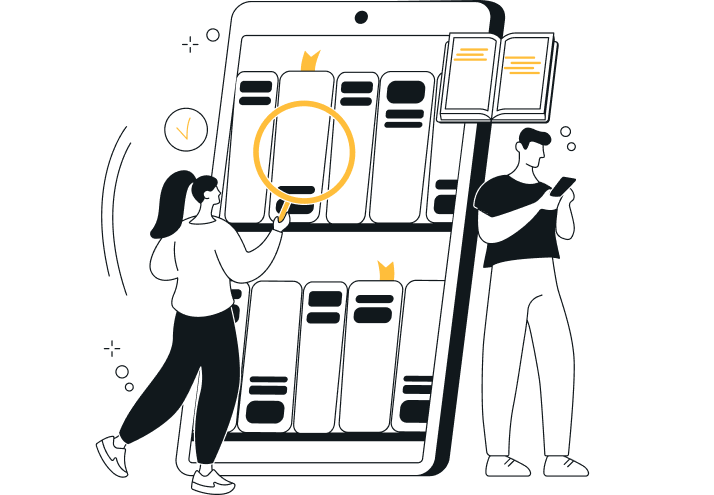